Birçok polimer türüne kıyasla üstün fiziksel ve kimyasal özellikleri ile poliüretanlar (PU), günümüzde en çok tüketilen polimer türlerinden biri haline gelmiştir. Bu polimerlerin yaygın olarak kullanılan en önemli sınıflarından biri ise sert poliüretan köpüklerdir (SPK), çünkü düşük yoğunluk ve ısıl iletkenlikleri, güçlü mekanik özellikleriyle birleştiğinde onları mükemmel ısı ve ses yalıtım malzemeleri yapar.
Birçok polimer türünde olduğu gibi PU’ların üretiminde de petrokimyasal hammaddeler kullanılmaktadır. Günümüzde birçok araştırmacı ve endüstri kuruluşu, çevre konusundaki artan endişeler, petrolün hızla tükeniyor olması ve bunlarla ilgili her geçen gün artan kanuni düzenlemelerden dolayı PU’ların sürdürülebilirliğini artırmak için petrol temelli kaynakları yenilenebilir kaynaklarla değiştirmeye odaklanmıştır. Bu noktada biyokütle kaynakları en önemli alternatif malzemeler olarak karşımıza çıkmaktadır. PU’ların en önemli bileşenlerinden biri olan poliollerin çeşitli biyokütlelerden farklı kimyasal yaklaşımlarla sentezlenmesi kolay ve hızlı olmasına rağmen, halen geliştirilmesi ve yeni alternatiflerin oluşturulması gereken çok önemli bir konudur.
Günümüzde polimerlerin büyük çoğunluğu petrol temelli hammaddelerden üretilmektedir. Petrol temelli polimerler, kimyasal olarak dayanıklı bir yapıya sahip oldukları için doğada uzun süre bozulmadan/parçalanmadan kalabilmekte ve bu da çevre için büyük bir atık problemi oluşturmaktadır. Petrol kaynaklarının hızlı bir şekilde tükenmesi ve gelecekte yaşanacak kıtlığı da ayrı bir sorun teşkil etmektedir. Bu problemlerden dolayı araştırmacılar, tükenmekte olan petrolden elde edilen hammaddelerin yerine geçebilecek ucuz ve devamlılığı olan kaynaklar aramaya başlamışlardır. Bu arayış, doğal biyokütleleri her geçen gün daha popüler hale getirmiştir ve bunların gelecekte petrol türevi hammaddelerin yerini alabileceği düşünülmektedir [1].
Biyokütleler, kimya sanayisi için umut verici yenilenebilir kaynakların başında gelmektedir. Bunlar, biyolojik olarak kolaylıkla ve kirletici/zehirli bileşenler açığa çıkarmaksızın parçalanabilmelerinin yanı sıra bol ve ucuz olmalarıyla da ön plana çıkmaktadırlar [2]. Özellikle tarımsal gıda ve ormancılık endüstrileri tarafından üretilen ve düşük ekonomik etkiye sahip biyokütleler, polimerik malzemelerin üretimi için önemli bir kaynak olarak görülmektedir. Biyokütle kullanımının yenilenemeyen petrokimyasal ürünlerin kullanımını azaltmak ve biyobozunurluğu artırmanın yanısıra sera gaz emisyonunu azaltmak, üretim maliyetlerini düşürmek ve elde edilen ürünün fiziko-mekanik özelliklerini artırmak gibi ilave avantajları da vardır [3].
Katı ve gaz fazlarından oluşan poliüretan köpükler, düşük ısıl iletkenlik, yüksek mekanik mukavemet, düşük yoğunluk gibi üstün özelliklerinden dolayı başta ambalajlama, yalıtım, kaplama, biyomedikal ve otomotiv sektörleri olmak üzere farklı endüstriyel alanlarda tercih edilen mühendislik malzemeleridir [4, 5]. 2015 yılında 100 milyar Dolar’dan fazla olan polimerik köpük pazarının, 2021 yılında yaklaşık 122,4 milyar Dolar’lık hacme ulaşacağı tahmin edilmektedir [6]. Polimerik köpükler arasında endüstriyel ve evsel amaçlar için en yaygın olarak kullanılanı ise PU köpüklerdir. PU köpüklerin dünya genelinde tüketiminin 2024 yılında yaklaşık 92 milyar Dolar’a ulaşacağı tahmin edilmektedir [7].
