Giriş
Dünya nüfusu gün geçtikçe artarken bu nüfusun yaşam ihtiyaçlarını gidermek üzere kullandığı sınırlı doğal kaynaklar ise önemli ölçüde azalmaktadır.
Enerji insanlığın en temel ihtiyaçlarından biri olup artan nüfusa ve gelişen teknolojilere bağlı olarak gerek endüstriyel, gerekse evsel uygulamalarda enerji ihtiyacı artan bir ivmeye sahiptir.
Bu nedenle de enerjinin verimli kullanılması, yenilenebilir enerji kaynakları, düşük enerjiyle çalışan makine ve sistemler geliştirilmesi gibi konular gündemimizdeki yerini korumaktadır.
Günümüzde yeni ve yenilenebilir enerji kaynaklarının araştırılması kadar önemli olan bir diğer araştırma alanı ise mevcut enerji kaynaklarının olabildiğince verimli kullanılmasıyla ilgilidir.
Ülkemizde binalardaki toplam enerji tüketiminin yaklaşık %85 gibi önemli bir kısmı mevsime bağlı olarak ısıtma ve soğutma amacıyla harcanmaktadır. Yalıtımsız veya kötü yalıtılmış duvarlardan kaynaklanan enerji kaybı ise %50 gibi çok yüksek değerlere ulaşabilmektedir.
Bu durum yalıtımın ne derece önemli olduğunu açık bir şekilde ortaya koymaktadır. Yüksek enerji tüketimi, sebep olduğu önemli ekonomik kaybın yanı sıra hava kirliliği, sera gazı emisyonlarında artış ve çevreye zarar verilmesi gibi önemli diğer sorunları da beraberinde getirmektedir.
Binalarda iyi bir yalıtım sağlanamaması durumunda kış döneminde ısıtma sağlamak amacıyla, yaz döneminde ise tam tersi soğutma sağlamak amacıyla aşırı bir enerji tüketimi söz konusudur.
Binalarda dört mevsim ısıtma ve soğutma amacıyla kullanılmakta olan enerjinin en az seviyelere çekilebilmesi için iyi bir yalıtım yapılması gerekmektedir.
Binalarda verimli ısı yalıtım malzemesi uygulamalarıyla çok önemli oranlarda enerji tasarrufu sağlanması ve bu yolla hem ülke ekonomisine ciddi bir katkı sağlanması hem de daha az enerji sarf edilmesi ile çevreye daha az zarar verilmesi mümkündür.
Bina yalıtım uygulamalarında kullanılmakta olan malzemeler genel olarak inorganik ve organik olmak üzere iki temel grup altında toplanmaktadır.
İnorganik malzemelerin sahip olduğu önemli avantajlar; A sınıfı yanmaz özellik göstermeleri, oldukça düşük ısıl iletkenlik sayısına sahip olmaları (0,030-0,045 W/m.K), geniş bir sıcaklık aralığında (-100−7500C arasında) kullanım imkanı sunmaları ve neme karşı organik malzemelere kıyasla daha yüksek dayanıma sahip olmalarıdır.
İnorganik malzemeler arasında yaygın olarak köpük veya fiber−yün şeklinde cam veya taş olarak adlandırılan seramik esaslı malzemeler kullanılmaktadır. Avrupa pazarına bakıldığında bu gruptaki malzemelerin payının %60 olduğu, polistiren, poliüretan gibi organik malzemelerin payının ise %27’de kaldığı görülmektedir.
Fiber inorganik malzeme kullanımında karşılaşılan en önemli sorun ince fiber malzemelerinin kanserojen etkisidir. Bu nedenle inorganik fiberlerin uygulama ve kullanım sırasında sağlık açısından önemli bir risk oluşturma potansiyeli bulunmaktadır.
Köpük inorganik malzemelerin kullanımıyla bu risk ortadan kalkmaktadır. Kalsiyum silikat, genleşme gösteren kil agregası, perlit, vermikülit gibi malzemeler kullanılan inorganik seramik köpük malzemelere örnektir.
