Frothers in Flotation
Introduction
Flotation is a widely used method in mining that provides the separation of minerals, based on their hydrophilic and hydrophobic properties patented in 1905.
In this method, air bubbles are formed by introducing air into the pulp phase, which consists of water and minerals mixed in a certain ratio. The minerals forming the solid phase are transferred to the froth phase by adhering to the air bubbles according to the surface properties. The simplified schematic view of the flotation system is shown in Figure 1.
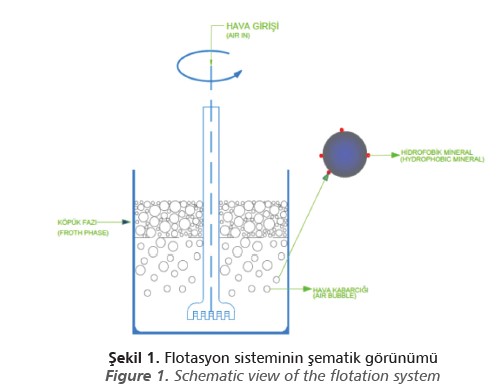
Frothers are used to produce stable froth and to reduce bubble size in flotation. Frothers facilitate the dispersal of air as fine bubbles (Gupta et al., 2007). Appropriate frother selection is very significant for flotation efficiency, as the structure and stability of frothers directly affect the froth characteristics and variables related to the entrainment of undesirable minerals.
Type and amount of frother, particle size, quality of process water, gas distribution and particle contact angle are the parameters that influence froth stability (Farrokhpay, 2011;
Schwarz and Grano, 2005).
Frother reagents are non-ionic organic compounds consisting of polar and non-polar parts. While hydrophilic/ polar groups of frothers are directed into the water phase, hydrophobic/nonpolar groups are oriented towards the air phase. The structure of the frothers and the image of the frother molecules on the bubble surfaces are given in Figures 3 and 4.
As the concentration of frother increases at the interface of the water and air bubbles, forming a film around the bubbles that prevents them from colliding. Therefore, in the presence of a frother, the forces generated around the air bubble prevent the bubbles from collapsing and bursting.
It is known that when frothers are added to water, the surface tension of the solution decreases due to its heteropolar structure. As the surface tension of the solution decreases, more stable frothers are formed and the coalescence of the bubbles in the pulp phase is prevented.
Classification of Frothers
In the literature, several different classifications have been made for frothers based on their properties and behavior in pulp. The four commonly used classification methods are;
1. pH sensitivity,
2. Solubility,
3. Froth/collector capability,
4. Selectivity/frothing power relationship.
The most widely used frother classification is pH sensitivity among these. Dudenkov and Galikov (1969) classified frothers according to their behavior and different pH values. This classification is shown in Table 1 (Khoshdast and Sam, 2011).
Acidic and Basic Frothers
Acidic frothers have been used since the 1960s and show well activity at acidic pHs. Their use is gradually decreasing due to environmental factors. Phenols and alkyl sulfonates are included in this group (Bulatovic, 2007).
Phenols are obtained as a by-product during the gasification of coal tar and/or the distillation of crude oil. The main problem with the use of phenol as a frother is that its composition varies depending on the source from which the frother is derived.
Alkyl sulfonate is an anionic frother with structure consisting of an aromatic hydrocarbon and an aliphatic radical. Although these frothers have well-foaming properties, their use is quite limited because they contain trace amounts of sulfur.
Basic frothers are mostly used in the flotation of base metal ores and are represented by pyridine and homologs recovered as by-products from the distillation of coal tar (Bulatovic, 2007).
Neutral Frothers
Neutral frothers are the most significant group of frothers that are widely used in the flotation of base metal ores, oxidized minerals and industrial minerals in both acidic and basic media.
In this frother group, the most preferred frother groups in flotation are aliphatic
alcohols, cyclic alcohols and polyglycol ethers.
Aliphatic Alcohols
Aliphatic alcohol type frothers are mixtures of alcohols containing 6-8 carbon atoms. The most well-known type of frother in this group is methyl isobutyl carbinol (MIBC), and its chemical structure is given in Figure 4.
Methyl isobutyl carbinol (MIBC), an organic chemical compound, is a liquid derivative of acetone with a pungent odor of alcohol. It has limited solubility in water but is soluble in most organic solvents (Phan et al., 2012).
