1.Titanium Dioxide (TiO2)
Titanium dioxide (TiO2) is the most important white pigment used in the coatings industry. It is used to give whiteness and hiding power, also called opacity, to coatings, inks, and plastics. The reason for this is two-fold:
• TiO2 particles of the right size scatter visible light, having wavelength λ ≈ 380 - 700 nm (nanometer), effectively because TiO2 has a high refractive index (RI=2.73).
• It is white because it does not absorb visible light.
Titanium dioxide is commercially available in two crystal structures-anatase and rutile. Rutile TiO2 pigments are preferred because they scatter light more efficiently, are more stable and are more durable than anatase pigments.
On the other hand, the pigment is expensive, especially when volume prices of systems are used. Most paint and ink companies buy raw materials per weight and sell their products by volume. As TiO2 has a relatively high density, ρ ≈ 4 g/cm3, the raw material contributes
substantially to the volume price of a system.
To understand why TiO2 and especially rutile TiO2 offer such great advantages in hiding, it is only necessary to compare the refractive indices of rutile and anatase with those of other commercial white pigments and paint vehicles (Table 1). The larger the difference between
the refractive index of the pigment and that of the medium in which it is dispersed, the greater the refractive light scattering.
[caption id="attachment_130601" align="aligncenter" width="367"]
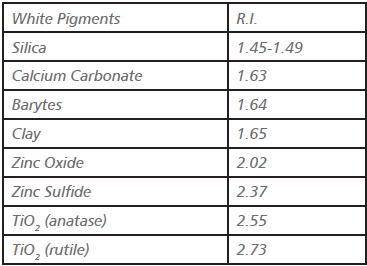
R.I. = speed of light-in-vacuum / speed of light-insubstance[/caption]
2. Production of TiO2 Pigment
A few processes are used to produce TiO2 pigment. Rutile TiO2 is found in nature (naturally). This is because the rutile crystal structure is the thermodynamically stable form of titanium dioxide. In chemical processes natural TiO2 can be purified, thus obtaining synthetic TiO2. The pigment can be made from ores, rich in titanium, that are mined from the earth.
Two chemical routes are used to make both rutile and anatase TiO2 pigments.
2.1. Sulfate Process
The sulfate method was commercialized in 1931, producing anatase TiO2 and later (1941) rutile TiO2. In this process, the titanium-rich ore is reacted with sulfuric acid (H2SO4), giving TiOSO4. Pure TiO2 is obtained from TiOSO4 in several steps, going via TiO(OH)2. Depending on the chemistry and route chosen, either rutile or anatase TiO2 is made. The crystal structure, anatase or rutile, is controlled by nucleation and calcination (Fig.1).
[caption id="attachment_130602" align="aligncenter" width="764"]
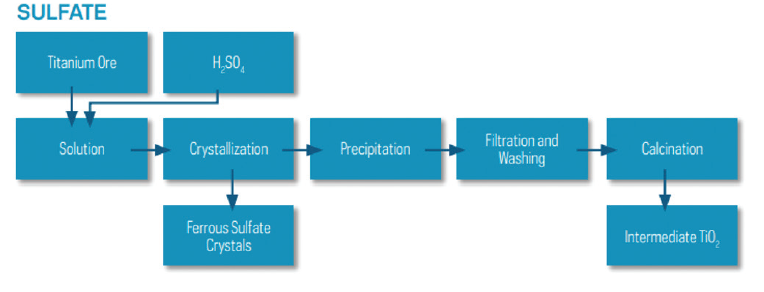
Fig. 1. Sulfate process flowsheet[/caption]
2.2. Chloride Process
The chloride method was commercialized by DuPont (USA) in the 1950s to produce rutile TiO2 and is now owned by the Chemours Company (USA). In this process, crude titanium-rich starting material is purified by converting titanium to titanium tetrachloride (TiCl4) by using chlorine gas (Cl2).
The titanium tetrachloride is then oxidized at high temperature, giving pure rutile titanium dioxide (Fig.2). Anatase TiO2 is not made via the chloride process.
