Çimento ile benzer türden olan sentetik reçine bağlayıcıları ve dolgu maddeleri (agrega) kombinasyonu, kürlendikten sonra geleneksel malzemelerle erişilemeyen özelliklerde harç benzeri bir kıvamda bir yapı malzemesi oluşturur.
Sentetik reçine betonu olarak da adlandırılan bu harcın göze çarpan özellikleri, son derece yüksek mekanik mukavemeti, kimyasal direnci, kısa kürlenme süresi ve geleneksel yapı malzemelerine mükemmel yapışmasıdır.
Sentetik reçine betonunun özellikleri ve ekonomisi için bağlayıcı kum oranıyla işlenebilirliği önemlidir. Düşük işlenebilirlik sınırı %2’lik bir reçine içeriği ile verilir, ancak böyle bir malzeme büyük bir olasılıkla çok güçlü olmaması ve üstelik hava ve sıvıya karşı geçirgen olması nedeniyle sınırlı bir ilgiden daha öteye gidemeyecektir.
Reçine oranı arttıkça dayanım gücü artar. Bu dayanım gücü en çok %15 bağlayıcıyla ulaşılır; bu nedenle daha fazla bağlayıcıya gerek yoktur çünkü daha fazla reçine gücü azaltır. Yine de, %20 bağlayıcılı sentetik bir beton yaklaşık 75.0 N/cm
2’lik bir baskı dayanımına ve yaklaşık 25.0 N / cm
2’lik bir çapraz baskı dayanımında iken, normal beton ancak 25.0 N/cm
2’lik bir baskı dayanımına ve 7.0 N/cm
2 çapraz baskı dayanımınar ulaşır.
Reçine içeriği daha yüksek olan sentetik reçine harçları, daha fazla akışkanlığa sahip oldukları ve self leveling özelliğinde oldukları için özel bir pratik ilgiye sahip olabilir. Bu durum, yüksek döşeme oranlarını mümkün kılan iyi işlenebilirlik sağlar. En yaygın sentetik reçine harcı, ağırlıkça % 10 - 15 reçine ve %85 - 90 kumdan oluşur.
Kaplanacak yerler ve yapılar sürekli olarak ağır koşullara açık bırakıldığında, boyalar ve vernikler kalıcı koruma için yetersiz kalmaktadır. Burada sentetik reçine harçları önerilebilir çünkü uygun rezinler kullanıldığında çok iyi mekanik dayanım, iyi kimyasal direnç elde edilebilir.
İki ana sentetik reçine harcı grubu vardır:
1. Malayla uygulanan harçlar,
2. Kendiliğinden yayılan (self-levelling) harçlar.
İki grup, bağlayıcı içeriğinin miktarı ve dolgu maddelerinin parçacık boyutu bileşimindeki miktar farkıyla karakterize edilir.
Malayla uygulanabilen harçlar, genellikle, %85 ya da daha yüksek dolgu içeriklidir ve normal olarak 5 - 10 mm kalınlıklarda kullanılırlar. Bu formülasyonlara göre hazırlanmış ve kürlenmiş sentetik reçine harçları aşağıdaki özelliklere sahiptir:
• Basınç gibi yüksek mekanik dayanım,
• Enine ve boyuna darbe dayanımı.
Düşük termal genleşme katsayısı, harcın düşük sıcaklıklarda rahatlıkla döşenebileceği anlamına gelir. Bunlar yalnızca mala gibi uygun bir aletle uygulanabilir.
Bazı formülasyonlar uygulamadan sonra iyice sıkıştırılmalıdır. Özel olarak hazırlanmış bazı formülasyonlar, sentetik reçine harçlarının dikey yüzeylere uygulanmasını sağlayabilir.
Self-leveling harçlar, %85 ya da daha az dolgu içeren harçlardır ve normal olarak 3-6 mm kalınlıkta kullanılır. Bu formülasyonlara üretilen sentetik reçine harçları hızlı bir şekilde serilebilir; yatay yüzeylerde sadece kaba tesviye gereklidir;
Bu harçlar, malayla uygulanan harçlarından darbeye karşı daha az dayanıklıdır. Düşük bağlayıcı içeren harçların aksine, yüzeyleri pürüzsüz, parlak ve sıvılara karşı geçirimsizdir. Sertleşmeden sonra herhangi bir yüzey yapışkanlığı varsa, su ile temizlenebilir.