Son on yılda ise kapalı hücresel paneller, vakum yalıtım panelleri, gaz dolgulu paneller, aerojeller ve faz değişimi gösteren malzemeler yalıtım sektöründeki yenilikçi uygulamalar olarak göze çarpmaktadır.
Kapalı hücresel paneller, cam yününe kıyasla %40’lık bir kalınlık azalması sağlarken, ısı yalıtım performansında herhangi bir fark görülmemektedir.
Artan nüfus ve gelişen endüstriler ile birlikte ortaya çıkan büyük miktarlardaki katı evsel ve endüstriyel atıklar da günümüzde önemli bir sorun olarak karşımıza çıkmaktadır.
Bu durum dünyamızın sınırlı doğal kaynaklarının verimli kullanımını engellediği gibi önemli çevre sorunlarına da sebep olmaktadır. Bu nedenle günümüz koşullarında katı atıkların yeni ürünlere dönüştürülmesi önemli bir ihtiyaç olarak karşımıza çıkmaktadır.
Kırmızı Çamur Nedir?
Kırmızı çamur Bayer prosesiyle alümina üretim sürecinde ortaya çıkan ve karmaşık bir yapıya sahip olan bir endüstriyel katı atıktır. Alümina üretiminde kullanılan boksit mineralinin kostik soda ile liç işlemi sırasında genellikle 1 ton alümina üretim sürecinde 1–1,5 ton kırmızı çamur açığa çıkmaktadır.
[1] Alümina ise pek çok farklı endüstriyel uygulama alanında kullanımının yanı sıra alüminyum metalinin üretiminde de kullanılmaktadır. Bir ton alüminyum metalinin üretimi için yaklaşık iki ton alümina kullanılmaktadır.
Demir dışı metal endüstrisinde en yaygın kullanıma sahip olan alüminyum dünyada çok büyük miktarlarda üretime sahiptir. Alüminyum ve alümina üreten tesisler için ortaya çıkan çok miktardaki kırmızı çamurun depolanması oldukça büyük bir sorun teşkil etmektedir.
[2] Alümina ve alüminyum üretim sürecinde çok miktarda kırmızı çamur atık olarak ortaya çıkmakta ancak bu atığın sadece yaklaşık %10 gibi oldukça düşük bir kısmı farklı uygulama alanlarında kullanılmaktadır. [3]
Kırmızı çamurun çimento [4-6], beton [7-9], jeopolimer [10], seramik [11-15] ürünlerin üretimi, değerli metallerin geri kazanımı (Fe, Ni, Ti ve Si gibi) [16-18], organik kirleticilerin [19], boyaların [20, 21], kurşun [22], kadmiyum, bakır, arsenik gibi toksik diğer kirleticilerin [23-26] sudan uzaklaştırılması gibi farklı uygulama alanlarında kullanımına yönelik olarak gerçekleştirilmekte olan bilimsel çalışmalar yoğun olarak devam etmektedir.
Bu konuda ülkemizde de özellikle kırmızı çamurun karakterizasyonu ve seramik sektöründe kullanımına yönelik çok sayıda bilimsel araştırma çalışmaları yapılmaktadır. [4, 10, 13, 14, 19, 20, 23-25, 27-32]
Kırmızı çamurun bileşimi sabit olmamakla birlikte içerisinde genel olarak yüksek oranda Fe2O3 (%30−60), yanı sıra Al2O3 (%5−20), SiO2 (%1−20), Na2O (%1−10) ve TiO2 (eser − %10) bulunmaktadır.
Bunların yanı sıra kırmızı çamurda eser miktarlarda baryum, bakır, sodyum, vanadyum, krom, nikel, kurşun, mangan, potasyum ve çinko gibi farklı safsızlıklar da yer alabilmektedir. Kırmızı çamur içerisinde yer almakta olan yüksek miktarlardaki alkali içeriği ekosisteme önemli zararlar vermektedir.
Özellikle de toprağa ve yeraltı sularına karışması ciddi sorunlara neden olmaktadır.
[33] Bu nedenle kırmızı çamurun yalıtım sektörü gibi büyük ticari hacme sahip uygulama alanlarında değerlendirilmesi hem doğal kaynakların verimli kullanılması adına, hem de endüstriyel üretimlerden kaynaklı çevreye verilen zararın en aza indirilmesi adına oldukça önemlidir.
