High Strength Hybrid Epoxy Ester Polymer
Resins are widely used as binders in industrial paints and coatings. Epoxy esters are resins obtained as a result of the reaction of fatty acid and epoxy resin (Figure 1). The epoxy esters obtained in this way have the air drying property and in this way, they provide an economic advantage, as no hardener is needed.
Epoxy esters are more preferred than alkyd resins because they give products properties of better color retention, better adhesion, more flexibility and chemical resistance. Epoxy esters are widely used in many areas such as the manufacture of primer paint for the
automotive industry, the manufacture of top coat marine paints, the primer paint binder in the painting of household goods, the filler varnish in floor covering materials and metal furniture painting.
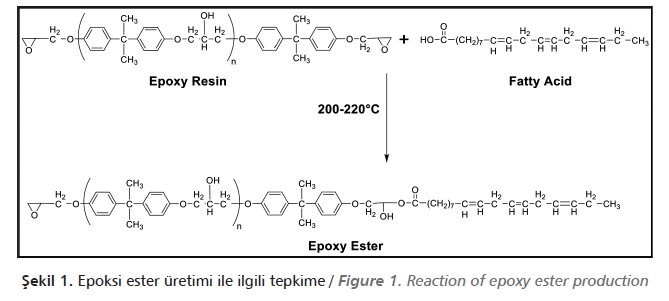
Urethane resins are widely used in wood and industrial paints because of their brightness, resistance to external conditions, fast drying, good filling and hardness. Urethane resins are used very often in wood applications, even though their yellowing resistance is low.
In order to overcome the inadequacies in some applications in the resin industry and the market need in finding alternatives, a need has emerged for the development of a hybrid resin type with high added value, which can replace imported products in market with low cost and high performance features.
In line with the researches, it was decided to develop a hybrid product with higher yellowing resistance than urethane resins, drying faster than epoxy esters, forming a harder film than each equivalent, high corrosion resistance and high adhesion.
It is aimed to contribute both to the economy of Turkey and to the academic literature, since the products developed do not have equivalents other than Serkim Resin Company and the project is unique.
Experiment
Epoxy ester resins which are the base of hybrid resins were synthesized from epoxy resins and 6 different vegetable fatty acids containing different fatty acid components. Modification of the epoxy ester resin with <5% and <10% aromatic and aliphatic NCO
was carried out and after the performance tests on the paints were examined.
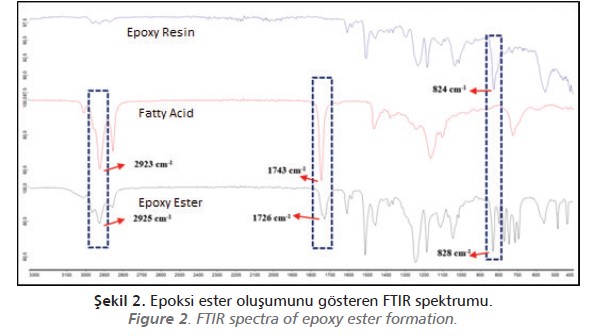
The epoxy ester FTIR spectra formed as a result of the reaction of epoxy resin and fatty acid are shown in the figure 2. The change in the peaks seen at wavelengths of 1726 cm-1 and 828 cm-1 occured as a result of the opening of the oxirane ring in the reaction between the fatty acid and epoxy resin. C-H bonds formed as a result of the opening of the oxirane ring are observed at a wavelength of 2925 cm-1 (Figure 2).
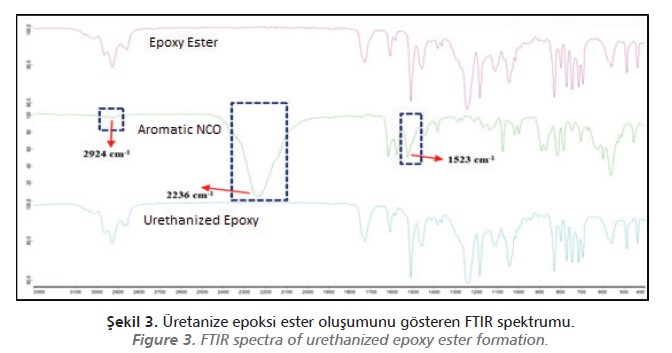
The peak seen at 2236 cm-1 in the FTIR spectra of the epoxy ester and aromatic NCO modification characteristically shows the N=C=O stretching vibrations belonging to the isocyanate group in the structure of aromatic NCO (Figure 3). In addition, the peak seen at
1523 cm-1 wavelength is caused by the C=N stretching vibration seen at 2924 cm-1 wavelength.
