Optimization of Production Processes in the Grinding System
1. Introduction
In discussions with specialists, colleagues and customers, the opinion is repeatedly expressed that, for the design of grinding and dispersing processes in the paints, coatings
and inks industry, the production capacity of the plant is the decisive factor, e.g. for new investments.
Agitator bead mills are employed for many products. Because of the fact, that the comminution result is essentially a function of the specific energy of a product, the maximum possible power input to the agitator bead mill is seen as the decisive operating parameter in most cases.
The argument that a mere increase in the power density, and thus the power input to the mill, also results in a rise in the specific energy requirement is all too often dismissed with the assertion that it is acceptable to have higher energy costs compared to the price of the product.
In the following article, a simple example for the comminution of a calcium carbonate will first be used to demonstrate the influence various parameters have on the power input, the specific energy requirement and the production capacity.
It will then be explained, how a tried and tested peg grinding system was modified and the operating parameters adjusted specifically for the paints, coatings and inks industry in order to facilitate higher production capacities while also increasing the efficiency.
The results of field tests will be used for discussion of the potential increase in production capacity.
2. Effect of various operating parameters on the production capacity and the specific energy requirement during comminution in agitator bead mills
The comminution and operational behavior of agitator bead mills was thoroughly researched by Stehr [1] and Weit [2]. A comprehensive factor in the comminution
behavior was revealed to be the specific energy, i.e. the energy supplied to the grinding chamber with respect to the mass or volume of the ground product (solid) (see Eq. (1)).
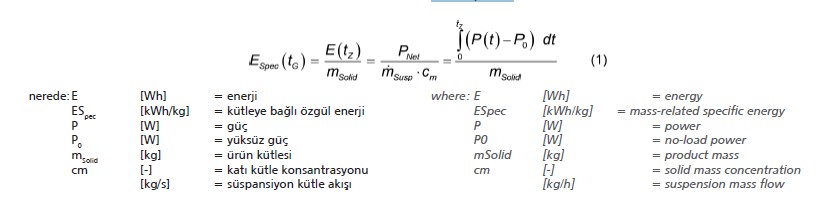
Investigations with different sizes of grinding media have shown that, in addition to the specific energy, the grinding bead size has a significant impact on comminution in agitator bead mills (Joost [3], Schwedes [4], Thiel [5], Bunge [6], Mankosa et al. [7], Stadler et al.
[8] and Roelofsen [9]. Adjusting the size of the grinding beads to the comminution task yields, to some extent, a significant reduction in the specific energy requirement.
For discontinuous comminution of limestone, Kwade [10] also noted that the circumferential speed of the agitator and the grinding media density had a systematic effect on the correlation between specific energy and product fineness.
As an expression for the kinetic energy of the grinding beads, Kwade [10] defined the stress energy of the grinding media SEGM as a function of grinding media density ρGM, grinding bead diameter dMK, and circumferential speed of the agitator vt (see Eq. (2)).
During investigations into the effect of the operating parameters grinding bead density, circumferential speed of the agitator disk and grinding media size he was able to show that with constant specific energy input, there was an optimal stress energy at which the greatest product fineness could be achieved.
These effects should become clear through a simple example. Calcium carbonate was selected for two reasons:
1. For pigmented systems, a simple evaluation of the test results by means of the particle size distribution is not representative, since additional quality characteristics such as gloss, transparency and color intensity must match collectively in order to get an appropriate product quality.
2. In addition, changing loading conditions can mean that for the characterization of an identical product quality for paints, coatings and inks, a modification of the formulation is also necessary.
However, the correlations between the operating parameters discussed from this example can be carried over qualitatively to any material system. For the determination of an optimum, a minimum of three test settings are required.
The range of optimal stress energy required to advance the comminution is not always attained. With regard to operational reliability or the target product throughput, in many cases it appears to be impractical to use even smaller grinding beads.
