Additive manufacturing is a production technique that creates 3D geometries by applying the additive designing principle by adding materials to each other layer by layer.
Terms such as direct digital production, free form production, rapid prototyping, layer additive manufacturing are also used to describe additive manufacturing.
This production technique is divided into different groups in the processing of polymerbased materials. Various methods have been developed to process polymers in different forms, from rigid polymer materials to liquid ones with additive manufacturing methods [1-3].
Considering the industry standard criteria such as mechanical properties, thermal stabilization, component sensitivity, long-term stability, one of the most qualified additive manufacturing methods in recent years is the laser bed sintering method, which is a powder bed additive manufacturing technique.
The SLS method is in the form of a thermal process that takes place with the integration of the materials, the melting of the powder, and the subsequent solidification of the melted polymer [4], [5].
One of the most significant advantages of Selective Laser Sintering (SLS) is that many different parts can be produced together in a single production at the same time.
Unlike other additive manufacturing techniques, in laser sintering the parts to be sintered can be placed freely in the entire production area (x-y-z directions) without the need for any support structure [5].
Figure 1 shows the different schematic illustrations of the SLS technique. In this technique, laser sintered parts are formed layer by layer thickness from 0.06 mm to 0.18 mm [6].
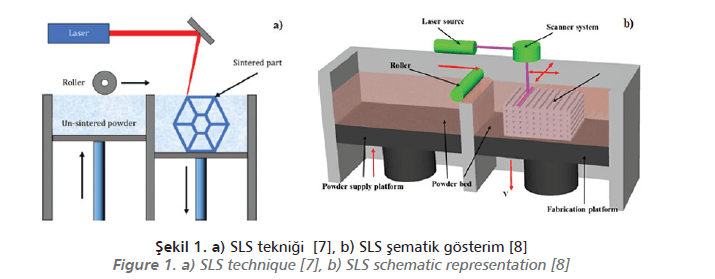
In additive manufacturing methods such as selective laser sintering, selective laser melting, laser sintered parts are produced under pressure-free conditions, unlike conventional plastic processing techniques such as injection moulding or extrusion.
The driving force in laser sintering is the temperature increase caused by the laser interaction of the polymer in the powder bed with the temperature provided by the heating system.
As a result, the properties of the manufactured parts depend on the interaction of the energy input, the melting temperature and the melt viscosity of the materials [6].
In the laser sintering process, the sintering window is one of the most essential criteria of the availability of a polymer powder in the laser sintering (LS) process. The sintering window covers the starting point of the crystallization temperature (Tc onset) and the starting point of the melting temperature (Tm onset).
The differential scanning calorimetry (DSC) evaluation of powders enables the determination of the temperatures that can be selected in the process [4], [5]. Figure 2 shows an exemplary sintering window area in a DSC thermogram.
Figure 2. DSC Thermogram- Laser Sintering (LS)
temperature range as “Sintering Window” [4].
For the SLS method, the most commonly used thermoplastic polymers (mainly PA 12, followed by PA 11, PA 6) and some of the following and non-polyamide polymers can be listed as polystyrene, polypropylene, polyethylene, polyetheretherketone, thermoplastic urethane [3], [9], [10].
In some studies in the literature, to improve the mechanical and physical properties of laser sintered polymer parts, polymers have been filled with micron and/or nano level additives such as glass beads, silicon carbide, aluminum powder, hydroxyapatite, nano-clay, nano-silica, nano-Al2O3, etc. [11].
On the other hand, in the production of polymer composite structures with SLS additive manufacturing method of many other additives and combinations, investigating the condition of the additives in the polymer structure and developing the interface compatibility properties of the additives with the polymer are among the current issues.
Therefore, some different featured additive like hollow glass microsphere can be usable to obtain lightweight polymer composite structure via SLS method. The weight reduction is significant in terms of automotive and aerospace industry, mainly to increase fuel efficiency and reduce CO2 emission.
One of our studies is to investigate the effects of Hollow Glass Microspheres (HGM) and their amounts in the Polyamide 12 (PA 12) matrix on the final properties of the PA 12-HGM composite structure produced by the SLS method.
The main aim of the research is to provide weight reduction without compromising the mechanical properties of products produced with SLS by the addition of HGM to PA 12. According to the physical and mechanical test results, the weight of composite structures has been significantly reduced by, up to 20%, in addition to a significant increase in the EModulus, upon increasing the amount of HGM in the structure [12].
With SLS additive manufacturing method, which is the powder bed additive manufacturing method, we continue our efforts to develop new types of polymer composite structures.
References
[1] International Organization for Standardization (ISO)/ASTM International. ISO/ASTM 52900:2015 [ASTM F2792], Additive manufacturing-General principles-Terminology. https://www.iso.org/standard/69669.html. Publication date: December 2015. Access date: 18.01.2020.
[2] Forster A. M., Materials Testing Standards for Additive Manufacturing of Polymer Materials: State of the Art and Standards Applicability, National Institute of Standards and Technology, Gaithersburg, (2015).
[3] Dizon, J. R. C., Espera, Jr. A. H. , Chena, Q., Advincula, R. C., “Mechanical Characterization
of 3D-Printed Polymers”, Additive Manufacturing, 20: 44-67, (2018).
[4] Schmid, M., Wegener, K., “Additive Manufacturing: Polymers Applicable for Laser Sintering (LS)”, ICMEM 2016, Nový Smokovec, (2016).
[5] Schmid, M., Laser Sintering- with Plastics Technology, Processes, and Materials”, Carl Hanser Verlag, Münih, (2018).
[6] Mielicki, C., Wegner, A., Gronhoff, B., Wortberg, J. , Witt, G., “Prediction of PA 12 Melt Viscosity in Laser Sintering by A Time and Temperature Dependent Rheological Model”, RTejournal, 9, (2012).
[7] Wang, X., Jiang, M., Zhou, Z., Gou, J., Hui, D., “3D Printing of Polymer Matrix Composites: A Review and Prospective”, Composites Part B, 110: 442-458, (2017).
[8] Stansbury, J., Idacavage, M., “3D Printing with Polymers: Challenges Among Expanding Options and Opportunities, Dent. Mater., 32: 54-64, (2016).
[9] Kumar, S., “Selective Laser Sintering: Recent Advances”, Journal of Laser Applications, 607: 1-8, (2010).
[10] Yan, C., Hao, L., Xu, L., Shi, Y., “Preparation, Characterisation and Processing of Carbon Fibre/Polyamide-12 Composites for Selective Laser Sintering”, Composites Science and Technology 71: 1834-1841, (2011).
[11] Mousa, A. A., “The Effects of Content and Surface Modification of Filler on the Mechanical Properties of Selective Laser Sintered Polyamide12 Composites”, Jordan Journal of Mechanical and Industrial Engineering, 8 (5): 265-274, (2014).
[12] Özbay, B., Serhatlı, İ. E., Bulduk, M. E., “Manufacturing and Characterization of Filled Polyamide 12 Composite Structure by Selective Laser Sintering Method”, 5th Edition of International Conference on Polymer Science and Technology, Berlin, (2019).
Prof.Dr. Ersin Serhatlı
Istanbul Technical University
Department of Polymer Science and Technology
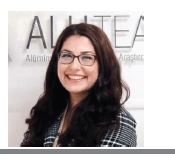
Burçin Özbay
Metallurgical and Materials Engineer / Researcher
Fatih Sultan Mehmet Foundation University
ALUTEAM