Lightweight and Comfortable Sole Systems
Feet are the most important parts of the human skeleton, which carry the weight of the body for a life time and are therefore subject to constant stress. It is expected that the feet will be able to support body weight and withstand the forces that come into contact with the ground while performing functions such as walking, running and stopping.
There are connection with Foot comfort which is contact pressure between the sole of the foot and the ground. High pressure values, especially at the ground-foot interface, may cause blood flow to be blocked, pain formation or the emergence of various pathological disorders.
In order to increase the comfort of the foot, it is necessary to use materials that reduce the contact pressure in the risky areas on the sole of the foot during load bearing, and polyurethane systems are the most common materials we encounter here. The printing of the product printed in shoe sole and slipper systems with a lower weight is obtained from the feature of low mold density.
However, generally low density products need to have more open cells than high density products, which causes problems in the dimensional stability of the product after the final application and decreases in strength tests of the product compared to high density products.
In this article, we will see that high strength and comfort values can be obtained from low density products with the new generation systems developed by Kobe Polyurethane. We provide a solution with our newly developed Kobester polyester product for the dimensional stability problem that poses a risk in low density products.
Thanks to the new system polyester, the desired saturation product has been achieved in soft products.While these new system combinations we have developed provide comfort, lightness and high impact resistance, they also provide long-term use with their durability.
While the reaction profiles of these new systems are the same as the reaction profile of standard sportswear and slipper systems, the shorter mold opening time provides convenience in maximum efficiency in production capacity. Thanks to the use of appropriate paint and mold release agents, it shows excellent surface performance even at low mold temperatures.
Kobe Polyurethane Shoe Systems
In the Kobecat 120-Kobester LB1732-Kobenat Z002 system, which was developed for the production of sports soles with low density and low hardness, the hardness value of 50-60 shA and the mold density can be printed as 320-420 kg / m3 depending on the model.
[caption id="attachment_141525" align="aligncenter" width="237"]
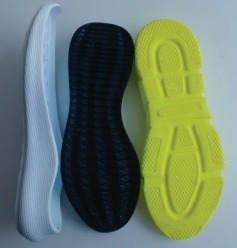
Figure 1. Kobe Polyurethane Sole System[/caption]
In slipper and sole systems, mechanical tests are carried out to examine the behavior of materials. The most important of these tests are flex resistance and tensile tests. In the developed base system, both the flexing resistance test and the tensile tests are better than standard products.
In the Kobecat 120 / Kobester LB1732 / Kobenat Z002 system developed for the sports sole, the test conditions are made more difficult, and the flex feature is more than 150,000
steps at 0°C in the test. In the tensile test, the maximum load carrying capacity and the percent elongation at break were determined.
[caption id="attachment_141527" align="aligncenter" width="300"]
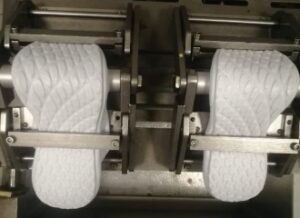
Figure 2. Flex Test[/caption]
The work consists of three stages. First of all, laboratory synthesis and application studies are carried out together with the design, in the second step, test castings and their tests with the low pressure machine in the company, and in the last stage, the tests of the
products that come as a result of customer trials and customer serial trials are carried out. The results of these triple confirmation tests are given in the table below.
[caption id="attachment_141531" align="aligncenter" width="687"]
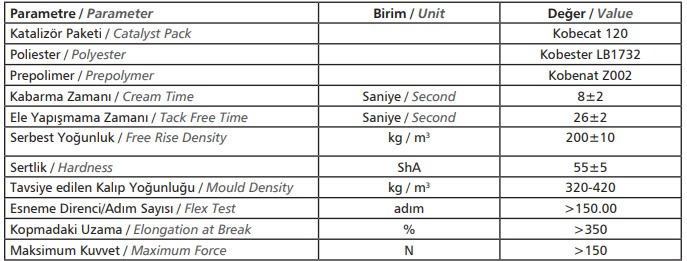
Table 1[/caption]
Kobe Polyurethane Slippers System
In the Kobecat 118-Kobester LB1732-Kobenat X001 system developed for the production of low density and low hardness slipper soles, the hardness value is 55-65 shA and the mold density can be printed as 220-250 kg / m3 depending on the model.
[caption id="attachment_141532" align="aligncenter" width="300"]
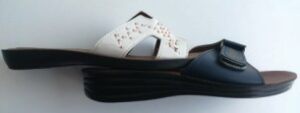
Figure 3. Kobe Polyurethane Slipper System[/caption]
Although the expectation of flexing resistance in slipper systems is low, the developed Kobecat 118 / Kobester LB1732 / Kobenat X001 system has more than 40,000 steps of flex feature. It is observed that these values are between 10,000-30,000 in competitor products tested under the same conditions.
[caption id="attachment_141533" align="aligncenter" width="686"]
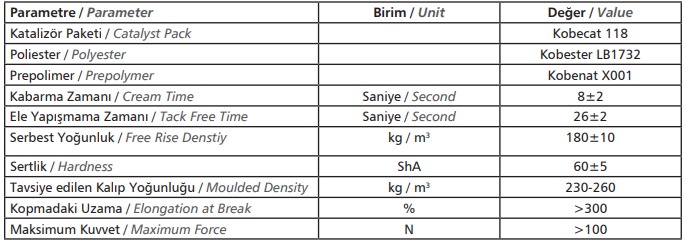
Table 2[/caption]
Gülhan Sarıgöl
R&D Engineer
Kobe Polyurethane