Elektrostatik toz boya yöntemi, çeşitli tozların elektrostatik olarak bir depodan hortum yardımıyla boyanacak parçaya yüksek voltaj jeneratörüyle ile yüklü olarak atılması veya püskürtülmesi olarak bilinmektedir. Toz boyanın çalışma prensibi; topraklanmış iş parçası ile tabanca ucunda, parça yüzeyi arasında elektrostatik alan oluşmasıdır. Bu uygulama diğer boya sistemlerine göre düşük boya maliyeti, daha az üretim riskleri, çevre kirliliğine karşı avantaj sağlamaktadır. Toz boya tesisleri sanayide çok sık karşılaşılan ve ATEX yönetmelikleri kapsamında risk analizi yapılıp patlamadan koruma dokümanı hazırlanması gereken tesislerdir. Bu makalede yüksek basınçlı döküm aydınlatma parçalarında toz boya hataları ve çözüm öneri süreçleri analiz edilecektir
1.1. Toz Boya Hakkında Genel Bilgi
Dünyada oluşan çevre bilincine paralel olarak geliştirilen, metallerin ve toz boya materyalinin bir manyetik ortam içerisinde farklı elektrikle yüklenmeleri, bunun sonucunda toz materyalin mıknatıs etkisiyle metal yüzeyi kaplaması esasına dayanan bir boyama yöntemi olarak ortaya çıkmıştır. Toz boya kaplanan metal yüzey 180-200°C derece yüksek ısı ile fırınlanarak boyanın kürlenmesi sağlanmakta ve böylece metalin bir parçası haline gelen boyalı bir yüzey elde edilmektedir.
Günümüzün önde gelen çevreci bir ürünü olan elektrostatik toz boya, uygulama esnasında kullanılan boya miktarının %98’inin metale tutturulabilmesi sonucuyla bunu kanıtlamaktadır. Uygulama, püskürtme esnasında boya zerreciklerini, çok düşük 07 mA ve çok düşük doğru akım yükleyerek topraklanmış parçanın üzerine transferidir. Sistemde diğer elektrikli el aletlerindeki gibi (matkap motoru, vs.) cereyan çarpma ihtimali yoktur. Boya tabancadan çıkarken (-) elektrik yüklenir. Boyanarak topraklanmış parçanın yüzeyine çengel şeklinde kuvvet yollarını takip ederek gider.
Boya zerrecikleri; zıt kutuplar birbirini çeker prensiplerine göre parça üzerine çekilirler. Ancak kendi aralarında aynı kutupta olduklarından birbirlerini iterek homojen dağılımı sağlarlar. Böylece akıntı ve damlama ihtimalini yok denecek düzeye indirirler. Polimer tozlarının elektrostatik olarak kaplanacak parçaların üzerine ayrıştırıldıktan sonra eritilmesi ile meydana gelen kaplamaya toz boya kaplama denir. Elektrostatik toz boyama solvent içermeyen bir yüzey kaplama metodudur. Kaplayıcı malzeme, son kat boya tabakasını oluşturan çok ince toz boya partikülleridir. Toz boya, boya kabininde özel boya tabancaları vasıtasıyla atılır.
Tabancadan geçerken elektrostatik yüklenen toz boya partikülleri kabin içinde boyanacak malzemeye yapışır ve kaplama işlemi gerçekleşmiş olur. Toz boyanın malzeme yüzeyine tam olarak yapışabilmesi için malzemenin de çok iyi bir şekilde topraklanması gerekir. Fazla atılan boya, kabinde bulunan boya geri kazanım sistemi sayesinde toplanır ve tekrar kullanıma sokulur. Boya geri kazanım sistemi elektrostatik toz boyama teknolojisinin en büyük ekonomik avantajlarından biridir. Malzeme toz boya ile kaplandıktan sonra pişirme fırınına girer. 200ºC olan fırın ısısı toz boyanın erimesini ve malzeme üzerine yapışmasını sağlar. Sonuçta çok dayanıklı, ekonomik, çevre dostu, geniş renk yelpazeli ve parlak bir yüzey kaplaması elde edilir.
