Many basic substances for the production of biochemicals are obtained by fermentation from renewable resources. The range covers alcohols, organic acids such as lactic acid and citric acid, enzymes as well as biomonomers and -polymers.
Figure 1 shows a principle flow scheme of a fermentation process with possible applications for membrane filtration technologies marked in blue.
Fig. 1: Principle scheme of a fermentation process.
Cross-flow membrane filtration technology plays an important role in the downstream processing of high-purity biochemicals, which are necessary for the production of high quality and competitive products. Membrane filtration plants are used for biomass separation, isolation and purification of valuable substances and preliminary concentration.
Biomass Separation
The biomass separation by means of membrane filtration has the crucial advantage that a solid-free fermentation solution (filtrate) can be produced in a continuous and almost maintenance- free operation.
Preferably, ceramic membranes are used as they also reject genetically modified organism (GMO) from the filtrate (containment). Alternatively, combinations of centrifuges and membrane plants equipped with spiral wound modules can be applied.
Fig. 2: Pilot plant with ceramic membrane modules.
Isolation and Purification of Valuable Substances
After the biomass has been separated, the valuable substances are isolated from the fermentation solution. For this purpose, ultrafiltration and nanofiltration are used in a 2-step fractionation process. Most often diafiltration water will be added to increase yield and purity.
Fig. 3: Ultrafiltration plant with polymer membranes.
Concentration
Membrane filtration plants can also be used for the pre-concentration of large process streams before evaporation plants, especially for aqueous solutions in the case of low viscosities. This will significantly reduce the operation costs of the evaporator.
Cross-Flow Membrane Filtration – The Technology Behind
In cross-flow membrane filtration technology the product tangentially flows over the membranes (cross flow) contrary to the normal cake filtration (dead end). This allows a continuous operation over extended periods.
Cross-flow membrane filtration is a pressure driven technology with pore sizes ranging from 100 g/mol of molecular weight up to 5 microns. Depending on the application, different membranes and system configurations are possible.
Reverse Osmosis (RO)
Reverse Osmosis is a high pressure, energy-efficient process for the de-watering of process streams, concentration of low molecular weight compounds or purification of waste effluents. Common applications include pre-concentration of streams prior to evaporation and purification of process water.
Nanofiltration (NF)
Nanofiltration is a unique filtration process in-between UF and RO designed to achieve highly specific separation of low molecular weight compounds such as minerals and salts from complex process streams.
Typical applications are the purification of fermented products, recovery of hydrolyzed proteins, concentration of sugars and purification of soluble dyes and pigments.
Ultrafiltration (UF)
Ultrafiltration is a selective separation step used to concentrate and purify medium of high molecular weight components such as proteins, carbohydrates and enzymes. Common areas of application include the purification of fermented products, gelatin de-ashing and concentration, and clarification of juices.
Microfiltration (MF)
Microfiltration is a low pressure process for the separation of suspended or colloidal compounds with a high molecular weight from dissolved solids. Applications include cell harvesting from fermentation broths, fractionation of proteins, clarification of sugar solutions and CIP chemical recovery.
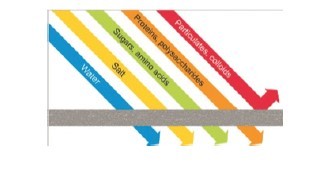
Various system configurations and membrane types allow the optimization of specific separation applications. The range of membrane types includes a number of both polymeric (spiral, tubular and hollow fiber) and inorganic membranes (ceramic and stainless steel).
The ability to produce very specific separations at low or ambient temperatures with no phase change can make membrane filtration a much more gentle and cost-effective process solution than conventional methods in many applications.
Benefits compared with other methods of separation include: accurate separation of multiple streams, reduced risk of product damage especially for heat-sensitive products, no loss of nutritional value or clinical efficacy, reduced energy consumption, higher yields, and greater flexibility of new product development.
GEA specializes in individually designed membrane filtration plants and complete process lines tailored to customer requirements. GEA operates test facilities with various pilot plants for product testing and the development and optimization of fluid recovery processes.
This allows customers to demonstrate practically the feasibility and effectiveness of recovery processes before adopting them within the plant. Pilot plants supplied by GEA on skids can be integrated at customers’ premises for more extensive testing ahead of full-scale production.
Christian Entrup
Process Engineer - Membrane Filtration
GEA
İlker Damar
Sales Manager
Industrial Applications
GEA Türkiye