Acrylic resins are obtained as a result of the polymerization of acrylic monomers and their derivatives, such as acrylic and methacrylic acid, with or without functional groups, by addition reaction over reactive double bonds (C=C).
Monomer selection is an important parameter in acrylic resins.
Acrylic monomers are vinyl monomers containing acid or ester groups (Table 1).
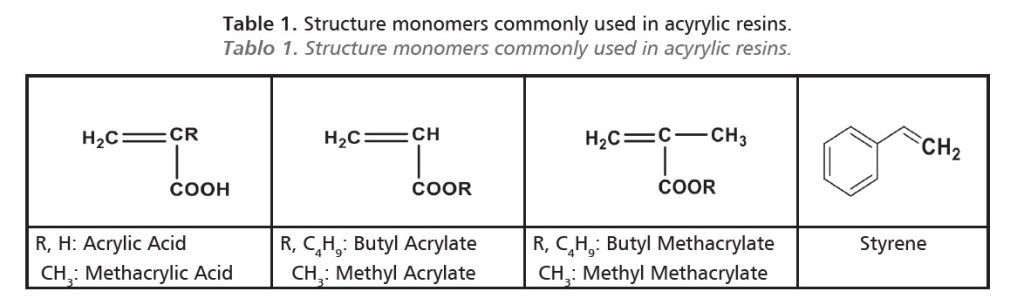
Many qualities can be added to the resins with various monomer combinations according to the purpose of use, and resins with the desired properties can be developed (Table 2). The properties of the copolymer produced using two or more monomers are more excellent than those of the homopolymer obtained using one monomer.
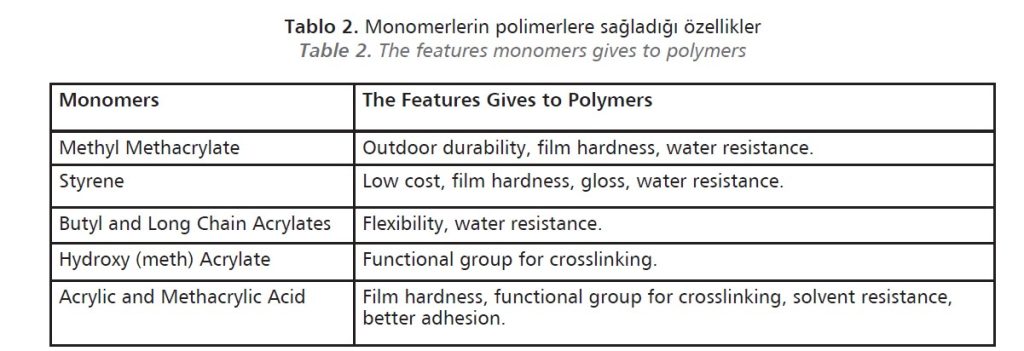
Another important parameter in acrylic resins is the glass transition temperature (Tg), that is, the temperature at which the chain movements begin. If a very hard monomer is copolymerized with a very soft second monomer, polymers with the desired flexibility and Tg can be produced, and the Tg values of the copolymers can be found experimentally.
There is a correlation between the Tg of the copolymers and the Tg of the homopolymers of the monomers, which gives an approximate result: 1/ Tgk= (A1/Tg1+A2/Tg2). The Tgk value is an approximate value of the copolymer. Tg1 and Tg2 are the glass transition temperatures of homopolymers. A1 and A2 show the value of both monomer weights in
terms of ratio. (A1+ A2=1).
Acrylic resins are generally produced by solution polymerization method. There are factors that affect the solution viscosity and the molecular weight of the polymer. These factors are:
Reaction Temperature: With the increase in temperature, the number of monomers bound to active radicals decreases. Thus, polymer chains are formed shorter and more, and polymers with low molecular
weight and viscosity are obtained.
Monomer Concentration: If the monomer concentration is low, low molecular weight and low viscosity polymers are obtained, if the monomer concentration is high, high molecular weight and high viscosity polymers are obtained.
Solvent: To obtain a regular polymer, the monomers must be dissolved in the appropriate solvent.
Chain transfer agents show different reactivity in different solvents and polymers with different molecular weights are formed. Solvents with the highest transfer coefficients form polymers with the lowest molecular weights.
