Protolabs Redefines Surface Quality Standards
Protolabs, a technology-enabled company produces custom parts and assemblies, has announced that is has enhanced its surface quality standards for 3D printed prototypes and parts.
From cracks and adhesion, to contact stiffness and static friction, the surface roughness is an important indicator of what parts will look like and how they will perform, however, not all parts require the same level of performance.
Protolabs has redeveloped its surface quality standards for MJF and SLS produced parts, delivering an excellent finish through flexible surface roughness options. According to these standards, Protolabs’ base option, classified as Pure and only available for some materials, delivers a pure finish with surface roughness as expected from a high-quality 3D-Printed part.
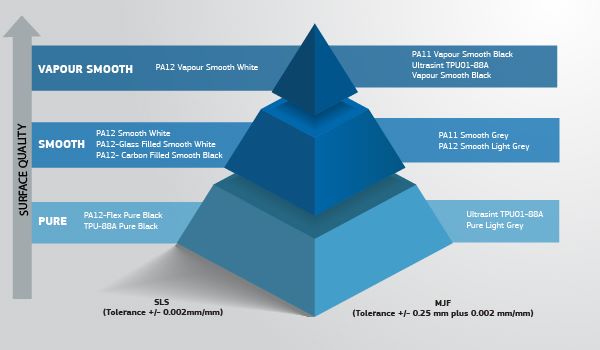
Blast parts are beaded to remove all powder, leaving a consistent overall texture. The company’s standard option (Smooth) delivers a smooth finish with reduced surface roughness, delivering value far beyond the standards Protolabs has ever offered. This is what customers receive as a default option for most materials.
As for Protolabs’ premium option Vapour Smooth, it delivers a vapour smooth finish, offering a finish close to what you usually associate with Injection Moulding, but on a 3D-Printed part. Parts are treated through an automated, high-quality post-processing technique, which leaves them with great aesthetics and sealed surfaces that are water and air-tight and easy to clean.
Source