İğne delikleri (pinholes), özellikle yüksek sıcaklıklarda hızlı kürlenen ve yüksek ıslak film kalınlığında uygulanan su bazlı kaplamalar/boyalar geliştiren formülatörler için bir sorundur. İğne delikleri sıklıkla kaplamanın geri akıp oluşan boşlukları onaramayacak kadar yüksek viskoziteli olduğu durumlarda, kaplama filminden salınan hava ve solvent buharları sebebiyle oluşmaktadır.
İğne delikleri fırın kurumalı kaplamalarda da oluşabilmektedir. Isı altında yumuşayan film tabakasına hapsolmuş buhar, çapraz bağlanma/sertleşme tamamlanmadan önce hareket yeteneğini geri kazanıp, oluşan boşlukların kaplama tarafından doldurulmasını-giderilmesini engeller.
Hidrokarbon bazlı köpük kesiciler bu formülasyonlardaki köpüklerin ve iğne deliklerinin giderilmesinde yardımcı olmaktadır; ama uyumluluklarının kısıtlı olması sebebiyle kaplama filminde daha düşük parlaklığa, yayılma ve yüzey görünümünde performans kayıplarına sebep olmaktadırlar.
Bu makale, iğne deliklerinin giderilmesi için hem sistemden mikro köpük atımını hem de modifiye edilmiş yüzey kurumasını kombine edebilen yeni bir katkı maddesi olan Surfynol® 118 ile ilgili bilgi sunmaktadır. Bu yeni katkı maddesi, iğne deliği giderilmesinde hidrokarbon bazlı köpük kesiciler kadar yüksek performans verirken, aynı zamanda hidrokarbon bazlı köpük kesicilerin neden olduğu kötü yüzey görünümü ve uyumluluk problemleri göstermez.
Giriş
İğne deliği oluşumu, “Islak film içindeki hava veya gaz kabarcıklarının patlaması sebebiyle uygulama ve kuruma sırasında, ıslak filmde anlık deliklerinin oluşması ve film kurumadan kapanamayan/birleşemeyen küçük kraterlere yol açması” olarak tanımlanmıştır.1
Bu küçük kusurlar, özellikle parlak formülasyonlarda, yüzey görünümünü bozar ve bitmiş kaplamanın koruyucu özelliklerini azaltır. İğne delikleri hem su bazlı hem de solvent bazlı kaplamalar için bir sorundur ancak kusurun nedeni farklı olabilir. İğne delikleri, fırın kurumalı sistemlerde de sıkça görünür. Ancak bu kusurlar, film kürleninceye kadar ortaya çıkmayabilir.
İğne deliklerinin en yaygın nedeni, uygulamadan sonra kuruma sırasında, filmden uçucu bileşiklerin veya sıkışmış havanın salınmasıdır. Bu gazlar, film içerisinde bulunan kaldırma kuvvetleri veya yüzey gerilimi sebepli akış ile, kaplama-hava ara yüzeyine doğru hareket eden gaz baloncuklarını oluşturur.2 Bu baloncukların hareketi, boya filminin artan viskozitesi ile yavaşlayacaktır.
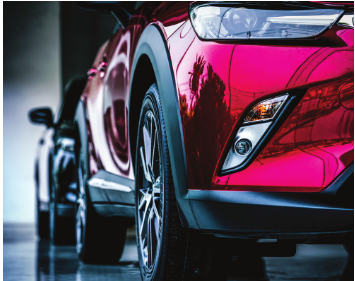
Bu durum, yüzeye doğru hareket eden kabarcığın, film içerisinde akışın zorlaşması sebebiyle geride bıraktığı boşluğun kaplama tarafından doldurulamamasına ve bir iğne deliği oluşumuna neden olur (Şekil 1). Bazı baloncuklar kuru filme hapsolmuş olarak kalabilir, ancak kaplama ısıtıldığında ve çapraz bağlamadan önce yumuşadığında hareket kabiliyetini geri kazanabilir.