Kaymaz bir yüzey oluşturmak için, kaplama kürlenmeden önce üzerine kum serpilmelidir. Eğer self-leveling harç, yüksek oranda reçine içeriyorsa, sertleşmeden sonra, beton veya demirinkinden üç ila beş kat daha büyük olabilen bir termal genleşme katsayısına sahiptir.
Bu durum, harcın düşük sıcaklıklarda bulunan (0⁰C ya da daha düşük) yüzeylerde kullanılamayacağı anlamına gelir. Kaplama 2 mm’den daha fazla bir kalınlıkta olduğunda, kaplamanın çatlamasına neden olabilecek gerilme koşulları ortaya çıkabilir.
Ancak bu gerilmeler, 2 mm kalınlığındaki kaplamalarda pek gözlenmez. Sentetik bir reçine harcı üretmek oldukça basittir. Reçine ve sertleştirici bileşenlerinin karışım oranları iyi bir biçimde hazırlanmışsa ve harç susuz bir ortamda uygun şekilde karıştırılmışsa, sevindirici sonuçlar verecektir.
Uygulama için standart değerler aşağıda verilmiştir; yüzey kuşullarının durumuna bağlı olarak biraz değişebilirler.
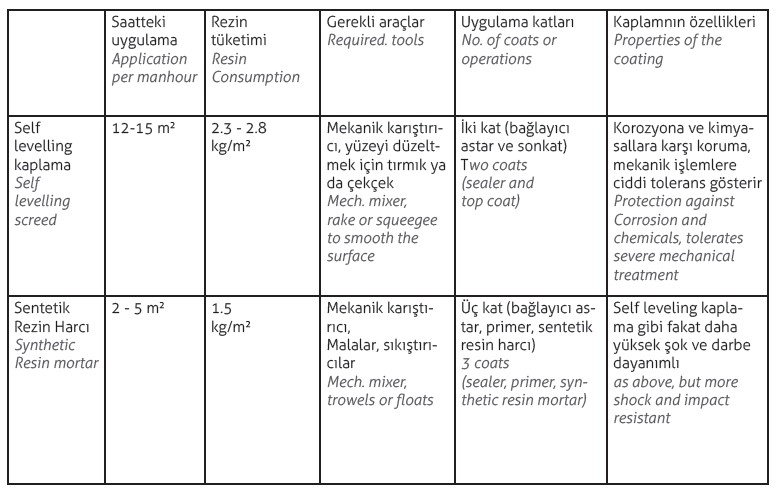
Kaplama kalitesinin doğru çalışma şartlarına bağlı kalması önemlidir. Reçine sistemleri, formülasyonlarda verilen karışım oranlarında optimum özelliklere sahiptir.
İki bileşenin yalnızca tümüyle homojen bir karışımı harç işlemi boyunca istenen bir biçimde reaksiyon verir. Bu nedenle tam ve yeterli karıştırma gerekliliğini unutmamak gerekir
İyi bir sentetik reçine harcı yapmak için kenar sıyırıcıları olan ve genellikle 50 - 80 litre kapasiteli mekanik karıştırıcılar gerekir. Yerçekimi karıştırıcılarının karıştırıcı etkisi yeterli değildir. İlk önce uygun miktarlarda epoksi reçine ve sertleştirici mekanik bir karıştırıcıda üniform bir şekilde karıştırılır.
Daha sonra dolgu maddesi tam olarak ıslanıncaya kadar karıştırılır ve yoğurulur. Karıştırma yaklaşık beş dakika sürer. Harç karıştırılırken aşırı hava girişini önlemek için, bağlayıcı üzerine %0.5 silikon yağı eklenebilir. En uygun silikon yağlarından bazıları Wacker, Bayer ya da Byk gibi firmaların silikon yağlarından olabilir.
Silikon yağların eklenmesi, self leveling sentetik reçine harçları için özellikle önerilir çünkü sürüklenen hava, self levelin kaplama yayıldıktan sonra kabarcıklar oluşturarak yüzeye geçer.
Normal ortam koşulunda bağlayıcı, sertleştiricinin türüne bağlı olarak 20 dakika ile altı saat arasında değişen sınırlı bir kap ömründedir. Kap ömrü ayrıca karışımın boyutundan ve ortam sıcaklığından önemli ölçüde etkilenir.
Oldukça büyük partiler, reaksiyonun hızlanarak aşırı ısınmayı önlemek için karıştırmadan sonra daha küçük partiküllere ayrılır. Bağlayıcının iyi yapışması, formülasyona bağlı olarak sentetik reçine harcı yayılması sırasında bir dezavantaj olabilir.