Yalıtım Sektöründe Seramik Köpük Malzemelerin Kullanımı
Seramik köpük malzemeler sahip oldukları hafiflik, yüksek gözenek miktarı, yüksek yüzey alanı, düşük ısıl iletkenlik, iyi ısıl şok direnci ve yüksek kimyasal direnç gibi mükemmel özellikleri nedeniyle ısıl ve akustik yalıtım uygulamalarında önemli bir kullanım potansiyeline sahip değerli bir malzeme grubu olarak karşımıza çıkmaktadır.
Yalıtım sektöründe kullanılmakta olan polimer esaslı köpüklerle kıyaslandığında seramik esaslı köpük malzemelerin daha yüksek mekanik, kimyasal ve ısıl kararlılığa sahip oldukları görülmektedir.
[34] Bir yangın çıkması durumunda, yalıtım amaçlı kullanılan polimerik köpüklerin yangın esnasında açığa çıkan toksik gazlardan büyük ölçüde zarar gördüğü bilinirken, seramik ve cam−seramik köpükler, inorganik doğaları nedeniyle yanıcı değildir. [35]
Cam seramik köpüklerin üretilmesi 1930’larda erimiş hammaddelerin içerisine gazların gönderilmesiyle gerçekleştirilmiş olup bu yöntem günümüzde pek tercih edilmemektedir. Günümüzde gözenekli seramik ve cam−seramik üretimi için pek çok farklı üretim yöntemi kullanılabilmektedir.
Gözenekli seramiklerin üretilmesi için en basit üretim yöntemlerinden biri köpükleştirici maddelerin ilavesiyle birlikte başlangıç tozlarının sinterlenmesidir. Köpürtme ilavelerinin sisteme katılmasıyla yüksek sıcaklıklarda meydana gelen reaksiyonlar sırasında gaz oluşumu sağlanarak yapıda istenen gözeneklilik sağlanmaktadır.
[36] Sinterleme sırasında, köpürme oksidasyon veya bozunma etkisi ile sağlanabilmektedir. Örneğin karbon esaslı köpükleştirici maddeler örneğin grafit, karbon siyahı, kömür, SiC vb. oksidasyona uğramakta ve bu süreçte meydana gelen gaz çıkışları sayesinde yapıda gözenek oluşumu sağlanmaktadır.
Diğer taraftan karbonatlar (Na2CO3, CaCO3, MgCO3, vb.) veya sülfatlar (CaSO4, alçıtaşı) gibi minerallerin bozunma sürecinde açığa çıkan gazlar nedeniyle yapıda gözeneklilik sağlanabilmektedir.
Kırmızı Çamur Kullanılarak Seramik Esaslı Köpüklerin Üretimi
Seramik ve cam−seramik köpük malzemelerin pek çok farklı başlangıç malzemeleri ve farklı yöntemler kullanılarak üretilmesi mümkündür.
Literatür incelendiğinde endüstriyel üretim süreçlerinde bir katı atık olarak karşımıza çıkan kırmızı çamurun özellikle son yıllarda seramik ve cam−seramik köpük malzemelerin üretiminde kullanılmasına yönelik bilimsel çalışmalarda belirgin bir artış söz konusudur. [34, 37-44]
Guo ve arkadaşları [34] başlangıç malzemesi olarak kırmızı çamur ve uçucu kül ile birlikte CaCO3 köpürtme ilavesi kullanarak sinterleme yöntemiyle cam− seramik köpük malzemeler üretmiştir.
Bu çalışmada kırmızı çamur/uçucu kül oranının 2:3’ü geçmediği bileşimlerde, düşük sinterleme sıcaklıklarında (760–840 °C) oldukça düşük yoğunluğa (0,33–0,41 g/cm3) sahip köpük malzemelerin üretilebildiği belirlenmiştir.
Üretim sürecinde uygulanan sinterleme sıcaklığı ve süresi gibi süreç değişkenlerinin köpüklerin basma mukavemeti üzerinde oldukça etkili olduğu belirlenmiştir. Süreç değişkenlerine bağlı olarak 0,33–2,74 MPa basma mukavemeti değerleri elde edilmiştir.