In this example, a commercial limestone was initially processed with identical grinding beads in the same mill in recirculation mode operation and with three different circumferential speeds of the agitator shaft: 7 m/s, 10.5 m/s and 14 m/s. Each time, samples were analyzed with a Malvern MasterSizer 3000 after a specific energy input of 0.03 kWh/kgFS, 0.07 kWh/kgFS and 0.1 kWh/kgFS (see table below).
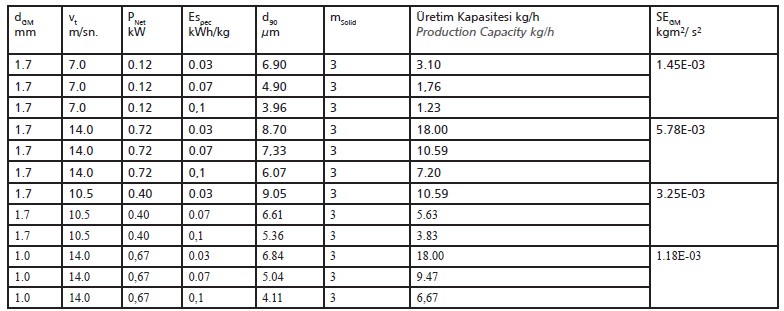
The results of the test are shown in Fig. 1, where d90 is a function of specific energy input. A d90 of 6 μm was defined as the target value.
This demonstrates that, with the grinding media used, the desired target value can be achieved with the lowest circumferential speed of the agitator shaft and the lowest specific energy consumption.
However, due to the very low power input at these settings, the resulting production capacity is also the lowest (see. Figure 4).
[caption id="attachment_143249" align="aligncenter" width="446"]
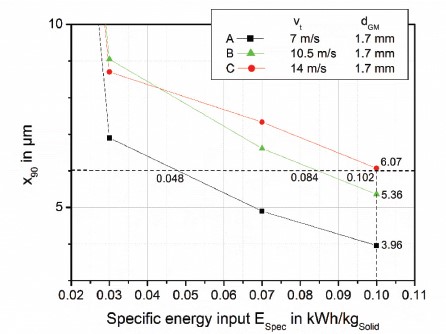
Figure 1: Comminution of limestone with different circumferential speeds of the agitator shaft.[/caption]
This finding is confirmed when one now considers the stress energies of the grinding media for the tests conducted (see Figure 2). Now the goal is to achieve the highest production capacity with the lowest energy requirement.
To this end, the stirrer tip speed of the agitator shaft is increased and the grinding media
size is calculated for which the same stress energy per grinding bead impact is available (see the following straightforward calculation).
Now if grinding beads with a diameter of 1.0 mm rather than 1.7 mm are used with a constant grinding media density and circumferential agitator shaft speeds of 14 m/s, the comminution results are comparable when plotted as a function of specific energy (see Figure 3).
[caption id="attachment_143251" align="aligncenter" width="289"]
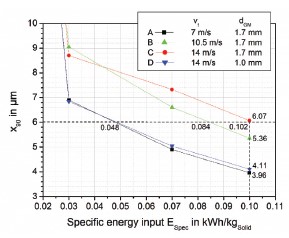
Figure 3: Comminution of limestone with different circumferential agitator shaft speeds, additional variation of the grinding bead size.[/caption]
Considering the possible production rates, it becomes clear that a higher production capacity can be achieved merely by increasing the power input due to the increase in the tip speed of the agitator shaft and thus the kinetic energy of the grinding media.
However, this higher production capacity is associated with an increased specific energy requirement. In contrast, with simultaneous optimization of the grinding bead size, the production capacity can be increased tremendously without the necessity of higher energy inputs (see Figure 4).
[caption id="attachment_143252" align="aligncenter" width="280"]
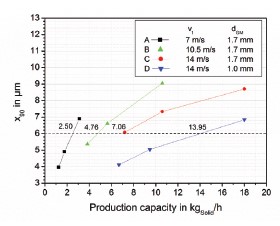
Figure 4: Production capacity as a function
of operating parameters[/caption]
3. Optimization of an Existing Peg Grinding System
Compared to the ZETA peg grinding system patented in 1991, several significant upgrades have been made with the NEOS grinding system (see Figure 5):
• The flow of the coolant in the double jacket of the grinding chamber has been optimized. In addition, a ceramic material with high wear resistance and maximum thermal conductivity is now the standard for the inner l of the grinding chamber.