Kaplama kürlendikçe, viskozite yükselir ve bu da hava kabarcıklarının oluşan boşluklara geri akışını engeller. Gaz basıncı da çok katmanlı bir uygulamadaki astar veya son kattan, kabarcığın yüzeye ilerlemesi için yeterli olabilir. Bu durum, aynı zamanda hava patlakları, kraterlerler ve diğer yüzey kusurlarını oluşturabilir. Bu kusur, yüzeyden ya da yüzeyde emilip tutulmuş ancak ısıtma ile salınmış hava veya gazlardan da kaynaklanabilir.3
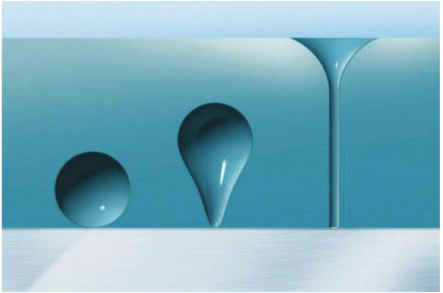
Filmden baloncuk çıkışı, tamamen anlaşılmış bir mekanizma olmamasına ve hala araştırılmaya devam edilmesine rağmen, iğne deliği oluşumunu engellemek veya sayılarını azaltmak için çeşitli yöntemler vardır: Film kalınlığını azaltmak, daha yavaş buharlaşan uçucu yardımcı çözücüler kullanmak bunlardan bazılarıdır. Azaltılmış film kalınlığı, hem mevcut gaz ve uçucu madde miktarını hem de baloncukların kaçması için gereken mesafeyi ve zamanı azaltır. Daha yavaş buharlaşan uçucu yardımcı çözücüler kullanmak da filmin kurumasını geciktirebilir ve viskoziteyi artırabilir.
Böylece kabarcıkların dışarı kaçması için daha fazla zaman sağlar. Film kalınlığının azaltılması, örtücülük ve yüzey koruma performansını olumsuz etkileyebilir. Bunun yanı sıra gerekli toplam film kalınlığını elde etmek için birden fazla uygulama gerekebilir ve bu durum da iğne deliklerine yol açabilir. Yardımcı çözücü içeriğinin/kombinasyonunun değiştirilmesi ise kuruma özelliklerini ve koşullarını etkileyebilir. Ek olarak yeni düzenlemeler ile getirilen VOC (Uçucu Organik Bileşen) sınırlamaları veya yerel çevre düzenlemeleri çerçevesinde mümkün olmayabilir.
Hava giderici ve köpük kesici katkılar, iğne deliklerini kontrol etmek için kullanılır. Ancak bu katkı maddeleri, kraterler, balık gözleri veya daha zayıf yüzey yapışması ve/veya katlar arası yapışmanın zayıflaması gibi başka sorunlara neden olabilir.4,5
Ayrıca köpük kesiciler otomotiv kaplamalarında kritik özellikler olan parlaklık, portakal kabuğu görünümü ve görüntü derinliği gibi özellikleri de etkileyebilir.6. Bu nedenle, bu tür kaplamalarda, iğne deliği kontrolü için katkı maddeleri seçerken dikkatli bir şekilde köpük kesici seçimi yapılmalıdır.
Yeni İğne Deliği Giderici Katkı Surfynol® 118
Yeni bir ürün olan Surfynol® 118, köpük kontrolünü, yüzey etkinliğini ve uygulama zamanını (open time) uzatmak için geleneksel ve moleküler köpük kesici kimyalarının7 kombinasyonuyla geliştirilmiştir. Bu ürün, hassas formülasyonlardaki iğne deliklerini nasıl azaltabileceğini göstermek için birkaç farklı formülasyonda, test edilmiştir.
İğne deliği oluşumunu engelleyen katkı maddelerini değerlendirmek için, kaplamanın ya film kalınlığı artacak şekilde sprey tabancasıyla uygulanmasını ya da artan film kalınlığına sahip bir “Wedge” tipi aplikatörle çekim yapılarak uygulanmasını içeren yaygın ve etkili bir test kullanılır (Şekil 2). Daha sonra, kaplama tabakası iğne delikleri için görsel olarak değerlendirilebilir. Kaplama şeffaf bir filme veya cama uygulanırsa, kusurları daha iyi gözlemleyebilmek için arka aydınlatma kullanılabilir. Bu test ayrıca dikey veya şekilli parçaları boyarken ortaya çıkabilecek farklı film kalınlığındaki varyasyonları simüle eder. İğne deliklerinin ilk gözlemlendiğindeki en düşük film kalınlığının ölçülmesi, katkı performansını ayırt etmenin etkili bir yoludur.
