Superior Performance in Transparent Resins with EGECat® ClearCo Series
Unsaturated polyester resins (UPR) are the general name of a very wide class that has many applications today. Although the first applications were seen during WWII, it now has a variety of applications in many fields, including building and construction materials, vehicle parts used in land and sea transportation, infrastructure products, the energy and defense industries, textiles (buttons, accessories), and sports equipment.
UPR are formed as a result of the condensation reaction of diacid(s)/anhydride(s) and glycol(s). The ratio of acids/anhydrides to glycols in the formulation vary according to the desired resin properties. The resin obtained at the end of the reaction contains unsaturated
double bonds and is dissolved in reactive diluents.
The next step, the curing process of the resin, starts with peroxide addition, is controlled by accelerators and other additives. Various additives can be added to the resin structure according to the desired properties.
The accelerators are most often a metal carboxylate. Metal carboxylates accelerate the free radical polymerization reaction that begins on the unsaturated polyester resin through the decomposition of the peroxide.
Cobalt, Potassium and Copper are the metals commonly used as accelerators. Other metals such as, Barium, Calcium and Manganese have been used but little or no benefit to the final resin properties are achieved with these metal carboxylates. Catalyst addition amounts are determined by the desired gel time, cure time, and peak exotherm temperature.
The levels of catalyst will vary depending on the reactivity and type of unsaturated polyester used, as well as the application. Other determining factors for performance
are inhibitor types, levels, and the usage of other additives.
Cobalt is utilized primarily to achieve the desired gel time while taking an active role in the free radical polymerization reaction. It is the primary (oxidative) and most important accelerator. For cobalt the oxidation (2+ to 3+) and reduction (3+ to 2+) potentials are
similar and this makes cobalt a very effective accelerator.
In both processes the cobalt produces radicals yet, cobalt oxidation is the predominant process. So, during the redox reaction there is a steady build up of Co3+ salts until the polymer is cured. The accumulation of excess Co3+ salts at the end of the curing
process can lead to a discoloration of the cured resin, a phenomenon called pinking.
The pinking effect caused by the use of cobalt carboxylate is a major problem for low color end products, such as clear casts and artificial marble. Cobalt carboxylates are used in almost all unsaturated polyester-based composite applications because of their unique redox potential.
This requirement makes pinking effect a serious problem for users. In order to solve the ongoing serious problem, Ege Kimya has developed the EGECat® ClearCo series. EGECat® ClearCo series are special complexes which have reduced cobalt metal content. It consists of EGECat® ClearCo 101 and EGECat® ClearCo 102.
EGECat®ClearCo 101 is 2% Co and EGECat® ClearCo 102 s 1% Co. Both products are designed to maintain gel and cure characteristics whilst reducing the discoloration
in end products.
EGECat®ClearCo series has been tested in isophthalic and orthophthalic resins using MEK peroxide as the initiator and compared to standard cobalt neodecanoate 6%. Gel time, peak time and peak temperature values are shown in (Table I). No additional inhibitors or co-catalysts were used in the tests.
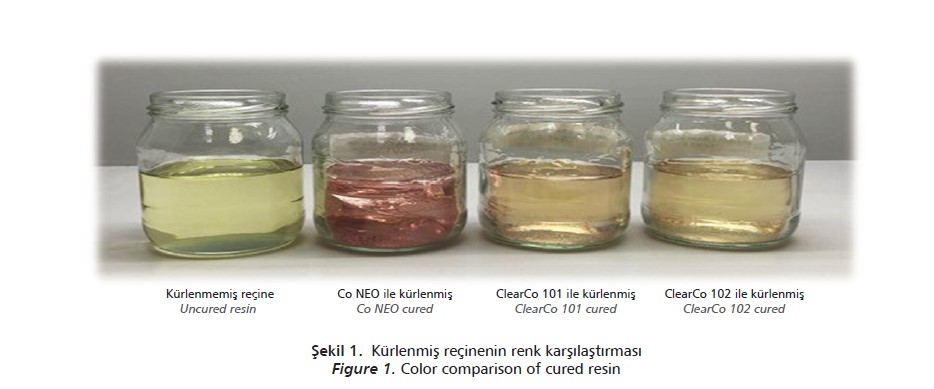
These results show that EGECat® ClearCo 101 and EGECat® ClearCo 102 can provide similar gel time, cure time and peak exotherm performance compared to a standard cobalt carboxylate in isophthalic or orthophthalic resins.
EGECat® ClearCo 101 and EGECat® ClearCo 102 with lower cobalt content, showed much lighter color without any performance loss (Figure I).
M.Sc. Bahar Taylanlı - R&D Assistant Specialist
Ege Kimya
Dr. Andrew Mason - Technical Sales Manager
Ege Kimya