Bir süre sonra harç mala üzerine yapışır ve bu da düzgün bir pürüzsüzleştirmeyi zorlaştırır. Perdah makinesini fırçayala bir solvent sürmek yararlı olur, bunun için 2-etoksietanol kullanılması etkili olur.
Bu zorluk, formülasyonda parafin yağı bulunduğunda ortaya çıkmaz. Harcın silikon yağı ile havalandırılması da malaya yapışmayı azaltır.
%10 gibi düşük reçine içeriğindeki harçlar serildiğinde, astar ya da bağlayıcı madde önerilir. Harçta kullanılan, ancak dolgu maddesi içermeyen reçine / sertleştirici karışımı, harcı döşemeden önce yüzeye ince bir şekilde uygulanan bir bağlayıcı madde olarak kullanılabilir.
Uygulamada, zemin ile düşük bağlayıcı harcı arasında bir yapıştırıcı görevi görür.
Dolgu verilmiş bir bağlayıcı maddenin uygulama avantajları vardır. Kuvars tozu ve Aerosil, yapıştırıcı bağlayıcının benekli, yağlı bir görünümünü önleyen uygun dolgu maddeleridir.
Yapıştırıcı bağlayıcı, uygulanmasından hemen sonra sentetik reçine harcı ile kaplanabilir. Bununla birlikte, eğer harç yaklaşık %15 oranında bağlayıcı içeriyorsa yapıştırıcı bir bağlayıcıya gerek yoktur.
Sentetik reçine harcı veya yapıştırma bağlayıcısı uygulanmadan önce yüzeyin hazırlanmasına çok dikkat edilmesi gerekir. Yalnızca mükemmel hazırlanmış bir yüzey, kaplamanın mükemmel yapışmasını garanti eder.
Zayıf bir beton zeminin mekanik gerilmelere karşı daha iyi direnç göstermesi için, sentetik reçine betonunun zayıf betonu desteklemsi için yeterince kalın olması, yani en az kalınlığın 15-20 mm olması gerekir.Buna karşın, iyi, sağlam bir zeminde 5 mm kalınlık normalde mükemmel derecede yeterlidir.
Reçinelerin ve sertleştiricilerin viskozitesiyle kap ömrü ortamda bulunan sıcaklığa bağlıdır. İyice karıştırıldığından emin olmak için, reçineler ve agregalar 15°C’den daha düşük sıcaklıklarda olmamalıdır.
Bu sıcaklık aynı zamanda hızlandırılmamış bağlayıcı sistemlerin sertleşme sıcaklığının alt sınırıdır. Düşük sertleşme sıcaklıkları kaçınılmaz olduğunda, hızlandırıcı sertleştiricilerle ile hızlandırılmalıdır.
Normal bir sıcaklıkta, sentetik reçine betonu, bağlayıcı maddenin reaktivitesine bağlı olarak 24 - 28 saat içerisinde tamamen kürlenir. Bu şartlar altında beton, sadece 12 saat sonra küçük mekanik baskılar almaya yetecek kadar güçlüdür.
Tam mekanik yükleme 3 - 7 gün sonra mümkündür. Beton asla yedi günden daha az bir sürede kimyasal etkilere açık bırakılmamalıdır.
Koşullar, amin değeri 350-400 ve AHEW 93 olan düşük reaktiviteli ve uzun kap ömrü olan amino poliimidazolin tip bir sertleştirici ile farklıdır, çünkü yalnızca 24 saatten fazla sertleşmeden sonra ölçülebilir bir güç kazanır. İki veya üç gün sonra hafif mekanik gerilme uygulanabilir.
Yine de tam mekanik ve kimyasal hizmet koşulları yedi gün sonra da uygulanabilir çünkü bu tip bir sertleştirici içeren sistem kalan süre içinde ilk geciktirilmiş kürü oluşturur.
M. Namık Kayaalp
Kimya Mühendisi
Ecelak Boya Kimya Ltd. Şti.
Kaynakça
1 Schering Industrie-Chemikalien.
2. H.Lee, K.Neville handbook of Epoxy Resins.
3. Huntsman Advanced Materials (Switzerland) GmbH Klybeckstrasse 200 P.O. Box 4002 Basel Switzerland
4. Epoxy Polymers, Edited by Jean-Pierre Pascault and Roberto J. J. Williams, WILEY-VLH Verlag umbH.
5. Paint and Coating Testing Manual Fifteenth Edition of the Gardner-Sward Handbook, Joseph V. Koleske.