Chen ve arkadaşları [43] sinterleme yöntemi ile ana hammadde olarak uçucu kül ve kırmızı çamur kullanarak köpük seramikler üretmiştir. Bileşimde sinterlemeyi kolaylaştırmak için az miktarda sodyum borat ve köpükleştirmeyi sağlamak için ise sodyum silikat kullanmışlardır.
Gerçekleştirilen çalışmada kırmızı çamur/ uçucu kül ve sodyum borat oranı ile sinterleme sıcaklığının üretilen köpüklerin mukavemet, yığınsal yoğunluk, su absorpsiyonu, mikroyapı ve kristalin faz bileşimine etkileri incelenmiştir.
[43] Elde edilen sonuçlar %40−50 kırmızı çamur, %26,25−40 uçucu kül, %15−20 sodyum borat ve %5 sodyum silikat bileşiminde 9000C’de iki saat sinterleme sonucunda büyük gözeneklerden oluşan homojen bir mikro yapının elde edildiğini ortaya koymuştur.
Bu köpüklerin gözenek miktarının %64,14−74,15 olduğu, basma mukavemetinin 4,04−10,63 MPa, eğme mukavemetinin 2,31−8,52 MPa, yığınsal yoğunluğunun 0,51−0,64 g/cm3 ve su emme değerinin %2,31−6,02 olduğu bildirilmektedir. [43]
Şekil 1. A1 (%40 kırmızı çamur, %40 uçucu kül), A2 (%50 kırmızı çamur, %30 uçucu kül) ve A3 (%60 kırmızı
çamur, %20 uçucu kül) numunelerinin taramalı elektron mikroskobu görüntüleri. [43]
Hou ve arkadaşları [44] yaptıkları çalışmada ana hammadde olarak uçucu kül ve kırmızı çamur, sinterleme ilavesi olarak sodyum borat ve köpükleştirici ilave olarak nişasta ve MnO2 kullanarak sinterleme (10000C, 2 saat) yöntemiyle seramik köpük malzemeler (Şekil 2 ve Şekil 3) üretmiştir.
Gerçekleştirilen çalışma sonucunda artan köpükleştirici ilavesiyle basma mukavemeti değerinin de arttığı belirlenmiştir.
Elde edilen genel özellikler; 0,59-0,96 g/cm3 yığınsal yoğunluk, %3,16−9,17 su absorpsiyonu, 4,22−8,38 MPa basma mukavemeti, 2,44−5,82 MPa eğme mukavemeti, %95,59−%99,60 asit dayanımı, %99,82−%99,99 alkali dayanımı.[44] Elde edilen bu özellikler nedeniyle üretilen köpüklerin yapı sektöründe kullanım potansiyeli olduğu bildirilmektedir. [44]
Şekil 2. (a) %1, (b) %5 ve (c) %15 oranında nişasta içeren köpük numunelere
ait taramalı elektron mikroskobu görüntüleri. [44]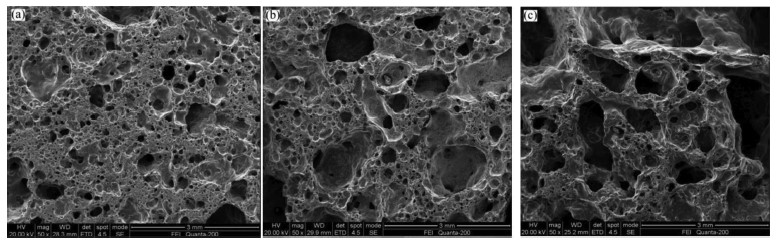
Şekil 3. (a) %1, (b) %5 ve (c) %15 oranında MnO2 içeren köpük numunelere ait
taramalı elektron mikroskobu görüntüleri. [44]
Liu ve arkadaşları [3] tarafından ana hammadde olarak kurşun−çinko maden atıkları, silika kumu ve kırmızı çamur kullanılarak, sinterleme yöntemiyle farklı sinterleme sıcaklıklarında üretilen seramik köpükler Şekil 4’te sunulmaktadır.
