Adhesion of a coating to a substrate is the resistance of the coatings film to mechanical removal from that particular solid substrate in terms of force/area. In multicoat systems, the term intercoat adhesion refers to the resistance of an individual coating layer from the bottom coating layer.
A good adhesion and/or intercoat adhesion is a must for the overall performance of the coating system like:
• Flexibility,
• Physical, chemical&outdoor resistances,
• Corrosion, humidity and water resistances.
A Good Adhesion of a Coating Depends on:
I. Surface Preperaton:
A proper surface treatment process should be applied to the substrates before painting to increase adhesion and to add/improve some properties, one or combination of these surface preparation methods depending on the final quality expectations.
Traces of oil, silicone or wax based mold release agents together with other contaminations caused by hands of operators, dirt or dust and electrical charges on the substrate have very important impacts on the final performance and appearance including adhesion.
Basic Surface Preparation Processes: Metalls: Sand blasting, cleaning, degreasing, chemical treatments. Plastics: Degreasing, flaming, application of adhesion promoter layer. Wood: Cleaning, fumigation, sanding. Glass: cleaning, degreasing, cerium oxide abrasion.
II. Application and Curing Conditions:
Correct selection of application method (spray, roller, brush, dipping, curtain, etc.) for a particular usage is important.
Beside correct application method, correct application parameters like viscosity, correct thinner and hardener in correct mixing ratios, not to exceed pot life limits for 2K systems, obeying flash off times, conditions and curing cycles are very important not only for adhesion, but for overall performances as well.
III. Selection of Proper Coating System for Each Particular Application:
All kind of materials to be painted have different physical and chemical properties. Selection of the specific coating system for each particular substrate/material and also requirements for the end product should be carefully studied.
Selection of the proper coating systems for commonly used metal substrates like galvanized steel, aluminum, plastic substrates like polypropylene, polyethylene, PVC and glass are critical examples.
Also each product in the selected coating system should be compatible with each other. It will be useful to review some basic concepts in the coating terminology to understand the concept better:
1) Cohesion:
Molecular attractive forces of a material itself. Here, cohesion of a coating film is attractive forces of the molecules within the solid coating film itself. For adhesion, adhesion>cohesion and as difference increases without decreasing cohesion, adhesion increases.
2) Surface Tension:
For liquid and solid materials, molecules have a higher energy level at their interfaces than the molecules in bulk volume. In liquid-gas interface, molecules are forced to move to inner phase of the liquid bulk to minimize the surface area to a spherical droplet for maximum volume with this minimum surface area.
This means the molecules at the interface has higher potential energy at the interface. An energy should be spent to overcome this potential energy and move the molecules from the bulk to the surface and increase the surface area.
This force, work to increase per unit surface area is named surface tension in liquid-gas interface and directly measure of surface energy.
σ= Energy / area = force / length = dyn/cm or mN/m Higher surface tension means higher cohesion of that particular liquid.
3)Substrate Wetting:
Whatever the application method is; the first perquisite for a good adhesion is a good wetting of the substrate. Liquid Paint should penetrate into the cavities of the substrate and should wet as high as high surface area and cured coating film should be mechanically anchored into the substrate.
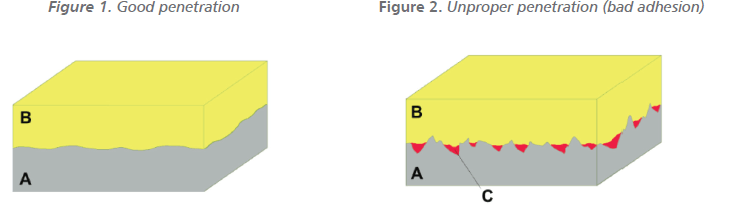
A: The substrate
B: Coating Film
C: Area not wetted by coating
Low application viscosity is better for good penetration and adhesion.
Another phenomena to have a good wetting is; having a surface tension of the substrate which is greater than that of paint.
To measure surface tension values of solid surfaces directly is not possible; but a drop of a liquid with known surface tension to a solid surface can be used to calculate the surface tension of the solid surface using contact angle principle.
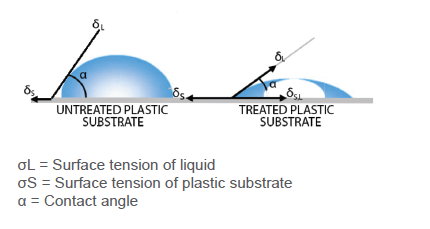
As contact angle α approaches to zero; it becomes σL = σS and wettability of the surface by the liquid increases; which means wettability of the liquid paint increases with decreasing surface tension of the liquid paint and/or increasing surface tension of the solid substrate.
In multicoat systems like automotive paints, surface tension of each layer should be lower than the bottom layer and this relation should successively continue until the final layer like a ladder.
Table 2. Shows the surface tension of some common
materials for the coatings industry
Adhesion Tests
Adhesion of a coating film to the substrate can be tested mainly by two methods:
1. Cross Cut Test (Cross Hatch Test): BS/EN ISO 2409, ASTM D 3359 3302
2. Pull Off Test: EN1542/12004-2, ASTM D4541/ D72342
TABLE.3: ADHESION PROPERTIES OF SOME KNOWN KROLAC RANGE ACRYLIC RESINS ON VARIOUS COMMON SUBSTRATES:
Muhammet Demirkıran - Sales Manager- Coating, Ink, Adhesives Raw Materials - Kempro Kimyasal Mad. ve Dış. Tic. A.Ş.
References
1.” Basics of Coating Technology” by Dr.Artur Goldschmidt & Dr.Hans-Joachim Streitberger
2.” Painting of Plastics” by Rose Ann Ryntz
3.” Pigments, Paints,Polymer Coatings and printing inks” by R.A.Ryntz
4. “Organic Coatings: Science and Technology”; by Zeno W. Wicks,2007