Kimya Endüstrisinde Sürdürülebilir Dijitalleşme: İkiz Yönetim Yaklaşımı
Bir tesis hayal edin. Belirli sayıda karıştırmalı tank ya da reaktörlerin çalıştığı, her birinde belirli reçeteye bağlı reaksiyonların ya da karışım proseslerinin aralıksız devam ettiği, birkaç teknisyenin sürekli belirli dakikalarda her tanktan analiz numunesi aldığı ve laboratuvara götürdüğü, laboratuvar cihazının başında örneklerin biriktiği ve sırada beklediği, dolum ve paketleme için laboratuvardan gelecek sonucun beklendiği…
Çok tanıdık geldi değil mi? Aslında hayal etmemize gerek yok, birçoğumuzun proseslerindeki günlük rutinlerinden bir kesit anlattım. Herhangi bir proses profesyoneli için çok tanıdık bir senaryo. Kimyasal üretimlerin çoğu, uzun yıllardır gerçekleştirilen eski proseslerdir. Üretim süreçlerinde uygulanan yöntemlerin de çoğu oturmuş yöntemlerdir.
Bu durum avantajlarla beraber dezavantajları da beraberinde getirir. Mesela hammaddelerde bir değişiklik olmazsa uzun yıllar hiç değişiklik yapmazsanız aynı üretimi aynı kişilerle yapmanız mümkündür. Çünkü bu kişiler tesisin, reaktörlerin kronik problemlerini bilir. Son üründe yaşanan problemlerin kaynaklarını tespit edebilir. Üründe yaşanan sorunun telafi yöntemlerini de kendilerince belirlemişlerdir.
Çoğu zaman üst yönetime raporlanmaya gerek kalmadan sorun çözülür. Ancak avantaj olarak sayılabilecek kişilere bağımlı bu süreç aynı zamanda dezavantaja da dönüşebilir. Süreçlerin oturmuş olması manuel operasyonların yeterli olduğu algısı yaratmaktadır. Ta ki
telafi edilmesi maliyetli bir durum oluşana kadar... Bu durumda tanıdık bir diğer senaryo devreye girer.
Günlük üretim rutinleri devam ederken bir gün polimerizasyonda reaksiyon sonu kaçırılır ve ürün donar. Reaktör bir süre kullanılamaz halde kalacaktır. Bir diğer senaryoda mevsim geçişi nedeniyle sıcaklıklarda sorun yaşanmaktadır. Son üründe müşteri şikayetleri artmaya başlamıştır. Bu sorunlar her fabrikanın belli periyotlarda yaşadığı sorunlardır.
Bir üretim tesisi için dijitalleşme bu tarz durumlarda varlığını ya da eksikliğini sonuna kadar hissettirir. Çünkü dijital sensörler size bu anlamlı verileri sağlar. Bu veriler anlık ve tarihi (historical) verileri kapsar.
Bir Dijitalleşme Örneği: Inline Viskozite Ölçümü
Mesela bir polimerizasyon reaktöründe sıcaklık, viskozite ve pH en önemli kritik kontrol parametreleridir. Proses viskozimetreleri, inline pH ve sıcaklık sensörleri anlık veriler ile reaksiyonların kontrol altında tutulmasını sağlar. Belirli set değerleri önceden tanımlanarak olumsuz durumlar henüz gerçekleşmeden alarm verebilir.
Olumsuz durumlar gerçekleştiğinde de geriye dönük nedenlerin tespitini sağlar. Bu
verilerin hepsi saniye hatta daha kısa sıklıklarda dahi izlenebilir. Bu sayede saat başı laboratuvar numunelerinde tespit edilemeyen zamana bağlı değişimler de kaydedilir.
Dijitalleşme, tabii ki genellikle verimsiz çalışan fiziksel unsurlarda ve süreçlerde bir dönüşüme gidilerek gerçekleşir. Fakat bu, mevcut süreçlerin ve altyapının tamamen yok olacağı anlamına gelmez. Bunu aksine, mevcudun ve dönüştürenin aynı anda hibrit olarak
kullanıldığı bir durum yaratılır.
Bir su bazlı boya üretiminde karıştırma prosesini ele alalım. Her ürün için önceden tanımlanmış bir reçete ve karıştırma süresi vardır. İşleyiş şöyledir: su tanka alınır, karıştırıcı devreye girer, toz ve diğer sıvı içerik reçeteye göre eklenir ve belirlenen sürede karıştırma
tanımlanır. Süre biter laboratuvara bildirilir viskozite için numune alınır. Uygunluk sonrasında dolum başlatılır. Reçetedeki önceden belirlenen karıştırma süreleri genelde emniyetli olarak belirlenmiştir ve genelde gerektiğinden fazla sürelerdir.
