Polymeric Color & Antioxidant Technologies Helping to Propel the Growth of the PU Foam Industry
The polyurethane (PU) industry has evolved significantly in the last decade, through continuous innovation and the demand for more sustainable and higher-quality materials. To make a single mattress, manufacturers use raw materials produced in every part of the world, starting with the main components of polyols and isocyanates.
The other additives used in PU formulations also play a critical role in enhancing the foaming reaction and delivering the final quality and aesthetics that the foam requires.
We all want a mattress that is comfortable and ensures a good night’s sleep.
Continuous industry innovation, mostly driven by polyol developments and foam quality improvements, has allowed polyurethane to stand out as the material capable of meeting the most critical consumers’ requirements.
PU foam has become the material of choice for millions of consumers because of its technical advantages. These advances have led to the development of multi-layered viscoelastic, hypersoft and high-resilience foams with premium quality, durability, breathability, comfort, thermal regulation, and body support for the mattress construction.
Its increasing success is based on the improved foam quality and durability that make mattresses more resistant, comfortable and breathable. As efforts aimed at creating a circular economy continue, companies across the value chain are working to make PU foam more sustainable.
In addition, certification schemes such as Certipur or Europe’s REACH legislation are helping to ensure the use of safer and healthier materials with reduced emissions.
Processes and manufacturing improvements in the past decade have driven both cost reductions and improvements in foam quality. These changes include a further shift to automation, plant and process digitalization, and the reduction of scrap.
The growth of e-commerce has also revolutionized the polyurethane sector with, for example, new mattress concepts such as “Bed in a Box”. These mattresses, delivered to a customer’s doorstep, are the fastest growing trend in the mattress industry and require the use of high-quality foams with excellent recovery properties.
Color Technology
It’s well known that consumers choose with their eyes and color is an important sensory part of this decisionmaking process. The value that color provides is related to the foam quality and to the features that the foam producer or the brand owner wants to emphasize.
Moreover, in an industry that is continuously evolving and innovating, the use of color is a perfect way to highlight the value of each layer in a mattress. Color can ensure that everyone across the value chain, from the foam producer to the brand owner and the final
consumer, fully understands the value and quality behind each foam layer.
Mattress producers have long used color to help differentiate their products. However, there remain significant opportunities to more fully exploit this feature to maximize how quality and branding are conveyed throughout the supply chain. Milliken’s Reactint® colorants for polyurethane are leading the way with this trend.
Milliken invented Reactint polymeric colorants specifically for coloring polyurethane and other thermoset resins. These reactive polymeric liquid colorants consist of chromophores that are chemically bound to polyols. This innovative colorant reacts into the polyurethane
polymer matrix, yielding deep, vibrant shades of foam.
Unlike pigment pastes, which are dispersions of solid particles in a liquid carrier, Reactint colorants are 100% homogeneous liquids that are soluble in polyol and will not settle over time, preserving ultimate quality (see Figures 1 and 2). To help manufacturers use the value of color Milliken has unveiled its Emerging Confidence ColorDirection 2022 trend report for PU mattresses with prominent trend colors.
To help you create the perfect color combination, Milliken has also launched its new, digital Reactint Color Studio – enabling customers to find a Reactint formulation for any Pantone number, with the color wheel, or for any shade in a photo. This is a special feature that
allows you to build your own mattress.
The primary colorants principle is one of the benefits of Reactint colorants. This means that by using just five primary colorants, you can produce PU foam in any shade via simple blending in-line before the mixing head. Additionally, the colorants’ low viscosity and high efficacy allow you to achieve intense shades without affecting the formulation or the foam quality.
