Creating Effective Defoamers and Deaerators by Design of Experiment (DOE) Method
Not a day goes by that we do not come across a foamy material such as coffee, fizzy drinks, soaps, insulation materials (polyurethane foam) and so forth. Foam is a desired feature for this kind of materials and wellaccepted in our daily life. Especially, a foamy Turkish coffee is indispensable.
For paint manufacturers and applicators this case is completely an opposite phenomenon. Foam control is a mandatory work during the manufacture and application of paint to provide smooth and competent paints. Therefore, usage of highly efficient defoamers and deaerators in paints and coatings is necessary to eliminate the existing foam. Defoamers and deaerators prevent the formation of foam during the production, application and transportation of paints to ensure that the performance of the paints remains at the desired level.
Foam formation is a serious and undesired problem, especially in industrial applications such as dispersion, pumping and mixing process or during the application of paints. The formed foam may cause an increase on the production time (e.g., dispersion time),
generate difficulties effective and productive filling of vessels, reduce the efficiency of stirring operations and formation of paint defects on the surface of coatings such as craters, fish eyes and pinholes*.
Basically, foam is a dispersed gas bubbles (air, carbon dioxide, nitrogen etc.) in liquid paints. In pure liquids like water, formed foam is thermodynamically unstable which the foam occurs rapidly and quickly rise to the surface of the liquid, and collapsed immediately [Figure 1 (a)]. However, as everyone has experienced when adding soap to water, soap generates and stabilizes huge amount of foam due to its surface-active structure. Just as it is, wetting agents and emulgators present in water-based paints, inks and adhesive
formulations act as a surface-active agent to stabilize of formed foams. Surface-active agents prevent the coalescence of trapped bubbles formed in liquid paints by wrapping the bubble surface, therefore slows down the rising speed of the bubbles to the surface and stabilize them as micro-foam** in the liquid body. The foams succeeded to reach the surface of the liquid paint can be described as macro-foam [Figure 1 (b)].
[caption id="attachment_136867" align="aligncenter" width="633"]
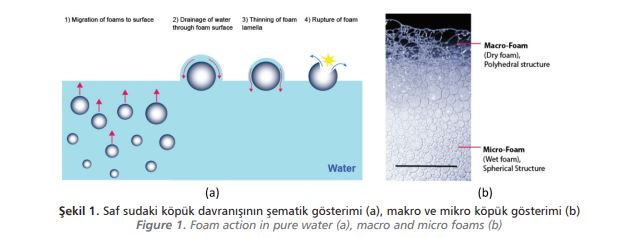
Figure 1. Foam action in pure water (a), macro and micro foams (b)[/caption]
Defoamers and deaerators can be classified differently from each other due to their working mechanism on different type of foam. While defoamers are effective on macro-foams existing on the surface of the liquid, deaerators destroy the micro-foams which are trapped inside the liquid body. It is not always easy to visual observation micro-foams because of their tiny bubble structures. However, they can be detected by lower density of paint than expected. The main principle of deaeration is to coalescence of micro-foams to form larger bubbles which can be removed from the paint more quickly. Micro-foams try to reach to
the surface right after formed in the liquid. As stated in Stoke’s Law***, rising speed of foam to surface depends on foam diameter and liquid viscosity. The lower the viscosity of liquid, the faster they rise to the surface.
The rising speed of the foam to surface of the liquid depend on the square of radius according to Stoke’s Law. Therefore, the diameter of the foams is more effective on rising speed than the viscosity of liquid. Deaerators enable micro-foams merge with one another to increase their size which makes the foams rise more quickly to surface. Deaerators destabilize the surface-active agents around the bubbles and allow the air diffuse into liquid. Thus, microfoams are converted into larger bubbles that can be rise to surface rapidly (Figure 2).
[caption id="attachment_136868" align="aligncenter" width="561"]
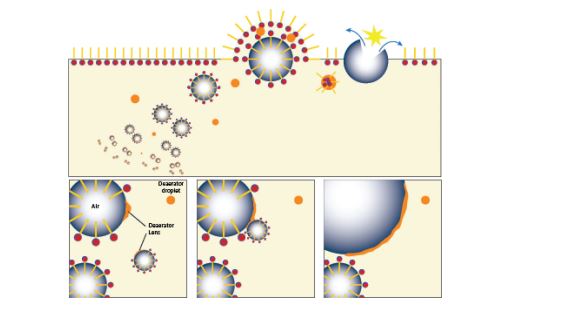
Figure 2. Deaeration mechanism[/caption]
Designing of a high-performance deaerator depends on versatile parameters and process. It is required to make a reliable study considering various properties of the deaerator such as compatibility of deaerator with the system, deaeration efficiency, cost and clear coat
applications without haziness. Six Sigma**** methodology enables to understand the outputs of the hundreds of experimental data by applying much less experiments and provide efficient time management. Design of Experiments (DOE) is a Six Sigma tool that
helps project teams determine the effects that all the inputs of a process have on the final product. Denge Kimya embrace Six Sigma methodology in all the projects that the company involved in. By this approach, a new project has been started in Denge Kimya to produce effective deaerators for clear coatings.