MIBC is a type of frother with superior performance in flotation, so it is often used. It is cheaper than many other frothers (Tan et al., 2005). It can provide effective performance with many different ore types. It is the most effective among the aliphatic alcohol types. The froths formed with MIBC are generally large bubbles (Sam et al., 2011).
Cyclic Alcohols
Chemically, pine oil mainly consists of α-terpineol and other cyclic terpene alcohols. It may also contain ethers and esters. The composition depends on several factors, such as the type of pine from which it is produced and the parts of the tree used.
Although terpene hydrocarbons do not have frothing properties, they improve the quality of the resulting froth. Pine oil forms small froths tightly bound together, which easily bursts when removed from the machine.
This froth structure prevents mineral particles to collapse readily. Therefore, it cannot be obtained high-grade concentrate with pine oil as much as with other frothers, but the metal recovery is high. In addition, more usage of pine oil reduces the froth volume (Atak, 2017).
At first, eucalyptus oil was a popular frother in flotation, after as pine oil was more available in the west, it was popularly used as a natural oil frother. Some challenging
have been encountered in flotation as pine oil is obtained in different grades in pine growing countries such as the USA, China and Finland. Due to these, it has become less popular than MIBC (Crozier, 1992).
Polyglycol Ethers
Polyglycol ethers are methoxy polypropylene glycol or polypropylene glycol methyl ethers. Polyglycol ether type frothers are produced by different manufacturers such as Dow Chemical Company as Dowfroth and Solvay as Aerofroth.
MIBC and polyglycol ethers constitute 90% of the frother used in the flotation of metallic
ores. Dowfroth 250 is one of the most used and preferred Dowfroth type frothers and its chemical structure is shown in Figure 5 (Croizer, 1992).
Molecular weight and length of polyglycol ether carbon affect power and performance of frother. It has been observed that more durable froth is formed at higher molecular weights, while it is less selective at lower molecular weights.
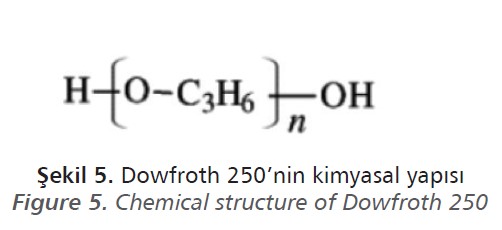
The physical and chemical properties of MIBC, pine oil and Dowfroth 250, which are the most used frothers in the neutral frother group in flotation, are given in Table 2.
Kaynaklar
• Atak, S. 2017. Flotasyon Cevher Hazırlamada 100 Yıl. İstanbul: İTÜ Vakfı Yayınları.
• Bulatovic, S. M., 2007. Handbook of Flotation Reagents (Chemistry, Theory and Practice: Flotation of Sulfide Ores), vol.1. Amsterdam: Elsevier Science & Technology Books.
• Crozier, R.D., 1992. Chemical Properties of Frothers: Flotation—Theory, Reagent and Ore Testing; Pergamon: New York, NY, USA.
• Dudenkov, S.V., A.A. Galikov, 1969.Theory and Practice of Application of Flotation Reagents. Nedra: Russia.
• Farrokhpay, S., 2011. The significance of froth stability in mineral flotation — A review. Advances in Colloid and Interface Science, 166, 1-7.
• Gupta, A. K., Banerjee, P. K., Mishra, A., Satish, P., Pradip, 2007. Effect of alcohol and polyglycol ether frothers on foam stability, bubble size and coal flotation. International Journal of Mineral Processing, 82, 126-137.
• Phan, C., M., Nakahara H., Shibata, O., Moroi, Y., Le, T., N., and Ang, H., M., 2012. Surface Potential of Methyl Isobutyl Carbinol Adsorption Layer at the Air/Water Interface. The Journal of Physical Chemistry B, 980-986.
• Sam, A., Khoshdast, H., 2011. Flotation Frothers: Review of Their Classifications, Properties and Preparation. The open mineral processing journal, 4, 25-44.
• Schwarz, S., Grano, S., 2005. Effect of particle hydrophobicity on particle and water transport across a flotation froth. Colloids and Surfaces A, 256, 157-164.
• Tan, S. N., Pugh, R. J., Fornasiero, D., Sedev, R., Ralston, J., 2005. Foaming of polypropylene glycols and glycol/ MIBC mixtures. Mineral Engineering, 18(2), 179-188.
Dr. Ş. Beste Aydın
Mineral Processing Engineering Department
Istanbul Technical University
Prof. Dr. Gülay Bulut
Mineral Processing Engineering Department
Istanbul Technical University