Polimer Üretim Proseslerinin Dijitalleşmesinde PAT Yaklaşımı
Polimerler, monomer adı verilen kovalent kimyasal bağlarla bağlanmış tekrar eden birimlerden oluşan yüksek moleküler ağırlıklı moleküllerdir. Polimerizasyon reaksiyonları genelde başlangıçta monomerlerden oluşur ve ortam düşük viskoziteye sahiptir. Katalist eklenmesiyle ve / veya ısı ile polimerizasyon prosesi başlar ve viskozite zamanla artar.
Viskozite ile polimerin molekül ağırlığı arasında doğrudan bir ilişki vardır. Bir başka ifadeyle viskozite molekül ağırlığını takip etmek için bir dolaylı parametredir.
Bu bağlamda polimerizasyon içeren polimer üretimlerinde ya da polimerlerin herhangi bir aşamada kullanıldığı proseslerde viskozite üretim takibi için kritik kalite kontrol parametrelerindendir.
Polimerizasyon süreçlerinde başlangıç ve bitiş noktasının belirlenmesi genelde viskozitenin ve asit sayısının “off-line” takibi ile gerçekleştirilmektedir. Yaygın olan uygulamada bu izleme süreci, manuel olarak alınan örneklerde titrasyon ve Ford / DIN Cup ya da dijital masaüstü tip cihazlarla viskozite ölçümü ile yapılır.
Özellikle reaksiyonun bitiş noktasını tespit edip polimerizasyonu doğru noktada durdurmak için örnek alma sıklığı çok artar. Üretim takibi zahmetli, maliyetli ve operatör hatalarına açık hale gelir.
Bu noktada gerçekleştirilecek bir hata, viskozitenin jelleşmeye hatta katılaşmaya kadar gidecek derecede artması, kabul kriterlerinin altında olacak şekilde düşük viskoziteli bir ürün elde edilmesi gibi geri-dönüşlü olmayan sonuçlar doğurabilir.
Bunun ötesinde, beçler arası ürün kalitesinde ciddi farklar oluşması ve uygunsuzluk nedeniyle ürün kayıplarının oluşması ekonomik kayıplara neden olmaktadır. Bu nedenle aslında ortalama 50 yıllık bir teknoloji olan proses viskozimetreleri ile tanklara ya da sirkülasyon / besleme hattı gibi noktalarda sürekli viskozite ölçümü gerçekleştirilmesi her geçen gün yaygınlaşmaktadır.
Ayrıca nispeten daha yeni teknolojiler olan proses spektrometreleri ile asit sayısı ya da renk parametresinin inline olarak takip edilmesi mümkün hale gelmektedir. Bu sayede minimum numune ihtiyacı ve minimun kayıp ile yatırımın geri dönüşü hızlı olmaktadır.
Polimerizasyon ve viskozite arasındaki ilişkiyi konu alan yukarıda bahsettiğimiz ve sık karşılaşılan senaryolar aslında uzun yıllardır birçok endüstride birçok farklı kritik
kontrol parametresi ve farklı ürünler için benzer şekilde ve benzer olumsuz sonuçlarla endüstrilerde paradigma değişikliğine neden olmuştur. Bunlardan birisi bitmiş üründe kalite-kontrol sağlamak yerine “tasarımla kalite” yaklaşımıdır.
“Tasarımla kalite” kimyasal üretim proseslerini de kapsayan tüm üretimleri ilgilendiren yeni bir paradigmadır. Özetle “kalite-kontrol son üründe yapılmaz, ürün kaliteli üretilir” şeklinde tanımlanabilecek bu yaklaşım kalite-kontrolün prosesin her yerinde ve henüz tasarım aşamasında tesis edilmesini hedeflemektedir.
Bu hedefin gerçekleşmesi için proses aşamasında önemli parametrelerin sürekli takip edilmesi ve gerektiğinde kontrol senaryolarının işletilmesi gerekir. Proses analitik
teknolojisi (PAT) tam da bu amacı mümkün kılan araçları içeren teknolojidir. PAT geleneksel laboratuvar analizleriyle, proses otomasyon sistemleri arasında köprü kurar.
