Printing Tiles Perfectly
Naphthenic oil performs very well as a liquid vehicle in ceramic inkjet ink formulations, a recent comparative study has established. This is good news for the ceramics industry, as inkjet technology is now widely used for printing patterns on tiles.
Offering several advantages over traditional methods, inkjet printing is fast becoming a leading technology in ceramic tile decoration, and the development of inkjet ink with
the right chemical and physical properties plays a key role.
Ceramic inkjet inks must satisfy a wide range of requirements regarding not only their behaviour during the jetting cycle, but also their performance before and after the printing stage. Stability during storage and transportation, when sedimentation and agglomeration
should be avoided, is a must, as are thermal stability and low evaporation at the working temperatures used in the processes.
The ink must also pass filters easily and not clog up nozzles, whilst at the same
time behave in the desired way on the unfired ceramic substrate.
A solvent-borne ceramic inkjet ink is comprised of solid particles, such as pigments, liquid vehicles, and additives. The vehicle, which accounts for around 50% of the ink by weight plays a critical role in terms of the ink’s chemical and physical properties, greatly impacting on the behaviour of the ink during the formation of drops and dots.
Although ether and ester are the commonly used vehicles in ceramic inkjet ink, specialty
naphthenic oil is a recognised alternative. To compare the performance of these different vehicles in ceramic inkjet ink, Nynas devised a study in collaboration with an external institute.
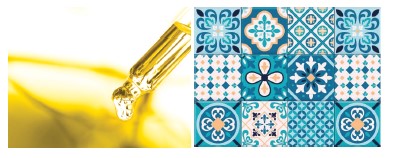
Alongside ether and ester, several different products from Nynas’ range of naphthenic oil were used for ink formulations, which were then put through an extensive programme of tests.
The results revealed that the viscosity of a vehicle is an essential property which greatly impacts the key properties of ceramic inkjet inks. Low-viscosity naphthenic oils, as well as ether and ester, exhibited excellent performance in ink formulations in terms of not only the right viscosity, density, and dynamic surface tension, but also the colloidal stability and printability before and after accelerated ageing.
• The colloidal stability of the ink formulations was evaluated by measuring to what extent particles settled and agglomerated. The less settling and agglomeration, the better the colloidal stability of the ink.
Inks formulated with the naphthenic oils NYFLEX® 201B and NYTEX® 801 exhibited less or
equivalent settling compared with inks made with ether and ester. All the inks showed very low agglomeration (figure).
• Inks prepared with the above vehicles also exhibited excellent filterability through a 5 μm filter membrane, as well as excellent printability. In addition, no obvious variation was observed regarding the printability before and after ageing for these inks, indicating that the use of the naphthenic oils NYFLEX ® 201B and NYTEX® 801 resulted in the same
stability as ether and ester.
• Due to the higher viscosity of NYTEX® 810, the inks made with it showed less filterability than the other four vehicles. However, its higher viscosity tended to reduce the time required for milling during ink preparation.
Hence, NYTEX® 810 could be used together with other vehicles to balance these physical properties and advantages.
Keeping inks stable
Elvis Li
Technical Advisor
Chemical Manufacturing
Industry
Nynas Naphthenics