Günümüzden yaklaşık 100 yıl önce hayatımıza girmeye başlayan polimerik malzemeler gelişen teknoloji ile birçok malzemenin yerini alarak hayatımızı değiştirmeye devam etmektedir.
Üstün mekanik özellikleri, kolay şekillendirilebilmeleri ve düşük yoğunlukları nedeniyle birçok sektörde kullanılan polimerler otomotiv sektörü için de çok önemli bir malzeme haline gelmiştir. Polimerlerin performanslarının yetmediği durumlarda ise polimerik kompozitler kullanılmaya başlandı.
İlk zamanlarda bu tür kompozit malzemeler termoset polimer matrisler kullanılarak geliştirildi. Çok yüksek mekanik değerlere ulaşılmasına, oldukça hafif olmasına karşın otomotiv gibi saniyelerin önemli olduğu üretim prosesleri için oldukça uzun olan proses süreleri en büyük sorundu.
Ayrıca bu malzemelerin geri dönüşümlerinin olmaması ve üretimi sırasında açığa çıkabilen VOC (uçucu organik bileşikler) bu tür ürünlerin yerini termoplastik kompozitler almaya başladı.
Kompound olarak enjeksiyon prosesinde kullanılan termoplastik kompozitlerin gelişmesi ile prepreg ya da dokumasız yüzeyler olarak termoform yapılmaya başlandı.
Böylelikle geri dönüşümü olan oldukça yüksek mekanik dayanımı olan ve bir o kadar hafif parçalar üretilebilir hale geldi. Fakat bu gelişme otomotiv için yeterli olacak mıydı?
Dünyada ve ülkemizde artan nüfus ve şehirleşme, değişen yaşam şartları ve teknoloji ile araç sayısıyla birlikte araçtan beklenen konfor güvenlik gibi özelliklerde artmıştır. Bu artış ile araçlara eklenen ekstra donanımlar günümüz araçlarının ağırlıklarının 50 yıl öncesine göre neredeyse iki kat yükselmesine neden olmuştur.
Bu artışa paralel olarak gelişemeyen içten yanmalı motor teknolojileri ve alternatif yakıtlı motor teknolojileri araçların dünyamızı hızla kirletmesini engelleyememiştir.
Bu nedenle otomotiv firmaları araçlarını hafifletme yoluna yönelmiş ve bu konuda uluslararası anlaşmalar ile kabul edilen emisyon hedefleri için hızlı bir şekilde çalışmaya başlamıştır. CAFE regülasyonları bu yasal düzenlemelerin en başında gelmektedir.
Bu düzenleme ile kademeli olarak binek araçların CO² emisyon değerleri 95 gr/Km seviyesine çekilmek istenmektedir. Bu değerin araç başına değil marka başına verildiğini belirtmek gerekir. Bu nedenden dolayı firmalar içten yanmalı motorlu araçların yanında hızla elektrikli araçları Piyasaya sürmeye başlamıştır.
Elektrikli araçlarda da tek şarjda gidilebilecek yolu arttırmak için hafifletme yapılması gereken en önemli gereksinimler arasındadır.
CAFE Regülasyonları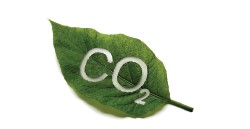
Termoplastik kompozitler ile belli bir düzeye gelen otomobil ağırlıkları henüz istenilen seviyeye çekilemedi. Bu nedenle farklı takviye malzemeleri kullanılmaya başlandı.
Bu malzemelerin başında ise doğal elyaflar başta gelmektedir. Doğal elyaf katkılı kompoundlar dışında termofor yapılabilen woodstock (%50 polimer + %50 odun talaşı) denilen malzemeler yoğun olarak kullanılmaya başlandı.
Woodstock Levhalar
Günümüzde kullanılan bir diğer yapı ise polimer ve doğal elyafın dokusuz yüzey yani keçe halinde birleştirilmesi ve termoform ile şekillendirilmesidir. Bu tür malzemeler istenilen parça kalınlığında ve istenilen ağırlıkta üretilebilmektedir.
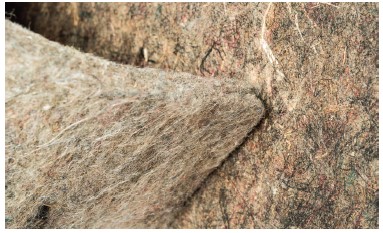
Projemiz kapsamında hedef olarak ağırlık azaltmanın yanında parçanın karbon ayak izinin de en düşük seviyeye düşürülmesi hedeflendi.