Concentration of Initiator: The amount of initiator used varies between 0.2%-4%. When the concentration of the initiator decreases, the molecular weight of the polymer increases.
When the concentration of the initiator is increased, the molecular weight and viscosity of the polymer formed decrease. The radical formation times of peroxides, which form
free radicals when heated, change. Therefore, the decomposition temperatures and half-lives of peroxides must be taken into account. (Table 3).
1.1 Thermoplastic Acrylic Resins
They are high molecular weight (~30.000-130.000) film forming by evaporation of solvent, without intrinsic chemical reaction action, softening when heated, long-chain polymers that do not contain active functional groups.
They are obtained by solution polymerization of monomers that don’t contain functional
groups such as methyl (meth) acrylate, butyl (meth) acrylate, acrylic acid and styrene, using initiators that form free radicals.
Products produced with thermoplastic acrylic resin are one component(1K). Fast curing and air drying provide ease of application (Figure 1).
Advantages of acrylic paints and varnishes:
• Resistant to UV light. High resistance to external atmospheric conditions.
• Resistant to water, dirt and corrosion.
• Almost colorless or very light colored varnishes. Very clear appearance.
• High gloss level.
• Can be shaped easily after various heat treatments.
1.2. Thermosetting Acrylic Resins
Reactive property is given to the polymer by using monomer mixtures with functional groups (hydroxyl, carboxyl, epoxy, amine, amide) (Table 4). Thus, these functional groups react with polymers containing another reactive group to form long chain films with high amount of crosslinks.
They are two component (2K). The molecular weight of thermosetting acrylic resins varies between ~20,000 – 30,000.
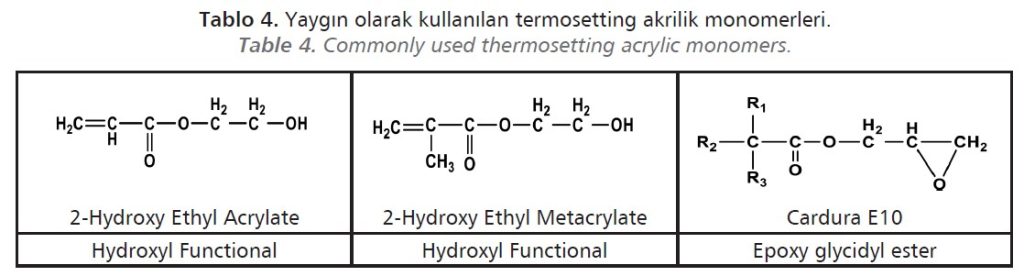
Polymers containing the hydroxyl group are cured with amino formaldehyde resins and isocyanates, Polymers containing the carboxyl group are cured with epoxy resins and polyvalent metal salts, Polymers containing the amine groups are cured with epoxy resins, isocyanate and amino formaldehyde resins, Polymers containing, amido and carbomate groups cured by cross-linking reactions with aldehydes.
Advantages of thermosetting acrylic paints and varnishes:
• Films formed by cross-chemical bonds are resistant to physical and chemical effects.
• Very high gloss.
• Resistant to solvent and chemicals.
• They have rigid structure and form film with high hardness.
• High resistant to UV light and yellowing.
Usage areas of thermosetting acrylic resins
• Acrylic resins modified with acrylic amide; painting of household appliances in general,
such as dishwasher and coolers,
• Carboxyl functional acrylic resins when cured with epoxy resin; in the manufacture of household goods and metal decorative paints,
• Hydroxyl functional acrylic resins when cured with amino formaldehyde resins; because it
is resistant to external conditions and creates glossy films, in automobile top coat glossy and non-yellowing paint production,
• Hydroxyl functional acrylic resins when cured crosslinking agent isocyanates; car refinish
paints production.
References
Yürekli, Ş., Reçine ve Boya Teknolojisi, Cilt 1, 1995.
Deligny, P., Tuck, N., Resins for surface coatings, Acyrlics&Epoxies 2nd edition, Vol.1 (Edited by PKT Oldring), 2001.
Coating Formulation 2nd Revised Edition ,Vinzenz,Network 2012
Gündüz, G., Boya Bilgisi, Kimya Mühendisleri Odası, Ankara, 2007.
Dr. Çiğdem Yüceel Project and R&D Specialist
Serkim Resin
Zeynel Turna
R&D Specialist
Serkim Resin