Üretan ilk kez 1849 yılında Wurtz tarafından sentezlenmiştir fakat o zamanlarda işe yaramaz olarak düşünülmüştür. Sonrasında, 1937 yılında Dr. Otto Bayer tarafından bir poliester diol ile bir izosiyanat arasındaki reaksiyondan PU sentezlenmiştir (Şekil 1) [8]. PU’ların kimyasal yapıları, her uygulama için özeldir, fakat temelde tüm PU’lar, -OH grupları içeren polioller ile -N=C=O grupları içeren izosiyanatlar arasındaki poliadisyon adı verilen bir polimerizasyon reaksiyonu sonucunda oluşan yüksek molekül kütleli polimerlerdir [9]. PU’lar kullanım alanlarına göre, sert, esnek, termoplastik, kaplama, yapıştırıcı gibi birçok farklı gruba ayrılabilirler [10].
[caption id="attachment_104240" align="aligncenter" width="594"]
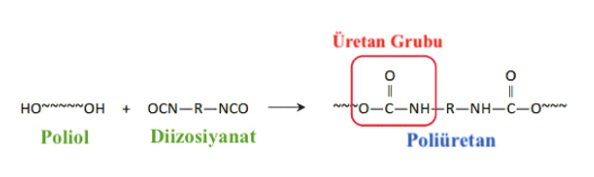
Şekil 1. Poliüretan oluşum reaksiyonu[/caption]
Dünya poliüretan tüketiminin büyük bir kısmını oluşturan sert poliüretan köpükler (SPK), bir polimerik diizosiyanat bileşiği (örneğin polimerik metilen difenil diizosiyanat, pMDI) ile içerisinde şişirici gaz, katalizör ve yüzey aktif madde bulunan bir poliolün (formülize poliol, FP) reaksiyonu sonucu kendi hacminin 30-40 katına şişmesiyle oluşurlar [11]. İçerisinde ısıl iletkenliği düşük şişirici gaz moleküllerinin hapsedildiği kapalı hücresel yapıları sayesinde SPK’lar, dünyadaki en iyi ısı yalıtım malzemelerinden birisidir. Köpük formülasyonundaki ham madde türleri ve miktarları, köpüğün hem uygulama alanını hem de özelliklerini belirler. Esnek ve sert poliüretan köpükler temelde benzer bir kimyaya sahip olmalarına rağmen, özelliklerindeki farklılıklar onları oluşturan bileşenlerin özellikle poliollerin ve izosiyanatların nitelikleriyle doğrudan ilişkilidir [12].
Polioller, nihai ürünün fiziko-mekanik özelliklerinin belirlenmesinde büyük önem taşırlar. Köpüğün sertliği veya esnekliği, kimyasal direnci ile gaz ve nem geçirgenlik dereceleri büyük ölçüde kullanılan poliol tarafından belirlenmektedir. Poliollerin hidroksil sayıları, işlevsellikleri ve ortalama molekül kütleleri gibi üç temel özellik genellikle köpüklerin son özelliklerini etkileyen en önemli parametrelerdir. Örneğin, molekül kütlesi değiştirilmeden yüksek hidroksil sayısına sahip bir poliol kullanılırsa, köpüğün sertliği, boyutsal kararlılığı ve ısı kararlılığı artarken, çekme ve uzama mukavemet özelliklerinde ufak azalmalar gözlenir [10].
Köpüklerin en az poliol kadar önemli olan diğer bir bileşeni ise izosiyanatlardır. En çok kullanılan izosiyanat türleri metilen difenil diizosiyanat (MDI) ve toluen diizosiyanattır (TDI). Güneş ışığı altında sararmaya karşı dirençli olan hekzametilen diizosiyanat (HDI), kaplama ve yapıştırıcı endüstrisinde kullanılırken, TDI ve MDI’lara göre daha az reaktif olmasından dolayı köpük endüstrisinde tercih edilmez. Köpük formülasyonunda sırasıyla 2 ve 2,7’lik ortalama işlevselliğe sahip olan petrol temelli TDI ve polimerik MDI (pMDI) kullanılmaktadır. Kapalı hücre yapılarına sahip SPK uygulamalarında genellikle TDI’a göre daha kontrollü bir reaksiyon kinetiği sağladığı için pMDI’lar tercih edilir.
