Cellulose Ethers Used in the Building Industry and Test Methods
Cellulose is an environmentally friendly natural polymer that originates from trees and plants and is generally obtained from wood, cotton or fibrous plants. The trees and plants from which cellulose and its derivatives are obtained are decreasing day by day in the world.
In order to prevent this situation, studies on obtaining cellulose from cotton waste and renewable plants have recently been among the priorities of scientists. (1)
[caption id="attachment_142803" align="aligncenter" width="402"]
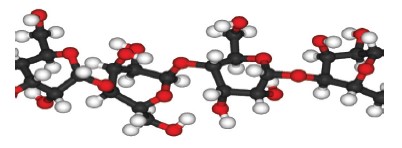
Figure 1: Three-dimensional image of cellulose (2)[/caption]
Cellulose, which finds different applications such as cleaning materials, pharmaceuticals, and cosmetics, is synthesized in different forms such as methyl cellulose (MC), hydroxyethylcellulose (HEC), hydroxyethylmethylcellulose (HEMC), hydroxypropylmethylcellulose (HPMC) through the etherification process, and plays a very important role in the construction and paint industry.
[caption id="attachment_142804" align="aligncenter" width="368"]
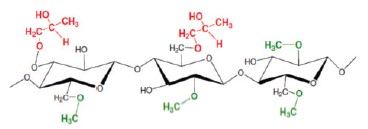
Figure 2: HPMC[/caption]
[caption id="attachment_142805" align="aligncenter" width="373"]
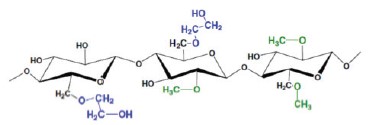
Figure 3: HEMC[/caption]
Cellulose ethers used in the paint and coating industry are used to improve stability and solubility of paints. It is also used in the construction industry to increase binding, water retention and working time.
In addition, it is one of the effective inputs in ceramics with its binder in textiles, thickening and water retention in adhesives. Shrinkage and spreading parameters are evaluated in order to determine the suitable cellulose ether for the system as well as the other parameters such as viscosity, moisture content, ash content, open time.
In this article, some of materials were examined, based on the products of MIZUDA, which is one of the global cellulose derivative manufacturers and represented in Turkey by the Reaksiyon Kimya. Thanks to Reaksiyon Kimya R&D laboratory to support this study.
Viscosity Value
It is measured with a viscometer measuring according to the Brookfield method at 20°C and by preparing a 2% solution of the product. The value is determined in mPa.s, which is obtained as a result of the measurement according to the ASTM D2364 (3) standard.
Viscosity is one of the most important parameters that determine the usage areas and quality of cellulose product groups. Cellulose ethers retain the mixing water with increasing viscosity and prevent the substrate from absorbing the mixing water, as they impart water retention to the mortar.
In the absence of water loss, hydration continues
and the mortar does not lose its strength. (4)
Moisture Value
The amount of moisture in the cellulose ether content to be tested is measured by placing 1 g in a moisture analyzer set at 105 degrees, according to the ASTM D2364-15 (2021) (3) standard.
%Moisture=100-value in moisture analyze,
% Moisture is determined by this equation.
The increase in moisture causes a decrease in the water holding property of the cellulose ether in the system.
Ash Value
The amount of ash in the cellulose ether content to be tested is measured in accordance with ASTM D3516-89(2019)e1 (3) by burning in an oven at high temperatures.
M2: Final weighing
M1: tare
% Ash Value = ((M2-M1) / sample quantity)* 100
% Ash is determined by this equation.
High ash content reduces the performance of cellulose ether in the system.
Spread Test
According to TS EN 13395-1 standard (4); the spreading table is placed on a flat and stable surface. The contact blocks, plate and mold are cleaned and wiped with a damp cloth just before the experiment, leaving no free water.
The mold is placed in the center of the top plate and fixed in its position by pressing the foot parts in order to prevent the material from escaping from the base during the filling process.
Fresh concrete is filled into the mold in two equal layers by using a ladle, and each layer is compacted by ramming lightly 10 times with a compression rod during filling. Excess concrete overflowing from the upper level of the mold is stripped and the free part of the table along the base edges of the conical mold is wiped clean.
30 seconds after the upper surface is stripped, the mold is lifted vertically within 3-6 seconds by holding the hand grips. By pressing the end plate on the front of the table, the spreading table is fixed and the top plate is slowly lifted up to the stop.
The plate is dropped freely on the lower stops and this process is repeated for a total of 15 drops. Each lifting and lowering operation must be completed within 2-5 seconds. After the lowering operations are completed, the largest dimensions of the concrete layer spread over the top plate are measured as d1 and d2 with caliper in two directions parallel to the plate edges.
The measurement results taken in two directions are recorded by rounding to the nearest 1 mm and the average of the two test results made in the same time is taken.
