Sealing Technologies
Sealing solutions, also known as sealants, have three primary functions: filling the gap between substrates, forming a barrier, and maintaining substrate adhesion and sealing properties. Formulated with an elastomer containing an inert filler material that imparts
elongation and flexibility, sealants have a paste-like consistency.
Adhesives and sealants used in construction, transportation, industrial, electrical, and consumer applications, among others, are based on cutting-edge synthetic polymer technology. However, even before this technique, similar compounds, such as pitch,
were employed to hold items together and create sealing. Let us now look at the most generally employed mastic technologies nowadays.
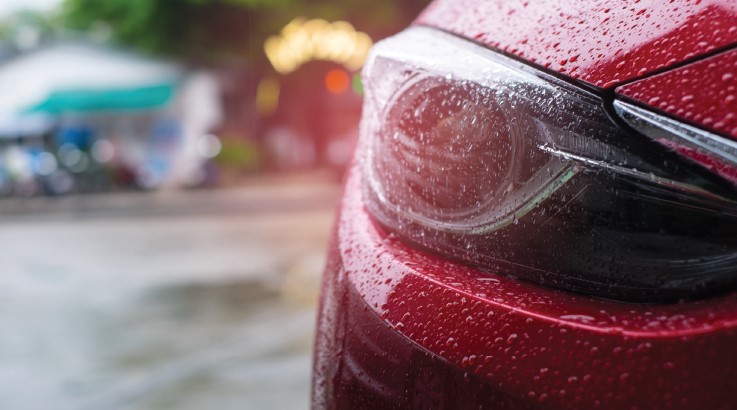
1. Polymer Based Mastics
Polyester, polysulfide, polyamide, polyurethane, and vinyl sealants are examples of these compounds, which typically cure at room temperature, anaerobic, or thermal curing.
Polymer sealants are useful for producing permanent flexible sealing in moving or expanding joints. Two-part epoxies and urethanes for general composite bonding, flexible urethanes and epoxies, cured epoxies for durability and high strength, acrylics for bonding metals and plastics, and surface-energy acrylics for bonding low polyolefins are materials used by sealing technology end users.
Choosing the correct adhesive is the key to effective composite bonding. End users and producers that require sealing technologies are advised to seek expert assistance for the specific applications required.
Adhesive and sealing technologies are used in the fabrication of parts or components for the automotive or car manufacturing, aerospace, military, marine, and sports and entertainment sectors.
2. Epoxy Mastics
Epoxy sealants are the greatest choice for making items that need to be extremely resistant and durable. Epoxy sealants, like epoxy adhesives, are twocomponent solutions with a hardener and resin combined before application.
They are allowed to cure at ambient temperature. In general, thermoset epoxies require additional heat to solidify. Epoxies are among the few sealants that have excellent adhesive characteristics. As a result, they are employed in a variety of industries, including aviation, maritime, and automotive.
Epoxies also provide excellent electrical insulation, making them suitable for use in electronics. Today, specialized epoxies for high performance coatings, capsules, adhesives, and composites are available.
Specialty epoxy resins outperform regular liquid epoxy resins in terms of chemical resistance, curing speed, modulus, UV resistance, and thermal performance. Non-crystallizing modified BPA resin and low viscosity bisphenol A/F modified phenol epoxy resins are an example of an unique epoxy mix.
They are an excellent substitute for high purity BPA resins in filament winding applications. Cycloaliphatic epoxy resin is another form of epoxy. It has a lower viscosity than regular BPA resin and is UV resistant.
It is a great sealing method for metal components. At all temperatures, modified BPA epoxy cures faster. Browning is eliminated with slow-curing epoxies. For high temperature applications, a low melt viscosity and high functionality resin is provided.
The lowest viscosity phenol epoxy resins and mixes to prevent crystallization near the monomeric product. It’s employed in industrial floor coatings, secondary containment tank coatings, and other abrasive applications.
3. Silicone Based Sealants
Because of the material’s resilience, adaptability, and affordability, manufacturers frequently employ silicone-based sealants. These materials, which typically have a lifetime of 10 to 20 years, offer alternatives for novel manufacturing techniques.
They are commonly available as acetoxy and neutral curing silicone sealants. Acetoxy cure silicones receive their name from the fact that they emit acetic acid, which has a distinct vinegar-like stench when it cures. These silicones cure in the presence of ambient moisture, have a relatively short cure time, and cling to most surfaces well.
However, acetoxy cured silicones have a harsher odor than neutral cure silicones due to the
acid generated, and acid can be harmful to some delicate electronic components. Certain substrates and metals can even be corroded by acid. Window and door frames, kitchens, countertop sealing applications, restrooms, and tubs are among the uses.
Some neutral cure silicones emit a chemical known as methyl ethyl ketoxime when they cure, whereas others release acetone. Because these materials are non-corrosive and thixotropic, neutral-curing silicones are appropriate for electronic applications.
These silicones also have a much more delicate aroma than acetoxy cure silicones and have a longer cure period, making them ideal for interior applications such as kitchen sets. Roofing, industrial seals, HVAC, compressor pumps, and refrigeration are some of the applications.
4. Acrylic Sealants
Acrylic sealant solutions are created by a catalytic reaction and can be cured in a variety of ways. Acrylic sealants that are thermally cured have the shortest curing time. Acrylic sealants have good adhesive capabilities, are odorless, flexible, and paintable, and are ideal for sealing window frames and doors.
5. Phenolic Sealants
It is a formaldehyde and phenol mixture that seals seams and offers good bonding while being resistant to heat and temperature variations. Phenolic sealants come in liquid, film, and powder forms and are utilized in the sealing and bonding of plywood, the appliance sector, and building construction.
References
• https://roboticsandautomationnews.com/2020/05/22/5-sealing-technologies-commonly used-by-manufacturerstoday/32395/
• https://www.chemical-concepts.com/blog/2018/12/whats-difference-acetoxy-vs-neutral-cure-silicones/
• Görseller: shutterstock.com / pixabay.com
Translation and Compilation by: B. Serhat Cengiz