İlke Endüstriyel Boyama Sistemleri ve Otomasyon A.Ş. has been active in the field of paint booths for more than 26 years. Throughout our experiences, many know-how has been acquired over the years and the information is stored within the framework of corporate memory.
The potential customer approach of our company in recent years has been evolved to provide the most suitable option to satisfy customer expectations by using this filtered information.
Firms that will invest in a painting plant, because they are composed of sector-specific customer-specific contract work, mostly do not know what they will get, make late or wrong decisions and cannot provide space-infrastructure-energy source for the facility.
As İlke Endüstriyel A.Ş. our approach has evolved in recent years to decrease the energy, first investment and operating costs of the companies that will invest and to adopt the latest technology to the global paint shop trends and environmentalist approaches. If we are to mention a few of our innovative projects in recent years;
İlke Endüstriyel A.Ş. Horizontal Paint Shop Project
Along with this project, the parts produced by our company, which consist mainly of flat surfaces, are loaded horizontally on roller conveyor.
Washing, nanoceramic coating, discharging of coarse water on the surface with air knife, gas infra-red system drying oven, robotic automatic painting system and gas infra-red cooking processes are carried out automatically.
The innovative side of this project is the horizontal use of flat and wide sheet metal surfaces, the use of a lanemark in-tank tube system in tank heating, and the horizontal use of gas type infra-red heaters in cooking and drying booths.
The first thing that comes to mind in all the paint shop designs is hanging these pieces vertically to the conveyor. With this automatic line completed, the flat surface parts were successfully powder coated, cured and passed the 350-400 hours saline test.
Ümit Bisiklet Automatic Wet Paint Application Plant with Turbo Disc System
This plant’s speed rate is approximately 2.5m/min. Plant processes; nanoceramic surface preparation, drying booth, primer coat application, primer coat flash-off, top coat application, top coat flash-off, clear coating, curing booth.
The plant has been successfully commissioned. 50% paint and filter savings have been achieved by directing the company’s first investment to turbo disc painting and surface quality has been standardized.
Toyota Plastic Department Apron Painting Booth
Toyota’s ready-to-serve service and manual spray booth which did not meet the company’s requirements have been re-designed from beginning. The new spray booth is highly efficient and capable of holding 100kg/m3 of overspray.
The differential pressure sensors of the filters read with a high accuracy. This information is processed in the plc group and decided how the system will operate according to the filters’ condition. The booth is designed to be environment-friendly as it’s wasting less energy and consumables.
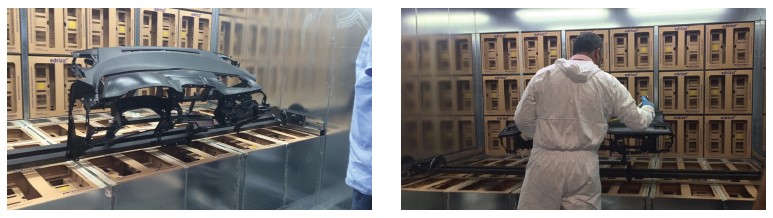
Company gains at the end of this investment can be summarized as; the company’s monthly maintenance downtimes have decreased, the energy consumption of the circulation pump in the water curtain cabinet has decreased to zero, the chemical consumption in the water curtain spray booth has been discontinued, solvent-VOC
odor problem in the factory has been eliminated, a brighter and more spacious painting environment is created, the most ergonomic painting position for the operator is ensured thanks to the adjustable hanger fixing device designed by our company for parts in different shapes.
Aydın Merken
Sales Manager
İlke Endüstriyel Boyama Sistemleri ve Otomasyon A.Ş.