1. Galvanizasyonun Temel Malzeme Üzerindeki Etkisi
Konstrüksiyon ve bileşenler kural olarak temel malzemenin mekanik özelliklerinin zorlandığı gerilmelere maruz kalır. Bu husus aynı zamanda korozyon koruması nedeniyle elektrogalvaniz işlemine tabi tutulan parçalar için de geçerlidir. Bu nedenle, galvanizasyon temel malzemenin mekanik özelliklerini etkileyebilir.
Çeşitli araştırmalara göre, elektrogalvaniz işlemine tabi tutulan çinko katmanlarının çekme yükü gibi çekme dayanımı alanındaki etkileri oldukça az olup, elektro kaplama işleminin bir sonucu olarak biriken diğer metallerin etkilerine göre daha azdır (deformasyonu engelleyen krom hariç).
Buna göre, ana çinko katmanındaki iç gerilmelerin dahi, temel malzemeye etki etmediği söylenebilir. Asidik elektrolitlerde gerçekleştirilen galvanizasyon işleminde, yorulma dayanımı ve yapısal dayanım gibi dinamik yorulma özellikleri üzerinde herhangi bir etki gözlenmez.
Ancak, düşük akım verimi ve yüksek hidrojen gelişimi ile alkalin elektrolitler içinde galvanizasyon yaparken bu durum gözlenmez. Sonuç olarak, temel malzemenin özelliklerine göre hidrojen gevrekleşmesine neden olabilecek daha güçlü veya güçsüz bir hidrojen yüklemesi gerçekleşir.
Örneğin, galvanizli yay çeliği numuneleriyle yapılan bükme testlerinde, çinko tabakası bir alkalin elektrolitten ayrıştırıldığında temel malzeme üzerinde önemli ölçüde daha kötü zayıf davrandığı tespit edilmiştir.
Bükme katsayısı ve artan çinko katman kalınlığı ile kırılacak bükülme sayısı, katmanlar asidik elektrolit olduğunda zorlukla değişirken, alkalin elektrolit kullanıldığında sert bir şekilde düşer (bkz. Şekil 1).
Bunların yanı sıra yapılan pek çok incelemede, galvanizasyonun temel etkisinin hidrojen yüklemesi ve bunun neden olduğu hidrojen gevrekleşmesinden kaynaklandığı görülmüştür.
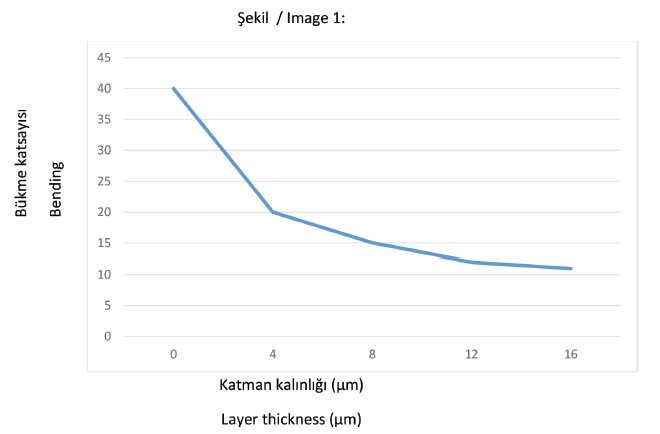
Malzemedeki bu gevrek kırıkların nedeni genelde hidrojen emilimidir. Bu da genelde makro ölçekte bir şekilde değişiklik olmadan çatlaklarda meydana geldiği için, malzeme ve bileşenlerin davranışı için çok tehlikeli olabilir.
Bunlar hemen ortaya çıkmaz, önceden fark edilmeden malzeme uzun bir süre kullanıldıktan sonra aniden ortaya çıkar. Bu nedenlerden dolayı, hidrojen kaynaklı çatlak oluşumu veya katodik gerilme korozyonu çatlaması ifadeleri, özellikle bilimsel literatürde kısmen hidrojen gevrekliği yerine kullanılmaktadır.
Bu sorun son zamanlarda özellikle düşük alaşımlı veya alaşımsız yüksek mukavemetli çeliklere daha fazla ve giderek yüksek oranda ısıl işlem uygulanmasıyla çeliğin mukavemetinden daha fazla yararlanılmak istenmesi nedeniyle daha kronik bir hal almıştır.
Malzeme bu şekilde tokluğunu yitirerek, özellikle hidrojen difüzyonuna karşı hassas hale gelir.