Solvent içermemesi, yüzey kalitesi, dayanıklılığı, boya geri kazanım sistemi, ekonomikliği ve çevre duyarlılığı elektrostatik toz boyamayı geleneksel boyama işlemlerine göre daha çekici bir alternatif yapmaktadır.
Alüminyum ve çelik parçalar üzerinde uygulanan toz boyama teknolojisinin son yıllardaki sürekli gelişimi endüstriyel yüzey kaplama alanında önemli bir atılımın gerçekleşmesini sağlamıştır. Birçok ihtiyaca kolaylıkla çözüm sağlayan toz boyama teknolojisinin kaplama, dış görünüş, kalite, dayanıklılık, ekonomi ve çevre korunumu gibi geleneksel boyalara göre sayısız avantajları vardır [1-4].
1.2. Toz Boya Teknolojisinin Avantajları;
• Mükemmel Kaplama,
• Bakım Kaplama,
• Çevre Korunumu,
• Ekonomik,
• Kazandıran Yatırım.
1.3. Toz Boya Uygulama Teknikleri
Toz boyanın uygulanması elektrostatik temele dayanır. Toz boya partiküllerinin belirli bir basınçtaki hava ile boya tabancasına gönderilmesi ve elektrostatik yüklenerek daha önce topraklanmış malzeme üzerine püskürtülmesi olarak açıklanabilir. Toz boya ile yüzey arasında boyanın eksi (veya artı) yüklenmesinden dolayı bir çekim meydana gelir ve boya malzemeye elektrostatik olarak yapışır. Daha sonra 200ºC lik fırında eriyerek birbirine ve malzemeye yapışır. Bu prensipten yola çıkarak yapılan araştırmalarda boya partiküllerinin genel olarak 2 değişik metotla yüklenebileceği ortaya çıkmıştır. Bunlar; Corona (iyonlaşma) ve Tribo (elektro kinetik) teknikleridir.
a) Corona Tekniği: Bu teknik tabanca gövdesinin içerisinde bulunan kaskatın, tabancanın ucunda bulunan iğneye gönderdiği yüksek voltajla (max 100 kV) tabancadan çıkan boyaya elektrik yüklenmesi prensibine dayanır. Yüksek voltaj havanın nötral durumunu bozarak eksi iyonlar oluşturmaktadır. Bu iyonlar birbirine ya da en yakın objeye yani toz taneciklerine tutunmaktadır. Böylece toz boya partikülleri de yüklenip, daha önce topraklanmış yüzeye püskürtülmektedir. Daha sonra malzeme 180ºC - 220ºC arası sıcaklıktaki fırına girerek üzerindeki boyanın erimesi, birbirine ve yüzeye iyice yapışması sağlanmaktadır. Corona metodunun en büyük avantajı; kolaylıkla yüklenebilmesi ve şu anda üretilen her türlü termoset toz boya ile başarıyla uygulanabilmesidir.
b) Tribo Tekniği: Bu sistemde hava ile boya, tabancaya geldikten sonra özel olarak tasarlanmış yollardan geçmesi ve sürtünmenin etkisiyle elektrostatik yüklenmesi temeline dayanır. Tribo sisteminde kaskat bulunmaz toz partikülleri sürtünme ile kinetik olarak yüklenir. Bu mekanizma farklı yüklerdeki iki maddenin (birisi elektron almaya diğeri elektron vermeye meyilli) birbirleriyle teması sonucu harekete geçer. Tribo tabancaların içerisindeki özel tasarlanmış yükleme yolları mekaniksel özelliğinden dolayı fazla toz boya birikimi sağlamayan ve yüzeye yapışmadan hızlı bir yüklemeye olanak veren PTFE yani teflondan yapılmaktadır.
1.4. Toz Boyanın Kullanım Alanları
Toz boya, otomotivden inşaata beyaz eşyadan bisiklet sanayine kadar çok geniş bir kullanım alanı bulunmaktadır. Ayrıca, her çeşit alüminyum saclar, çelik kapı ve asansör sistemleri ve her türlü metal malzemeler toz boyanın kullanıldığı yerlerdir. Görüldüğü gibi toz boyama, çok geniş bir kullanım alanına sahiptir.