TDI’lar ise daha çok açık hücre yapısına sahip esnek köpük üretiminde tercih edilirler [13]. pMDI sağlık açısından TDI’a göre daha zararsız olmasına rağmen, diizosiyanatların hassas bireylerde çok düşük konsantrasyonlarda bile astıma neden olduğu toksikolojik çalışmalar sonucunda tespit edilmiştir [14]. Bu durum izosiyanat kullanımı ile ilgili en azından bazı kısıtlamaların olabileceğini göstermekte, dolayısıyla alternatif izosiyanat sentez yöntemlerinin geliştirilmesi her geçen gün önem kazanmaktadır [15].
Köpüklerin hücresel yapılarının oluşmasını sağlayan şişirici ajanlar şişirme mekanizmalarına göre iki ana gruba ayrılabilirler: (i) Kimyasal ve (ii) fiziksel şişirici ajanlar. Kimyasal şişirici ajan olarak kullanılan su, izosiyanat bileşiği ile reaksiyona girerek kararsız bir karbamik asit bileşiği oluşturur. Poliol ve izosiyanat arasındaki reaksiyon sayesinde açığa çıkan ısının da yardımı ile bu karbamik asit bileşiği bir amin bileşiğine dönüşürken karbondioksit gazı açığa çıkarır (Şekil 2).
Karbondioksit gazı, reaksiyon süresince artan ortam viskozitesi nedeniyle ortamdan uzaklaşamaz ve köpük yapısını oluşturur. Fiziksel şişirici ajanlar ise kloroflorokarbonlar, hidrokloroflorokarbonlar, bazı alkan veya sikloalkanlar gibi düşük kaynama noktasına ve düşük molekül kütlesine sahip bileşiklerdir. Reaksiyon sürecinde açığa çıkan ısı ile birlikte fiziksel şişirici ajanın hızla buharlaşması, köpük oluşumunda yürütücü kuvvettir. Fakat, klor ve flor içerikli bileşiklerin ozon tabakasını inceltme potansiyeli çok fazla olduğu için 1987 yılında Montreal protokolü ile kullanımları yasaklanmıştır. Bundan sonra da SPK endüstrisi, siklopentan, izopentan ve su gibi ozon inceltme potansiyeli sıfır olan şişirici ajanlara yönelmiştir.
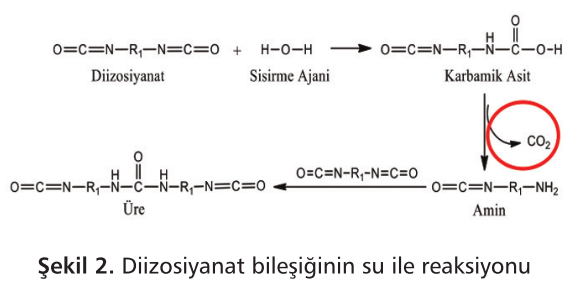
Ucuz olması, kolay bulunabilmesi ve zararsız olması suyu şişirici ajan olarak avantajlı hale getirmektedir. Fakat fiziksel şişirici gaz kullanarak şişirilen SPK’lar, su kullanılarak şişirilenlere göre daha düşük ısıl iletkenlik katsayısına sahip olduklarından ısı yalıtım performansları da yüksek olur. Bununla birlikte bu malzemeler içerisindeki parlama noktası düşük şişirici gazdan dolayı bir yangın durumunda çok daha kolay alev alabilirler.
Yüzey aktif maddeler, küçük oranlarda kullanılmalarına rağmen, köpükleşme reaksiyonunda oluşan gaz kabarcıklarının dağılımlarının ve boyutlarının hem kontrolünde hem de stabilizasyonunda rol oynayan diğer önemli bileşenlerdir. Tipik bir yüzey aktif madde, omurgasında silikon içeren bir kopolimerdir. Yüzey aktif maddeler; birbirleri içerisinde çözünmeyen sıvıların karışmasını (emülsifikasyon), karışımları sırasında hava kabarcıklarının oluşmasını, şişen köpüğün jelleşme süresine kadar çekirdeklenmesini ve köpüğün stabilizasyonunu sağlama gibi önemli işlevleri vardır [16, 17].
