Teknolojinin ilerlemesi ve insan popülasyonunun hızlı artışı, küresel dünyada büyük bir gereksinim olan enerji kaynaklarının tükenmesine yol açmaktadır. Yenilenemeyen enerji kaynaklarının büyük bölümünü oluşturan fosil yakıtların, önümüzdeki bir asır için yetersiz kalacağı öngörülmektedir.
Ayrıca, fosil yakıtların kullanımı karbondioksit salınımı nedeniyle oluşan küresel ısınma ve hava kirliliği gibi birçok olumsuz senaryolara neden olmaktadır.
Bu nedenle sürdürülebilir ve yenilenebilir enerji kaynaklarından olan güneş enerjisinden elde edilen elektrik enerjisinin kullanımı, fosil yakıt bazlı enerji kaynaklarının yerine geçebilecek güçlü bir seçenektir.
Bu çalışmada, Solaris Güneş Arabaları Ekibinin 7. solar arabası olan Solaris 11 isimli aracın polimer kompozit gövde imalatı incelenmiştir.
Kompozit malzemeler; iki veya daha fazla malzemenin mikroskobik düzeyde birleştirilmesi ile elde edilen ve geleneksel malzemelerden (demir, çelik, alüminyum vb.) daha iyi mühendislik özelliklere sahip olacak şekilde oluşturulan malzemelerdir.
Bu malzemelerin üretilme amacı her bir bileşenin tek başına sahip olmadığı veya olamayacağı özellikleri tek bir malzemede toplamak ve daha hafif, mukavemetli, rijit ve maliyet açısından daha uygun ürünler elde etmektir.
Polimer kompozit imalatında çeşitli yöntemler bulunmaktadır. Bunlardan en yaygın olarak kullanılanlardan biri ise el yatırma (elle tabakalama) yöntemidir. Bu yöntemin olumlu özelliklerinden bazıları; düşük üretim maliyeti, yerinde kalıplama olanağı ve tasarım esnekliği sağlamasıdır.
Uygulama alanı çok geniş olan bu yöntem özellikle yüksek mukavemet gerektiren oldukça büyük ve tek yüzü düzgün istenen parçaların üretimleri için uygundur. [1] Yöntemin uygulama şekli ise sıvı reçinenin bir takviye malzemesi ile açık kalıba uygulanmasıdır.
Kompozit malzemelerin en önemli avantajlarından biri, güneş enerjisi ile çalışan bir aracın enerji verimliliğini artıracak yönde hafiflik sağlamasıdır.
Güneş arabalarında elektrik enerjisi, yaklaşık altı metrekare yüzey alanına sahip güneş paneli (fotovoltaik) vasıtasıyla sağlanmaktadır. [2] Bu alana sahip panelden elde edilecek elektrik enerjisi yeterli miktarda değildir.
Bu nedenle, güneş enerjisi ile çalışan araç üretimlerinde polimer kompozit malzemeler tercih edilmektedir.
Enerjinin daha temiz elde edilebilmesi için güneş arabaların sayısı gün geçtikçe artmaktadır. Bu araçların verimliliklerini ve tasarımlarını geliştirebilmek için uluslararası yarışmalar düzenlenmektedir.
Bu yarışmaların en büyüğü Avustralya’da düzenlenen WSC (World Solar Challange) organizasyonudur. Bu yarışmalara katılan Solaris Güneş Arabaları Ekibi 2003’ten beri güneş enerjisi ile çalışan araç üretimlerini gerçekleştirmektedir. Bu çalışmada, Solaris ekibinin tasarladığı Solaris 11 isimli aracın polimer kompozit gövde imalatı ele alınmıştır.
Aracın Tanıtımı
Bilgisayar destekli çizim ortamında (Solidworks), Solaris 11 aracı Şekil 1 ve 2’de gösterildiği gibi modellenmiştir. Güneş enerjisinden elde edilen kısıtlı enerjinin verimli bir şekilde kullanılabilmesi için aerodinamik bilimi dikkate alınarak aracın geometrisi su damlası formuna yaklaştırılmıştır.
Böylece, yüksek hızlarda araca etkiyebilecek aerodinamik kuvvetlerin azaltılması amaçlanmıştır. Ek olarak, aracın tasarımında, ekibin katılacağı ilgili organizasyonların belirlediği yarış kuralları gözetilmiştir.
