Su Bazlı Çinko Lamelli Kaplamanın Yay Parçaların Korozyon Performansı Üzerine Etkisi
Özet
Yapılan bu çalışmada, endüstride kullanılan farklı tipteki yayların su bazlı çinko lamelli kaplama ile kaplanabilirliği ve farklı katman sayısının yayların korozyon performansı üzerine etkisi incelenmiştir.
Kaplama çalışmasının kumlama basamağında, S20 (paslanmaz çelik bilya) kum kullanılmıştır. Gerçekleştirilen kumlama işlemi sonrasında yayların sarım aralıklarında doluluk uygunluk testi, Hogaboom testi ve kuru yapışma testi uygulanmıştır.
Sonraki deneysel çalışmalarda, iki farklı tipteki yaya su bazlı çinko lamelli kaplama işlemi uygulanmıştır. Bu aşamada ise, kaplamanın korozyon performansına etkisinin belirlenmesi
için 2 kat kaplanan yayların kaplama kaliteleri karşılaştırılmıştır.
Bu amaçla, kaplanmış yay örneklerinde kaplamanın yüzeye tutunup tutunmadığını belirlemek için kuru yapışma testi ve kaplama sonrası korozyon dayanımı performansını
ölçmek adına tuz sisi testi uygulanmıştır.
Kaplama sonrası uygulanan kuru yapışma testi sonuçlarına göre 2 kat kaplanmış sıkı sarımlı yaylarda sarım aralıklarında kısmen kaplama doluluğu gözlenmiştir. Bunun yanı sıra seyrek
sarımlı yay yüzeylerinde ve sarım aralarında kaplama doluluğu tespit edilmemiştir.
Yaylara uygulanan korozyon direnci testi sonuçlarına göre ise minimum 24 g/m2 kaplama ağırlığına sahip yayların yüksek korozyon direncine sahip olduğu belirlenmiştir.
1. Giriş
Korozyon, bir elementin düşük valans değerinden daha yüksek valans değerine dönüşmesidir. Altın ve platin dışında metallerin çoğu tabiatta oksit bileşikler halinde bulunur.
Kimyasal ve elektrokimyasal olmak üzere iki farklı korozyondan bahsedebilir (Campbell, 2008). Genel korozyon tüm yüzeyde metalin aynı derecede korozyona uğraması ile gerçekleşen elektrokimyasal korozyon türüdür.
Malzeme üzerinde tortu bırakmakta ve bu da malzeme ömrü hakkında bize kolayca bilgi vermektedir. Genelde çinko, kurşun ve alüminyumda gözlenmektedir. En yaygın korozyon türü olan homojen dağılımlı korozyonun yol açtığı metal kaybı diğer türlere oranla çok yüksektir.
Homojen dağılımlı korozyon farklı koruma yöntemleri uygulayarak kolaylıkla kontrol edilebilir (Kakani S. ve Kakani A., 2004).
Korozyondan korunma yöntemleri katodik korunma ve yüzey kaplamaları ile korunma olarak temelde ikiye ayrılır. Katodik koruma paslanan metallerin katot olarak polarizasyonunu gerektirir ve korunacak metali daha aktif bir metalle eşleyerek ya da dıştan akım verilerek gerçekleştirilebilir.
İlk yöntemde korunma için gereken akım, metal ve anot çiftinin oluşturduğu hücre tarafından üretilir. Anotlar korunma sırasında belirli hızlarda çözünerek ağırlıklarını kaybederler.
İkinci yöntemde ise metal ve anot çiftinin akım üretmesi gerekmez. Çünkü korunma için gereken akım dış kaynaktan sağlanır (Kakani S. ve Kakani A., 2004). Yüzey kaplama ile korunmada temel olarak üç çeşit kaplama tipinden bahsedilir. Bunlar organik, inorganik ve metalik kaplamalardır (Kakani S. ve Kakani A., 2004).
