Importance and Use of Safety Valves in Process and Storage Tanks
What are Pressure Relief Valves?
Pressure relief valves are self-actuated valves located on pipes, vessels, tanks, and other pressurized systems such as compressors and pressure regulating stations.
They are designed to open automatically at a preset pressure. When open, a portion of the gas, steam or liquid in the system is allowed to escape, preventing it from being overpressured beyond safe limits.
The valve will reclose when the pressure has dropped to a safe level, thus maintaining the integrity of the installation and conserving the remaining process fluid.
What is Overpressure?
We are referring to overpressure as that case when a system (a tank, vessel, piping, pipeline, process unit, etc.) containing liquids and/or vapors (gases) under pressure
exceeds the safe limit or design pressure.
Some way to vent the pressure that is over the safe or design pressure limit must be provided.
Overpressure can occur for four major reasons:
1. Process failure: An example of this would be a compressor that continues to feed pressure into a vessel without control (like blowing too much into a balloon).
On some customer specs, “blocked outlet” will be listed as the reason for specifying a pressure relief device.
2. Overheating (fire case): Typically from an external fire around a tank or piping, which increases the internal pressure due to expanding gas or vapors and/or liquids flashing into vapor.
3. Thermal expansion: Whenever a closed section of piping, filled with liquid is exposed to warming by the sun or ambient temperature rise, the liquid expands, creating a very slow but substantial increase in internal pressure.
If this is not relieved, vessel or piping rupture or yielding can occur.
4. Internal chemical reaction: Some chemical processes can “run away” creating pressure build-up. This kind of accident may occur so suddenly that only a rupture disc can respond quickly enough to provide overpressure protection.
What is Overpressure Protection?
Overpressure protection refers to any method of discharging (venting) the fluid (liquids and/or vapors) from a system either to the atmosphere or to some other system so that the pressure will not exceed some specified value.
This is accomplished by a pressure relieving device that opens at a predetermined pressure. The sole purpose of these valves is to prevent injury of personnel and damage
to property.
For our purposes, there are two basic kinds of overpressure protective devices used to discharge excessive pressure.
These are reclosing (pressure relief valves) and nonreclosing (rupture discs). The need for overpressure protection is usually determined by codes or regulations giving minimum and/or specific requirements for pressure containing systems (tanks,vessels,piping, etc.) which include pressure relieving devices.
The two most frequently referenced organizations that publish requirements are the American Society of Mechanical Engineers (ASME) and the American Petroleum Institute (API).
What Kinds of Pressure Relief Valves are there?
There are three basic types of pressure relief valves.
1. Weighted pallet type valves are those in which direct weight is used to keep the seat closed. This valve is limited as to the maximum set pressure available because of the weight required.
Substantial overpressure (often 100% or more) is necessary to get the pallet into full lift.
Weighted pallet valves, also called weightloaded valves or conservation vents, are used for both pressure and vacuum applications (see Figure 1). (e.g. Anderson Greenwood Type 96A Vacuum Breaker, Enardo 950 series PVRV).
2. Direct spring operated valves are those in which the valve disc or spindle is held closed by a spring (see Figure 2). As pressure increases under the disc, the force pushing up on the disc increases.
When this force equals the force of the spring pushing down, the valve is on the threshold of opening. Any additional increase in pressure causes the disc to lift and the valve to open.
(e.g. Crosby (JOS, JBS, JLT, 800, 900, BP))
3. Pilot operated pressure relief valves (POPRVs) are those in which the main valve seat is held closed by the system pressure itself. The pressure acts upwards on the seat area (nozzle-to-seat contact area) and downwards on the top side of an unbalanced moving
member, usually a piston, called the dome area (see Figure 3).
The piston area is larger than the seat area, causing the force pushing down to be greater than the force pushing up. A pilot controls the pressure in the main valve dome. (e.g. Anderson Greenwood Series 200,400, 500, 700, 800, 900, and 5100 are piston type POPRVs.)
An important functional difference between the direct spring operated valve and the POPRV occurs as set pressure is approached. With all direct spring operated valves, the closing force on the seat decreases as the system pressure approaches set pressure.