Karıştırmanın tamamlanıp, numunenin laboratuvara ulaşması, numunenin hazırlık süreci ve laboratuvar cihazının müsaitliği düşünülürse bu süreler çok uzayabilmektedir. Aynı karıştırma sürecini şimdi dijitalleştirelim. Polimer söz konusu olan proseslerin çoğunda en önemli parametre viskozitedir. Bu karıştırmalı tankın gövdesine bir proses viskozimetresi monte ettiğimizi düşünelim. Bu andan itibaren artık anlık viskozitenin saniye bazında değişimi takip edilebilecektir.
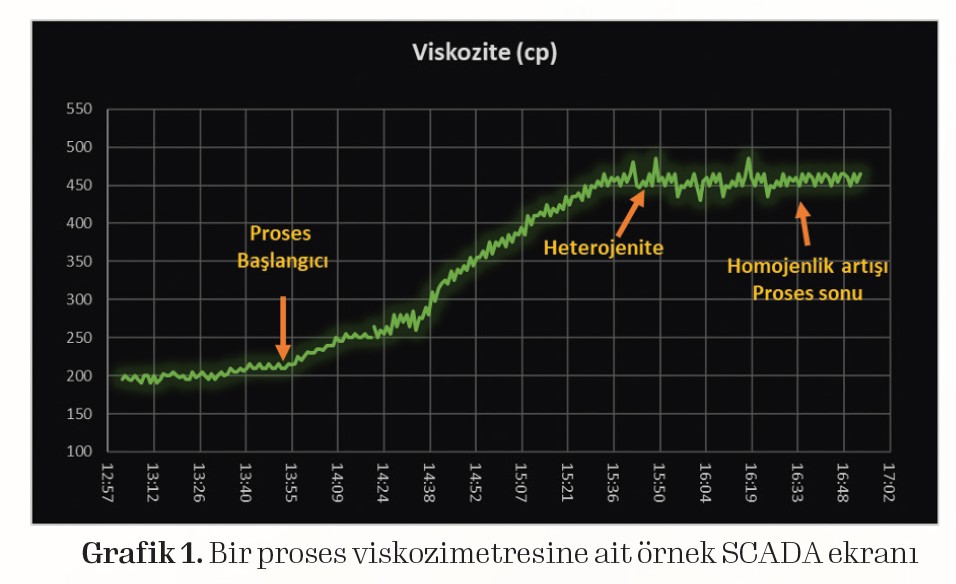
Süreç Makale şu şekilde işleyecektir. Su ve diğer bileşenler tanka alınacak. Viskozitedeki kademeli artış viskozitenin bağlı olduğu sistem tarafından sürekli kaydedilecek. Önceden belirlenen uygun viskozite aralığına girildiğinde ürünün hazır olduğu operatörler tarafından anlaşılacaktır.
Bu anda artık hiç beklemeden tank boşaltılmaya başlanabilir. Kalite laboratuvarı da kendi şahit numunesini boşalma sırasında gelip alabilir. Grafik 1’de bir karışım prosesine ait örnek bir proses viskozimetresinden alınan verilerinin zamana bağlı grafiği görebilirsiniz.
Bu mikser örneğinden hareketle bir proses viskozimetresinin sisteme entegrasyonunun katkılarını aşağıdaki gibi sıralayabiliriz. Bu faydalar genel olarak diğer dijitalleşme aksiyonları için de geçerlidir:
• Ölçümler sürekli ve yerinde olduğu için problem yaşandığı anda tespit edilebilir.
• Laboratuvar ölçümlerine göre daha hızlı bir sonuç verir. Bu sayede bekleme sürelerini kısaltır. Zamansal verimlilik sağlar.
• İnsan kaynaklı ölçüm hatalarının önüne geçer.
• Önceden belirlenmiş eski reçetelerde geliştirme yapmayı sağlar. Proses geliştirmeye ve sürekli iyileştirme çalışmalarına katkı sağlar.
• Otomasyon sistemlerine ve yapay zekâ araçlarına veri sağlar.
• Fazla karıştırma ya da uygunsuz ürün nedeniyle ortaya çıkan kayıpların önüne geçer.
• Proses viskozimetreleri üretim tanklarına ya da boru hatlarına monte edildikleri için doğrudan proses etkileri altında ölçüm yapılmasını sağlar. Bu sayede akışkanın proses sırasındaki reolojisi de takip edilebilmektedir.
• Karışım proseslerinde viskozitenin yanı sıra akışkanın homojenliğinin de tespit edilmesini sağlar. Grafik 1’de görüleceği gibi karışımın sonlarında veri çizgisi düzelmektedir. Bu durum homojenliğin arttığı, katı maddelerin daha çok çözündüğü şeklinde yorumlanabilir.
• Zamana bağlı değişen bir reaksiyon gerçekleşiyor ise proses viskozimetresi ile reaksiyonun başlangıç ve bitiş süreleri kolayca tespit edilebilmektedir. Jelleşme ve aniden katılaşma süreçlerinin önüne geçilebilmektedir.