[caption id="attachment_141621" align="aligncenter" width="577"]
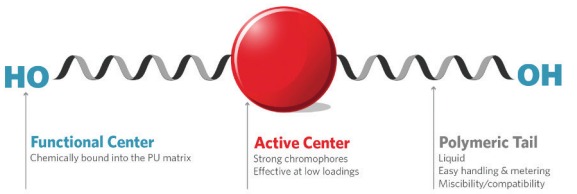
Figure 1: The polymeric nature of Reactint helps to ensure long-term quality and stability of the color.[/caption]
Antioxidant & Scavenger Technology Background
During the past few years, Milliken’s Chemical Division has concentrated on developing additives that can meet both OEMs’ more stringent automotive requirements for emissions and consumers’ perceptions of improved product quality.
Milliken designed Milliguard® AOX-1 to reduce degradation by-products by stabilizing carbon-centered radicals generated by the exothermic nature of the manufacturing process of polyurethane flexible foams without contributing to VOCs, FOG and or odor.
Additionally, Milliken has recently developed Milliguard AS-270 as an aldehyde scavenger, aimed at reducing the acetaldehydes and formaldehydes generated during the foaming process, a continuous stringent requirement from the automotive industry.
Technology Overview
Polyurethanes are particularly susceptible to radical attack. Aldehydes and other compounds of concern tend to be formed during the curing process as the result of thermal degradation and oxidation during the exothermic foam-making process (See Figure 2).
The issue is further complicated since PU foam is a great insulator and keeps the heat inside the bun or part for a relatively long period of time. This same heat generation can also degrade the auxiliary additives such as catalysts and surfactants that are used to make and stabilize the foam.
[caption id="attachment_141622" align="aligncenter" width="300"]
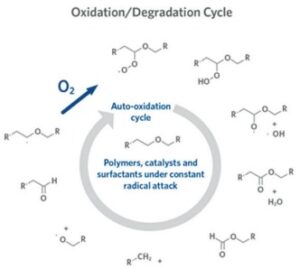
Figure 2: The auto-oxidation cycle[/caption]
Milliken’s first venture into the stabilizer market involved developing a unique, polymer-bound benzofuranone technology. Milliguard AOX-1 addresses the first stage of the oxidation cycle by stabilizing carboncentered radicals before they can react with oxygen and further perpetuate the degradation process.
Conventional antioxidants provide minimal protection at this point and only become effective once oxygen-centered radicals are generated well into the oxidation cycle. Milliguard AOX-1 protects the polymer backbone from continuous attack by various radical types, allowing a reduction in aldehyde generation and in emissions from degraded catalysts and surfactants.
Milliguard AOX-1 allows the use of amine-free antioxidant packages in polyol stabilization, which helps to reduce yellowing of the PU foam after exposure to ultraviolet light or to nitrous oxide fumes. At the same time, due to its fully reactive nature, it allows the foam
to meet the VDA-278 requirements in terms of VOCs and FOG (See Figure 3).
[caption id="attachment_141623" align="aligncenter" width="435"]
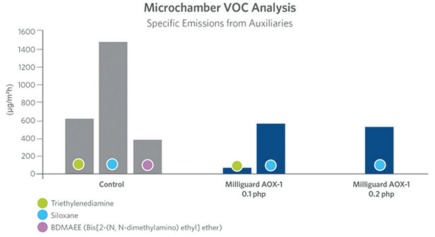
Figure 3: Milliguard AOX-1 antioxidant delivers reduced VOC emissions[/caption]
Milliguard AS-270 is a water-based polymer designed to scavenge aldehyde substrates with high efficiency. It is compatible with a wide range of PU applications, both in flexible and molded foams for automotive seating.
In Conclusion
So, it is no coincidence that polyurethane foam continues to grow in market popularity for products such as mattresses, since the technologies behind its chemistry and manufacture continues to evolve and improve-in no small part due to the advanced polymer colorant and additive technologies developed by Milliken’s Chemical Division.
Both its Reactint liquid polymer colorants, which deliver high quality and long-term stable colors to PU foam, and its Milliguard AOX-1 antioxidant and scavenger technologies, which help to reduce degradation, VOC emissions and aldehydes, are serving to improve the overall aesthetics and performance of polyurethane foam.
Herbert De Breuck
Global Polyurethane Technical Lead
Milliken