2. Toz Boya Uygulama Hataları
Toz kaplama uygulaması sırasında birçok faktöre bağlı olarak bazı sorunlar ortaya çıkmaktadır. Bu çalışmada toz boya uygulama esnasında karşılaşılan problemler ve çözümleri açıklanacaktır.
Elektrostatik toz boya prosesi yöntemiyle üretim esnasında aparat tasarımı, tabanca konumu, hava debi değeri, çevresel faktörler, amper ve voltaj değerleri gibi birçok farklı etmene bağlı olarak hata türleri meydana gelebilmektedir. Bu hataları önlemek için problem doğru olarak tanımlanmalı, problem çözme teknikleri kullanılarak hata için kök neden tespiti yapılmalı ve gerekli aksiyonlar alınarak sonuçlar takip edilmelidir.
Bu çalışmada; yüksek basınç alüminyum enjeksiyon döküm prosesinde üretilmiş olan aydınlatma ve motor gövdesi parçalarının toz boya prosesi esnasında karşılaşılan hatalar ve çözüm yöntemleri incelenecektir (Tablo 1) .
Tablo 1. Yüksek basınç alüminyum enjeksiyon döküm yöntemiyle üretilmiş olan parçaların toz boya prosesi esnasında karşılaşılan hatalar ve çözüm yöntemleri
3. Toz Boya Prosesinde Aydınlatma Sektöründe Kullanılan Örnek Parça Üzerinde Hata Analizi ve Çözümü
Bu bölümde aydınlatma sektöründe alüminyum yüksek basınç enjeksiyon yöntemi ile üretilmiş olan örnek bir aydınlatma parçasında karşılaşılan toz boya hataları ile ilgili problem çözme teknikleri kullanılarak kök neden analizi yapılacak ve yapılan iyileştirmeler sonrası alınan sonuçlara ilişkin veriler paylaşılacaktır.
3.1. Mevcut Durum Analizi
Elektronik pompa sektöründe kullanılan alüminyum gövde parçalarının toz boya işlemi esnasında birçok hata ile karşılaşılmış, mevcut durum analizi yapabilmek için hata çetele formu oluşturulmuş ve sahadan veriler toplanmıştır. Toplanan veriler neticesinde oluşturulan hata çetele grafiğinden (Şekil 1), görülebileceği gibi hata türleri ve karşılaşma sıklıkları yüzdesel olarak pareto diyagramında tanımlanmıştır.
Toplam hataların %80’ine karşılık gelen tüm hatalar için önlem alınması gerekmektedir. Grafikte toplam hataların %80’ini oluşturan hata türleri; portakallaşma %52.35, çerçeve etkisi %13.42, blister %12.08 ve krater %6.71 olarak saptanmıştır. Karşılaşılan hata türlerinin kök nedenleri aynı nedene dayanabileceği gibi farklı nedenlerden de kaynaklanıyor olabilir. Bunun için hata türünü doğru olarak tanımlamak ve parça üzerinde hatanın bulunduğu konuma öre değerlendirmede bulunmak elzemdir.
[caption id="attachment_123740" align="aligncenter" width="742"]
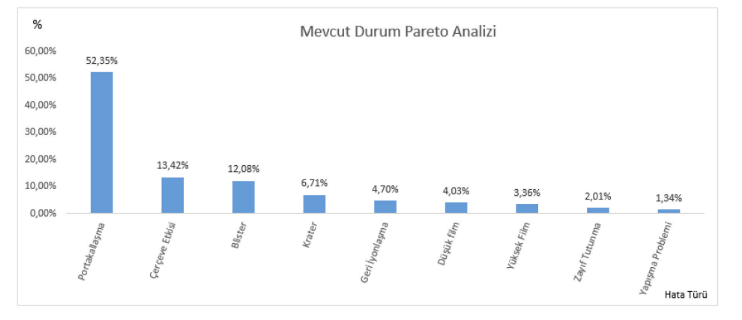
Şekil 1. Mevcut Durum Hata Pareto Analizi[/caption]
3.2. Çözüm Planı
Mevcut durum için yapılan balık kılçığı analizi sonrasında tüm olasılıklar göz önünde bulundurularak saha çalışması yapılmış, Toz boya esnasında problemli bölgede tabanca ayarlarının, tabanca nozül büyüklüğü, tabanca açısı, tezgah topraklamasının ve havanın basıncının sabit olmamasından dolayı oluştuğu gözlemlenmiştir.