Malzeme Seçimi
Gövde imalatında kullanılan kompozit malzemeler iki ayrık bileşenin çeşitli imalat teknikleri yardımı ile bir araya getirilmesi ile oluşan yapılardır. Bu yapılardan biri takviye elemanı diğeri ise matris bileşenidir.
Takviye elemanı yapıya yüksek dayanım kazandırırken matris olarak adlandırılan diğer yapı, takviye elemanında bulunan lifleri sıkıca bağlayarak yapıya etki eden kuvvetlerin eşit bir şekilde yayılmasına olanak sağlar.
[3] Kompozit malzemeler matris malzemesine ve kullanılan takviye malzemesine göre sınıflandırılır. Tablo 1’de kompozit malzemelerin sınıflandırılması belirtilmiştir.
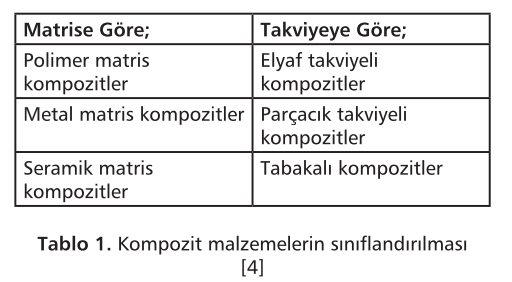
Genelde takviye elemanı olarak cam elyaf, kevlar fiber (aramid), karbon fiber vs. kullanılmaktadır. Solaris 11 aracında ise takviye elemanı olarak karbon fiber kumaş kullanılmıştır.
Bunun başlıca sebepleri; karbon fiberin oldukça güçlü ve dayanıklı bir malzeme olmasının yanı sıra düşük ağırlık / yüksek mukavemet oranına sahip olmasıdır. Tablo 2’de karbon fiber kumaşın mekanik özellikleri belirtilmiştir.
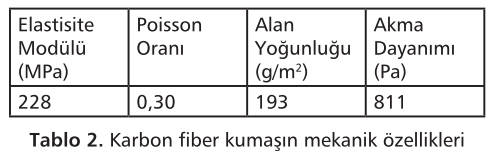
Otomotiv endüstrisinde yaygın olarak polimer matris kompozitler kullanılır. Polimerler genel olarak termoplastikler ve termosetler olarak ikiye ayrılır. Termoplastikler, ısı uygulandığında eriyen yüksek molekül ağırlıklı malzemelerdir.
Termosetler ise ısıya maruz kaldığında sertleşen ve bu halini sonsuza dek koruyan düşük molekül ağırlıklı polimerlerdir. [5] Termoset malzemelerden olan epoxy reçine, üretim sürecinde matris malzeme olarak tercih edilmiştir. Bunun nedeni, reçinede meydana gelen kimyasal tepkimelerin sonucunda, malzemeyi yüksek dayanımlı ve hafif ürünler elde edebilecek şekilde sertleştirmesidir. [1]
Karbon fiber polimer matrisli kompozitler temel olarak aşağıdaki özelliklere sahiptir:
• Düşük yoğunluk (alüminyumdan daha az),
• Yüksek mukavemet (çelik kadar güçlü),
• Yüksek sertlik (titanyum kadar sert ama yoğunluğu daha az),
• Kimyasal direnç,
• Titreşim sönümleme yeteneği,
• Düşük elektrik direnci. [6]
Yapının mukavemetini güçlendirmek amacıyla çekirdek (kor) malzeme olarak end-grain balsa kullanılmıştır. Tablo 3’te end-grain balsanın mekanik özellikleri belirtilmiştir.
Kalıpların İmalata Hazırlanması
Bilgisayar destekli ortamda tasarımı yapılan alt gövde ve üst kabuğu imal edebilmek için strafor kalıplar temin edilmiştir. Strafor kalıpların seçilmesinin nedeni düşük üretim ve malzeme maliyetine sahip olmasıdır.
Kalıpların ilk aşamada yüzey kalitesi yeterli seviyede olmadığı için yüzey iyileştirme çalışmalarına başlanmıştır. Yüzey iyileştirme malzemesi olarak poliüretan Jelkot seçilmiştir. Ayrıca, farklı zımpara numaralara sahip zımparalar kullanılmıştır.
Zımpara numara adlandırılması 1 inç uzunluktaki delik sayısını gösterir. Bu nedenle zımpara numarası arttıkça yüzeyde bulunan kumlar inceleşir. [7] İlk katlarda düşük, ara katlarda orta ve son katlarda yüksek numaralı zımparalar kullanılır.