Katalizörler kullanımı ile reaksiyonun hızlı bir şekilde gerçekleşmesi ve şişirici gazın yapıdan uzaklaşma fırsatı bulamadan hücrelerin içinde kalmasını sağlanır. Köpük oluşumunda su-izosiyanat arasındaki reaksiyondan sorumlu amin bileşikleri (1,4-diazobisiklo [2.2.2]-oktan) [18] ve jelleşmeden (polimerizasyondan) sorumlu metal kompleksleri (dibütil kalay dilaurat) [19] en çok tercih edilen katalizörlerdir. İyi bir köpük yapısı elde etmek için bu iki bileşiğin belli oranlarda birlikte kullanılması tavsiye edilmektedir. Diizosiyanatlar arasında meydana gelen trimerizasyon reaksiyonları ise yüksek sıcaklıkta meydana gelmektedir. Bu reaksiyonlar için ana katalizör aileleri ise karboksilat türevleri ve kuarterner amonyum tuzlarıdır [20].
Birçok polimer endüstrisinde olduğu gibi SPK endüstrisinin de temel bileşenler poliol ve izosiyanat, ağırlıklı olarak petrol temelli ham maddeler kullanılarak üretilmektedir. Yenilenebilir biyokütlelerden polimer üretimi için hammadde eldesi hem akademi hem de endüstride büyük ilgi görmektedir. Bu malzemelerin kullanımına olan ilginin artması, büyük bir pazara sahip olan SPK’ların üretiminde yeşil ve biyo temelli polioller gibi yenilenebilir ve uzun vadede sürdürülebilir ürünlerin kullanımının artmasına neden olmuştur. Biyo kaynaklardan üretilen polioller:
(i) Düşük karbon emisyonları,
(ii) Geri dönüştürülebilir olmaları,
(iii) Çevreyi kirletmeyen kaynaklardan
(iv) Doğada hızlı parçalanabilir/bozulabilir olmaları, (v)
elde edilmiş olmaları, Ucuz olmaları,
(vi) Bol bulunmaları gibi üstün avantajlarıyla
ön plana çıkmaktadırlar.
Bu ilginin sonucu olarak, 2021 yılında yeşil ve biyo temelli poliol pazarının 4,7 milyar Dolar’a ulaşması beklenmektedir [21]. Diğer yandan, Dow Chemical, Bayer Material Science, BASF, Huntsman, DuPont ve Shell Chemicals Ltd. gibi dünya devi şirketler bu tür poliolleri uzun süredir ticarileştirmektedirler [22, 23]. Bunun yanında, son 10 yıldır akademik çalışmalar büyük oranda biyokütle artıklarından, bitkisel yağlardan ve endüstriyel yan ürünlerden ekopoliol üretimine yönelmiştir. [24-28]. Şekil 3’te biyolojik kaynaklardan ekopoliol eldesi ve bu ekopolioller ile SPK üretimine ilişkin yıllara göre bilimsel yayın sayısı verilmiştir. Akademinin bu alana ilgisinin özellikle son 5 yılda hızla arttığı grafikten rahatça görülebilmektedir.
[caption id="attachment_104242" align="aligncenter" width="498"]
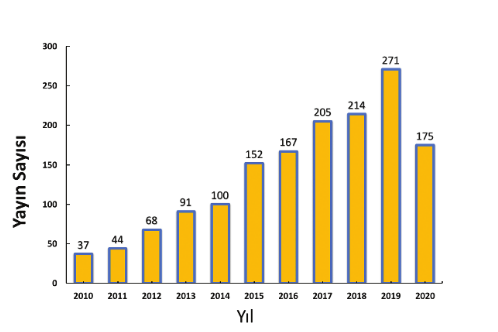
Şekil 3. Biyolojik kaynaklardan ekopolioller ve PU köpük eldesine yönelik yayın sayısının yıllara göre değişimi[/caption]
Yemeklik yağlar, tarım ve ormancılık endüstrisi sonrasında oluşan lignoselülozik biyokütleler gibi yenilenebilir kaynaklardan ekopoliol elde etmek için kapsamlı çalışmalar yıllardır sürdürülmektedir. Bu kaynaklardan verimli bir şekilde ekopolioller üretilebilmesine rağmen, üretim aşamalarındaki fazla enerji ve zaman sarfiyatından dolayı yeni, kolay ve hızlı yöntemlerin geliştirilmesine ihtiyaç duyulmaktadır.