Bu amaçla mevcut durumda PP (Polipropilen) %20 talk katkılı hammaddeden enjeksiyon prosesi ile üretilen bir parça baz alınarak PP yerine bio bir polimer, talk yerine doğal elyaf ve enjeksiyon işlemi yerine termoform kullanılarak bu parçanın üretilmesi hedeflenmiştir.
Bilindiği üzere, 1 ton PP üretimi sırasında 6 ton CO2 emisyonu oluşmaktadır. Yapılan bu çalışma ile ağırlık azaltmanın yanında PP üretimi sırasında oluşacak CO2 emisyon değerlerini düşürmeyi hedeflemekteyiz.
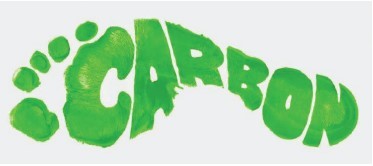
Yapılan araştırmalar sonucunda mekanik, ısıl özellikleri ve üretebilirlik açısından parçaya en uygun olan polimerin PLA (Poli laktik asit) olduğu görüldü.
Polilaktik asit (PLA) biyopolimeri yenilenebilir kaynaklar kullanılarak üretildiği için firmaların sürdürülebilirlik politikalarını gerçekleştirmek amaçlı önemli rol oynamaktadır. Çoğunlukla bitkisel kaynaklardan elde edilen şekerin fermantasyonu sonucu üretilen laktik asidin polimerizasyonu ile üretilmektedir.
PLA biyoplastik çeşitleri arasında konvansiyonel plastik hammaddelere fiyat açısından en yakın özellikte olan polimerdir, bu sayede son yıllarda geniş bir kullanım alanı bulmaktadır.
Fakat özellikle kırılganlığı ve düşük darbe mukavemeti sebebiyle ve konvansiyonel plastik işleme makinalarında işlenmesinin daha zor olması gibi etmenlerden dolayı çoğunlukla çeşitli kampaundların ana bileşeni olarak kullanılmaktadırlar. Biobozunur özelliklerinden dolayı ise birçok gıda ambalajı da bu malzemeden üretilmektedir.
Projede plakalar halinde istenilen özellik ve ölçülerde alınan iki adet PLA tabakanın arasına Jüt kumaş ya da UD lifler konularak sandviç bir yapı oluşturulmuş, bu yapı daha sonra ısı ve basınç ile birbirine lamine edilmiştir. Bu çalışma Kocaeli Üniversitesi öğretim üyesi Sayın Doç. Dr. Güralp Özkoç’un gözetiminde yapılmıştır
Sandviç yapı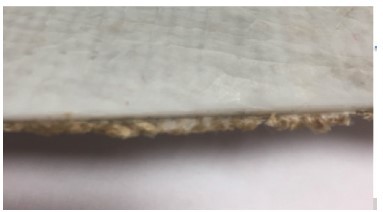
PLA+Jüt Tabaka
Üretilen plakalardan numune çubukları alınarak mekanik değerler ölçülmüştür. Bu çalışmada üretilmesi hedeflenen otomobil iç trim parçasının araç üzerine takılabilmesi için gerekli bağlantı kulelerinin parça üzerine kaynak yapılması için tabakanın bir yüzeyindeki PLA kalınlığı daha fazla alınmıştır.
PLA + Jüt Tabaka Kesit Görünümü
Farklı oranlarda hazırlanan PLA + Jüt kompzit tabalar için çekme, DMA (Dinamik Mekanik Analiz) ve Nem tutma testleri gerçekleştirildi.
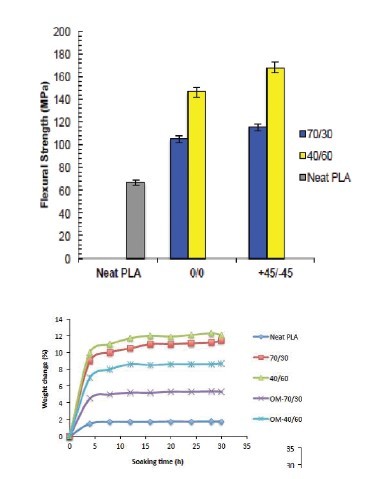
Yapılan değerlendirmelerde üretilen malzemenin mekanik değerlerinin otomobil şartnamelerine göre oldukça uygun olduğu görüldü.