Bu çalışmada farklı gözenek oluşum mekanizmalarıyla çok miktarda kapalı gözenek oluşumunun meydana geldiği belirlenmiştir. Liu ve arkadaşları [3] tarafından gerçekleştirilen çalışmada 9700C’de sinterlenmiş olan seramik köpüğün yoğunluğu 0,56 g/cm3, gözenek miktarı %76, eğme mukavemeti 5,3 MPa ve ısıl iletkenliği 0,21 W/(m K) olarak belirlenmiştir.
Sahip olduğu yüksek gözenek miktarı ve düşük ısıl iletkenliği nedeniyle bu köpüklerin ısıl yalıtım amaçlı kullanılabilecekleri bildirilmektedir.
Şekil 4. (a) 9000C, (b) 9500C ve (c) 10000C’de sinterlenen numunelere ait taramalı elektron mikroskobu görüntüleri. [3]
Genel Değerlendirme
•Kırmızı çamur, uçucu kül gibi farklı katı atıklar ile birlikte kullanılarak yalıtım sektöründe değerlendirilmek üzere seramik ve cam− seramik köpük malzemelerin üretiminde kullanılabilecek ekonomik bir ana hammaddedir.
•Bu tür köpük seramiklerin sinterleme gibi çok kolay uygulanabilen ve ekonomik bir yöntem ile düşük sıcaklıklarda ve hava ortamında üretimi gerçekleştirilebilir.
•Ülkemizde de sorun olarak görülen kırmızı çamur, uçucu kül, curuf ve mermer atığı gibi farklı katı atıkların yapı sektörü gibi büyük ve hızla gelişen bir sektörde yalıtım malzemesi üretiminde kullanılması ülkemiz ekonomisine önemli katkılar sağlama potansiyeline sahiptir.
•Ayrıca bu tür uygulamalar ile mevcut koşullarda endüstriyel katı atıkların ekosisteme verdiği zararı en aza indirmek mümkün
olacaktır.
Dr. Öğretim Üyesi Ayşe Kalemtaş
Metalurji ve Malzeme Mühendisliği Bölümü
Mühendislik ve Doğa Bilimleri Fakültesi
Bursa Teknik Üniversitesi
Kaynaklar
[1] C. Brunori, C. Cremisini, P. Massanisso, V. Pinto, L. Torricelli, Reuse of a treated red mud bauxite waste: studies on
environmental compatibility, Journal of Hazardous Materials, 117 (2005) 55-63.
[2] S. Kumar, R. Kumar, A. Bandopadhyay, Innovative methodologies for the utilisation of wastes from metallurgical and allied
industries, Resources, Conservation and Recycling, 48 (2006) 301-314.
[3] T. Liu, X. Li, L. Guan, P. Liu, T. Wu, Z. Li, A. Lu, Low-cost and environment-friendly ceramic foams made from lead–zinc mine
tailings and red mud: Foaming mechanism, physical, mechanical and chemical properties, Ceramics International, 42 (2016)
1733-1739.
[4] T. Kavas, G.N. Angelopoulos, R.I. Iacobescu, Production of belite cement using boron and red mud wastes, Cem Wapno
Beton, 20 (2015) 328-+.
[5] D.V. Ribeiro, J.A. Labrincha, M.R. Morelli, Potential Use of Natural Red Mud as Pozzolan for Portland Cement, Mater Res-
Ibero-Am J, 14 (2011) 60-66.
[6] R.C.O. Romano, H.M. Bernardo, M.H. Maciel, R.G. Pileggi, M.A. Cincotto, Hydration of Portland cement with red mud as
mineral addition, J Therm Anal Calorim, 131 (2018) 2477-2490.
[7] W.C. Tang, Z. Wang, Y. Liu, H.Z. Cui, Influence of red mudon fresh and hardened properties of self-compacting concrete,
Constr Build Mater, 178 (2018) 288-300.
[8] D.R.C. de Oliveira, C.R.C. Rossi, Concretes with Red Mud Coarse Aggregates, Mater Res-Ibero-Am J, 15 (2012) 333-340.