[caption id="attachment_126626" align="aligncenter" width="980"]
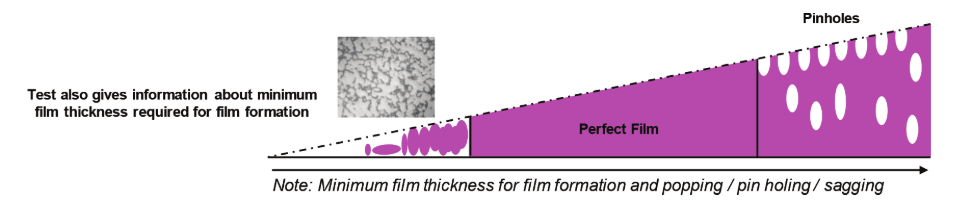
Şekil 2. “Wedge” tipi aplikatör uygulama testi[/caption]
Yeni iğne deliği önleyici katkı maddesi, Covestro’dan Bayhydrol® UA2856XP ile formüle edilmiş, beyaz bir otomotiv baz kat formülasyonunda test edildi. Boya, “Wedge” tipi aplikatör deseninde, oda sıcaklığında, elektrostatik kaplamalı, çelik panellere püskürtüldü (20°C, %48). Daha sonra 120°C’de 30 dakikada kürlenmeden önce dört dakika ani kuruma (flash off) yapıldı. Paneller daha sonra görsel olarak değerlendirildi ve iğne delikleri için minimum film kalınlığı ölçüldü. (Şekil 3)
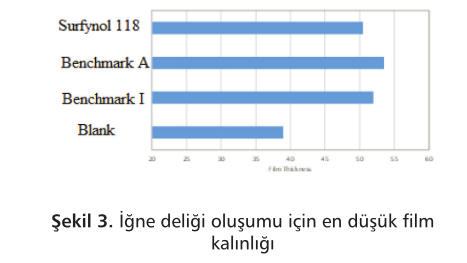
Baz boya formülasyonunda %2 oranında test edilen yeni iğne deliği oluşumu önleyici katkı maddesi, Surfynol® 118, mineral yağlı köpük kesici (Benchmark A) ve polimerik köpük kesici (Benchmark I) ile karşılaştırıldığında benzer iğne deliği performansı göstermektedir. Yüksek karıştırma hızı ile test edilerek ölçülen köpük kesme performansı da benzer görünürken, yüzey görünümü (parlaklık, pus, yayılma ve kraterler) gibi kriterlerde, Surfynol® 118 ile çok daha iyi performans gözlenmektedir. (Şekil-4) Mineral yağlı ürün, önemli derecede portakal kabuğu görüntüsü ve DOI kaybı yaratırken, polimerik köpük kesici ise filmde kraterlere neden olmaktadır. Surfynol® 118 ile yayılma veya kraterler üzerinde hiçbir olumsuz etki olmadan, son kat boyada mükemmel uyumluluk elde edilebilmektedir.
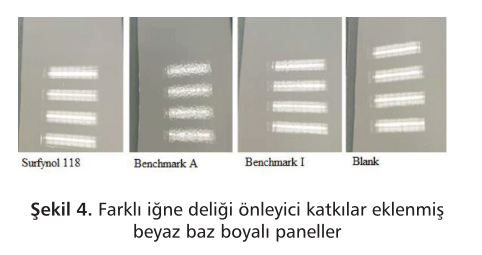
Benzer sonuçlar, Allnex’ten Daotan TW6466 ile formüle edilmiş su bazlı, metalik son kat formülasyonunda da gözlenmiştir. Surfynol® 118, bu formülasyonda da mükemmel köpük kontrolü sağladı ve şeffaf baz uygulanmış ya da uygulanmamış son kat kaplamalarda iğne deliği tespit edilemedi. Ayrıca, katkı maddesi içermeyen ve diğer köpük kesicileri içeren kaplamalarla kıyaslanacak olursa, Surfynol® 118, yüzeye yapışmada ve katlar arası yapışmada herhangi bir olumsuz etki göstermedi. Parlaklık ve flop indeksi de katkı maddesi seçiminden etkilenmedi. Portakal kabuğu görünümü ve yayılmada hafif bir iyileşme oldu.
