Pigment Selection Criteria
Pigment producers and users apply different test methods during development and select pigments according to their purposes.
We will focus primarily on the criteria that manufacturers realize and emphasize. Although
users also do many of these tests, what these tests are, will be the subject of another article.
Principal tests applied by the pigment producers are:
• Surface area - BET and oil absorption,
• Dispersion,
• Rheology,
• Color shade and strength,
• Chemical resistance,
• Solvent resistance,
• Durability - internal and external,
• Overpaint fastness,
• Pigment stability - flocc, float, flooding,
• Gloss.
Let’s look at what they are in more detail: The most straightforward test that can be applied for the pigment surface area is the “Oil Absorption Test.” The “Rub out” test is to find out how much linseed oil is absorbed by 100 grams of pigment, and this means that
the less the amount, the better the flow.
• The BET (Brunauer Emmet Teller) value is determined for the Pigment Surface Area. Nitrogen absorbance is used to calculate the specific surface area.
This value is especially usable to predict how much additive necessary for the dispersion of the pigment.
• Another critical test is the determination of particle size distribution. The pigment particles in a pile are different sizes, from tiny to large.
When their distributions are examined, it is seen that they form a bell curve, and the peak where this bell curve is maximum gives information about the average particle size.
However, this bell curve can be leaning or narrower. Narrowness indicates that large
proportions of particles have average particle sizes.
• Another critical test is the study of the dispersion of the pigment.
In previous tests, the surface area, oil absorption values, and average particle size of
the pigment were determined, and the BET value of the pigment indicates estimating how much additive is needed for the dispersion.
When dispersing, the color strength of the paint film increases up to a specific value (preferably 100%). After this point, theoretically, each pigment particle is separated
from the other in the maximum possible ratio.
After reaching this maximum point, the color strength remains constant for a certain period.
However, after the dispersion time exceed a certain critical point, the color strength begins to go backward and tends to fall, and the color strength begins to weaken.
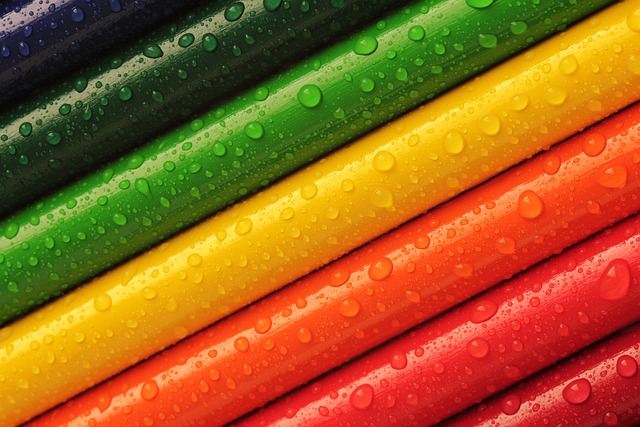
This test will show you how long it takes to achieve maximum color intensity and when not to maintain it. Keeping the dispersion time at an optimum level is essential for time-saving and energy-saving.
• After determining the optimum dispersion time, the next step is determining whether the pigment provides the desired rheology.
Rheology is the study of the flow and deformation of materials. Pigment added to a paint system irreversibly changes the rheological properties of the medium.
The commonly used term in this field is viscosity. Viscosity is the resistance, drag, or friction on many objects moving through a liquid or the resistance (due to the chemical attraction and physical shape of molecules) which hinders the flow of the liquid.
• The test applied in the next stage is the test of color shade and strength. This test can be done visually in the simplest way, but scientifically it should be determined through the Spectrophotometer.
The pigment is tested in a full tone without TiO2 and TiO2 in certain proportions according to the nature of use, and the color shade and intensity are determined.
• After the color measurement stage, the next test is to determine the chemical resistance of the paint film. This test is performed in both acidic and alkaline environments. According to this test’s results, the pigment’s suitability to the place of use is determined.
Just as important as chemical resistance is solvent resistance. It is crucial to predict the movement of the pigment in the dry film after the paint film is formed.
Most paint systems will contain solvents; the pigment is expected not to dissolve in these solvents. In addition, the pigments may tend to move in the paint film even though the system looks solid, this property is called bleeding, and it is an undesirable feature.
If this property is weak, the pigment can move into the paint film, which is applied to or
in contact with it.
• The most important feature when reaching the final stage is the determination of the pigment and whether it can maintain its color shade and strength in the environment where it is applied.
In determining this feature, common mistakes are usually made. Color is formed following the absorption and reflection of the visible wavelengths of the light coming from the sun or another illuminating light source onto the paint film.
It is mainly the absorbed visible light energies that destroy the pigment. For this reason, the rapid test method for this test is done with the WOM device, which emits the closest
visible light of the sunlight. However, many people use UV-CON devices, which are much cheaper, to test light fastness.
This equipment emits UV radiation and is not intended to test pigment resistance
but the polymeric materials that form the paint film. Polymeric materials are mainly destroyed by UV, and the effect of UV on pigments is much less than visible light.
The created paint film, which is tested in the WOM device, is subject to be tested in
different periods changing from 250 hours to 4000 hours depending on the place of the use of the paint.
Studies conducted in the natural environment and calculated visible light energy amounts show that approximately 1200 hours of WOM correspond to one year’s test of the open environment.
However, studies conducted in different parts of the world still show no 100% equivalence. Even if this equivalence is not precise, this test is the most reliable test of pigment and paint film durability.
Assoc. Prof. Dr. Gürses Öner
Regional Sales Manager – Türkiye
SUDARSHAN Chemical Industries Ltd.