2. Bir Sistem Özelliği Olarak Hidrojen Gevrekleşmesi
Bir malzemenin gevrekleşmesi, görece küçük bir mekanik enerji emiliminin dahi giderilemeyecek bir hasara yol açabileceği bir düşük süneklik hali olarak tanımlanır. Malzemenin içine hidrojen girmesi nedeniyle meydana gelirse, hidrojen gevrekliği olarak adlandırılır.
Belirli koşullar altında hidrojenin absorbe edilmesi sonucunda temel malzemenin elastik özellikleri büyük oranda etkilenir, kırılgan hale gelir ve kademeli etkiyen mekanik bir yüke karşı yeterli direnci gösteremez. Darbe veya gerilme etkisi gibi ani bir zorlanmaya karşı davranış az miktarda değişse de, plastik alanda güçlü bir etki gözlenir.
Gerilme mukavemeti, çentik darbe mukavemeti ve benzerleri gibi özellikler genel olarak bozulmaz, ancak süneklik, akma dayanımı, uzama, daralma, eğilme dayanımı vb. etkilenir. Daha önce belirtildiği gibi, bu sonuç çok, tehlikeli ve genellikle ani meydana gelen bir malzeme ayrışmasını temsil eden gevrek kırılma olarak adlandırılabilir.
Temel malzeme veya bileşen üzerindeki hidrojen etkisi, üç koşula bağlıdır: Yeterli hidrojen varlığı olmalı, temel malzemede yeterli hidrojen yüklemesi olmalı ve son olarak, malzemede veya bileşenin mekanik özelliklerinin hidrojen nedeniyle etkilenmesini sağlayan uygun koşullar mevcut olmalıdır.
Tüm faktörler ve parametreler birbirlerini olumlu ve olumsuz olarak etkileyebilir. Bu nedenle, hidrojen gevrekleşmesi genellikle yalnızca bir değil, birden fazla etkileyici faktöre bağlı olup, çeşitli nedenlere atfedilebilir. Bu nedenle, sistem özelliği karakterine sahiptir.
2.1 Elektrogalvanizasyonda Hidrojen Beslemesi
Galvanik yüzey işleminde, hidrojen esas olarak üç işlem adımında malzemenin veya temel malzemenin içine girebilir:
•Paklamada,
•Katodik ön işlemlerde ve,
•Elektrolitik metal bırakımında.
Malzemeye giren hidrojenin baskın kısmının elektrikli bırakımdan değil, ön işlemden kaynaklandığı açık bir şekilde kabul edilebilir. Yaygın görüşe göre, hidrojen gevrekliğinin çinko bırakım işleminden (ve ayrıca diğer galvanik katmanlı metallerden) kaynaklanması çoğu durumda doğru değildir.
Paklama, malzemenin anodizasyonunun anodik bölgelerde gerçekleştiği, hidrojen iyonlarının azalması ve katodik bölgelerde hidrojen atomlarının oluşması ile sonuçlanan bir elektrokimyasal reaksiyondur.
Bu işlem, katod yüzeylerinde, elektrolitik yağ giderme ve metalde elektrikli bırakım nedeniyle de gerçekleşir, ancak daha sonra sadece akım verimi %100’den az olduğunda gerçekleşir.
Hidrojen atomları ilk önce bileşen yüzeyinde adsorbe edilir, daha sonra (koşullara bağlı olarak daha hızlı veya daha yavaş bir şekilde) hidrojen gazı olarak çıkan hidrojen moleküllerine yeniden bağlanır.
Bu işlemler aşağıdaki gibi açıklanabilir: Hidrojen iyonları (protonlar H+) genelde suya bağlıdır ve hidronyum iyonu (H3O+) formundadır. Hidronyum iyonları, faz sınırındaki malzemede / sıvıda hidrat kabuğundan serbest bırakılır, indirgeme (elektron alımı) ile boşaltılır ve metal yüzeyine bağlanır:
H3O+ → H2O + H+
H+ + e- → Had
Bağlanan her iki hidrojen atomu, bir hidrojen molekülü oluşturmak üzere malzeme yüzeyinde yeniden birleşebilir:
Had + Had → H2,ad
Bağlanan hidrojen H2,ad ayrılarak çözeltiye difüze edilir veya hidrojen gazı olarak dışarı çıkar. Hidrojen böylece metal yüzeye hem atomik hem de moleküler şekilde geçer.