1980’lerde ve 1990’larda, bu kaplama sistemi yaygın olarak otomotiv endüstrisi içinde yüksek seviyede korozyon direnci sunan kaplama sistemlerine çözüm olarak kullanıma
başlanmıştır.
Çinko lamelli kaplamalar, işlemde herhangi bir hidrojen oluşturmadığından, elektro kaplama işlemine bir alternatif olarak kritik uygulamalar için kullanılmıştır. Kaplama sistemi, çelik yapıların ömrünü ve çalışma kapasitesini uzatabilecek en etkin korozyon önleyici önlemlerden biridir.
Organik kaplama veya metalik kaplama gibi birkaç farklı kaplama sistemi vardır ve bunlar arasında organik kaplamanın, örneğin çinko lamelli kaplamanın, davranışı kaplanmış parça üzerinde meydana gelen çizikler ve darbeler gibi yerel hasara karşı kendi kendini iyileştirme
özellikleri nedeniyle, korozyonun önlenmesinde çok etkilidir (Sugimura vd., 2016).
Günümüzde özellikle otomotiv sektöründe darbeye, sürtünmeye, kimyasal etkiye, korozyona maruz kalan malzeme tiplerinden yay, somun, bağlantı braketleri, kapı
menteşeleri, denge milleri, fren diskleri, debriyaj balata sistemleri vb. gibi birçok otomotiv parçalarında yaygın olarak kullanılan kaplama yöntemidir (Sugimura vd., 2016).
Yay, kuvvet etkisi altında büyük miktarlarda deformasyon gösteren ve bu deformasyon esnasında enerji biriktiren makine elemanıdır. Yaylar geniş bir kullanım alanına sahiptirler.
Yaylar, sistem içerisinde kuvvet uygulamak, hareketi kontrol etmek, sönümleme yapmak, frekans değiştirmek, kuvvet ve tork ölçmek gibi birçok görevi üstlenirler.
Bu özelliklerinden dolayı üretilen birçok ürünün vazgeçilmez elemanıdırlar. Metalden plastiklere birçok tip malzemeden imal edilirler. Yayların şekil ve yükleme karakteristikleri
ise kullanıldıkları uygulama alanlarına göre değişir.
Her şeyden önce yaylar, deformasyona uğradıklarında mekanik enerji biriktirmek için kullanılan elemanlardır. Bu sebeple iyi bir yay önemli derecede deformasyona uğrayabilmeli
ve herhangi bir boyutsal değişime uğramadan denge haline dönebilmelidir.
Mühendislik alanında hizmet veren tasarımcılar meslek hayatlarında çoğu kez yay tasarlamaya ihtiyaç duymaktadırlar. Çoğu zaman yayı tasarlamaya, tasarım proseslerinde
gerekli önem verilmese de dikkat edilmesi gereken en önemli elemanlardan birisidir.
Eğer kullanılan yay istenilen şekilde çalışmıyorsa üründen iyi bir netice alınmayacaktır.
Bu sebeple ürününü dizayn etmeden önce yay tasarımının doğru bir şekilde yapılması gerekmektedir.
Bu işlem ürünün maliyetini düşürüp, verimini arttıracaktır ve ürüne uzun bir çalışma ömrü sağlayacaktır. Yapılan bu çalışmada sıkı sarımlı ve seyrek sarımlı olmak üzere iki farklı tipteki yayın su bazlı çinko lamelli kaplama ile kaplanabilirliği ve kaplamanın yayların korozyon performansına etkisi incelenmiştir.
2. Materyal ve Metot
Çalışma kapsamında gerçekleştirilen su bazlı çinko lamelli kaplama işlemi yüzey hazırlama ve kaplama basamaklarını içermektedir.
2.1. Yüzey Hazırlama Basamağı
Numunelere çinko lamelli kaplama öncesi yüzey hazırlama işlemleri olarak yağ alma ve kumlama işlemi uygulanmıştır. Yağ alma işlemi için yaylar helezon yardımıyla yağ alma makinasından geçirilmiştir.