PU endüstrisinde lignoselülozik biyokütleleri kullanarak ekopoliol elde etmek için kullanılan iki temel yöntem vardır; bunlar asitle sıvılaştırma [29] ve oksipropilasyon [30] yöntemleridir. Oksipropilasyon yöntemi, temel olarak, propilen oksit içerisindeki biyokütlenin bazik bir katalizör varlığında ve basınç altında ısıtılması esasına dayanır [31]. Oksipropilasyon, poliüretan köpüklerin üretiminde alternatif ekopoliollerin sentezlenmesi için uygun bir yöntem olmasına rağmen, propilen oksit gibi kolay alev alabilen, ciddi derecede toksik ve kanser yapıcı bir reaktant kullanılması bu yönteme olan ilgiyi azaltmaktadır.
Ayrıca, bu yöntemde çok hızlı ve kontrolsüz ekzotermik polimerizasyonların neden olduğu patlamalara önlem olarak yatırım maliyetlerini arttıran çelik reaktörler kullanılması gerekmektedir [32]. Bu nedenlerden dolayı bir biyokütleyi poliole dönüştürmek için başka bir işlem kullanmak daha güvenli olacaktır. Asit ile sıvılaştırma yöntemi çok daha ilgi çekici bir alternatiftir, çünkü bu yöntemde propilen oksit gibi zararlı reaktantlar kullanılmadığı gibi, yüksek basınç gibi tehlikeli reaksiyon koşullarına da ihtiyaç yoktur. Asit ile sıvılaştırma yönteminde kullanılan çözücüler kozmetik sektöründe dahi kullanılan biyolojik olarak uyumlu maddelerdir.
Ayrıca, oksipropilasyon yöntemi hidroksil sayısını arttırmayıp işlevselliği arttırmakta ve elde edilen ekopolioller çoğunlukla daha yüksek viskozite değerlerine sahip olmaktadırlar. Asitle sıvılaştırma yönteminde ise yüksek hidroksil sayısına sahip sıvılaştırılmış ürünler elde edilir ve yüksek hidroksil sayısı da SPK eldesi için çok önemlidir [33].
Çevre dostu PU köpük malzemeleri geliştirmek için ekopoliol üretiminde kullanılan diğer yenilenebilir kaynaklar ise yemeklik yağlardır. Yemeklik yağlar, temelde, kaynaklarının bolluğu ve çeşitliliği sayesinde PU köpük üretimi için önemli bir hammadde olan trigliseritler ve uzun zincirli yağ asitlerinden oluşurlar (Şekil 4) [34]. Bu yağların birçok avantajı vardır:
(i) Çok yönlü bileşimlere ve yapılara sahiptirler,
(ii) Kolay parçalanabilirler,
(iii) Çevre dostudurlar,
(iv) Birçok endüstriyel çözücü içerisinde çözünebildikleri için petrokimyasal temelli polioller ile karışıma izin verirler, (v) Ayrıca, bu yağlardan elde edilen köpükler, esneklik, mekanik mukavemet, aşınma direnci, tokluk, yapışma, kimyasal ve korozyon dirençleri açısından iyi özellikler sergilerler [35].
[caption id="attachment_104243" align="aligncenter" width="467"]
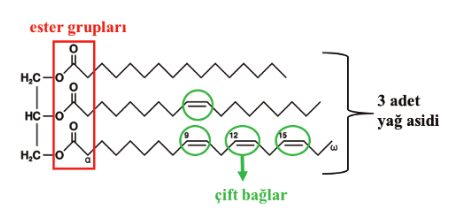
Şekil 4. Yağın trigliserit yapısı[/caption]
Hint yağı ve lesquerella yağları hariç, yemeklik yağlar izosiyanatlar ile reaksiyona girebilecek hidroksil gruplarını içermemektedirler. Bu nedenle yemeklik yağlar ile doğrudan PU sentezlemek imkansızdır [36]. Ayrıca, yemeklik yağların öncelikli kullanım alanı ekopoliol elde etmek değil yemek pişirmektir. Bu sebeple yemeklik yağlardan ekopoliol üretimi, gıda üretimi ile rekabet edememektedir.