• The agitator shaft has been designed such that, on the one hand, due to the flow-related optimization, the product exchange on available cooling surfaces has been improved. On the other hand, care was taken to ensure that the maximum cooling surface is available for addition rotor cooling.
The improvement in the cooling efficiency is an essential aspect in the new design of the grinding system, since in many cases the power input to the grinding chamber is limited primarily by the temperature limits of the product.
• The spacing between the grinding chamber liner and the pegs on the agitator shaft was reduced. As a result, more intensive acceleration of extremely small grinding beads is possible. This leads to a considerably higher energy density and thus to higher possible
power input to the grinding chamber.
Consequently, with the same grinding bead size, grinding media density and agitator shaft speed, this means that the grinding beads have a higher average kinetic energy. In addition, this results in higher shearing stresses on the product, which, particularly in the case of shear-thinning products, leads to a lower viscosity product in the machine.
• The diameter of the screen in the grinding media separation system was enlarged. This significantly increased the separation area of the screen. In combination with the previously-described viscosity effect, this more efficiently prevents deposits of grinding
beads and coarse product fragments at the separation screen.
Because of these new features, it was possible to use smaller grinding beads at considerably higher product throughput rates during grinding or dispersing of various products.
[caption id="attachment_143118" align="aligncenter" width="300"]
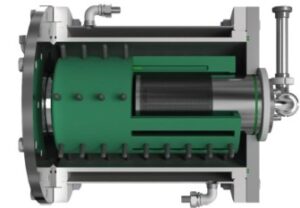
Figure 5: Basic representation of the NEOS
grinding system[/caption]
With the same grinding media fill mass, the use of smaller grinding media means that the number of grinding beads and thus the number of contacts or stresses per unit time increases exponentially.
A higher potential product throughput leads to an increase in the number of cycles per grinding time and thus to a narrower residence time distribution of the product particles in the grinding chamber.
Due to the shorter residence time of the product during one pass through the grinding chamber from the product feed to the product outlet and the consequently lower energy input, control of the product temperature is facilitated, provided that the grinding circuit is equipped with cooled batch tanks.
• In addition, the agitator shaft geometry was changed such that the circulation of the grinding media is improved without compression in the area of the grinding media separation system, even with very high product throughput rates.
This means that, with comparable installed motor power and grinding chamber sizes, a higher production capacity is not all that can be achieved. Due to the ability to use smaller grinding media and the higher product throughput rates, for a variety of products it is accompanied by a lower energy requirement as well.
This inevitably leads to reduced wear on the grinding media, less stress on the machine components and therefore reduced downtime, maintenance and spare parts costs relative to the manufactured product volume.
4. Results of Field Tests With Real Customer Product
Together with the company Siegwerk Druckfarben AG&Co. KgaA, field tests were carried out with various real products.
By switching from the ZETA grinding system to the NEOS grinding system it was possible to increase the power input to the grinding chamber of the machine over a very broad range between 18% and 143% for all products, though the potential increase in the power input is a function of several criteria.
Important factors here, in addition to the installed motor power of the machine, are
the temperature limit, the viscosity and the rheological behavior of the product. With the ZETA grinding system, depending on the viscosity of the strongly shear-thinning products, it was often not possible to reach the power limit of the machine for various products.
In contrast, with the NEOS grinding system, it was always possible to achieve the power limit of the mill without reaching the temperature limit of the product. (see Figure 6)
This can be explained of course by the cooling capacity of the machine on the one hand, but on the other hand also by the previously discussed viscosity effect. Due to the higher shearing stress and the resulting lower viscosity of the product in the mill, there is a better exchange of product near the grinding chamber wall and near the agitator shaft, which in turn results in improved heat dissipation from the grinding chamber.