Ayrıca üretimler devam ederken sürekli ve hızlı proses takibini en önemlisi de hızlı kontrol müdahalelerini gerçekleştirmeyi sağlar. PAT teknolojisi bileşenleri PAT araçları olarak adlandırılır.
2.1 Proses Analitik Teknolojisi (PAT)
FDA’ya göre PAT son ürün kalitesini temin edebilmek için hammaddelerin, proses girdilerinin ve çıkıtılarının ayrıca prosesin kendisinin kritik kalite parametrelerinin off-line ya da at-line analizler yerine in-line, on-line ya da temassız olarak zamana bağlı analiz etmenin bir yoludur. Aslında proses analitiği ile ilgili çalışmaları ilk gündeme getiren FDA olmamıştır.
Proses analitiği aslında 1950’lerden beri petrol ve petrokimya endüstrisinde kullanılmaktadır.
Ancak ilaç, gıda ve kimya gibi endüstrilerin ortaya çıkan ihtiyaçları ve analitik teknolojilerdeki gelişmelerle beraber proses analitik kimyasının ortaya çıkmasıyla konu adeta reenkarnasyona uğramıştır 2.
Kavramsal olarak ilk çalışmalar 1980’lerin başında proses analitik kimyası (PAC) konseptinde Washington Üniversitesi’nde Bruce Kowalski önderliğinde bir ekip tarafından
başlatılmıştır. Kowalski’nin başkanlığında 1984 yılında endüstri temsilcilerinin de içinde bulunduğu bir konsorsiyum olan Proses Analitik Kimyası Merkezi (Center of Process Analytical Chemistry-CPAC) kurulmuştur.
Bu merkez öncelikle halihazırda gerçek zamanlı analizlerin kullanıcısı olan tesislerle ortak çalışmalara odaklanmış, mevcut verilerin analizi ve “kemometri yaklaşımı ile verilerin değerlendirmesi” konusunda çalışmalar yapmışlardır.
Bu tesislerden birisi Dow Kimya Şirketi’dir. Dow’da gerçekleştirilen örnek uygulamalar hammaddelerin NIR ile analizi ve proses sırasında değişken sıcaklıklarda kostik ve tuzun miktarının kemometri yaklaşımı ile tespit edilmesi gibi çalışmalardır3. Kimya endüstrisinde
kullanılan analizörler genel olarak spektroskopi temelli olup yakın kızılötesi spektroskopisi NIR (near infrared) ile Nükleer manyetik rezonans (NMR), Raman spektroskopisi, Fourier dönüşümü kızılötesi spektroskopi (FTIR) gibi örneklerdir.
Yalnızca verimlilik ve ürün kalitesi optimizasyonu değil proses modelleme ve istatiksel yaklaşımlar da yapan sistemler kullanılmıştır. Yaygın olarak kullanılan istatistiksel yaklaşımlardan birisi “kısmi en küçük kare yöntemi (Partial Least Square-PLS)” olmuştur4.
Kowalski ve ark. çalışmalarında off-line, at-line, on-line, non-invasive gibi proses analiz tiplerinin tanımlarını yapmış günümüzde dahi karıştırılan kavramların terminolojisine
katkı sağlamışlardır5. Proseslerde analiz tipleri şu şekilde tanımlanabilir (Şekil 1):
[caption id="attachment_143774" align="aligncenter" width="670"]
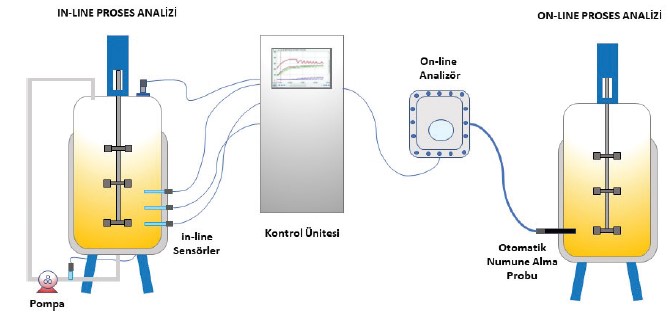
Şekil 1. In-line ve On-line proses analiz tiplerinin karşılaştırılması[/caption]
Off-line Analiz: Prosesten genelde elle alınan örneğin laboratuvara götürülüp analiz edildiği tiptir.
