Alt Katmana Özgü Yüzey Ön İşlemi
Alüminyum ve Al-alaşımları
Alüminyum ve alüminyum alaşımlarının yüzey ön işlemi; temizleme, yağ giderme, aşındırma ve muhtemelen dönüşüm katmanı oluşturmayı içermektedir.
Alüminyum dökümler aşındırılmaz, ancak kumlanır. Yağ giderme ve aşındırma sistemleri ve prosesleri prensip olarak demirli malzemelerin ön işlemlerine benzemektedir.
Alüminyum ürünlerin şimdiye kadar en büyük oranı anodize edilecek olanlardır. Bunların, özellikle yarı işlenmiş alüminyum ürünlerin ön işlemleri DIN 17611’de belirtilmiş olup, özeti
1. Tablo’da verilmiştir.
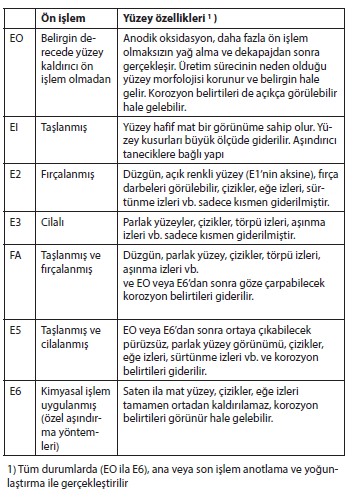
Alüminyum yüzeyleri yağlardan temizlemek için organik çözücüler, sulu, emülsifiye veya zayıf alkali yağ giderme çözeltileri ve düşük fosfatlama etkisine sahip asit yağ gidericiler
(%1 ila 10 ortofosforik asit, teknik olarak %85) kullanılabilir. Alkali maddelerle yağdan arındırırken, sonrasında bol su ile durulanmalıdır.
Aşındırmak
Genellikle alkalin, bazen ise asidik olarak aşındırılır. Alkalik aşındırma işlemleri için, aşındırma maddesi olarak %10 ila 30 oranında sodyum hidroksit veya potasyum hidroksit
kullanılır. Aşındırma süresi 1 ila 3 dakikadır. Aşındırma işleminden sonra su ile iyice durulanır ve %20 nitrik asit ile nötralize edilir.
Asitle aşındırma için sülfürik asit ve/veya hidroflorik asit kullanılır. Hidroflorik asit ile aşındırma yaparken özel koruyucu önlemler gereklidir.
Dönüşüm Katmanlarının Oluşturulması
Dönüşüm kaplamaları, organik katmanların doğal olarak pürüzsüz ve yoğun alüminyum yüzeye yapışmasını iyileştirmek amacıyla uygulanır. Genellikle organik kaplama sürecine entegre edilen oksit, anodize ve fosfat katmanlar özellikle önemlidir. Süreç, dönüşüm katmanlarının üretimi ile aynıdır.
Bakır
Üst katman, oksitlenmiş veya kararmış bakır yüzeylerden, aşındırıcı keçe silindirlerle işleme, pomza/su karışımıyla kumlama veya seyreltilmiş H2S04’te kireç çözme yoluyla önceden yağ giderme işleminden sonra çıkarılır. Na2S207’de ilave aşındırma işlemi de mümkündür.
Cilalar pürüzsüz bakır yüzeylere yeterince yapışmaz. Ön işlem, organik çözücülerle yağ giderme ve yüzeyin mekanik ön işlemden geçirilmesini içerir. Baskılı devre kartı teknolojisi gibi özel durumlarda, fotorezistlerin yapışma mukavemeti, örneğin ponza tozu püskürtülerek önemli ölçüde artırılabilir.
Çinko
Özellikle sonraki organik katman için, sprey galvanizleme ve çinko döküm herhangi bir özel yüzey ön işlemi gerektirmez; çinko sac, sıcak daldırma galvanizli bileşenler ve elektro galvanizleme, yüzeyin yağdan arındırılması ve fosfatlanmasından oluşan bir ön işlem gerektirir.
En fazla 30 dakikalık bir işlem süresinden sonra, soğuk ve ılık su ile durulanır ve ardından kurutulur. Çinko karbonat katmanıyla kaplı eski yüzeyler mekanik işlemlerle toz ve kirden
temizlenir.
Plastik
Plastiklerin ön işleminin genellikle iki amacı vardır. İlk olarak, yukarıda açıklanan süreçler kullanılarak uygun ıslanabilirlik elde etmek için yağdan arındırma ve ikinci olarak, mekanik adezyon noktaları oluşturmak için yüzeyin pürüzlendirilmesi.
Tipik bir örnek, ABS plastiklerin ve polipropilenin harici akım olmadan metalizasyon için
ön işlemden geçirilmesidir (bkz. Şekil 1), burada kimyasal işlem gerçekleşir.