[9] K. Kohno, K. Amo, Y. Ogawa, M. Gyotoku, Properties of mortar and concrete using red mud and finely ground silica, Amer
Conc I, 153 (1995) 1103-1120.
[10] K. Kaya, S. Soyer-Uzun, Evolution of structural characteristics and compressive strength in red mud-metakaolin based
geopolymer systems, Ceramics International, 42 (2016) 7406-7413.
[11] M.P. Babisk, T.P. Altoe, H.J.D. Lopes, U.S. do Prado, M.C.B. Gadioli, S.N. Monteiro, C.M.F. Vieira, Properties of Clay Ceramic
Incorporated with Red Mud, Mater Sci Forum, 798-799 (2014) 509-+.
[12] M.P. Kolesnikova, S.S. Saigofarov, E.A. Nikonenko, I.I. Kalinichenko, T.P. Kochneva, N.A. Surkova, The use of red mud for
brick coloring, Glass Ceram+, 55 (1998) 70-71.
[13] B. Karasu, E. Agun, G. Kaya, Effects of red mud based pigments on wall and floor tile glazes, Cfi-Ceram Forum Int, 82 (2005)
E41-E44.
[14] B. Karasu, M. Caki, E. Akgun, G. Kaya, Effects of the red mud based pigment addition on the physical and micro-structural
properties of porcelain tiles, Euro Ceramics Viii, Pts 1-3, 264-268 (2004) 1613-1616.
[15] C.S. Hu, X. Wang, Using Red Mud Manufacturing Building Glass-ceramics, Applied Materials and Technologies for Modern
Manufacturing, Pts 1-4, 423-426 (2013) 1014-1017.
[16] A.P. He, Z.L. Hu, D.G. Cao, J.M. Zeng, B.L. Wu, L.J. Wang, Extraction of Valuable metals from Red Mud, Chemical, Material
and Metallurgical Engineering Iii, Pts 1-3, 881-883 (2014) 667-+.
[17] M. Isshiki, K. Igaki, Winning of High-Purity Iron from Red Mud and Iron Concentrated Tailing, T Jpn I Met, 22 (1981) 418-422.
[18] T. Kasai, T. Mizota, K. Takahashi, Waste Materials Utilization of Red Mud from Bayer Process, Recovery of Rare Metals and
Zeolite - Synthesis, First International Conference on Processing Materials for Properties, (1993) 165-168.
[19] S. Aydin, Removal of Organophosphorus Pesticides from Aqueous Solution by Magnetic Fe3O4/Red Mud-Nanoparticles,
Water Environ Res, 88 (2016) 2275-2284.
[20] O. Kazak, Y.R. Eker, I. Akin, H. Bingol, A. Tor, A novel red mud@sucrose based carbon composite: Preparation,
characterization and its adsorption performance toward methylene blue in aqueous solution, J Environ Chem Eng, 5 (2017)
2639-2647.
[21] V.K. Gupta, Suhas, I. Ali, V.K. Saini, Removal of rhodamine B, fast green, and methylene blue from wastewater using red
mudan aluminum industry waste, Ind Eng Chem Res, 43 (2004) 1740-1747.
[22] A.N. Babu, G.V.K. Mohan, K. Kalpana, K. Ravindhranath, Removal of Lead from Water Using Calcium Alginate Beads Doped
with Hydrazine Sulphate-Activated Red Mud as Adsorbent, J Anal Methods Chem, (2017).
[23] R. Apak, K. Guclu, M.H. Turgut, Modeling of copper(II), cadmium(II), and lead(II) adsorption on red mud, J Colloid Interf Sci,
203 (1998) 122-130.
[24] R. Apak, G. Atun, K. Guclu, E. Tutem, G. Keskin, Sorptive Removal of Cesium-137 and Sr-90 from Water by Unconventional
Sorbents .1. Usage of Bauxite Wastes (Red Muds), J Nucl Sci Technol, 32 (1995) 1008-1017.
[25] Z. Katircioglu, S. Dursun, M.S. Yavuz, Fabrication of magnetic nanoparticles from red mud for arsenic removal, Abstr Pap
Am Chem S, 252 (2016).