At-line Analiz: Off-line işlemin üretim sahasında üretim hattının hemen yakınında yapılan analizdir.
On-line Analiz: Numunenin otomatik olarak bir by-pass hattında bir vana ile ya da numune alıcı bir sistem ile prosesten alındığı ve analizöre beslendiği analiz tipine verilen isimdir.
In-line Analiz: Numunenin proses dışına çıkmadan prosesin içinde yapıldığı analiz tipidir. Genelde bir örnek alma işlemi gerçekleşmez prosese daldırılan prob, sensör aracılığıyla ya da akış hücresi ile ölçüm gerçekleşir.
PAT süreci online ve in-line analiz tiplerini kullanarak PAT araçları ile gerçekleştirilir. PAT araçlarının kullanımının amaçları: üretim döngü süresin kısaltmak, kalite olarak reddedilme nedeniyle ürün imhasını engellemek, gerçek zamanlı veri sağlamak, otomasyonu artırmak, malzeme ve enerji tasarrufu sağlamak, sürekli üretimi kolaylaştırmak, vb. olarak sayılabilir.
Esasında PAT, geçmişteki terminolojide Proses Analitik Kimyası (PAC) olarak adlandırılan kavramdan biraz farklıdır. PAT aslında sadece bir analiz değil analizin ötesinde bir kavramdır.
Sadece laboratuvarda off-line olarak yapılan bir analizi at-line, on-line ya da in-line’a taşımak mutlaka PAT değildir7. Örneğin; HPLC ile laboratuvarda son üründe off-line olarak analiz edilen bir parametrenin sadece on-line NIR spektroskopisi analizi ile değiştirilmesinin
ilk bakışta bir PAT aksiyonu olduğu izlenimi olabilir.
Ancak bu yanlış olur. Çünkü bu durumda hala süreç analiz edilmeyecek sadece son ürün analizine devam edilmiş olacaktır. PAT felsefesini ve arka planına göre; bir on-line analizörden alınan veriler incelendiğinde ürün kalitesiyle ilgili çıkarımlarda bulunulabilecek
sonuçlar alınabilmelidir.
Böylelikle hedeflenen son ürün kalitesini sağlamak için prosese erken bir aşamada müdahale etme imkânı sağlanır. Örneğin bir kimyasal harmanlama prosesinde yeni bir in-line NIR analizör kullanılmaya başlanacak ve bu analizör; işlemi önceden sabitlenmiş bir süre boyunca karıştırmak yerine, karışım homojen hale gelene kadar harmanlanmasını sağlayacak ve bu süreç NIR tarafından gerçek zamanlı olarak izlenecektir.
Bu yöntem ile mevcutta yalnızca bitmiş ürünün kalitesinin belirlendiği bir süreç yerine gerektiğinde düzeltici eylemi üstlenebildiği bir yenilik olacaktır. Öte yandan bu analizörün amacı, süreci yalnızca doğru kalite ile sonuçlanabileceği şekilde kontrol etmek ve izlemektir.
Dolayısıyla bu örnek “kalite ürünler üzerinde test edilemez; yerleşik olmalı veya tasarım gereği olmalıdır” durumunu karşılamaktadır.
Proses Viskozimetreleri
Endüstride üretimi ve kullanımı yaygın olarak gerçekleştirilen polimerler: fenolik reçineler gibi yapıştırıcılar, poliüretan tipleri, yaş mukavemet kimyasalları gibi kağıt kimyasalları, tekstil endüstrisinde kullanılan haşıl ve oluklu mukavva endüstrisinde kullanılan tutkal gibi nişasta bazlı polimerler, alkid reçineler, boyalar ve boya hammaddeleri, PE, PP, vb olarak sayılabilir.
Bu proseslerde viskozite en önemli kritik kalite kontrol parametrelerindendir ve in-line ölçüm yaygınlaşmaktadır. Proses viskozimetresi tipleri Döner tip, titreşimli tip, kılcal tip vb. laboratuvar cihazlarına benzer şekilde sınıflandırılmaktadır.