2.2 Galvanizlemede Hidrojen Difüzyonu Mekanizması
Hidrojenin malzeme yüzeyine difüzyonu için atomik formda bulunması gerekir. Hidrojen atomları küçük çaplarından dolayı malzemeye nüfuz eder, kafes kusurlarını, tane sınırlarını ve mikro çatlak alanlarını doldurur, aynı zamanda (mevcut koşullara bağlı olarak) kristallerin içinden de geçebilir.
Hidrojenle etkilenen 30 μm derinliğe ulaşabilen yüzey katmanları oluşur. Moleküler hidrojen difüzyonla nüfuz edemez. Yüzey çok gözenekli ise, daha büyük çatlaklar veya boşluklar varsa, hidrojen moleküler halde olsa bile nüfuz edebilir.
Bununla birlikte, faz sınırlarında olan yüksek hidrojen konsantrasyonunda, hidrojen moleküllerinin tekrar ayrışıp atomik biçimde difüze edilmesi görülebilir. Uygun formda olması dışında, hidrojen ayrıca temel malzemenin yüzeyi ile doğrudan temas halinde olmalıdır.
Difüzyonun gerçekleşebilmesi için kısmen hidrojen ile dolu olması gerekir. Bununla birlikte, elektrolitik galvanizasyonda, faz sınırındaki absorbe edilebilir hidrojen, temel malzeme ile çinko tabakası arasında dağıtılır.
Ancak, temel malzemenin özellikleri sadece yüzeyde difüze edilen oranı etkileyebilir. Bu oranın ne kadar büyük olduğu, hem elektrolite hem de galvanizasyon koşullarına ve temel malzemeye bağlıdır.
2.2.1 Elektroliz Koşullarının Etkisi
Galvanizasyon işlemi sırasında, hidrojen belirli aktif bölgelerden başlayarak, çinko ile aynı anda çökeltilir, ardından tüm yüzey üzerinde yoğun bir çinko tabakası oluşturur.
Bu nedenle hidrojen atomlarının adsorpsiyonu, önce faz sınırındaki temel malzemede / elektrolitte, ardından faz sınırındaki çinko katmanında / elektrolitte artan bir oranda gerçekleşir. Ne kadar fazla çinko ayrılırsa, hidrojen aşırı yüklenme oranı o kadar artar.
Son olarak, tüm yüzeyin yoğun bir çinko tabakası ile kaplanması, hidrojenin temel malzeme içine daha fazla yayılmasını engeller. Genel olarak, bu durumda 0,5 ila 1 μm kalınlığında bir katman oluşur.
2 μm kalınlığındaki katman hidrojene karşı iyi bir difüzyon bariyeri teşkil eder. Böyle bir katmanın oluşumu için gereken süre, hidrojenin temel malzemeye difüzyonu ve dolayısıyla hidrojen gevrekleşmesi için kritiktir. Farklı çinko elektrolitler için uzunluğu farklı olup aşağıdaki gibidir:
•Yüksek siyanürlü elektrolit için 56 mAs / cm²,
•Alkali siyanür içermeyen elektrolit için 18 mAs / cm² ve
•Zayıf asitli elektrolit için 6.7 mAs / cm².
Bu katman oluştuktan sonra, temel malzemede hidrojen difüzyonu gerçekleşmez. Elektrolitin akım veriminin, hidrojen yükü üzerinde hiçbir etkisi yoktur. Hidrojen sadece çinko katmanda absorbe edilir.
Farklı hidrojen absorpsiyonu nedeniyle iki mekanizma öne çıkar. Parlatıcı içermeyen Kanada banyoları için genelde gözenek mekanizması geçerliyken, partlatıcı içeren banyolarda absorpsiyon-difüsyon mekanizması geçerlidir.
Bu mekanizmalar, difüze hidrojen kaynağının farklı olmasına göre birbirinde ayrılır. Diğer taraftan, absorpsiyon- difüzyon mekanizmasında, çinko tabakasında absorbe edilen ve buradan temel malzemeye nüfuz eden söz konusuyken, gözenek mekanizmasında, temel malzemenin açık noktalarındaki bırakım başlangıcında absorbe edilen hidrojen söz konusudur.
Çinko tabakasında daha az hidrojen emildiğinden ikinci işlem daha yavaştır. Hidrojen konsantrasyonunun gradyanı ne kadar düşük olursa, çinko tabakası tercihen öncekine kıyasla daha fazla hidrojen içermemelidir.
