Benefits of Using a Rupture Disc in Chemical Processes
Protect your Investment and your Personnel: the Benefits of Using a Rupture Disk with a Pressure Relief Valve
Excessive pressure in production processes can be the result of a wide variety of causes, from leak reactions and malfunctioning regulators to operator errors and faulty equipment. Excessive pressure can have serious consequences, not only damaging equipment and systems, but potentially leading to personal injury or even loss of life.
For this reason, pressure relief valves are widely seen as the primary safety solution. However, these valves themselves need protection in order to maintain the
desired level of safety in an issue that can sometimes be overlooked.
Most pressure relief valves are spring loaded and set to open at a certain pressure. When the pressure rises to an unacceptable level, the spring is pushed open and the pressure is released. When the pressure level returns to normal, the spring forcibly closes the valve and the process starts again.
So what do pressure relief valves need protection from? From the product itself. Valves are used in almost every industry, so there is a wide variety of processed products to which they may be exposed. Corrosion and wear and tear is always a risk as we are
dealing with mechanical moving parts, even where the environment looks relatively good. The risks are much higher with more abrasive, sticky or viscous products.
Threats to the operation of Pressure Relief Valves (PRVs) include:
• Product build-up,
• Corrosion,
• Leakage.
Build Up
Accumulation of product means the risk of clogging or lowering of the orifice. Complete congestion is not the only danger. In many cases, the pressure rise is very rapid, so the pressure relief needs to be at a very high flow rate and a high velocity with high volume. In this scenario, even a small reduction in the freeflowing orifice means that the valve will not be able to relieve pressure efficiently enough, causing damage to the processing
equipment.
Corrosion
Corrosion affecting the PRV needs to be considered with certain products, particularly where non-standard construction materials may be required for the pressure relief valve. Corrosion can cause the valve to leak at an increased rate or cause it to fail to
lift when needed, so it cannot relieve pressure as desired.
Leakage
When it comes to leakage, there are two separate problems. First, the leaked small amount of processed product leads to an unexpected accumulation of product on
the output side, creating the same risks identified for the accumulation on the input side. Secondly, there are environmental concerns depending on the processed product.
Emissions regulations are getting stricter around the world, so leakage can have serious consequences for both the environment and the business if it doesn’t comply with the required limits. An established solution to reduce risks to PRVs is to place a solid metal rupture disk upstream of the PRV to protect it against all of these potential threats. Rupture disks are industry-proven, nonmechanical devices which require
lower investment and maintenance in comparison to PRVs.
What are the advantages to pairing a rupture disk with a pressure relief valve?
• Leak Prevention,
• Corrosion Protection,
• Cost Savings,
• Testing Can be Done in Place,
• Elimination of Fugitive Emissions.
Leak Prevention
Isolating a pressure relief valve with a rupture disk has a major advantage; it prevents the process from leaking into the environment. A typical safety relief valve
will begin to leak as it approaches the set pressure. A rupture disk serves as a solid metal barrier between the process and the PRV.
Leakage is becoming globally more unacceptable due to international environmental restrictions or simply to avoid the loss of expensive product out of the system. Even if the process does not contain any toxic or expensive elements, safety equipment should be able to operate leak-free over long periods. The addition of a rupture disk to the valve will accomplish this.
[caption id="attachment_133220" align="aligncenter" width="569"]
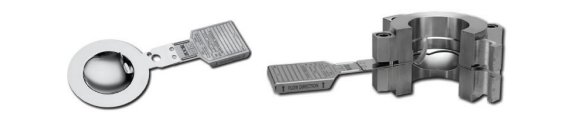
RA type rupture disc (left) and metal-to-metal seal holder (right)[/caption]
Corrosion Protection
If the pressure relief valve’s sealing surface is exposed to a corrosive process, it can be damaged over time, resulting in the need to replace an expensive valve, lined with material such as Hastelloy® or Tantalum. Corrosion can erode alloys and result in the valve leaking or it can fail to open when required to relieve pressure. By contrast, there are metal rupture disks that are virtually leak-free and, when used upstream, are
a simple and effective way to isolate the PRV.