•Strafor kalıpta taban yüzeyi oluşturmak amacıyla poliüretan bazlı macun uygulaması yapılmıştır.
• Sürülen macun işleminde bulunan kusurlar ve fazlalıklar zımparalanmıştır.
•İstenilen yüzey kalitesi elde edilene kadar Jelkot kat atma işlemi uygulanmıştır. Jelkot hızlı bir şekilde katılaştığı için kısa sürede kalıbın tüm yüzeyine atılmıştır. Her bir Jelkot kat atma işleminden sonra zımpara işlemi gerçekleştirilmiştir.
•Kalıpların yüzey kalitesi istenilen düzeye geldikten sonra tamamlayıcı işlem olarak su zımparası uygulanmıştır.
Tüm bu işlemler hem alt gövde hem de üst kabuk kalıbı için uygulanmıştır.
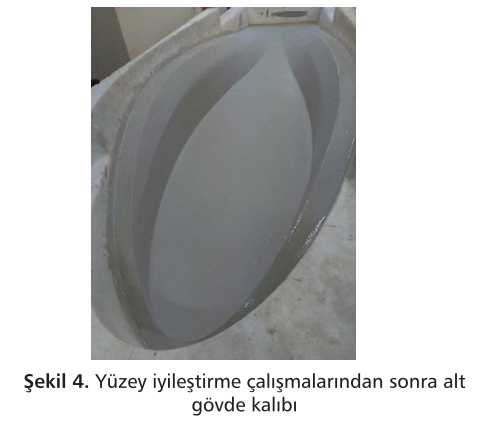
Kalıplara Malzeme Dökümü Kalıpların yüzey kalite işlemleri bittikten sonra ürünün kalıptan hasar almadan ve kolaylıkla çıkabilmesi amacıyla döküm işlemine başlamadan önce kalıp ayırıcı film kullanılmasına karar verilmiştir.
Ayrıca, kompozit malzeme bileşenleri polimer kompozit sandviç yapı tekniği kullanılarak bir araya getirilmiştir. Sandviç kompozitler, dış yüzeylerinde yüksek mukavemetli ve ince malzemelerin, çekirdek (kor) olarak adlandırılan orta kısımda ise düşük mukavemetli, kalın ve düşük yoğunluklu malzemelerin kullanıldığı yapılardır. [8] Şekil 5’te sandviç yapı gösterilmiştir.
Solaris 11 aracı üretiminde karbon fiber kumaşlar arasına çekirdek malzeme olarak end-grain balsa yerleştirilmiştir. Ek olarak, döküm tekniği olarak el yatırma yöntemi tercih edilmiştir. Şekil 6’da el yatırma yöntemi gösterilmiştir.
Üst Kabuk Üretimi
- Kalıba ilk olarak uygun ölçülerde kesilen kalıp ayırıcı film serilmiştir.
- Matris malzeme olan epoxy reçine, sertleştiricisi ile uygun oranda bir araya getirilerek yaklaşık 10 dakika karıştırılır.
- Alt kısımda iki kat karbon kumaş üstüne end-grain balsa kor malzeme ve onun da üstüne bir kat karbon kumaş yerleştirilmiştir. Bu işlemler yapılırken her kata hazırlanan epoxy reçine bileşimi, rulolar yardımı ile sürülmüştür. Ruloların kullanım amacı tabakalar arasında kalan hava kabarcıklarını gidermektir. [1]
- Son kata uygulanan reçine işleminden sonra karbon fiber kumaş üzerine filenin rahat sökülmesini sağlayan soyma kumaşı (Peel-Ply) yerleştirilir. [9]
- Epoxy reçine akışının orantılı olarak dağılımını sağlama amacıyla akış filesi serilmiştir. [10]
- Fazlalık olarak kalan reçinenin giderilmesi amacıyla keçe konulmuştur.
- Vakum ile kalıp arasındaki bağlantı elemanları olarak keçenin üzerine spiral ve T borular bağlanmıştır.
- Kalıp içerisinde vakum yaratmaya olanak sağlaması için vakum torbası serilmiş ve kalıbın kenarlarına vakum macunu uygulanmıştır.
- Vakum tezgahına yerleştirilen kalıp, kalıba yerleştirilen spiral ve T borular vasıtasıyla 600mmHg basınç değerinde vakum yapılarak ısıtıcılar yardımıyla 40 derece sıcaklıkta yaklaşık 15 saat boyunca kürlenmeye bırakılmıştır. Bu aşamada tezgâh 5 farklı noktadan sıcaklığı kontrol edilmiş ve veriler kaydedilmiştir.