Bu nedenle, çelikte hidrojen absorbe etme oranı ve bırakım sırasındaki değişimler, esas olarak tabaka oluşum parametrelerine bağlı olup, kaplanmış çeliklerde daha az görülür.
Kural olarak, çinko bırakımı daha hızlı olduğu ve yoğun bir tabaka oluşturduğu sürece, hidrojen yükleme riski de o oranda azalır. Bu nedenle, yüksek akım yoğunluklarında çalışma uygundur.
2.2.2 Temel Malzemenin Etkisi
Alaşımsız veya zayıf alaşımlı yüksek mukavemetli çeliklerin hidrojeni absorbe etme eğilimi üzerinde durulmuştur. Bunun dışında, karbon içeriği >% 0,5 olan çelikler hidrojen yüklemesine karşı daha duyarlı olmalıdır. Krom, tungsten ve nikelin alaşım bileşiklerinin etkisine dair görüşler farklılık göstermektedir.
Yüzeydeki mikro çatlaklar, mikro gözenekler, boşluklar ve diğer düzensizlikler hidrojen penetrasyonunu arttırır. Bu olumsuzluklar, galvanik kaplamadan önce malzemenin ciddi şekilde deforme olması durumunda veya mekanik taşlama veya polisaj işlemiyle pürüzlü hale gelmesi veya hasar görmesi durumunda söz konusu olabilir.
Kimyasal veya elektrokimyasal olarak parlatılmış bir yüzey, mekanik işlem görmüş bir yüzeye kıyasla hidrojenin sadece %30 ila 40’ını absorbe eder. Bununla birlikte, pürüzlü yüzeyler, pürüzlü bölgelerdeki hidrojen atomları tercihen moleküller halinde yeniden birleştirildiğinde, hidrojen yükleme eğilimini de azaltabilir.
Hidrojen difüzyonu, yüzey kirleticileri, karbon, fosfor, kurşun veya kalay gibi temas zehirleri içerdiğinde tercih edilir. Bunlar hidrojen aşırı potansiyelini düşürür ve çinko tabakasının büyümesini yavaşlatırlar. Yapının önemli bir etkisi vardır. Temel malzemede hidrojen yüklenmesi, özellikle zorlanma veya bozulma durumunda yüksektir.
Bu durum, önceden soğuk işlem veya ısıl işlem (sertleştirme, sementasyon) yapılarak önlenebilir. Hidrojen, bu gibi durumlarda kafes içine girerek, daha sonra oda sıcaklığında veya daha yüksek sıcaklıklarda tekrar çıkarsa, kafes büzülmesine neden olur.
Mikro yapıdaki anomalilerde hidrojenin davranışı ile ilgili teoriler oldukça farklıdır.
3. Hidrojen Gevrekleşmesini Önleme
Hidrojen gevrekleşmesi bir sistem özelliğidir. Engellenmek isteniyorsa, hem malzemede hem de bileşende, galvanik yüzey işleminde etkileyen tüm alanlarda önlemler alınmalıdır. Genel olarak, malzeme ve bileşene dayanan önlemler tercih edilmelidir.
Kritik hidrojen yüklemesi,çoğu durumda sadece üretim teknolojileri zincirindeki son işlemden sonra önlenebilir, bu da yüzey işleminin gerçekleştiği ve bu nedenle kusurun daha sonra bulunduğu anlamına gelir. Bu gibi kritik durumlarda, yüzey işlemede galvanizasyon bölümünde mümkün olan önlemler alınmalıdır.
Uygulamada, sertleştirilmiş parçalar, temperli vidalar, yaylar ve yüksek mukavemetli çelikten mamül parçalar veya soğuk kesim, soğuk haddeleme veya çekme yoluyla üretilenler parçalar varsa, hidrojen gevrekleşmesi beklenmelidir.
Teknik olarak önemli alaşımsız karbon çelikler ve düşük alaşımlı temperlenmiş çeliklerde, 1200 N/mm²’lik çekme dayanımı kritik olarak kabul edilmelidir; bunu önlemek için aşağıda açıklanan önlemlerin alınması gereklidir.
Titanyumdan mamül malzemeler de hidrojen gevrekleşmesine duyarlı malzemeler arasındadır. Bu tür önlemlerin verimliliği, DIN 50969’a göre veya onaylı bir test ile tespit edilebilir.
