Sand casting, the oldest known casting process, has been implemented since the 1000 BC.
Although the features such as process controls,
material options, tolerance capabilities, ability to produce elaborate parts, wide size ranges, etc. of course have been very important, the foundations of the application remained largely the same.
In short, the sand casting process is the formation of a space in the form of the desired piece and pouring molten metal into it. Sand casting is the most versatile and probably the most widely used metal casting method for thousands of years.
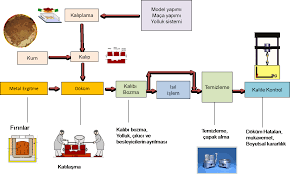
When choosing how a product is produced, design requirements (including shaping and dimensional requirements), parts and tooling costs, the amount needed, and even the feasibility of the production process, shape which metal processing processes (including which casting processes) are most appropriate.
The sand casting process uses techniques that produce shaped parts of almost every design, including very large parts and internal passages.
The tolerances required for any specific product may be more suitable casting or metal processing processes according to design complexity, volume, tool availability, or delivery time, but in the required configuration a casting can be made using the sand process and this is a decision left to the design engineer.
The process is called sand casting because the mold containing the cavity in which the metal is poured is made of compressed or concentrated sand. The sand may also contain other reinforcing materials to maintain its shape.
Sand Casting Process
A. Casting Model Production - Desired Product
The process utilizes a reusable model having the same details as the desired finished part. It has a tolerance for thermal shrinkage or shrinkage.
B. Casting Model: Gates and Riser:
Metal Distribution System
The casting model produced in step A also includes metal paths which will feed the desired bulk product design with suitable gating and risers. This draws the inevitable thermal shrinkage into acceptable areas (from the actual desired final product) and manages the metal flow and the required gas ventilation.
Casting models are made of many different materials such as wood, metal, synthetic, disposable polystyrene (EPS) and others depending on the required volume and tolerance.
C. Formation of Mold
A refractory material is formed which is stable at high temperature (sand in our example) around the casting model.
The material should be strong enough to bear the weight of the molten metal during casting and although it is resistant to reaction with the metal, it must be brittle enough to be easily separated from the solidified metal after the casting has cooled. There are various sand materials that can be used to make the mold.
The sand is typically reinforced with other materials such as clay or other chemical binders to withstand the pouring process. Alternatively, the mold may be formed by processing the desired shaped cavity directly into a sand block.
This technique is widely applied during product development, because design changes can be quickly used, managed, or used for infrequently used parts to prevent storage and maintenance of a physical model. The mold is generally produced in two parts, upper and lower half.
When the sand is set (traditional / without machine), the halves are separated and the casting model is removed. A refractory coating is added to provide a better surface coating and to protect the mold from the turbulence of the cast metal.
The halves are placed together and a space is left in the form of the casting model. The mold may also comprise cores which are a method used to produce the desired internal passages in the final product.
D. Metal Casting
The molten metal is poured directly into the static mold. Fills both the finished part and the gap defining the risers. The risers supply the casting process with a flowing source of liquid metal. As they are finally designed to cool and solidify, the shrinkage and potential gap concentrate in the riser rather than the desired part.
There are several variations of inclined casting, a process that allows metal to flow more smoothly into the cast and eliminate turbulence. Less turbulence can help prevent the formation of oxides and casting defects. Almost any alloy can be produced using this process.
For materials that are particularly reactive with oxygen, a procedure such as an argon preservative may be used to keep the air away from molten metal.
E. Shakeout
Casting, solidifying and cooling both the desired part and the additional metal required to form it. Sand breaks in a jerky process. Most of the sand used to form the mold is collected, refreshed and reused.
F. Final Touch
The gates, runners and riers are cut out of the casting and, if necessary, sandblasting, grinding, etc. for the dimensional finishing of the casting. Is performed. In general, sand castings require at least some additional work to achieve final dimensions or tolerances.
The parts can be heat treated to improve dimensional stability or properties. Non-destructive testing can also be performed. This may include fluorescent penetrant, magnetic particle, radiographic, or other controls. Final size checks, alloy test results and NDT are verified before shipment.
Resources
• Metal Casting: A Sand Casting Manual for the Small Foundry, Volume 2. Steve Chastain, 2004.
• The Complete Handbook of Sand Casting. C. W. Ammen. McGraw Hill Professional, Mar 22, 1979.
• Metal Casting: Principles And Practice. Ramana Rao. New Age International, 2007.