[caption id="attachment_143119" align="aligncenter" width="438"]
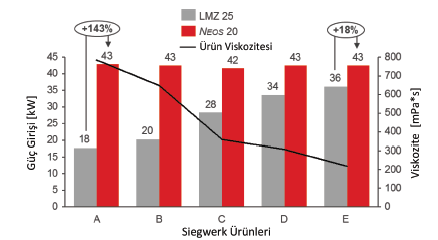
Figure 6: Performance Increase achieved by switching from ZETA 25
(LMZ 25) to NEOS 20 grinding system for various customer products [12][/caption]However, Schönstedt [12] demonstrated in particular that, depending on the product, modification of the formulation could also be necessary. Depending on the mill technology employed, changes may occur for example in the product viscosity, the color intensity,
the transparency or the gloss.
In order to achieve the specifications of the standard, it is therefore necessary in the simplest case to modify the concentration of the solvent. However, in some cases, only replacement of the binding agent yielded the desired result.
5. Summary
Field tests have shown that, with the use of a new grinding system, varied increases in the power input and thus the production capacity can be achieved.
Combined with the modification of the operating parameters of the mill and/or the formulation of the product, the specific energy requirement can be drastically reduced to some extent, even with constant product quality.
Here, important operating parameters are primarily the grinding media size and the product throughput through the mill. Decisive factors for the increase in production capacity that can be achieved are mainly product properties such as the viscosity, the rheological behavior and the temperature limits.
Further, it was shown that a partial adjustment of the formulation was required when the loading conditions on the product were changed due to the optimization of operating parameters or increase in the power density in the mill.
References
[1] N. Stehr, Zerkleinerung und Materialtransport in einer, Rührwerkskugelmühle. Tez, TU Braunschweig, 1982
[2] H. Weit Betriebsverhalten und Maßstabsvergrößerung von Rührwerkskugelmühlen. Tez, TU Braunschweig, 1987
[3] B. Joost, A. Kwade Feinstzerkleinerung, Rührwerksmühlen. Das Keramiker - Jahrbuch 1996, s. 23 -38
[4] J. Schwedes, A.Kwade, H. - H. Stender, Hochschulkurs Zerkleinern und Dispergieren mit Rührwerkskugelmühlen Umdruck zum Hochschulkurs vom Institut für Mechanische Verfahrenstechnik und Kwade + Schwedes Zerkleinerungstechnik, Braunschweig, 2008
[5] J. P. Thiel, Energiebedarf und Durchsatzverhalten der Kohlenasszerkleinerung in einer Rührwerkskugelmühle. Tez, TU Braunschweig, 1993
[6] F. Bunge, Mechanischer Zellaufschluß in Rühr¬werkskugelmühlen. Dissertation, TU Braunschweig, 1992
[7] MJ Mankosa, G. T. Adel, RH Yoon, Effect of media size in stirred ball mill grinding of coal. Toz
Teknolojisi 49, 1986, S. 75 -82
[8] R. Stadler, R. Polke Chemie, J. Schwedes, F. Vock, Naßmahlung, Rührwerkskugelmühlen.- Engenieur - Technik, 62, 907 -915, 1990
[9] D. P., Roelofsen Entwicklungen auf dem Gebiet des Pigmentdispergierens mit Rührwerkskugelmühlen. Farbe + Eksiklik 97, 1991, 3, S. 235 -242
[10] A. Kwade, Autogenzerkleinerung von Kalkstein, Rührwerkmühlen. Tez, TU Braunschweig, 1996, ISBN 3 -8265 -2082 -3
[11] H. - H. Stender, NETZSCH ile ambalaj mürekkebi üretiminin ilk endüstri test sonuçları Neos teknolojisi, sunum, Dispersiyon Günleri, 15 -17 Mayıs 2017, Selb
[12] B. Schönstedt, Yeni boncuk değirmeni teknolojisinin düzenli üretime uygulanması, sunum, Dispersiyon Günleri, 15 -17 Mayıs 2017, Selb
Dr. Stefan Mende
Feinmahltechnik GmbH-Manager
of Technical and Scientific Communication
NETZSCH
Büşra Örs
Technical Sales Engineer
NETZSCH