Yemeklik yağlar, poliol üretimi için hammadde olarak kullanılmak istendiğinde, kimyasal olarak modifiye edilip yapılarına hidroksil gruplarını koymak gerekir. Karbon-karbon çift bağları ve ester bağları, bitkisel yağların yapılarında bulunan iki önemli fonksiyonel gruptur. Bitkisel yağ temelli poliol elde etmek için bu iki fonksiyonel grubun birinden başlayan bazı sentetik yöntemler vardır: (i) Epoksidasyon sonrası oksiran halka açılması, (ii) hidroformilasyon sonrası hidrojenasyon, (iii) ozonoliz, (iv) tiyol-en bağlanması, (v) transesterifikasyon ve (vi) amidasyon [37].
Epoksidasyon, karbon-karbon bağının fonksiyonelleştirilmesi için kullanılan en yaygın yöntemlerden biridir [38, 39]. Epoksidasyon reaksiyonları kullanılarak soya fasulyesi, kolza tohumu, keten tohumu, zeytin, mısır, aspir, karanja, kavun tohumu ve pamuk tohumu yağları gibi birçok yağ türü ile endüstriyel ölçekte ekopoliol üretimi gerçekleştirilmiştir [35]. Epoksidasyon, genellikle hammadde tipine ve reaktant oranına göre 30 ile 80°C arasındaki bir sıcaklıkta ve 5-20 saat arasındaki reaksiyon sürelerinde gerçekleştirilir [40]. Optimize edilmiş koşullar altında, %90’dan daha yüksek dönüşüm verimleri elde edilebilir. Epoksidasyon reaksiyonundan sonra, polioller, alkoller, inorganik ve organik asitler, aminler ve su gibi aktif hidrojen içeren bileşikler kullanılarak oksiran halka açma reaksiyonları ile epoksitlenmiş bitkisel yağlardan ekopolioller elde edilir [39-41].
Biyolojik malzemelerden SPK’lar elde edilirken karşılaşılan en büyük problem, petrol temelli poliollerden elde edilenlere göre, fiziko-mekanik özelliklerindeki azalmalardır. Elde edilen SPK’ların özelliklerindeki düşüşlerin önüne geçmek için literatürde birçok farklı strateji uygulandığı görülmektedir. Bunlar basitçe aşağıdaki gibi sıralanabilirler:
(i) Düşük hidroksil sayısında elde edilen ekopoliollere, gliserin gibi yüksek hidroksil sayısına sahip bir çapraz bağlayıcı ekleyerek SPK’ların sertliğini artırmak [42],
(ii) Elde edilen ekopoliollerin hidroksil sayılarını arttırmak için bir takım kimyasal modifikasyonlar uygulamak [43],
(iii) Elde edilen ekopoliolleri ticari petrol temelli polioller ile harmanlamak [44, 45],
(iv) Elde edilen ekopoliol ile en iyi fiziko-mekanik özellikleri verecek SPK için izosiyanat oranı, katalizör, yüzey aktif madde ve şişirici ajan türlerini ve miktarlarını çeşitlendirerek formülasyon çalışması yapmak [46, 47],
(v) Çeşitli nitelikte katkı/dolgu maddeleri ile SPK kompozitler oluşturmak [48-50].
Yemeklik yağlar, lignoselülozik biyokütleler ve benzeri biyolojik malzemeler son yıllarda endüstriyel açıdan önemli bir hale gelmekle birlikte kendilerine pek çok farklı uygulama alanı bulmuşlardır. Son yıllarda ise biyolojik kaynaklardan poliüretan malzemelerin elde edilmesi hem ekolojik açıdan hem de ekonomik açıdan son derece önemli hale gelmiştir. Hem akademi hem de endüstri kuruluşları petrol temelli poliolleri biyolojik kaynaklardan elde edilen poliolleri ile değiştirmeye odaklanmışlardır.