The spectra were compared in order to see the structural changes that may occur after the production of urethanized epoxy ester.
Results
Paints made with hybrid paints were applied to glass and metal surfaces at 60 micron. In general, the adherence performance of all films are similar to each other and good. No significant difference in gloss results was observed when different fatty acids used.
Since the yellowing tendency of the aromatic NCO modified epoxy ester is higher than the aliphatic NCO modified epoxy ester, the glosses of epoxy ester modified with aliphatic NCO were better.
For <5% aromatic NCO modified hybrid resin;
• On glass surfaces, it was observed that the hybrid resin which is produced with fatty acid containing low rosin acid gave the best performance and the highest overall performance.
• At the end of the 10th day, it can be said that the performance of the hybrid resin which is produced with fatty acid containing low rosin acid with a hardness value of 106 köenig is the highest.
For <10% aliphatic NCO modified hybrid resin;
• At the end of the 10th day, it was observed that the performance of the hybrid resin which is produced with fatty acid containing low rosin acid with a hardness value of 108 köenig was the highest, followed by the hybrid resin which is produced with fatty acid containing high ricinoleic acid with a hardness value of 103 köenig.
• It can be said that the hardness values of the modified products are improved compared to the epoxy ester and the hybrid resins which are modified with aliphatic NCO give the best performance.
• At the end of the alkaline resistance test (20 days / 3% NaOH), it was observed that the strength of the all hybrid resin films was generally good.
• In the salt spray test (the salt resistance), when all epoxy esters and hybrid resins were tested in a salt-spray corrosion device, it was observed that there was no deterioration on the films at the end of 20 days. Salt-spray test performances of all resins were very good.
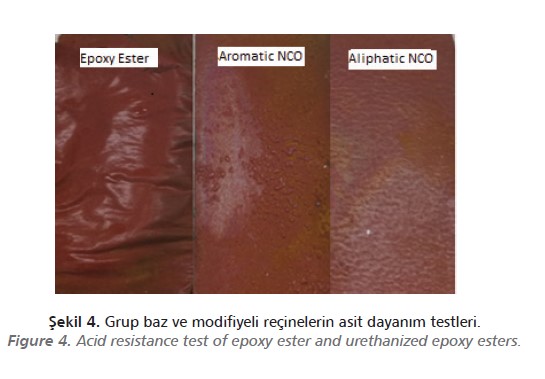
At the end of the acid resistance test (20 days / 3% H2SO4), it was determined that the epoxy ester films were removed from metal surfaces but after modification process the acid resistance of the hybrid resin which is produced with fatty acid containing low rosin acid
was good (Figure 4).
When the drying performances of hybrid modified resins made with 6 different fatty acids are evaluated in the drying test results, the device drying results of the epoxy ester resins is between 124-175 minutes, it was observed that there were significant improvements in
drying performance after the modifications.
The <5% aromatic NCO modified hybrid resin which is produced with fatty acid containing low rosin acid gave the very good performance with 20 minutes at drying time, the <10% aliphatic NCO modified hybrid resin which is produced with fatty acid rich in oleic and linolenic acid components gave the best performance with 19 minutes at drying time.
Significant improvements in drying performance were observed in all hybrid resins which are the subject of the project compared to epoxy resins.
Comment
In this project; it was observed that the drying, brightness, hardness, adhesion, alkaline resistance, thermal properties of hybrid resins produced by modifying epoxy ester resins with isocyanates were improved and hybrid resins with desired properties could be produced.
When all test results were evaluated, it was observed that the <10% aliphatic NCO modified hybrid resin which is produced with fatty acid containing low rosin acid exhibited the best performance.
In the future, it will be possible to produce hybrid resins with different desired properties in different combinations by changing the fatty acid, isocyanate and epoxy resins.
Dr. Çiğdem Yüceel - Project and R&D Specialist
Serkim Resin
Şenol Demir - R&D and P&D Specialist
Serkim Resin
Zeynel Turna - R&D and P&D Specialist
Serkim Resin