Dispensing systems are systems that enable the production of liquid or semi-liquid products, which are generally prepared on the basis of prescriptions, by dosing automatically and precisely.
Although it is used in many different sectors, in this article we will talk about its effects on quality in liquid ink and industrial paint applications, where it is used the most.
Automation and Prevention of Human Errors
Many companies decide to invest in a dispensing system because of the quality problems they experience as they prepare their products by hand beforehand.
Today, quality expectations in every sector are constantly increasing. In order to meet these expectations, it is necessary to minimize the differences between product lots. At this point, the margin of error is always higher in products prepared by human hands and it becomes difficult to achieve a standard.
In the use of the dispensing system, on the other hand, since the production can be made
with an error margin of ± 1 g, the differences between the lots can be minimized.
Traceability
It is very difficult to determine the source of the error in a possible quality problem, since the records of the errors made in the products prepared manually by humans cannot be kept properly. It will not be possible to be sensitive enough in manual dosing, and it will never be possible to be sure that the mistakes made are recorded correctly.
Since all operations made in dispensing systems are recorded, retrospective traceability is provided. In fact, while the product with quality problems is being prepared, the amount of error made in dosing each component and the manufacturer lot numbers of all components (raw materials) used in the product can be accessed. Thus, it becomes easier to identify the source of the quality problem.
Keeping The Raw Materials Ready for Production
The components that make up the products, especially in inks and paints, generally consist of color pastes, varnish-binder-bases, some additives and thinners. While these components are waiting before use, problems such as precipitation, drying, crusting, separation or viscosity change due to evaporation may occur.
In order to ensure that the quality and color of the product to be prepared are
always at the same standards, these components to be used must also be made ready for use.
Products with precipitation or decomposition must be mixed before use to become homogeneous. During this mixing process, there will be a rapid evaporation, especially in solvent-based products, since the lid of the container containing the component is mostly
opened.
This will cause the standard viscosity of the component to be used to change. If the viscosity is not adjusted again before use, a quality problem may arise in the product to be produced. If there are problems such as crusting or drying, these should also be removed before use.
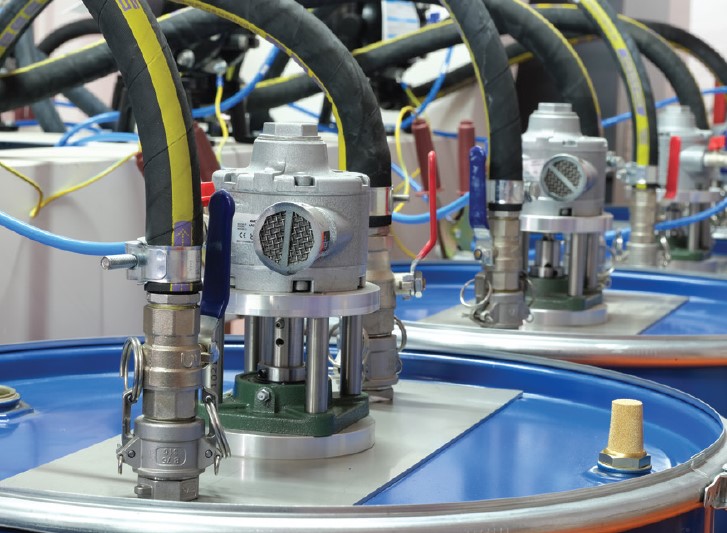
In products that are prepared manually, these situations can sometimes be overlooked and the production is carried out before the components are prepared well enough.
In the use of the dispensing system, on the other hand, since all the components connected to the system are stored in a closed system, problems such as viscosity change due to crusting and evaporation can be minimized.
In addition, all components can be kept homogeneous with the recirculation system in
the dispensing systems. The recirculation system can be operated automatically at desired times.
Thus, especially the components that tend to settle rapidly can be circulated more frequently so that they always remain homogeneous. In cases where the recirculation system is not sufficient, barrels or IBC mixers are mounted to the system to ensure better
mixing of the components.
As a result of all these, the components in the Dispensing system are always kept ready for use, ensuring that the quality levels of the products to be produced are also standard.
As mentioned at the beginning of the article, in order to better meet the increasing quality expectations today, the dispensing system investments have been decided not only according to the production tonnages, but also according to the quality increase.
As Kairos, it has always been one of our main goals to contribute to our customers’ better
quality and standard production with the ADAColor
Dispensing systems we produce in Turkey.
Deniz Sülar
Yönetim Kurulu Başkanı
Kairos Makina