Biyolojik malzemeler bol bulunması ve ucuz olmalarına rağmen, bunlardan poliüretan malzemelerin elde edilmesi bazı zorluklar içermektedir. Bu zorlukların en büyüğü ise ticarileşmeye çalışan ekopoliollerin ekonomik olmayan kimyasal süreçlere sahip olmamasıdır. Yeşil malzemeler çok ilgi çekici olsalar da çoğu tüketici yeşil etiketli ürünler için fazladan ücret ödemeye istekli değildir. Bu yüzden bunların üretim maliyetlerini düşürecek yeni teknolojilerin geliştirilmesi elzemdir.
Referanslar
[1] J. Zhang, N. Hori, A. Takemura, Optimization of agricultural wastes liquefaction process and preparing bio-based polyurethane foams by the obtained polyols, Industrial Crops and Products, 138 (2019) 111455. [2] B. Soares, N. Gama, C. Freire, A. Barros-Timmons, I.s. Brandão, R. Silva, C. Pascoal Neto, A. Ferreira, Ecopolyol production from industrial cork powder via acid liquefaction using polyhydric alcohols, ACS Sustainable Chemistry & Engineering, 2 (2014) 846-854. [3] S. Członka, M.F. Bertino, K. Strzelec, Rigid polyurethane foams reinforced with industrial potato protein, Polymer Testing, 68 (2018) 135-145. [4] S.-T. Lee, C.B. Park, N.S. Ramesh, Polymeric foams: science and technology, CRC press2006. [5] E. Akdogan, M. Erdem, M.E. Ureyen, M. Kaya, Rigid polyurethane foams with halogen-free flame retardants: Thermal insulation, mechanical, and flame retardant properties, Journal of Applied Polymer Science, 137 (2020) 47611. [6] S. Rapra, The Future of High Performance Polymer Foams to 2021, Smithers Rapra: Shawbury, UK, (2020). [7] G.V. Research, Polyurethane (PU) Foam Market Share, Size & Trend Analysis Report By Product (Rigid Foam, Flexible Foam), By Application And Segment Forecasts To 2024. [8] E. Sharmin, F. Zafar, Polyurethane: An introduction, InTech, London, UK, 2012. [9] E. Akdogan, M. Erdem, M.E. Ureyen, M. Kaya, Synergistic effects of expandable graphite and ammonium pentaborate octahydrate on the flame-retardant, thermal insulation, and mechanical properties of rigid polyurethane foam, Polymer Composites, (2020). [10] M. Szycher, Szycher’s handbook of polyurethanes, CRC press, New York, NY, USA, 2006. [11] N.V. Gama, A. Ferreira, A. Barros-Timmons, Polyurethane foams: Past, present, and future, Materials, 11 (2018) 1841. [12] J.O. Akindoyo, M. Beg, S. Ghazali, M. Islam, N. Jeyaratnam, A. Yuvaraj, Polyurethane types, synthesis and applications–a review, Rsc Advances, 6 (2016) 114453-114482. [13] P. Furtwengler, L. Avérous, Renewable polyols for advanced polyurethane foams from diverse biomass resources, Polymer Chemistry, 9 (2018) 4258-4287. [14] D.C. Allport, D.S. Gilbert, S. Outterside, MDI and TDI: safety, health and the environment: a source book and practical guide, John Wiley & Sons, New York, NY, USA, 2003. [15] G. Çaylı, S. Küsefoğlu, Biobased polyisocyanates from plant oil triglycerides: Synthesis, polymerization, and characterization, Journal of applied polymer science, 109 (2008) 29482955. [16] H. Lim, S. Kim, B. Kim, Effects of silicon surfactant in rigid polyurethane foams, Express polymer letters, 2 (2008) 194200. [17] M.S. Han, S.J. Choi, J.M. Kim, Y.H. Kim, W.N. Kim, H.S. Lee, J.Y. Sung, Effects of silicone surfactant on the cell size and thermal conductivity of rigid polyurethane foams by environmentally friendly blowing agents, Macromolecular research, 17 (2009) 44-50. [18] F. Schuster, F.N. Ngamgoue, T. Goetz, T. Hirth, A. Weber, M. Bach, Investigations of a catalyst system regarding the foamability of polyurethanes for reactive inkjet printing, Journal
Prof. Dr. Murat Erdem
Eskişehir Teknik Üniversitesi
Fen Fakültesi Kimya Bölümü
Araş. Gör. Emre Akdoğan
Eskişehir Teknik Üniversitesi
Fen Fakültesi Kimya Bölümü