Bu makina üç bölmeli olup ilk bölümde alkali temizleme kimyasalı ile yay yüzeyindeki
yağ, püskürtme yöntemiyle temizlenmiştir (Çizelge 1). Daha sonra ikinci bölümde kimyasal kalıntısı olmaması için saf su püskürtülerek durulanmıştır.
Durulama işleminin ardından yaylarda nem kalmaması ve kumun diş aralarına dolmaması için 130°C sıcaklığındaki kurutma fırınında kurutulmuştur. Bu işlemler ile birlikte, yağdan
arınmış yaylar kumlama işlemi için hazır hale getirilmiştir.
Mekanik bir temizleme yöntemi olan kumlama işlemi ile metal yüzeyde kalabilecek tüm kimyasalların, metal çapaklarının ve daha öncesinde oluşabilecek pasların sökülerek,
çinko lamelli kaplamaya uygun bir hale getirilmesi amaçlanır.
Yağdan arındırılmış ve kurutulmuş yaylar iki farklı kum tipi olan S20 ve S70 kum tipi kullanılarak 12 dakika boyunca kumlanmış ve ardından yüzeyde toz kalıntısı kalmaması için ortamdaki hava ve toz fan yardımıyla ortamdan uzaklaştırılmıştır.
[caption id="attachment_133705" align="aligncenter" width="539"]
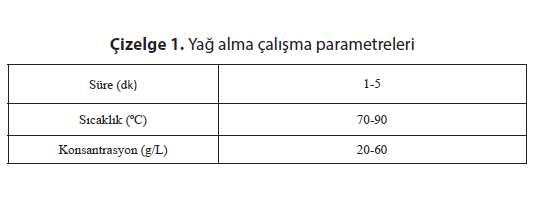
Çizelge 1. Yağ alma çalışma parametreleri[/caption]
2.2. Kaplama Öncesi Performans Testleri
Kaplama öncesi yüzey hazırlama basamağı olan kumlama sonrası yaylara sarım aralıkları doluluk uygunluk testi, Hogaboom testi ve yapışma testi uygulanmıştır. Öncelikle yaylar zirblast tozunun içerisine atılarak sarım aralıklarında kum kalıntısı olup olmadığı kontrol edilerek doluluk uygunluk testi gerçekleştirilmiştir.
Hogaboom testi ise kumlama işlemi sonrası metal yüzeyin lamelli kaplamaya uygun olup olmadığını tespit etmek amacıyla yapılan kontrol metodudur. Hogaboom çözeltisi hazırlanırken 30g bakır sülfat katısı 200 mL saf suda çözülür, üzerine 30 mL derişik sülfürik asit eklenir ve en son toplam hacim 1000 mL olacak şekilde saf su ile tamamlanır.
Test sırasında yaylar, behere alınan Hogaboom çözeltisinin içerisine tam olarak daldırılır, 15 s beklenir ve parça çözeltiden çıkarılır. Yapışma testi; kumlama makinesinden çıkan yayların yüzeyine yapışma bandının (3 M Nº610 çelik üzerine yapışma mukavemeti 47 N/100 mm) yüzeyde hava kalmayacak şekilde yapıştırılması ile gerçekleştirilmiştir.
Bant yapıştırılan yüzeylere 3M silecek ile üç kez aynı yönde basınç uygulanmış ve bant yüzeyden hızlı bir şekilde alttan yukarı doğru kuvvet uygulayarak kaldırılmıştır. Bantın yüzeyinde toz kalıntısı olup olmadığı yapışma testi skalasına göre incelenmiştir (Şekil 1).
2.3. Numunelerin Kaplanması
Kaplama süreci kaplama basamağıyla başlayıp, sırasıyla ön kurutma, pişirme ve soğutma basamaklarıyla devam eden bir işlemler zinciridir. Yapılan deneysel çalışmalar kapsamında, kaplama sayısının kaplama performansına etkisinin belirlenmesi için yaylar 2 gruba ayrılmıştır ve 15 adet yayın iki kat kaplanması işlemine başlanmıştır.
