Paint and coating failures pose a serious problem for manufacturers. Since paints and coatings are generally composed of a complex combination of raw materials, they require correct application in order to get the best results.
In order for the
paints and coatings to perform well, users must prepare and apply the paint correctly, and then allow it to dry and cure according to the specifications. It is also essential to prepare the substrate cautiously for the paint to perform to its maximum capability.
When done properly, the paint will adhere well and deliver the specified protection against the elements. However, in case of a mistake, paint and coating failures can diminish the integrity and qualities of the paint. Paint and coating failures can come in different
forms and occur at several times during the lifetime of a coating.
Detecting the cause of a paint or coating failure can be challenging, since there may be multiple contributory factors to analyze. In order to pinpoint the cause of a paint or coating failure, both the paint itself and the surface must be examined thoroughly.
First of all, the paint must be stored under appropriate conditions by adjusting the temperature. Maintaining the paint and coating at recommended temperatures for at least
the first few hours after application is also important to avoid adhesive failures resulting from changes in temperature or humidity.
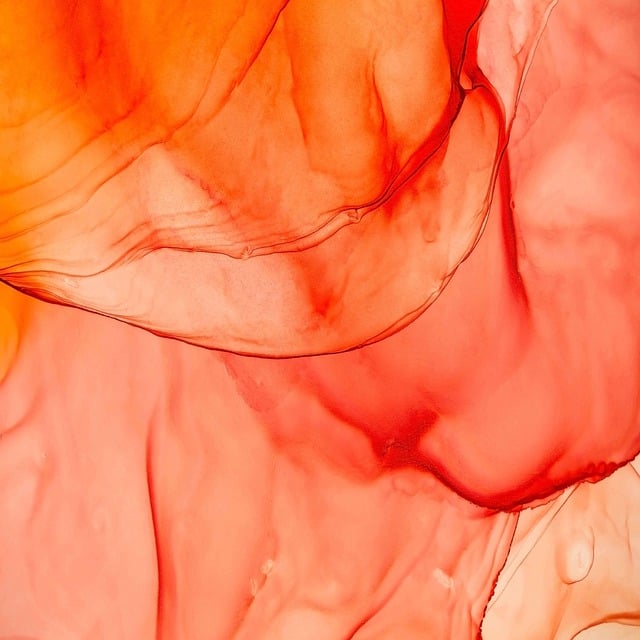
Besides, as the paint is a twopack product, it must be stirred in order to incorporate
pigment and other solids into the paint. Improper application techniques such as not maintaining a proper distance during the spraying process, thereby spraying too close or too far from the surface and setting up the spray equipment improperly can harm the quality of the paint and coating as well.
As for the surface, meticulous preparation is essential to avoid contamination. Contaminated surface is usually associated with dust, dirt or grease and has a bad effect on paint adhesion.
Chemical pretreatment and surface roughening should be performed to prepare the substrate surface properly for the paint and coating process.
Now that the causes of paint and coating failures are broadly explained, it is time to delve into the specifics of this multifaceted problem.
Abrasion, which can be defined as the process of scratching or wearing down by friction, is among the most common causes of paint and coating failures. Abrasion usually occurs as a result of exposure to abrasive materials, such as dirt, sand, chains and chippings, and it takes a toll on the durability of a painting or coating.
There are several factors that determine the durability. Roughness is one of these factors: The rougher the surface of the coating, the more susceptible it is to abrasion. Hardness is another factor that determines the durability, if a coating is not hard enough, even minor external impacts can lead to the fraction of the whole coating system, including the substrate.
Balancing the hardness is also important, since excessive levels of hardness can undermine the flexibility. Abrasion-resistant coatings can be used to strengthen these kinds of mechanical properties and reduce friction.
The application of abrasion resistant coating in surfaces guarantees that material does not have an adverse reaction to chemicals and does not face abrasion and wear due to friction. The most widely used abrasion resistant coating is polymers.
They are used on numerous applications, such as piping, valves, screens, mixers and agitators. Some specialized coatings, such as PTFE, have non-sticking properties. It allows for a more rapid surface cleaning process and minimizes expenses.
PTFE can also prolong an engine’s life and enhance its overall quality. Alligatoring, also known as crocodiling, occurs when the surface can no longer stop water and other corrosive substances from penetrating the substrate. It is characterized by a surface pattern of cracks similar to the skin of an alligator. Alligatoring usually begins as
small cracks and grows deeper and wider over time.
