In the WHW Center for Innovation and Technology (CIT), new methods and solutions are developed every day. It’s not just about galvanic coating processes, but also process-related test methods, in order to assure our customers, in addition to the highest level of corrosion protection, other product properties, such as protection against hydrogen embrittlement.
To effectively prevent production-related hydrogen embrittlement, high-strength components must be tempered. It’s a complex and expensive process that is not only timeconsuming but also energy-intensive.
With STRONGARD & OXIGARD, the WHW Hillebrand Group has been offering defined coating processes for several years that do not require tempering and yet prevent the risk of hydrogen embrittlement.
For this purpose, the coating process at WHW is closely monitored and every critical process regarding hydrogen embrittlement is carefully checked and approved. This applies particularly to the pickling and coating processes.
The coating process will be carried out and the goods are delivered to our customers only after the final inspection.
Everything from a Single Provider
In order to increase the efficiency in this effective process chain, we strive to carry out all the necessary inspections inhouse. That means: The right measuring instruments must be available in the company, the know-how must be anchored and the measurement method must be suitable. One of these tests is the measurement of hydrogen permeation according to DIN EN ISO 17081. This is suitable for determining the hydrogen hazard potential in the pickling process.
In this test a permeation cell will be used. This consists of two half cells that are separated by a membrane. The principle of the measurement can be illustrated as follows:
The development of hydrogen takes place in the left half cell, it thus represents the “loading side”. The hydrogen is generated either by galvanostatic processes (e.g. galvanic deposition) or by chemical processes (pickling attack by hydrochloric acid).
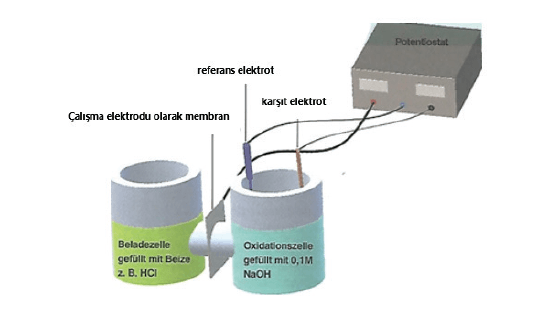
The adsorbed on the membrane through the membrane (migrates from “left to right” the membrane, due to the concentration gradient) and exits on the “measurement side”. The escaping hydrogen is immediately electrochemically oxidized in the right half-cell, creating one electron per hydrogen atom.
The hydrogen that passes through can be recorded quantitatively via the measured current. Which means, a current that flows over a certain time will be measured. The result is the charge in Coulomb, which is a measure of the hydrogen passing through and thus represents the hydrogen hazard potential.
In the past, the hydrogen permeation test at WHW Hillebrand was carried out by an external service provider. In order to meet our principle “everything from a single provider” also in the field of hydrogen embrittlement, a project was started at Hillebrand Chemicals in 2018, which will include this measurement in the portfolio of the WHW Hillebrand Group. Our goal: to carry out the hydrogen permeation measurement in-house in the future.
Said and Done
After the development of the method, the measurement method was validated. For this purpose, a round robin test was carried out with several independent testing institutes, including the State Materials Testing Institute of the TU Darmstadt.
The permeation measurement was established and integrated in the test laboratories of the WHW Hillebrand Group and has been used successfully ever since to ensure the required process reliability and efficiency for customers.
İzzet Aydın
General Manager
Hillebrand Chemicals Kimyasal Pazarlama Ltd. Şti.