Daldırma metodu ile kaplanacak parçalar bir sepete yüklenmiştir. Yaylar sepetle birlikte kaplama kimyasalının bulunduğu tanka daldırılmıştır. Yüzeyi tamamen kaplandıktan
sonra kimyasal ortamdan alınmış ve yayların yüzeyindeki fazla kimyasalı uzaklaştırmak amacıyla santrifüj basamağına geçilmiştir.
Kaplama işleminde önemli bir basamak olan santrifüj işlemindeki santrifüj hızı 320 rpm ve santrifüj süresi de (30+30 saniye sağa ve sola) 60 saniye olarak sabit tutulmuştur. Santrifüj sonrası kaplanmış yaylar konveyör banda dökülüp önce 110°C sıcaklıktaki ön kurutma
fırınında 10 dk tutulmuş daha sonra kaplama kimyasalının kürlenmesi için aynı konveyör bant yardımı ile 45 dk süresince 320°C sıcaklıktaki pişirme (kürleme) fırınına alınmıştır.
Kürlenmenin ardından kaplı yayların yüzeyi 37°C olana kadar soğutma işlemi uygulanmış ve böylece parçaların ilk kat kaplama işlemi tamamlanmıştır. Her iki gruptaki parçalar bir kez daha aynı işleme tabi tutularak parçalara iki kat kaplama işlemi uygulanarak kaplama basamağı tamamlanmıştır.
Kaplama basamağına ait çalışma parametreleri Çizelge 2’de verilmiştir.
2.3. Kaplama Sonrası Performans Testleri
2 kat kaplanan iki farklı tipteki yayın kaplama kalitelerini belirlemek amacıyla önce örneklerin kaplama ağırlıkları ölçülmüştür. Ardından bu yay örneklerine kuru yapışma
testi ve tuz sisi testi yapılmıştır. Kaplama sonrası uygulanan kuru yapışma testi, kumlama sonrası uygulanan kuru yapışma testiyle aynı şekilde gerçekleştirilmiştir.
Tuz sisi testinde, kaplanan örnekler kütlece %5’lik sodyum klorür çözeltisinin sprey olarak uygulandığı tuz sisi kabin içerisine yerleştirilir. Kabin içerisinde sıcaklık 35°C ve nem oranı
ise %95’tir.
Test sonunda, bu ortama maruz bırakılan örneklerin yüzeyinde beyaz ve kırmızı pas oluşup oluşmadığı gözlemlenmiştir. Korozyon dayanımının iyi olduğu bir örnekte 480 saat ve 720 saat korozyon testi sonrası lekelenme, bozulma, çatlama, kırılma, şişme, pul şeklinde
dökülme, tabakalara ayrılma, boya yapışmasında kopma gibi yüzey bozuklukları olmamalıdır ve parça yüzeyinin en fazla %5’inde kırmızı pas oluşmalıdır.
3. Deneysel Sonuçlar ve Tartışma
3.1. Kaplama Öncesi Performans Test Sonuçları Yapılan deneysel çalışmalarda yağ alma ve kumlama işlemi kaplama öncesi yüzey hazırlığı aşaması olarak birinci ve ikinci gruptaki yaylara aynı şekilde uygulanmıştır.
S70 ve S20 kum ile kumlanmış yay ile yapılan kumlama işleminin ardından yaylar zirblast tozunun içerisine atılarak dişli bölgelerde kum kalıntısı olup olmadığı kontrol edilmiştir.
Her iki kum tipinde de sarımlar arası birikme kontrolü Şekil 2’ de görülmektedir.