3.3. Sonuçların Değerlendirilmesi
Pareto analizinde belirtilen portakallaşma (hatalı bölgedeki yetersiz topraklama, hava ve tabanca ayarlarının), yapılmamasından dolayısı ile önüne geçilemez sonuçlar doğurmaktadır. Yapılan kök neden analizi sonucu olarak hatanın kök nedeni hatalı bölgedeki tabancaların, konumlarının, aparatların temizliği ve hava basıncının yetersiz olduğu tespit edilmiştir. Bunun için hatalı bölgede ki uygulamalar arttırıldı. Mevcut durum hata türü pareto analizinde (Şekil 1) portakallaşma hatası %52,35 olarak görülmekte iken, iyileştirme sonrası hata oranları grafiğinde de (Şekil 2) görülebileceği gibi portakallaşma hatası ile karşılaşılmamıştır. Yapılan iyileştirme sonrası kazanılan işçilik, ergitme, geri dönüşüm vb. maliyetler toplam kazanç tablosunda gösterilmiştir (Tablo 2).
[caption id="attachment_123741" align="aligncenter" width="718"]
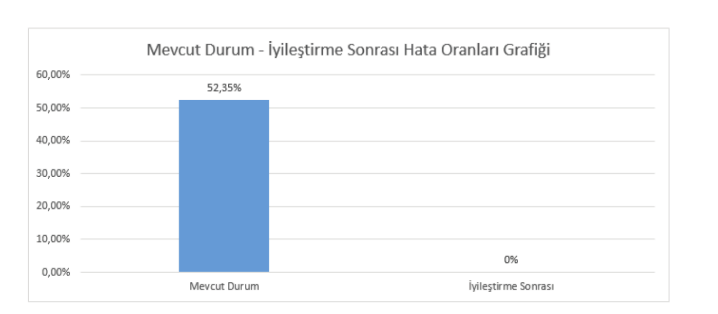
Şekil 2. Mevcut Durum – İyileştirme Sonrası Hata Oranları Grafiği[/caption]
4. Genel Sonuçlar
Dünya genelinde toz boya kullanımı gün geçtikçe artmaktadır. Aydınlatma, otomotiv, beyaz eşya gibi alanlarda daha çok kullanılmasının nedeni düşük maliyet ile yüksek korozyon direnci göstermesidir. Yüzey kusurları hem görünüşe hem de kaplamanın koruma sağlama yeteneğine zarar verir. En yaygın kusurlardan bazıları kraterleşme ve diğer yüzey gerilimi tahrik kusurları, kir ve patlamadır. Bu tür sorunları önlemek veya iyileştirmek çok önemlidir. Kaliteli ürünü kaliteli boya gösterir mantığı Avrupa ülkeleriyle rekabet etmemize olanak sağlamaktadır.
Örnek aydınlatma parçasında olası hata nedenleri incelendiğinde; pareto analizinde %52 ile portakallaşma hatası olduğu tespit edilmiştir. Tespit edilen hatanın çözümünde tabancaların konumlarının, aparatların temizliği ve hava basıncının yetersizliğinde yapılan iyileştirmelerle portakallaşma hatası tespit edilmemiştir. Böylelikle, bu hatanın ortadan kaldırılması ile işletmeye de 18.337 TL/Yıllık kazanç sağlanmıştır.
5. Referanslar [1] B. Fitzsimons and T. Parry, Fitz’s Atlas 2 of Coating Defects, MPI Group, Surrey, U.K., 2011 [2] Kenneth B. Tator, ASM Handbook Volume 5B: Protective Organic Coatings, ASM International, Ohio, USA, 2015 [3]RochesterInstituteofTechnology,PowderCoatingP rocess, https://www.rit.edu/affiliate/nysp2i/sites/rit. edu.affiliate.nysp2i/files/pdfs/powder_coating_process_final.pdf [4] Pulver, Electrostatic Powder Coating, http://www. pulver.com.tr/electrostatic-powder-coating