Ancak proseste çoğu zaman zorlu koşullarda sürekli çalışacakları için ilk koşul yüksek başınç, yüksek sıcaklık gibi zorlu ve değişken proses koşullarında çalışabilme, aşınma ve korozyona karşı dayanım, kabarcık ve katı partiküllerden minimum etkilenme gibi özellikler kullanılacak viskozimetrenin model ve prensip seçiminde önemli unsurlardır.
Söz konusu viskozite olunca önemsenmesi gereken diğer karakteristik ise çalışılacak akışkanın reolojisidir. Çünkü polimerler genelde non-newtonian ve yaygın olarak da psödoplastik karakterdedir.
Bunun iki önemli anlamı vardır: İlki proseste ölçülen viskozite değerleri ile laboratuvarda ölçülen değerler aynı mertebede olmayacaktır. Diğeri ise yanlış viskozimetre kullanımında prosesteki shear etkileri mesela karıştırıcı hızı / pompa debisi değiştiğinde viskozite değişecektir.
[caption id="attachment_143778" align="aligncenter" width="488"]
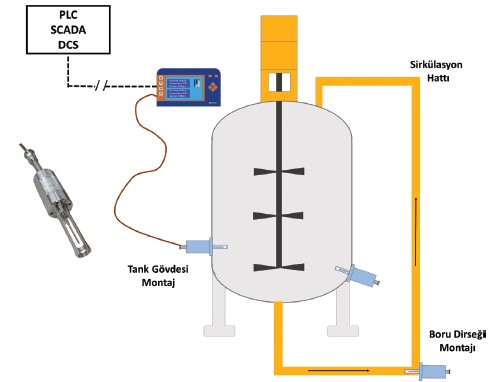
Şekil 2. Örnek bir proses viskozimetresi ve montaj tipleri[/caption]
Bu nedenle non-newtonian bir akışkan ile çalışıldığında high-shear tip olarak ifade edilen kendi kayma hızını yüksek bir şekilde kendisi üreten viskozimetrelerin kullanımı tavsiye edilmektedir. Mesela titreşimli tip bir high-shear viskozimetre 200 s-1 titreşim frekansının üstünde shear sağlayabilmektedir.
Bu da proses etkilerinin ölçülen viskoziteye etkisini minimumda tutmaktadır. Ayrıca bilindiği gibi psödoplastik akışkanlara uygulanan kayma hızı oldukça arttırılırsa akışkan newtonian akışkanı taklit eden bir davranış sergiler ve kayma-hızı daha fazla arttırılırsa bile viskozite artmaz.
Bu nedenle yüksek kayma-hızlı viskozimetreler bu akışkanlarda daha kararlı ve en önemlisi daha yüksek tekrarlanabilir ölçümler sağlar.
Proses viskozimetreleri çeşitli montaj flanşlarıyla tank gövdesi veya boru hatlarına uygun noktalara monte edilerek kullanılmaktadırlar. Bir kablo ile sensör elektronik konvertör kısımlar ile bağlanmaktadır.
Bu konvertörler genelde hem viskozite indikatörü hem de sinyalin aktarımını sağlayan transmitter görevi görmektedir. Şekilde bir proses viskozimetresinin montajı temsili olarak gösterilmiştir.
Proses Spektrometreleri
Spektroskopi, elektromanyetik dalgalar ile analit arasındaki ilişkinin dalga boyunun bir fonksiyonu olarak ifadesidir. Temel olarak atomik ve moleküler spektroskopi olarak sınıflandırılabilmektedir.
Ancak inline proses spektroskopisi genel olarak elektromanyetik dalgaların moleküler bağlar ile ilişkisini tanımlayan moleküler spektroskopi ile ağırlıklı olarak ilgilenmektedir. Madde ile ışık etkileştiğinde 3 farklı etki ortaya çıkar bunlar: absorpsiyon, emisyon ya da saçılmadır.
Bu etkileşimler farklı dalga boylarında farklı spektroskopik yöntemler kullanılarak tespit edilebilir. Bu yöntemler içerisinde kimyasal proseslerde ve özellikle polimer üretim proseslerinde yakın kızılötesi (Near Infrared-NIR), ultraviyole-görünür ışık bölgesi (UV-Vis)
spektrometresi en yaygın olarak kullanılan in-line proses spektrometrelerine örnektir.