Production period have been started using DOE setup by Six Sigma approach (Table 1) to reach the best performance deaerators for clear coatings.
Generally, high viscosity may occur in 2K clear coating systems. Air bubbles (micro-foams) that dragged into the system by mechanical stirring fight against the viscosity of the system to reach to surface. High viscosity extremely slows down the speed of formed
micro-foams in the system. Because of the fast-curing nature of these systems, micro-foams cannot find enough time to reach the surface and trapped in the system. This problem can be solved by efficient deaerators. Deaerators provide the fast rise of micro-foams within the system and burst on the surface before curing. Another expected feature from a deaerator is the ability of no haze in clear coating system as well as quick deaeration.
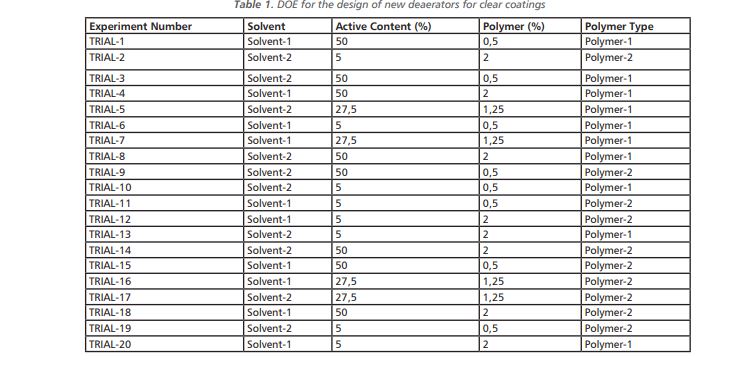
The products prepared using DOE in Table 1 have been tested according to the following methods: First of all, 0.5% amount of deaerator is added into high viscosity (11000-14000 mPas) solvent-free epoxy resin composed of A and B components. All the samples are mixed equal time after the addition of deaerators by applying the equal stirring speed. Prepared resins were applied as a 5 cm film without any cutting-power by pouring method. Visual control of foam quantity and turbidity are checked after 1 hour. Figure 3 demonstrates the visual analysis of the best product selected from the DOE study including the comparison of blank and benchmark dearator. In Figure 3, while the writing “Densurf” under the blank sample is not readable, the writing under the sample resin including deaerator coded as RD-Safe 80001-31 is clearly readable. Readability at benchmark product seems even better than blank, still it is not sufficient.
[caption id="attachment_136873" align="aligncenter" width="677"]
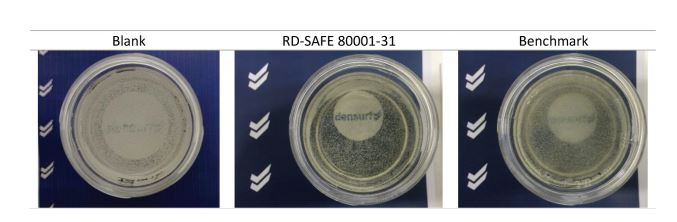
Figure 3. Top view of 5 cm coating films; blank, RD-Safe 80001-31, benchmark[/caption]
References
1. Béla Márton Somosvári, PhD Thesis, Foam evolution and stability at various gravity conditions, University of Miskolc, Faculty of Materials Science Department of Polymer Engineering, Miskolc, 2012.
2. Garrett, P.R. (Ed.). (1992). Defoaming: Theory and ndustrial Applications (1st ed.). CRC Press. https://doi.org/10.1201/9781315140827.
3. Web: http://www.kansaialtan.com/icerik/pinhol-ve-gaz-hapsi_274
Footnote:
* Pinholes are small blisters whose surface has broken during the drying process. Pinholes are often caused by trapped air, trapped solvents and trapped moisture escaping from the film.
** Micro-Foam, is a trapped air inside the liquid, generally having a spherical shape. It is also known as wet foam.Macro Foam, is a polyhedral air bubbles, generally formed on the surface of liquid. It is also known as dry foam.
*** ν=r^2/η (Stoke’s Law)
ν:Rising speed of foam
r:Radius of foam
η:Liquid viscosity
**** Six Sigma is a disciplined, data-driven approach and methodology for eliminating defects (driving toward six standard deviations between the mean and the nearest specification limit) in any process –from manufacturing to transactional and from product to service.
Aylin Aydemir
Senior Application Specialist
Densurf
Dr. İlker Yatı
Senior R&D Specialist
Denge Kimya