3.1 Galvanik Yüzey İşleme İçin Önlemler
Galvanik yüzey işlemindeki önlemler, ön işlemlerde, elektrikli bırakım ve işlem sonrası yapılacak müdahalelerle mümkün veya gereklidir.
3.1.1 İşlem Öncesi Alınacak Önlemler
•Tüm ön işlem prosedürleri için maruz kalma süreleri mümkün olduğunca kısa tutulmalıdır.
•Sadece hidrojen atomlarının H2 moleküllerine rekombinasyonunu aynı anda engellemeyen bu tür inhibitörlerin eklenmesi ile dekapaj yapılması.
Özellikle hassas parçalar söz konusu olduğunda, paklama işlemi koruyucu gaz atmosferinde gerçekleştirilmelidir. Paklama sırasında hidrojen yüklemesi kaçınılmazsa, ara temperleme işlemi gerekebilir (genellikle 150°C’de 0.5 saat).
•Yüksek mukavemetli parçalarda, özellikle emniyet parçaları için, sadece temizleme ve aktifleştirme için kumlama gibi (havacılıkta özellikle risk altındaki parçalar söz konusu olduğunda, kumlama maddesi olarak tanımlı bir alüminyum oksit ile kumlama yaparak) mekanik yöntemler kullanılmalıdır.
•Elektrolitik olarak sadece anodik yağ alımı.
3.1.2 Esas Galvanizasyon İçin Önlemler
•Hidrojen difüzyonunu engelleyen minimum bariyer tabakası kalınlığı olan 0,5 μm’a hızlı bir şekilde ulaşmak için iyi kaplanmış bir elektrolit seçimi. Kural olarak, asidik elektrolit uygundur.
•Somut bir uygulamada elde edilebilecek koşullar altında, mümkün olduğunca %100 akım verimi olan elektrolit kullanımı.
•Elektrogalvanizasyon işleminini düzgün değişen doğru akımla gerçekleştirme. Uygun parametreleri seçerek, ince taneli ve düşük zorlanmalı tabakalar elde edilmesini sağlayan kristalleşme koşulları sağlanabilir.
3.1.3 Temperleme ile İşlem Sonrası
•Hangi işlem adımının gerçekleştirildiğine bakılmaksızın, işlem sonrası temperleme en geç 24 saat sonra yapılır. Hidrojenin büyük kısmı 0.1 - 0.2 μm kalınlığındaki ilk çinko katmanındadır.
Bu nedenle, galvanizleme işleminden hemen sonra tavlama yapılırsa, faz sınırında zenginleştirilen hidrojenin temel malzeme içine değil çinko tabakadan dışarı yayılma olasılığı söz konusu olabilir. Ancak, bu da çok kalın olmamalı ve bir parlatma banyosundan gelmemelidir.
Temperlenmeye kadar geçen süre uzarsa, sadece faz sınırından gelen hidrojen değil, bazı durumlarda parlak çinko kaplamadan gelen hidrojen de temel malzemeye yayılabilir.
•Çok hızlı bir şekilde yayılan hidrojenden dolayı temel malzeme ve çinko katmana zarar gelmemesi için istenilen sıcaklığa kadar ısıtma işlemi kademeli olarak gerçekleştirilmelidir.
•Hidrojenin (ince, katkı maddesi içermeyen çinko tabakasından) kaçma ihtimali varsa, ayrıca bir yağ banyosunda da, 140 ila 200°C’de 2 ila 3 saat boyunca bekletmek genelde yeterlidir. Bileşenlerin daha yüksek deformasyon derecelerinde daha uzun tutma sürelerinin olması gerekli olabilir.
•Yüksek mukavemetli çelikler ve yüksek zorlanmalı yapılarda, örneğin pekleşmede, temperleme sıcaklığı ve malzeme durumuyla sınırlanan en yüksek sıcaklık ve temperleme süresi aşılmamalıdır. Kılavuz değerler Tablo 1’de verilmiştir.
* Isıl işlem, galvanizasyon işleminden hemen sonra yapılmalıdır.
İzzet Aydın
Genel Müdür
Hillebrand Chemicals Kimyasal Pazarlama Ltd. Şti.
Kaynaklar:
Metalloberfläche, Paatsch W.
DIN 50969.
Metalloberfläche, Tolls E.
Materials Performance, Isecke B.
Zasc. met., Schitanow W.J.
Korr. und Metallschutz, Fischer H.