Her spektroskopik teknik farklı moleküllerin analizi ile ilişkilidir. Örneğin UV-VIS spektroskopisi ultraviyole ve görünür ışığı 200-780 nm dalgaboyu aralığında kullanırken,
NIR spektroskopisi NIR ışık ve 800-2500 nm dalga boyu aralığında çalışan yöntemlerdir.
Proses spektrometreleri temel olarak Beer-Lambert yasasına bağlı olarak çalışır. Bu yasa, ışığı soğuran molekülün sıvı içerisindeki konsantrasyonu ile ışık ve dedektör arasındaki optik yolun ve ışığın soğurulması arasındaki ilişkiyi ifade etmektedir.
Bu ilişki sayesinde ışığın absorpsiyonu ölçülerek analitin konsantrasyonu tespit edilebilmektedir.
In-line proses spektrometreleri genelde üzerlerinde lamba ve dedektör modülleri içeren bir set olarak boru ile aynı çapta olan bir sensör gövdesi biçiminde ya da bir çubuk geometrisinde olan bir prob biçiminde üretilmekte ve kullanılmaktadır.
[caption id="attachment_143781" align="aligncenter" width="392"]
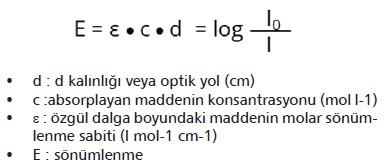
Denklem 1. Beer-Lambert Yasası[/caption]
[caption id="attachment_143782" align="aligncenter" width="286"]
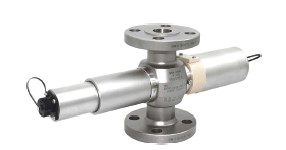
Şekil 3. In-line Spektrometre Örneği[/caption]
Işık kaynağı olan lamba modül ile dedektör modül arasındaki optik yol sabit ve ölçüm aralığına uygun olarak üretildiği için Beer-Lambert yasasına göre aynı analit için ışığın absorpsiyonu doğrudan analitin sıvı içerisindeki konsantrasyonu ile lineer bir ilişkide olmaktadır.
İlgili konsantrasyon, konsantrasyon birimi (CU) ya da absorpsiyon birimi (AU) şeklinde ortalama 0-5 aralığında takip edilebilmektedir. Bu ham veri görünür bölgede ise Lovibond, Saybolt ve benzeri renk birim sistemlerine dönüştürülebilmektedir ya da NIR bölgede ftu,
ppm gibi türbidite birimlerine matematiksel olarak dönüştürülebilmektedir.
Proses spektrometreleri, proses viskozimetreleriyle birlikte polimerizasyon reaksiyonlarında
asit sayısı ve viskozite takibinde kullanılabilmektedir. Örneğin, viskozite artarken asit sayısının azaldığı bir polimerizasyon düşünelim. Reaktöre monte edilen proses viskozimetresi ile viskozite artışını proses spektrometresi ile de asit sayısı takip edilebilmektedir.
Çünkü, 1200 ve 1700 nm’lerdeki C-H bölgesindeki piklerde çok değişim beklenmez iken 1410 nm’lerdeki -OH bölgesinde güçlü bir pik gözlemlenmesi beklenir.
Bu durum yüksek hidroksil sayısı, düşük asit sayısı demektir. 1410 nm dolaylarındaki pik takip edilerek asit sayısı değişimi takip edilebilir, kemometrik olarak bu değer asit sayısı için nümerik olarak da ifade edilebilir.
Polimer üretim süreçlerinde ve tesislerinde PAT kullanımı sadece polimerizasyon aşamasında değil aynı zamanda prosesin farklı aşamalarında da önemli avantajlar sağlar.
Mesela poliüretan ve ilgili hammadde üretim proseslerinde DNT ya da TDA gibi toksik olma
özelliği olan analitlerin kondensata ya da ısı değiştirici sistemlere sızıntısı ya da kaçağı da PAT araçları ile tespit edilebilir. Toluen içeriği olan bu aromatik türevi analitler UV absorbiyon ile inline olarak ölçülebilmektedir.