Kimyasal yollarla zarar verilmesi zor olan plastikler için plazma temizlik ve aktivasyon için yine uygundur. Teflon filmlerin (PTFE) erimiş sodyum ile ön işleme tabi tutulması uç bir durumdur. Bu şekilde işlenen folyolar yapıştırılabilir ve özel bileşenler için aktivasyon
yoluyla harici akım olmadan metalize edilebilir.
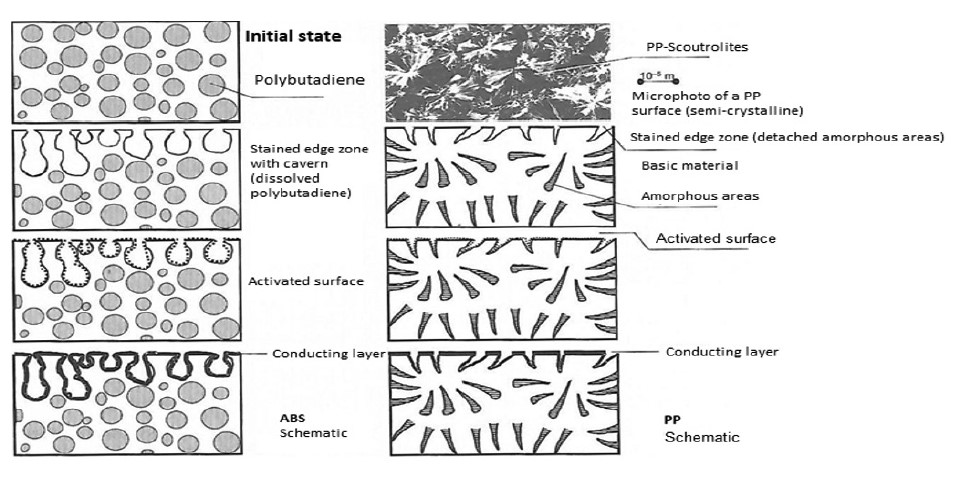
Yıkama
Sulu bir ortamda gerçekleştirilen yüzey teknolojisinin neredeyse tüm aktif işlem adımlarında durulama işlemi takip etmektedir. Bu gerçek genellikle süreç tanımlarında özellikle vurgulanmaz. Durulamanın amacı:
• Tanımlanan aktif süreci durdurmak,
• Elektrolitlerin taşınmasını en aza indirmek ve böylece banyo içeriğinden tasarruf etmek,
• Yüzeyin olası bir sonraki kimyasal reaksiyonunu önlemek,
• İçeriklerin ve suyun geri kazanılmasını sağlamaktır.
Durulama için deiyonize su (tanımlanmış saflık, su sertliği) kullanılırsa ve uygun ekipman ve teknolojiler kullanılırsa, durulama kriteri R’ye uygunluk, gerekli kaplama kalitesiyle sonuçlanır. Aynı zamanda, çevre koruma ve iş açısından su ve atık su tasarrufu talebi karşılanabilir.
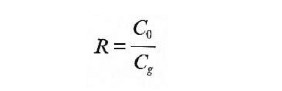
Burada Co, elektrolit veya arıtma solüsyonundaki tuzların konsantrasyonudur ve C, durulama suyundaki denge konsantrasyonudur. Altlık yüzeyinden çalkalama suyuna
geçen iyonlar ile yüzeye dönen iyonlar arasında denge sağlanır.
Bu durum akmayan yıkama suyu için geçerlidir. Bu, ayaklı bir lavabonun durumuna karşılık gelir. Yıkama kriteri R’nin tersi, yıkamada elde edilecek seyreltme X derecesini gösterir.
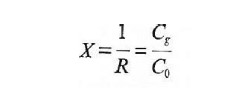
Durulama kriteri R’ye uygunluk ve bunun sonucunda mallar üzerindeki durulama suyu kalıntılarında izin verilen tuz konsantrasyonunun sınır değeri, temiz su miktarını belirler. 1/dk cinsinden katılmış elektrolit miktarı D ile, 1/dk cinsinden gerekli tatlı su W miktarı için aşağıdakiler geçerlidir: W = D . R
Kelimelerle ifade edecek olursak: bir durulama adımını gerçekleştirmek için gereken tatlı su miktarı, durulama kriteri R’den ve durulama suyuna taşınan elektrolit veya solüsyon D miktarından etkilenir. Su gereksinimi, sürüklenen elektrolit konsantrasyonu ve birim zamanda yıkanan alan ile artar.
Uygulama solüsyonlarının kalıntıları tüm yüzeylere yapışır. Çok sayıda araştırma sonucu mevcuttur. Genel olarak şunlar söylenebilir:
• Yüksek konsantrasyonlu elektrolitler (örn. nikel), düz, dikey yüzeyler için yaklaşık 40 ila 70 ml/m2 olan yüksek sürükleme kayıplarına neden olur.