When system pressure approaches set pressure, the upward system force and downward seat force are nearly balanced, causing a condition known as “simmer,” which can cause damage to the valve seat,resulting in leakage, product loss, and high valve maintenance costs.
Additional system overpressure (as much as 10%) is required to counteract the spring force to attain full lift. (The Anderson Greenwood Crosby Series 80 pop action valves - Types 81, 83, and 86 – are a unique exception to this rule. Contact us for details)Exactly the opposite is true with the POPRVs.
As set pressure is approached, the main valve seat sealing force is maximized due to the greater downward closing force developed by the system pressure acting on the dome area versus the upward opening force generated by the system pressure acting on the seat
area.
When the pilot senses that set pressure has been reached, it opens and reduces the dome pressure, which causes the main valve to open and go into lift.
There is no simmer in the main valve, and very little in the pilot, normally due to the pilot’s powerful huddling chamber (see definition) combined with a resilient soft seat.
What is Storage Tank Protection?
Tank blanketing is a process used to maintain a gas “blanket” in the vapor space of a pressuretight liquid storage vessel without admitting ambient air, as with a conventional vacuum breaker.
Either is essential to prevent collapse of the tank due to atmospheric pressure acting on the tanks outside walls with an excessive vacuum inside.
Using an inert or compatible blanket gas, rather than ambient air, will prevent a possible explosive mixture in the tank and tank product contamination.
Further, having a blanket gas in the tank vapor space can significantly reduce fugitive emissions, as the pressure relief valve, when activated, will discharge mostly blanket gas rather than perhaps dangerous and noxious product vapors.
[caption id="attachment_143187" align="aligncenter" width="388"]
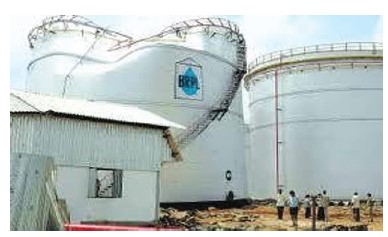
Figure 1: Pressure[/caption]
[caption id="attachment_143188" align="aligncenter" width="387"]
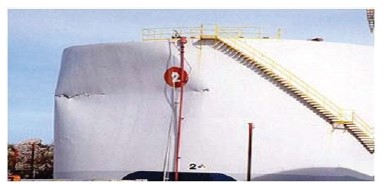
Figure 2 : Hurricane [/caption]
The Importance of Vapor Pressure Control
• Controlling the vapor space pressure (above the liquid) is one of the keys to safety.
• Pressure that is too high or low can collapse a tank
• This vapor space pressure changes due to:
- Pumping in or out of product,
- Temperature changes.
The Effect of Pumping (In or Out)
• When tank contents are pumped in;
- Tank vapor space pressure increases,
- Excess pressure needs to be relieved or vented.
• When tank contents are pumped out;
- Tank vapor space pressure decreases,
- Lower pressure needs to be compensated
The Effect of Temperature (Up or Down)
• As tank contents cool down, the vapors inside condense;
- Tank pressure decreases,
- Lower pressure needs to be compensated.
• As tank contents heat up, the vapors inside expand;
- Tank pressure increases,
- Excess pressure need to be relieved or vented.
Pressure Vacuum Relief Valves (PVRVs)
• Vacuum Relief;
- Tank pressure is sensed,
- If tank pressure < atmospheric pressure, then air enters tank,
- This will restore the tank to its proper operating pressure.
• Pressure Relief;
- Tank pressure is sensed,
- If tank pressure > design set point, then tank vapor is released,
- This will restore the tank to its proper operating pressure.
What is the Purpose of Tank Blanketing?
To isolate the tank contents from atmospheric air and moisture. = Longer storage life,
Higher quality products.
To safeguard the stored product from spoilage or contamination. = Less oxidation, Reduced emissions.
To contain tank vapors, preventing their release to the atmosphere vapor = Reduced product loss, Eliminates flammable.
To lower the oxygen content of the vapor space, or to inert the vapor space. = Enhances safety.
Mehmet Berk Güven
Field Sales Engineer
Pressure Management
Emerson Automation Solutions