[caption id="attachment_130603" align="aligncenter" width="739"]
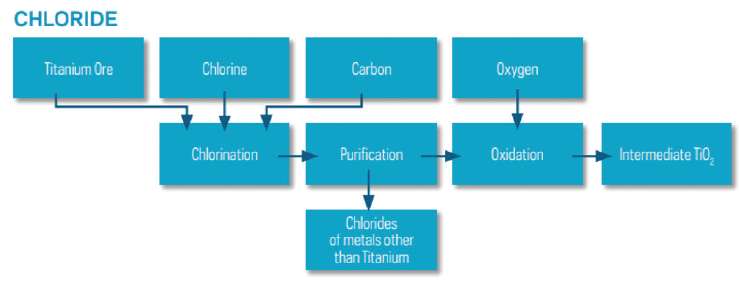
Fig. 2. Chloride process flowsheet[/caption]
In both processes, the size of the pigment particles as well as the post-treatment is adjusted by fine-tuning the final steps in the chemical route.
3. Ways to Optimize the Use of Titanium Dioxide for Paints
3.1. Optimize the Dispersion Process
Each primary TiO2 particle has to be used as efficiently as possible. TiO2 pigment scatters light most efficiently when all particles are separated from each and distributed over the system (Fig.3).
[caption id="attachment_130604" align="aligncenter" width="656"]

Fig. 3. Dispersion process: separation and stabilization of solid particles in a liquid[/caption]
A challenge in this respect is that solid particles attract each other strongly. This has two implications:
1.A lot of work must be done to separate the particles from each other during the dispersion process.
Separation is done by using high-energy dispersion equipment like:
• Disk disperser (often called dissolver) or
• Pearl mill.
The shear forces in a dissolver set-up are too weak to separate all primary pigment particles from one another. More complete separation is obtained by using a pearl mill.
2.The particles must be stabilized against flocculation. That is, the spontaneous gluing together of solid particles in a liquid caused by the attractive forces between the particles. Stabilization against flocculation is obtained by adsorbing a stabilizer, called dispersant, at the surface of the solid particles immediately after particles have been separated from each other.
The dispersant assures that the particles repel each other. Thus, particles remain separated from each other. Two mechanisms can be used for this; Electrostatic stabilization: It results when all particles have an identical electrostatic charge.
Steric stabilization: It results from polymeric tails, being part of the dispersant molecules, that dissolve in the liquid continuous phase surrounding the particles.
3.2. Distribute the Particles
The scattering efficiency of expensive titanium dioxide pigment is maximized when all primary particles are separated from each other, stabilized against flocculation and distributed over the complete system.
The distance between the individual pigment particles should be as large as possible. It is said that the pigment particles must be spaced in the system (Fig.4).
[caption id="attachment_130605" align="aligncenter" width="614"]
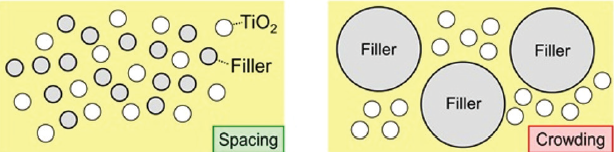
Fig. 4. Spacing (a) and crowding of TiO2 (b)[/caption]
Spacing can be obtained when TiO2 particles are combined with filler particles that have a comparable size. The filler particles do not scatter light but they prevent interference of the titanium dioxide particles.
Crowding, the undesired grouping together of TiO2 particles, results when the pigment is combined with filler particles that are big, compared to the TiO2 particles.
4. Laboratory Tests
Important laboratory tests are:
• Particle size distribution (PSD) using a laser lightscattering technique,
• X-ray fluorescence analysis for precise process control of surface treatments,
• Dispersion as measured by Hegman fineness of an alkyd mill base or by screening technique for aqueous dispersion,
• Dry color of a compressed TiO2 pigment in CIE L*a*b* color space,
• pH and resistance of 20% aqueous dispersions,
• Carbon black undertone, blue/red reflectance ratio of a mulled mixture of 20 parts TiO2 to 1 part carbon black in silicone oil,
• Oil absorption, a spatula rubout linseed oil test similar to ASTM D281-31.
Prof. Dr. Öner Yusuf Toraman
Niğde Ömer Halisdemir University
Mining Engineering Department