• 6 ila 10 saniyelik minimum damlama süreleri ile sürükleme kayıpları minimuma doğru yönelir.
• Islatma maddeleri ekleyerek, sürüklenme kayıplarını yaklaşık %20 ila 30 oranında en aza indirmek mümkündür.
Uygulamada, durulama sırasında tatlı su ihtiyacını belirlemek için R için ampirik değerler kullanılır. Tablo 2, yıkama kriteri için değerleri içerir.
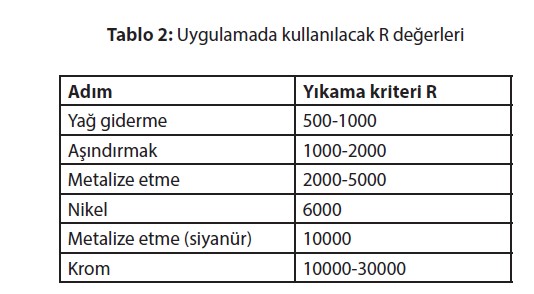
Optik, elektronik, vakum teknolojisi ve Si teknolojisi alanlarında sofistike uç yüzeyler elde etmek için 100.000 ve daha fazla durulama kriteri gereklidir. Gereksinimlere ve koşullara bağlı olarak, durulama tamamen tuzdan arındırılmış su, içme suyu veya sirkülasyon veya proses suyu ile gerçekleştirilebilir.
Teknik açıdan daldırmalı durulama, uygulanması en kolay olanıdır, bu sayede ürünler sabit hacimde durulama suyuna daldırılır. Verilen elektrolitin konsantrasyonu “ dip “ sayısı ile artar. Bu durulama tekniği ayakta durulama olarak bilinir.
Sürekli tatlı su akışıyla, ayakta durulamanın dezavantajları, daha yüksek su tüketimi, akış durulaması pahasına ortadan kaldırılabilir. Tek aşamalı durulama, kontrolsüz tatlı su temini ve malların yetersiz hareketi su ihtiyacını artırır ve durulama sonucunu kötüleştirir.
Yıkama tekniklerini birbiriyle birleştirmek ve böylece avantajları kullanmak ve dezavantajları mümkün olduğunca küçük tutmak mantıklıdır.
Bu, örneğin aşağı akışlı bir durulama banyosuna sahip çoklu bir durulama kaskadı ile elde edilir. Kademeli durulamada, bir dizi durulama tankındaki su bir öncekinden diğerine yönlendirilir.
Durulama suyu ve durulanacak iş parçaları karşı akımda hareket eder, iş parçaları
en son tatlı suyun beslendiği kapta ve ilk olarak en yüksek elektrolit konsantrasyonuna sahip durulama kabında durulanır.
Tablo 3’teki sonuçlar durulama uygulaması için bu bulguları yansıtmaktadır.

Püskürterek durulama, baskılı devre kartları gibi düz ve pürüzsüz iş parçaları için özellikle uygundur. Durulama suyu, püskürtme memelerinden gelen basınç altında iş parçasının yüzeyine püskürtülür, bu da durulama suyunda yüksek bir elektrolit konsantrasyonu elde edilebileceği anlamına gelir.
Prensip olarak, bir sistem yalnızca tek bir sprey durulama istasyonu gerektirir, ancak bu durulama suyunun ayrı olarak yönlendirilmesine izin vermez. Buna ek olarak, banyonun durulama suyuna taşınmasını azaltmak için sınırlı ölçüde basit önlemler mümkündür.
Bunlar:
• Elektrolit filmi boşaltarak, sıkarak, sıyırarak, üfleyerek, emerek çıkarma,
• Sıyırma ve sirkme,
• Drenaj uyumlu tasarım (küçük pürüzsüz yüzeyler; kepçeleme veya kılcal hareket olmadan),
• Düşük konsantrasyonlu kaplar,
• Artan yıkama sıcaklığı (daha düşük viskozite anlamına gelir),
• Düşük çıkış hızlarıdır.
Son kaplama adımından sonraki durulamayı, örneğin kararmayı veya lekelenmeyi önlemek için su tabakasını yüzeyden çok hızlı ve eşit bir şekilde temizlemek amacıyla kurutma takip eder. Son durulamaya genellikle bir ıslatma maddesi eklenir.
Kaynaklar
• Vorbehandlung als Herausforderung, Metalloberflaeche, RITUPER
• Reinigung in die Fertigung integrieren, Metalloberflaeche, LANDAU
• Prozesssicherheit in der Galvanotechnik, Metalloberflaeche, PENZ
• Wirtschaftliche und umweltgerechte Teilereinigung, Galvanotechnik, FALLOT
İzzet Aydın
Genel Müdür
Hillebrand Chemicals Kimyasal Pazarlama Ltd. Şti.