If used downstream from a valve, a disk will prevent corrosive vapors from contacting valve internals. It will also prevent backpressure from affecting the valve’s set pressure. Some rupture disks can be equipped with burst indication that will signal if the PRV opens or leaks.
Cost Saving
The PRV with its higher initial investment, is reusable and must be maintained while the lower-cost rupture disk is disposable. Pairing a rupture disk with a PRV allows for less expensive materials to be used for the valve internals, since the need for corrosion protection is reduced.
This combination actually saves a substantial amount of money due to:
• Reduced maintenance costs including calibration,
• Less downtime for testing or overhaul,
• Longer life-span for the PRV itself,
• Reduction in capital cost of the PRV due to standard materials used for the trim parts.
All while ensuring the reliability of the safety system. PRVs and rupture disks can be complementary to each other, each offering their own advantages and limitations. The combination of the two, either in parallel or series, can be the best solution for comprehensive protection of the facility. The combination of disks with PRVs is recognized by ASME Boiler & Pressure Vessel Code API520, ands EN ISO 4126-3 in Europe and Internationally and used in a variety of industries, including oil & gas, chemical and petrochemical plants.
[caption id="attachment_133221" align="aligncenter" width="465"]
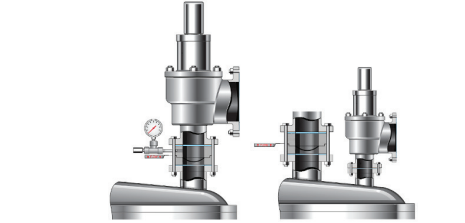
Rupture discs and relief valves can be used in parallel (left) and in series (right).[/caption]
Testin in Place
In any facility, downtime for inspection and maintenance can be expensive, as are replacement parts for PRVs. All have an impact on workflow and the profitability of a company. Regulations require that testing and monitoring be done to ensure safe operation of the system, but time-consuming overhauls and expensive replacement parts can be avoided with the added protection of a metal disk. Some companies still require removal of a PRV, if used alone, for off-site testing and service, but when protected by a rupture disk, PRVs can be tested in place.
In particular, with the use of a reverse-buckling disk installed at the inlet, the PRV
can be tested using a portable pressure source. Air, or an inert gas such as nitrogen, can be injected into the space between the disk and the PRV to initiate the set pressure of the PRV to ensure the settings are correct with minimal plant downtime.
Fugitive Emissions
Fugitive emissions are emissions of gases or vapors from pressurized equipment due to leaks and other unintended releases of gases, mostly from industrial activities. As well as the economic cost of lost commodities, fugitive emissions contribute to air pollution
and climate change. Many countries have strict regulations regarding the monitoring and reduction of these gas emissions. Fugitive emissions present other risks
and hazards.
Emissions of volatile organic compounds such as benzene from oil refineries and chemical plants pose a long-term health risk to workers and local communities. In situations where large amounts of flammable liquids and gases are contained under pressure, leaks also increase the risk of fire and explosion.
API standard 526 allows for a maximum leak rate of 40 bubbles per minutes, or 6 cubic feet per 24 hours. Fugitive emissions are reduced or eliminated with the addition of a rupture disk to a PRV. Zero emissions during normal operation means no collection and disposal costs, and significantly reducing possible fugitive emission fines.
Conclusion
The use of rupture discs at the inlet of pressure relief valves will improve the chosen level of pressure safety and reduce the need for cleaning, maintenance and repair. Corrosion problems and downtime costs on both the inlet and outlet side of the pressure relief valve can be significantly reduced with better efficiency from the production site.
Finally, by adding rupture discs to the inlet of the pressure relief valve, higher process safety is achieved in a low cost of ownership plant.
Hayri Mutluoğlu
Electrical-Electronical Engineer
Sales Manager
Elva Engineering