[26] S.H. Ju, S.D. Lu, J.H. Peng, L.B. Zhang, C. Srinivasakannan, S.H. Guo, W. Li, Removal of cadmium from aqueous solutions
using red mud granulated with cement, T Nonferr Metal Soc, 22 (2012) 3140-3146.
[27] S. Arslan, G.K. Demir, B. Celikel, M. Baygul, C.E. Suarez, Eti Aluminum Red Mud Characterization and Processing, Light Met,
(2012) 81-85.
[28] G. Atun, G. Hisarli, A study of surface properties of red mud by potentiometric method, J Colloid Interf Sci, 228 (2000) 40-45.
[29] R. Apak, E. Tutem, M. Hugul, J. Hizal, Heavy metal cation retention by unconventional sorbents (red muds and fly ashes),
Water Res, 32 (1998) 430-440.
[30] A. Atasoy, An investigation on characterization and thermal analysis of the Aughinish red mud, J Therm Anal Calorim, 81
(2005) 357-361.
[31] T. Kavas, Use of boron waste as a fluxing agent in production of red mud brick, Build Environ, 41 (2006) 1779-1783.
[32] Y. Kilic, E. Gunay, M. Marsoglu, From Hazardous Red Mud Waste to Non-Hazardous Commercial Products, Mater Test, 56
(2014) 140-144.
[33] N. Zhang, H. Sun, X. Liu, J. Zhang, Early-age characteristics of red mud–coal gangue cementitious material, Journal of
Hazardous Materials, 167 (2009) 927-932.
[34] Y. Guo, Y. Zhang, H. Huang, K. Meng, K. Hu, P. Hu, X. Wang, Z. Zhang, X. Meng, Novel glass ceramic foams materials based
on red mud, Ceramics International, 40 (2014) 6677-6683.
[35] E. Bernardo, R. Cedro, M. Florean, S. Hreglich, Reutilization and stabilization of wastes by the production of glass foams,
Ceramics International, 33 (2007) 963-968.
[36] J.P. Wu, A.R. Boccaccini, P.D. Lee, M.J. Kershaw, R.D. Rawlings, Glass ceramic foams from coal ash and waste glass:
production and characterisation, Adv Appl Ceram, 105 (2006) 32-39.
[37] T.Y. Liu, X.Y. Li, L.M. Guan, P.A. Liu, T. Wu, Z. Li, A.X. Lu, Low-cost and environment-friendly ceramic foams made from
lead-zinc mine tailings and red mud: Foaming mechanism, physical, mechanical and chemical properties, Ceramics International,
42 (2016) 1733-1739.
[38] T.Y. Liu, Y. Tang, Z. Li, T. Wu, A.X. Lu, Red mud and fly ash incorporation for lightweight foamed ceramics using lead-zinc
mine tailings as foaming agent, Mater Lett, 183 (2016) 362-364.
[39] Z.N. Ye, Y.W. Wang, H. Jiang, N. Li, S.Q. Liu, Foamed glass-ceramics made from red-mud, Key Eng Mater, 575-576 (2014)
461-464.
[40] X.J. Chen, A.X. Lu, G. Qu, Preparation and characterization of foam ceramics from red mud and fly ash using sodium silicate
as foaming agent, Ceramics International, 39 (2013) 1923-1929.
[41] Y.X. Guo, Y.H. Zhang, H.W. Huang, K. Meng, K.R. Hu, P. Hu, X.K. Wang, Z.L. Zhang, X.H. Meng, Novel glass ceramic foams
materials based on red mud, Ceramics International, 40 (2014) 6677-6683.
[42] L.J. Hou, T.Y. Liu, A.X. Lu, Red mud and fly ash-based ceramic foams using starch and manganese dioxide as foaming agent,
T Nonferr Metal Soc, 27 (2017) 591-598.
[43] X. Chen, A. Lu, G. Qu, Preparation and characterization of foam ceramics from red mud and fly ash using sodium silicate as
foaming agent, Ceramics International, 39 (2013) 1923-1929.
[44] L.-j. Hou, T.-y. Liu, A.-x. Lu, Red mud and fly ash-based ceramic foams using starch and manganese dioxide as foaming
agent, T Nonferr Metal Soc, 27 (2017) 591-598.