Antifoam
We frequently see bubbles in our daily life, in industry, and even in nature. Have you ever thought about what bubbles are, why they form, and how they disappear? Have you ever thought about what bubbles are, why they form, and how they disappear?
The foaming mechanism consists of a mass of bubbles that are well dispersed in a gaseous liquid. These gas bubbles, formed by the combination of surfactant, water, and air, appear as cleaning agents in our homes. Liquid detergents, laundry detergents, and shampoos that we use for home care with this mechanism.
The more foam we see when using these products, the better we are convinced that we clean. However, not every bubble that occurs makes us this happy. The presence and uncontrollability of foam in industrial processes bring serious problems.
If the foam formed cannot be controlled appropriately; It can increase processing time, affect the stability of chemicals, reduce pump efficiency, not standardize finished product performance, reduce equipment capacity, and prolong the filling process.
Each problem directly affects the costs of businesses. The foams observed in the enterprises are generally; It is formed during blending and mixing processes, circulating systems, distillation, straining, filling, and transportation.
How Is Foam Formed?
A suitable scientific theory has not yet emerged to explain why some solutions foam very strongly, some moderately, and many do not foam at all. Today, the most important problem of the foaming theory is that the physicochemical factors in different systems cannot be fully explained.
However, two theories have been accepted, partially related to foam formation. The first acceptance on this subject is pure liquids do not foam. The second acceptance is that there is a connection between the foaming solution and the surface activity of the solute.
The literature has made classifications to better explain the foam systems formed.
Non-foaming Systems: Pure liquids do not form foam. In addition, solutions with similar
chemical structures and surface tension and solutions of hydrophilic substances are defined
in the class of non-foaming systems.
Temporary Foaming Systems: It is obtained by solutions of substances that moderately reduce surface activity. Temporary foams are best characterized by dilute solutions of short-chain aliphatic alcohols and acids. Foam life varies depending on solution concentration.
Systems with Permanent Foam: Only when diluted, substances that reduce the
surface tension force (materials with high surface activity) form permanent foam. The cleaning soaps and detergents we use in our homes are examples of these structures.
Foam Cutting Mechanism
The most important effect of antifoams should be to decrease surface elasticity. Antifoams must exhibit constant surface tension in response to stress. To do this, it must eliminate the effects of foaming agents on the surface.
Therefore, it should have a very low surface tension coefficient alone and spread over the
film. In general, silicone compounds with an extremely low surface tension value of 20 dyn/cm are more effective than other types of antifoams because they do not dissolve in water.
They are used as antifoam, emulsion, or solution. It is known that even amounts between
1-60 ppm are extremely effective in cutting foam. In a foam cutting mechanism, there are physicochemical properties that must be considered and directly affect the cutting
performance.
These are;
Solubility: Many antifoams have low solubility in aqueous systems. To increase the effectiveness of the foam-cutting process, the amount of active substance should be dissolved in the solution in the best way.
Droplet Particle Size: The force that allows the antifoam drop to pass through the bubble wall increases as the antifoam particle size decreases. Presence of Hydrophobic Solids: Liquid/solid mixtures generally show more effective results than structures used alone.
The hydrophobic solid particles contained in the antifoam can easily break the resistance
by increasing the efficiency.
Shear Strength: This property is principally dependent on the separation of soli
Repetitive Foaming Effect: Generally, a repetitive foaming effect is observed in continuous processes. By fixing the hydrophobic particle size, the continuity of the foam-cutting effect can be ensured.
The continuity of this foam-cutting effect can be measured with more than one agitation method.
Surfactant Concentration: A antifoam system having a high concentration of surfactant weakens the foaming effect and can create a foaming effect by providing interfacial formation.
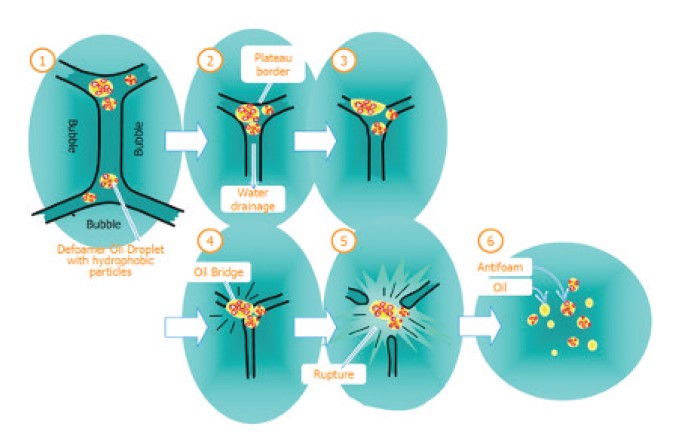
Dissolved Salt Particles: The presence of high amounts of metal ions in the environment is a feature that reduces the efficiency of the antifoam. Opposite ions surround the polar ends in the surfactant molecule and weaken the electrostatic interaction of the surfactant molecules.
What Affects Foam Cutting Performance?
There are areas where antifoams are used and environmental conditions are constantly changing. Antifoam products must be chemically incompatible with the foam formed. The higher the performance of a antifoam means that the lower its compatibility with the system.
The more compatible a antifoam is, the lower its performance will be. The characteristics of the application environment must be considered to determine the appropriate antifoam. For this reason, there is a wide variety of antifoams.There are many different functional structures and active amounts of antifoams.
The reason for this varies depending on the physicochemical conditions, environment
characterization, and usage method. With the work and technical know-how of our R&D Center, we need to answer some questions to determine the antifoam that will work best in your system.
• What is the pH in the working environment?
• Will heat be used during application?
• What is the determined solution concentration?
• Are there mechanical speeds and revolutions in operating conditions?
• What is the ionic character of the environment?
• What is the viscosity of the system?
• Are there volatile compounds in the system?
• What is the class of foam formed in the system?
What Is Expected Performance from Foam Cutters?
This is exactly the question that makes us think the most and even causes us to minimize our expectations. “How much performance should I expect from a foam cutter?” The product groups offered by our R&D Center have been developed to provide solutions to different problems.
Therefore, your expectation is our solution. In general, the performance criteria expected
from the foam cutter;
Fast Instant Foam Cutting Capability: It is added to the foaming system and classified as instant foam cutting performance. This performance is called the “knockdown” effect.
Long-term Durability: It is the situation in which foam formation is prevented despite all kinds of mixing and rotation speeds for a long time after the addition of antifoam material to the foaming system.
High Activity: They are antifoams that show high performance despite low dosing.
Low Viscosity: A physical property often expected in applications involving dosing and pumping systems.
Temperature: Antifoams operating at high and low temperatures are often preferred. Especially in continuous systems in operation, although long-term cycles start at 25oC, but over time, it gets hot with the increase in temperature. Antifoams that operate in a wide temperature range are highly preferred for these systems.
pH: Considering that the alkaline amount of the water used in the business is constantly changing, the antifoams that can operate in a wide pH range are not affected by possible pH changes that affect the system and do not adversely affect the processes.
High Salt Concentration: Depending on the operation and application differences, not all antifoams will perform well in salty environments. Therefore, antifoam selection should be made depending on the salt concentration of the environment.
Solubility: It directly affects both your shelf life and stability by using antifoams that provide ease of dissolution even in different ionic characters.
Good Breathability: Antifoams that perform air evacuation have high foam-cutting power.
Eda Kamertay Kurttay
Knowledge Spreader & Aggregator
Latro Kimya