Impacts of Colloidal Silica on Waterborne Clear Coating
In these days of global warming the usage of colloidal silica is become more common in the world with its positive effects on the environment and coating industry.
In the past there have been many studies on the usage of silica nano particles in resin based system. However there have been very few studies done on the use of silane modified water based colloidal silica in the formulations of waterborne coatings. Nouryon is the manufacturer company active in 80 countries that produces these products and can do the necessary technical studies.
Thanks to technical people who have been working in this company for many years such as Dr. Peter Greenwood, the number of similar studies has increased and many positive effects
of the products have been investigated.
Nouryon has researched the effect of silane modified colloidal silica on clear coating like open time, anti-blocking, sanding & mechanical properties of film. Open time extension
and decrease of resin usage ratio effects on VOC ratio were evaluated several data. Nouryon has developed Levasil CC 301 as silane modified colloidal silica.
What Is Colloidal Silica?
Very small particles of amorphous silicon dioxide (SiO2), dispersed in water. Safe for both humans and the environment. Large surface area, due to the numerous small particles. The particles are usually electrically charged, why they can easily interact with one another or to other substances. [4]
The properties of colloidal silica dispersions can be varied in many ways: Concentration: 7-50% silicon dioxide, Particle size distribution, Structure: Discrete particles (high S-value) or chains (low S-value), Particle diameter: 2-100 nm, Surface area: 30-1100 m2 / g, pH:
2-12, Modifications: ammonium, aluminate, chloride, silane, deionized.
Silane Modification
Epoxy-Silane surface modified colloidal silica is Extremely stable aqueous colloidal dispersions! Epoxy functional group is covalently (strongly) firmly bond to the particle surface. The epoxy functional group is ring-opened and transferred into a diol group. Nonaggregated (the full particle surface can work efficiently in a coating). [3]
Levasil CC 301
It is a neutral, aqueous dispersion of colloidal silica that is approximately 28% solids by weight. The amorphous silica particles carry a negative surface charge. The SiO2 particles are discrete, have a smooth, spherical shape, and are present in a narrow particle size distribution. The particles have also been surface modified with an epoxy silane. “Hydroxyl number” for 2-pack systems; 0.45 mole OH / kg product. The physical appearance of the dispersion is a clear liquid, slightly more viscous than water. [2]
Waterborne Coating Formulations W / O Levasil CC 301
Different varnish formulations were studied. 1 K or 2 K acrylic formulations containing resin, modified colloidal silica, coalescing agent and additives formulated clear floor coating.

[caption id="attachment_142830" align="aligncenter" width="713"]
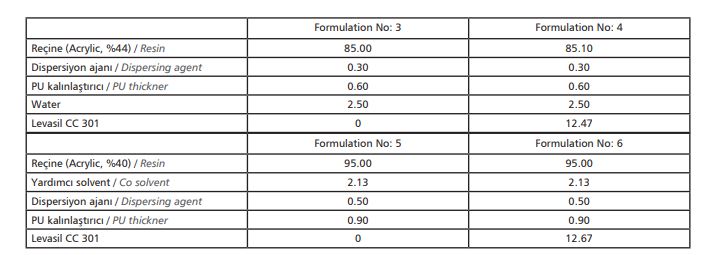
Table 2: Formulation 8 is 2K acrylic / industrial waterborne varnish and topcoat, Formulation 9 is 2K acrylic /
industrial waterborne high gloss varnish and topcoat [1][/caption]
Gloss & Haze
Gloss (20oC) has been measured of coatings applied on aluminum plates after 30 days of drying at ambient temperature. Dry film thickness between 40–50 µm. Haze index, defined as a gloss difference, was calculated from gloss measurements 20oC and 60oC following ASTM D 4039. [1] The results are given in the table 4 and table 5. There is a little or no
change in gloss or even an increase in gloss upon silica addition. [1]
[caption id="attachment_142834" align="aligncenter" width="742"]
![Table 3: Gloss 20oC [1]](https://www.turkchem.net/wp-content/uploads/2022/07/t3.jpg)
Table 3: Gloss 20oC [1][/caption][caption id="attachment_142835" align="aligncenter" width="711"]
![Table 4: Haze Index (Gloss 60oC-Gloss 20oC) [1]](https://www.turkchem.net/wp-content/uploads/2022/07/t4.jpg)
Table 4: Haze Index (Gloss 60oC-Gloss 20oC) [1][/caption]
Block Resistance
The block resistance of different systems has been evaluated according to ASTM D 4946 . Block resistance is defined as the ability of a coating to resist sticking to another surface. The coating have been applied in two layers on oak substrate and let dry at room temperature for 24 hours. The dry film thickness are around 65-70 µm. The wood coated parts have been placed face to face with a load weight of 1 kg (127 g / cm2) at 60oC during 30 minutes. A ranking has been established from the force to be applied on system to peel of the wood. [1] The addition of silane modified colloidal silica to the studied aqueous system is beneficial for the blocking resistance. [1]
[caption id="attachment_142836" align="aligncenter" width="417"]
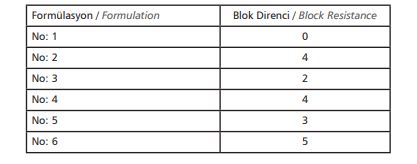
Table 5: Block resistance results for 1K acrylic clear formulations [1] Ranking: 0=worse, 5=best[/caption]
References:
[1] P. Greenwood, “Impacts of Silane Modified Colloiadal silica on Waterborne Clear formulations”, 2018
[2] Nouryon Product Information, Levasil CC 301
[3] P. Greenwood, “modified colloidal silica for enhancement of open time and dirt pick up resistance“, December 1, 2018
[4] Nouryon, “Natural part of everyday life“
Dr. Peter Greenwood
Ph.D. Chemical Engineer
Technical Development Manager
Nouryon Inorganic Specialties | Technology Solutions
Eliz Türkileri
Chemical Engineer
Senior Technical Sales Executive
Ravago Chemicals Turkey