Fakat malzemenin tabakalı yapısından dolayı detay verme konusunda sıkıntılar ile karşılaşıldı. Ayrıca üretim tekniğinin oldukça zor ve hatlara açı olmasından dolayı otomotiv için özellikle istenilen parçada kullanılamayacağı kanısına ulaşıldı.
Bu aşamada mevcutta farklı bir proje kapsamında üretilen PP + Kenevir keçe yapılarına benzer plakalar üretilmesi konusunda çalışmalar başladı. Başlangıçta PLA’nın mekanik özelliklerinden dolayı zorluklar ile karşılaşılacağı kanı olmasına karşın temin edilen PLA liflerin prosese oldukça uygun olduğu görülmüştür.
Kenevir Lifleri PLA Lifleri
PLA + Kenevir lifleri keçe üretim prosesinde işlenerek 1600 gr/m² olarak üretilmiştir. Bu keçe yapıları belirli süre ve ısılarda contact ve infrared fırınlarda ısıtılarak pres altında şekillendirilmiştir.
Contact Fırın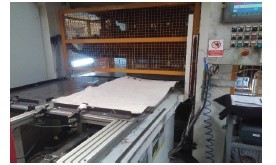
Form kalıbı üzerinde ısıtılmış PLA+kenevir Keçe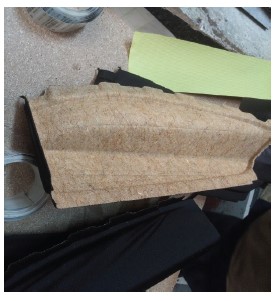
Şekillendirilmiş ürün
Bu tür malzemelerin şekillendirilmesinde sıcak malzeme, soğuk kalıp kullanılması uygundur. Kalıp içerisine yerleştirilen bir çerçeve vasıtasıyla üretilen ürün uygun bir kumaş ile kaplanabilir.
Bu proseste Poliester non- woven bir kumaş kullanılmıştır. Parçanın araç üzerine takılmasını sağlayacak bağlantı noktaları parçanın tasarımında yapılacak değişiklikler ile eklenecektir.
Projemiz ana sanayi ortaklı bir TEYDEB projesi olarak da devam ettirildiğinden dolayı keçe formunda yapılan çalışmalar konusunda henüz bilgi verememekteyiz.
Genel olarak yapılan çalışmada üretilen parçaların mevcutta kullanılan parçadan daha hafif olduğu ve mekanik değerler olarak istenilen değerlere oldukça yakın olduğu görüldü. Proje başında üretilen sandviç kompozitteki şekillendirme sorunları keçe yapısında görülmemiştir.
Ayrıca keçelerde polimer ve doğal lifler birbiri içinde karıştığından dolayı mekanik olarak da bir tutunma görülmüş ve polimerin elyafı ıslatma gerekliliği azalmıştır. Mekanik dayanımlar bu tür yapılarda üretim esnasındaki tasama yönüne göre değişebilir.
Sonuç olarak yapılan çalışmada hedeflenen araç hafifletme gerçekleştirilmiş ve bunun yanında karbon ayak izi oldukça düşük bir malzeme üretilmiştir. Parçanın otomobil ana sanayi şartnamelerine uyumu konusunda çalışmalar sürdürülmektedir.
Bu çalışmalar mekanik değerler yanında birçok klimatik çevrim ve yol testlerinin yapılmasını kapsamaktadır. Ayrıca mevcut koşullar ve gereklilikler göz önüne alındığında parçanın hammadde maliyetinin mevcut parçadan çok daha fazla olduğu görülmektedir.
Fakat yakın zamanda yürürlüğe girecek regülasyonlar ve üretim adetleri göz önene alındığında üretilebilir bir seviyeye geleceği düşünülmektedir.
Kadir Çatak
Ar-Ge Kıdemli Uzmanı
Fompak Ambalaj ve Poliüretan San. Tic. A.Ş.
Kaynaklar
• Kütahya Fompak İç Trim Üretim Tesisi Yönetimi
• Doç. Dr. Güralp Özkoç ve Ekibi – Kocaeli Üniversitesi
• Hassan Grup – Şiteks Tekirdağ / Saray tesisleri
• www.biyoplastik.com