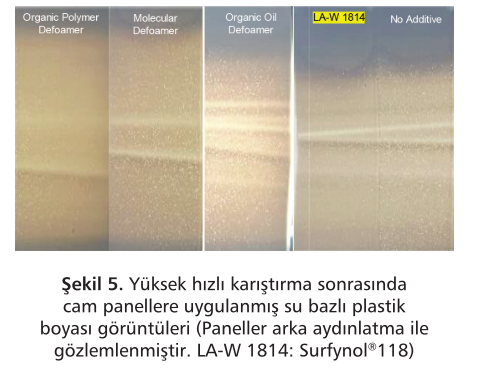
Diğer su bazlı kaplamalarda da benzer sonuçlar görülmüştür. Şekil 5,2000 rpm’de 15 dakika karıştırılan numunelerin cam panellere aplikatör (bird bar) ile 90 μ ıslak film kalınlığında çekilmesiyle, yeni katkı maddesi olan Surfynol® 118’in plastik kaplamadaki performansını göstermektedir. Surfynol® 118 ve polimerik köpük kesici, uygulamadan sonra çok daha az iğne deliği gösterdi ve ayrıca Surfynol® 118, 14 gün boyunca 50°C’de depolamadan sonra daha iyi renk kararlılığına sahipti.
Surfynol® 118, bazı siloksan bazlı köpük kesicilerle karşılaştırıldığında bile, su bazlı epoksi zemin kaplamasında ve astarlarda da iğne deliklerini azaltmada oldukça etkili. Su bazlı ambalaj mürekkeplerindeki köpük kontrolü konusunda organik polimer bazlı diğer köpük kesiciler gibi etkilidir, aynı zamanda yağ ve siloksan bazlı köpük kesicilerle kıyaslandığında da daha gelişmiş bir uyumluluk etkisi göstermektedir.
Sonuç
Surfynol® 118, alkil fenol etoksilat (APEO), silika ve siloksan içermeyen, su bazlı sistemlerde uygulama sırasında oluşabilecek solvent buharlaşması (solvent pops) ve iğne deliklerine karşı gelişmiş dirence sahip olan ve tüm bunlar ile birlikte film yüzey görünümünü koruyan yeni bir katkı maddesidir. Kaplama film kalınlığı artırılarak yüzey kusurları olmaksızın uygulanabilir. Hassas su bazlı formülasyonlarda, iyi derece makro ve mikro köpük kontrolü sağlar. Özellikle fırın kurumalı kaplamalar için uygundur.
Referanslar 1.Resene Datasheets, 1 (ix) Paint Terminology and Definitions, May 1996 (https://www.resene.co.nz/archspec/datasheets/Section1-Paint-Definitions.pdf) 2. Bubble Entrapment and Escape from Sprayed Paint Films, A. Dalili, S. Chandra, J. Mostaghimi, C. Fan and J.C. Simmer, Prog. Org. Coatings, 97 (2016), 153 – 165. 3. https://www.paint.org/article/automotive-coatingsapplication-defects/ 4. Novel Zero VOC Deaerators for Waterborne Coatings, C. J. Reader, C. Hegedus, C. Louis, K. T. G. Lai, S. el Ajaji and W. Chaigneau, Paper 16.4, 2012 American Coatings Show 2012. 5. Predicting Defoamer Performance in Waterborne Coatings, C. J. Reader and K. T. G. Lai, PCI Magazine, March 2013, 50 – 59. 6. Orange Peel Formation due to Surface Tension Flows within Drying Paint Films, N. Saranjam, S. Chandra, J. Mostaghimi, H. Fan and J. Simmer, J. Coat. Technol. Res., 13 (3) (2016), 413 – 426. 7. New Additives for Water Based Coatings: A New Class of Defoamers Is Born!, S.Y. Chan and C. Louis, EUROCOAT 2003, Lyon, France, September 23-25, 2003.