Alligatoring may occur due to various causes such as the application of a hard coating over a more flexible coating, or loss of paint film elasticity as a result of temperature fluctuation, or application of another coat without waiting for the previous coat to dry completely.
In this case, priming the surface with a high-quality latex primer and allowing it to dry up afterwards is the best solution. Surface shrinkage stemming from internal stresses may also cause alligatoring. If alligatoring is caused by applying excessive paint, a chemical paint remover can be used to scrape the paint in order to reobtain a clear surface.
Blistering refers to the formation of bubble-like spots within a coating. Blistering is often a result of pressure from moisture accumulation at certain points in a coating film and bubbles are produced by means of gas and vapor pressures within the coating film or the substrate.
Blisters typically fall into two main categories: osmotic and non-osmotic blistering. Osmotic
blistering occurs when moisture on the warmer side attempts to condense on the cooler side of the coated film as a result of considerable thermal gradients, whereas non-osmotic blistering is usually associated with the substrate or environmental conditions as part
of the painting operation.
In many locations, the coating application can only be performed when climate conditions are favorable, such as in summer and early fall). However, the environmental conditions that seem favorable sometimes may have its disadvantages too.
For instance, applying a coating to a surface in direct sunlight or applying the coating thicker than recommended can cause bubble formation. Bubbles form because the heat from the sun causes the surface of the applied coating to dry faster than the body of the coating film.
This quick surface drying process produces a rigid surface layer that prevents solvent in lower levels of the film from escaping. As the solvent in the lower substrates heats, it expands and creates vapor pressure within the coating film, causing bubbles to form.
To prevent blistering and accompanying bubbling, ensuring that the substrate and environmental conditions are unaffected by contamination and excessive moisture is of great importance during the coating process.
As mentioned above, blistering can result from temperature fluctuations, therefore applying a paint system with a higher tolerance to thermal gradients can minimize the risk of failure. If blisters reach the substrate, installing a vent can help eliminate the source of the moisture and remove blistering.
Peeling is another common paint and coating failure that is mostly characterized by loss of paint as a consequence of poor adhesion. Possible causes include improper drying, leakage of moisture through uncaulked joints, worn caulk or leaks in the walls, moisture escaping
through the exterior walls, insufficient surface preparation, use of low-quality paint, and applying an oil-based paint over a wet surface.
Due to loss of adhesion, soft and flexible coatings can easily be pulled away or spontaneously come off from the substrate. Peeling of the surface coat or paint can be considerably reduced by correct surface preparation before the application of the coating and the use of a coating material with strong adhesion characteristics through the use of an inhibitive primer on the substrate in advance of the application of a top coat.
Using a high-quality acrylic latex exterior paint for strong adhesion and water resistance can forestall the formation of peeling as well. As for bleeding, it can be described as a coating failure caused by the diffusion of pigments from the lower coat of coating film to the upper coat due to excessive use of solvents. Bleeding usually occurs when strong
solvents are used in the topcoats.
Overcoating bituminous- or tar-based products with topcoats, in which the tar or bitumen is soluble can cause discoloration on the upper coat. The best method of prevention is to use compatible materials and apply an appropriate sealer coat to remove the stained layer.
In conclusion, paint and coating failures still cause problems for manufacturers. However, as long as proper preparation of the coating surface is provided and compatible materials are used under appropriate conditions, minimizing the risk of paint and coating failure
is possible. Even when failures occur, they can easily be fixed with the use of certain materials such as primer or applications like scraping and sanding.
References
• https://www.pro-techpainting.com/single-post/2017/09/14/common-paint-failures-and-their-solutions
• https://www.rust.co.uk/paint-failure-guide
• https://www.ppcoatings.co.uk/wp-content/uploads/2016/06/Coating-Failure-Defects.pdf
• https://www.dunnedwards.com/explore/how-to/paint-problem-solver/alligatoring/
•https://www.corrosionpedia.com/definition/165/bleeding#:~:text=Bleeding%20is%20a%20coating%20defect,of%20solvents%20(sometimes%20resins).
•https://www.corrosionpedia.com/definition/2274/peeling#:~:text=Peeling%20refers%20to%20the%20formation,uniformly%20across%20an%20object’s%20surface.
• Görsel / Image: https://pixabay.com/
Prepeared by: Murat Soygür