Bunun haricinde separasyon / filtrasyon gibi ayırma işlemlerinde ünite çıkışlarında ve girişlerinde NIR ve UV / VIS spektroskopi ile konsantrasyon/renk ya da bulanıklık ölçülerek separasyon kontrolü gerçekleştirilebilmektedir. Özet olarak, polimer endüstrisi gıdadan ambalaja kadar birçok endüstriye hitap ettiği için dünyadaki tüketim hızındaki artış ile paralel olarak büyümektedir.
Bu nedenle sınırlı hammaddelerin verimli kullanımı ihtiyacı ortaya çıkmaktadır. Bu, ancak verimlilik artışı ile sağlanabilecektir. Bu konuda dijitalleşmenin insan hatalarını ve kayıpları azaltacak şekilde kurgulanması süreçlerin ve buna bağlı olarak ürünlerin kalitesini ve
verimi arttıracaktır.
Bu konulara yapılacak yatırımlar ve PAT konusunda yapılacak modernizasyonlar hızlı geri
dönüş sağlayacak yatırımlar olacaktır.
Referanslar
1. FDA. Guidance for Industry PAT: A Framework for Innovative Pharmaceutical Development, Manufacuring, and Quality Assurance. FDA official document http://
www.fda.gov/cvm/guidance/published.html (2004) doi:http://www.fda.gov/CDER/guidance/6419fnl.pdf.
2. McLennan, F. & Kowalski, B. R. Process Analytical Chemistry. (Springer Netherlands, 1995).
3. Pell, R. J., Beth, M., Beebe, K. R. & Koch, M. V. Process analytical chemistry and chemometrics , Bruce Kowalski ’ s legacy at The Dow Chemical Company. 321–331 (2014) doi:10.1002/cem.2535.
4. Rathore, A. S., Bhambure, R. & Ghare, V. Process analytical technology (PAT) for biopharmaceutical products. Anal. Bioanal. Chem. 398, 137–154 (2010).
5. Callis, J. B., Illman, D. L. & Kowalski, B. R. Process Analytical. 59, (1987).
6. Mandenius, C. F. & Gustavsson, R. Mini-review: Soft sensors as means for PAT in the manufacture of bio-therapeutics. J. Chem. Technol. Biotechnol. 90, 215–227 (2015).
7. Workman, J., Koch, M. & Veitkamp, D. J. Process analytical chemistry. Anal. Chem. 75, 2859–2876 (2003).
8. Hinz, D. C. Process analytical technologies in the pharmaceutical industry: The FDA’s PAT initiative. Anal. Bioanal. Chem. 384, 1036–1042 (2006).
9. Read, E. K. et al. Process analytical technology (PAT) for biopharmaceutical products: Part I. Concepts and applications. Biotechnology and Bioengineering vol. 105 276–284 (2010).
10. MIVI, the versatile direct insertion viscometer and density-meter - Sofraser. https://www.sofraser.com/products/mivi-viscometer/.
11. Proses Viskozimetresi - Proses Analitik Teknolojiler. http://prosesviskozimetresi.com/.
12. Claßen, J., Aupert, F., Reardon, K. F., Solle, D. & Scheper, T. Spectroscopic sensors for in-line bioprocess monitoring in research and pharmaceutical industrial application. Anal. Bioanal. Chem. 409, 651–666 (2017).
13. Bakeev, K. A. Process Analytical Technology: Spectroscopic Tools and Implementation Strategies for the Chemical and Pharmaceutical Industries: Second Edition. Process Analytical Technology: Spectroscopic Tools and Implementation Strategies for the Chemical and Pharmaceutical Industries: Second Edition (John Wiley & Sons, Ltd, 2010). doi:10.1002/9780470689592.
14. Chemical Process Control Solutions. https://www.optek.com/en/chemical/applications.asp.
15. Bruder, S., Reifenrath, M., Thomik, T., Boles, E. & Herzog, K. Parallelised online biomass monitoring in shake flasks enables efficient strain and carbon source dependent growth characterisation of Saccharomyces cerevisiae. Microb. Cell Fact. 15, 127 (2016).
Dr. Hulki Özel
Satış ve Aplikasyon Müdürü
Pikolab Mühendislik