Tüm bu avantajlara rağmen dijitalleşme araçlarına yapılacak yatırımlar karar vermesi uzun zaman alan süreçlere dönüşebilmektedir. Bu durum çoğu zaman yanlış algıdan kaynaklanır. Dijital dönüşüm, yaygın algının aksine tüm süreçlerde radikal dönüşümler ve yüksek teknolojik yatırımlar yapmayı gerektirmez.
Bir diğer ifadeyle dijital dönüşüm yıkıcı olmak zorunda değildir. Viskozimetre örneğine dönecek olursak. Bir proses viskozimetresi entegrasyonu üretimin ve kalitenin süreçlerini kolaylaştıran bir unsurdur. Kalite laboratuvarı faaliyetlerine devam etmektedir. Şahit numuneler, son ürün örnekleri alınmaya ve saklanmaya devam edilmektedir.
Proses viskozimetresi otomasyon sistemi ile ve SCADA ile haberleşen bir bileşen olarak sisteme eklenmiştir. Danışmanlık sağladığımız ve müşterimiz olan üretim tesislerinde bu
algının hakim olması bizim için sıradan bir durumdur.
Ancak aynı zamanda dijitalleşmenin doğru yönetilmesi gereken bir süreç olduğunu göstermektedir. Aynı sürdürülebilirlik gibi. Sürdürülebilirlik, ülkelerin ve toplumların
günlük ihtiyaçlarını karşılarken, gelecek nesillere aktarılacak kaynakların ve tüketim ihtiyaçlarının göz ardı edilmemesidir. Bu tanımdan da hareketle hem dijitalleşme hem de sürdürülebilirliğin ulaşmaya çalıştığı nokta benzerdir.
AB’ne göre Avrupa’yı küresel düzeyde rekabetçi, iklim açısından nötr ve dijitalleşmiş bir ekonomi ve toplum haline dönüştürme hedefi, iki temel sütuna dayanmaktadır: yeşil ve dijital dönüşümler. İkiz dönüşüm olarak tanımlayabileceğimiz bu dönüşümler üretici şirketler tarafınca da birlikte yönetilebilir.
“Sürdürülebilir dijitalleşme” de diyebileceğimiz bu kavram AB tedarikçisi olabilmek için kaçınılmaz bir kavramdır. Bu ikiz dönüşümün birlikte yönetilmesi her iki kavram için de yolun başında olan tesisler için bir avantaj olacaktır. Zaten bu iki kavram birbirlerine sebep sonuç ilişkisiyle bağlı kavramlardır.
Dijitalleşmenin özellikle kimya ve polimer endüstrisinde sürdürülebilirliği katkısı yüksektir. Bu katkıları; kayıpların azaltılması, üretim verimliliğin artışı ve enerji verimliliğinin sağlanması başlıkları altında toplayabiliriz. Biraz daha detaylandıracak olursak:
• Dijital ölçüm teknolojileri yerinde ve anlık ölçümler sayesinde hataları ve fireleri azaltır. Hammadde kullanımını optimize etmeye yardımcı olur.
• Sıcaklık, basınç, karıştırma hızı ve debi gibi enerji tüketimine neden olan parametreler hassas ve anlık ölçüm ile doğru yönetilebilir. Enerji verimliliği sağlanır.
• Dijital sensörler ile atık ve atık su miktarı azaltılabilir. Otomatik yıkama süreçlerinde drenaj hattında kullanılacak bir türbidimetre gibi bir sensör ile gereksiz su tüketiminin önüne geçilebilir. Aynı sensörler ile eşanjör, serpantin ve kondens hatlarına ürün sızıntısı da tespit edilebilir.
• Dijital ölçüm sistemleri büyük miktarda veri üretir. Bu sayede veri analizi ile verimsizliklerin önüne geçilebilir.
• Tekrarlanabilir ürün kalitesi sağlar. Uygunsuzlukların ve standart dışı ürün üretilmesinin önüne geçer.
• Daha iyi envanter yönetimi ve tedarik zinciri optimizasyonunu mümkün kılar.
Ham madde kullanımını ve envanter seviyelerini gerçek zamanlı olarak izleyerek üreticiler hammadde yönetimi yapabilir ve nakliye ihtiyaçlarını minimize ederek daha sürdürülebilir
ve verimli bir tedarik zinciri oluşturabilir.
Sonuç olarak, üretim tesislerinin mevcut yatırım planlarında yeşil ve dijital olma yolunda ortak hedefler koyarak ikiz bir yönetim anlayışı uygulayabilirler. Günümüz kaynaklarının verimli kullanımını günümüz teknolojileri ile birleştirmek gelecek nesillerine teni teknolojileri
üretecek kaynaklar bırakmamızı sağlayacaktır.
Dr. Hulki Özel
Satış ve Uygulama Direktörü
Pikolab Mühendislik