[caption id="attachment_133953" align="aligncenter" width="448"]
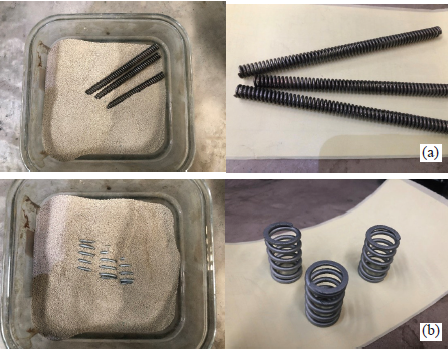
Şekil 2. Zirblast Testi Sonuçları (a) kumlanmış sıkı sarımlı yaylar (b) kumlanmış seyrek sarımlı yaylar[/caption]
Hogaboom testi uygulanan S70 ve S20 kum ile kumlanmış yayların test sonuçları Şekil 3’te verilmiştir. Yayların yüzeyinde homojen bir renk oluşumu gözlenmiş ve kumlanmış yayların kaplamaya elverişli olduğu belirlenmiştir.
[caption id="attachment_133957" align="aligncenter" width="429"]
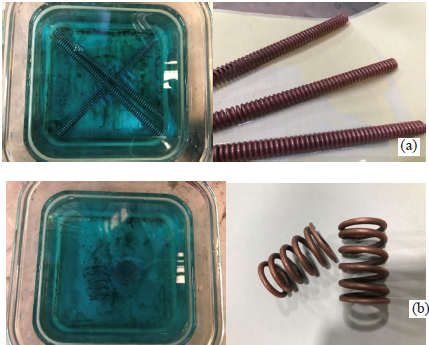
Şekil 3. Hogaboom Testi Sonuçları (a) S70 kum ile kumlanmış yaylar (b) S20 kum ile kumlanmış yaylar[/caption]
Farklı kum tipleri ile kumlanan yayların kuru yapışma test sonuçlarına göre yayların yüzeyinde herhangi bir kirlilik ya da kum tozu kalıntısı olmadığı görülmüştür (Şekil 4). Kaplama öncesi performans test sonuçlarına göre, S70 Kum ve S20 Kum ile kumlanan parçalar karşılaştırıldığında kayda değer bir farklılık gözlenmemiştir.
Fakat S20 paslanmaz çelik bilya olduğu için kumlama makinasının filtre bakımı açısından kullanımı daha uygun bulunmuştur.
[caption id="attachment_133960" align="aligncenter" width="451"]
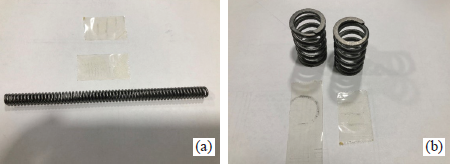
Şekil 4. Kumlama sonu kalıntı kontrolü sonuçları (a) sıkı sarımlı yay (b) seyrek sarımlı yay[/caption]
3.2. Kaplama Sonrası Performans Test Sonuçları
Çinko lamelli kaplama sonrası öncelikle örneklerin kaplama ağırlıkları ölçülmüştür. 2 kat kaplama yapılmış parçaların yüzeyinde sıkı sarılmış yaylar için sırası ile 24,6 g/m², 24,8 g/m² ve 25,6 g/m², 2 kat kaplama yapılmış seyrek yayların yüzeyinde ise sırası ile 26,8 g/m², 26,6 g/m² ve 27,1 g/ m² kaplama ağırlığı tespit edilmiştir.
2 kat kaplanmış farklı tipteki yaylara uygulanan kuru yapışma testi sonucunda kaplamanın yüzeye uygun tutunma sağladığı ve bant testiyle yüzeyden ayrılmadığı görülmüştür. Fakat sıkı sarımlı yaylarda sarım aralarında kaplama doluluğu gözlenmiştir (Şekil 5).
Yayların korozyona karşı dayanım performanslarını ölçmek amacıyla her iki tipteki yaya uygulanan tuz sisi testi sonucuna göre 2 kat kaplanan sıkı sarımlı yaylarda 480 saatte kırmızı pas, 2 kat kaplanmış seyrek sarımlı yaylarda ise 720 saatte kırmızı pas gözlenmemiştir (Çizelge 3).