[caption id="attachment_142806" align="alignleft" width="300"]
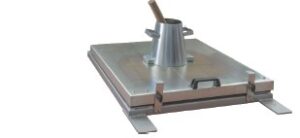
Figure 4: Spreading table, conical mold and knob[/caption]
[caption id="attachment_142807" align="alignnone" width="181"]
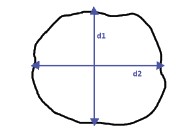
Figure 5: Measurement of spread size[/caption]
Consistency value is calculated according to this average value. If the deviation of the value obtained from the two samples from the mean spread value is more than 10%, two more samples should be taken and the test repeated.
Slip Test
After mixing the powder products (Sand + Cement + Cellulose ether), water is added and mixed for 1 minute at 280 prm in the concrete mixer. A flat tape is attached to the top of the EN 1323 standard concrete stone to ensure that the measurement of the sliding distance is clear.
The stone is wetted with a damp cloth and the mortar mixed homogeneously in the mixer is poured on the stone and the tape is pulled slowly. The tile stone is slowly left on the level that is ensured to be flat and 2 kg of weight is kept on this tile for 30 seconds.
The space remaining in the upper part (the part without mortar) is measured with the help of a caliper and recorded as the first measurement.
The standard stone is lifted slowly and kept in an upright position for 15 minutes, and at the end of the 15th minute, it is tilted and the part from the beginning of the concrete stone to the tile stone is measured again with a caliper, this value is recorded as the second measurement.
[caption id="attachment_142808" align="aligncenter" width="568"]
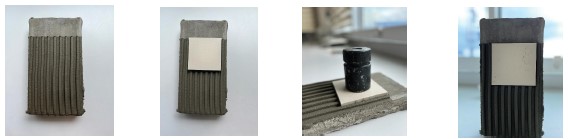
Figure 6: Tested with cellulose ether MH-EM50LX.[/caption]
The slip distance is concluded as the difference between the last measurement and the first measurement. Here, the sliding distance of the tile stone over the vertical mortar was measured as 0.17 mm. Absence / minimum sliding distance is the reason for preference for the manufacturer and the applicator. Therefore, high slip resistance is expected.
Open Time Test
After mixing the powder products (Sand + Cement + Cellulose ether), water is added and mixed for 1 minute at 280 prm in the concrete mixer. EN 1323 Standard concrete stone is wetted with a damp cloth, the mixture taken from the mixer is poured on this stone and the drawing is taken with a trowel.
The mortar drawn on the stone is left for 20 minutes. In the 20th minute, 1 ceramic tile is placed on the mortar slowly and 1 kg of weight is left on it. The weight is held on the tile for 30 seconds. 6 ceramic tiles are adhered to the mortar with the same method at intervals of 5 minutes.
After the 6th ceramic tile is adhered in the 45th minute, the first adhered tile is slowly removed with a spatula. Again, all ceramics are removed at intervals of 5 minutes. The surface views are examined and the open time test is concluded in line with these observations.
As of the pouring time of the mortar, the last tile was removed at the 65th minute. The open time, long scaling time allows the applicator to work easily and this time is a very important parameter in the selection of cellulose ether.
[caption id="attachment_142809" align="aligncenter" width="302"]
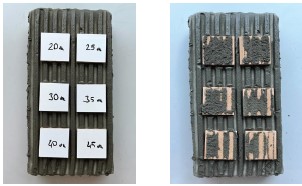
Figure 7: Tested with cellulose ether MH-EM50LX.[/caption]
[caption id="attachment_142810" align="aligncenter" width="449"]
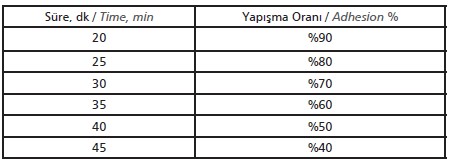
Table 1: Open time measurement results
for MH-EM50LX[/caption]
Cellulose ethers, which are used in the production of many products such as ceramic adhesives, plasters, repair mortars, leveling screeds and paints, are easily dispersed in the system due to their small particle sizes, while increasing the viscosity of the mortar and
preventing the material from slipping / flowing from the applied surface.
With its water-holding feature, when the powder mixture is turned into a mortar, it delays the drying of the product and prolongs its usage time. At the same time, with this feature, they help the mortar to spread more easily and adhere better to the surface on which it is applied.
When all studies are evaluated, it is observed that Reaksiyon Kimya-Mizuda cellulose group standard cellulose ethers support the preparation of products with added value for many
different application areas in the construction sector.
MH series cellulose groups offer valuable solution opportunities to meet the expectations of the industry with its pure and modified product variety. You can view the technical information of MIZUDA brand HPMC and HEMC products at our website and contact our sales executives.
References:
1. http://jes.ksu.edu.tr/tr/download/article-file/267726,
2. https://tr.wikipedia.org/wiki/Sel%C3%BCloz,
3. https://www.astm.org/catalogsearch/result/?q=cellulose,
4.https://www.cimsa.com.tr/ca/docs/71DDECEE521E470BA4ADA95A091840/75DBD3617E9D4378B8A17A2A4AE6AB5F.pdf
Sevtap Karasu
Sales Executive
Reaksiyon Kimya