[caption id="attachment_133963" align="aligncenter" width="570"]
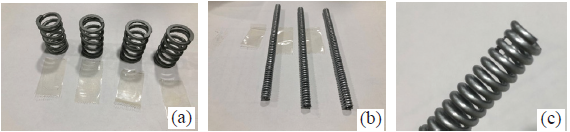
Şekil 5. Kaplama sonu kalıntı kontrolü (a) sıkı sarımlı yay (b) seyrek sarımlı yay (c) kaplama doluluğu[/caption]
[caption id="attachment_133964" align="aligncenter" width="501"]
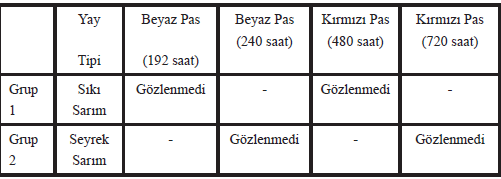
Çizelge 3. Kaplama Sonu Tuz Sisi Test Sonuçları[/caption]
[caption id="attachment_133966" align="aligncenter" width="555"]
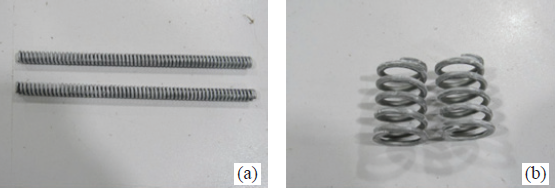
Şekil 6. Kaplama Sonu Tuz Sisi Uygulanan Yay Örnekleri (a) sıkı sarımlı yay 480 saat (b) seyrek sarımlı yay 720 saat[/caption]
4. Sonuçlar
Yağ alma işlemi yapılarak alkali kirliliği giderilmiş yaylar çapı 0,35 mm olan S20 ve S70 kum ile 12 Amper şiddetinde 12 dakika süre ile kumlanıp kumlama sonrası yüzey kontrolleri yapılmıştır.
S70 ve S20 kum tipi ile kumlanan yaylar karşılaştırıldığında performans test sonuçlarında
önemli farklar görülmemiş olup, S20 paslanmaz çelik bilya olduğu için kumlama makinasının filtre bakımı açısından bu kum tipinin kullanımı daha uygun bulunmuştur.
Kaplama işleminden sonra ölçülen kaplama ağırlıklarına göre, 2 kat kaplanan yayların kaplama ağırlıkları en az 24,6 g/m² ve 26,6 g/m² olarak belirlenmiştir. Birinci grup sıkı sarımlı yayların korozyon test sonucunda 192 saat sonunda beyaz pas ve 480 saat sonucunda kırmızı pas gözlenmemiştir.
İkinci grup seyrek sarımlı yaylarda ise 240 saat sonunda beyaz pas ve 720 saatte kırmızı pas gözlenmemiştir. Yapılan çalışmalar ve uygulanan testler, sıkı ve seyrek sarımlı yay malzemelerde dökme veya yığma usulü uygulanan ve çözücü içermeyen su bazlı lamelli kaplamanın kullanılabileceğini göstermektedir.
5. Kaynaklar
• Campbell, F.C. (2008). Elements of Metallurgy and Engineering Alloys, p. 323-549, ASM International, Materials Park, Ohio.
• FIAT 9.57513 (2017). ASTM B117 Korozyon Test Standardı.
• Kakani, S.L. ve Kakani, A. (2004). Material Science, p. 382-394, New Age International,
• Daryaganj, Delhi.
• Sugimura, S. & Liao, J. (2016). Long-term corrosion protection of arc spray Zn-Al-Si coating
• system in dilute chloride solutions and sulfate solutions. Surface & Coatings Technology, 302,
• 398-409
• Vu, T. N. (2012). Selective dissolution from Zn-Al alloy coatings on steel. Material chemistry.
• Universite Pierre et Marie Curie-Paris VI, (41)
• NOF METAL COATINGS GROUP. GEOMET 321/500 Technical manuel (EN). (2017)
Semih Ulubayrak
Ar-Ge Proses ve Kalite Mühendisi
Uzman Kataforez Yüzey Kaplama San. ve Tic. A.Ş.