- Kürleme işlemi bittikten sonra soyma kumaşı sökülmüştür. Ardından ürün kalıptan kolay bir şekilde çıkarılmıştır.
Alt Kabuk Üretimi
Üst kabukta gerçekleştirilen tüm işlemler alt kabuk üretiminde de uygulanmıştır. Fakat alt gövdenin kuyruk kısmına, araca etkiyen aerodinamik kuvvetlerin sönümlenmesi ve aracın ağırlık merkezinin bir miktar öne çekilmesi amacıyla balsa malzemesi yerine köpük yerleştirilmiştir.
Ayrıca, ürünün fiziksel durumundan dolayı yan duvarlarına aracın daha hafif olması amacıyla endgrain kor malzemesinin yerleşiminin Şekil 8’de gösterildiği gibi olmasına karar verilmiştir.
Sonuç
Sürdürülebilir enerji kaynakları ve kompozit malzemelerin araçlarda kullanımı çevreye daha duyarlı ve verimliliği yüksek araçların üretimine olanak sağlamaktadır.
Yenilebilir enerji kaynaklarının kullanımını artırmayı amaçlayan Solaris Güneş Arabalar Ekibi, güneş enerjisinden elde edilen elektrik enerjisinin kullanımını yaygınlaştıran çeşitli organizasyonlara katılım sağlamaktadır.
Güneş enerjisi ile çalışan araçlar için polimer kompozit gövde imalatında önem verilmesi gereken bazı hususlar bulunmaktadır. Bunlar;
• Kimyasal tepkimelerde bileşenlerin doğru karışım oranları, karışım sonucunda oluşacak özellikleri doğrudan etkilemektedir. Bu nedenle, farklı bileşenleri birbirine karıştırırken ölçülü ve hassas bir şekilde karıştırmak gereklidir. Aksi taktirde arzu edilen bileşim elde edilemeyebilir.
• Ürünün kalıptan deforme olmadan ve sorunsuz bir şekilde çıkması için kalıp ayırıcı film kullanımı büyük önem arz etmektedir. Ek olarak film, kalıbın yüzeyinde bulunabilecek lekelerin azaltılmasında rol almaktadır.
• Alınan ürünün yüzey kalitesi hassas olması istenilen yüzeylerde, kalıba zarar vermeyecek şekilde titiz bir çalışma ile zımpara işlemi yapılmalıdır. Zaman yönetimi ve işçilik göze alınarak zımpara kum yüzeyi, son katlara doğru incelmelidir.
• Reçine kürlenmesinin sağlıklı bir şekilde gerçekleşmesi için kalıbın kenarlarından, kalıp ile vakum torbası arasına vakum macunu yapıştırılırken dikkatli olmak gerekir. Çünkü vakumlama esnasında, bu noktalardan kalıbın içerisine hava girebilir ve istenilen basınç değerinde vakumlama işleminin yapılmasına izin vermeyebilir.
Bu çalışmada, bilgisayar destekli çizim ortamında tasarımı gerçekleştirilen ekibin 7. solar arabası olan Solaris 11 isimli araçta kullanılan malzemeler ve gövde üretim süreçleri anlatılmıştır.
Teşekkür
Solaris Güneş Arabalar Ekibi, Solaris 11 aracının üretiminde sağladığı karbon kumaş desteğinden dolayı Kordsa Teknik Tekstil A.Ş.’ ye teşekkür eder.
Referanslar 1. Işık A., “Kompozit Malzemeden İmal Edilmiş Bir Takviye Elemanının Eğilme ve Burulma Yükü Altında Deneysel ve Sayısal Olarak İncelenmesi”, İstanbul Teknik Üniversitesi, Fen Bilimleri Enstitüsü, Yüksek Lisans Tezi. 2. Aytaç GÖREN, “Güneş Enerjisi ile Çalışan Araçlar İçin Polimer Kompozit Gövde Tasarımı ve İmalatı”, PUTech & Composites, ISSN: 2146-9563, 5/22, Ekim-Kasım Aralık 2014, ss. 40-48, Aralık 2014.3. Aytaç GÖREN, Özgün BAŞER, Cuma POLAT, (2007), Mühendis ve Makina, Cilt:48 Sayı:569, “Güneş Enerjisi ile Çalışan Araç İçin Monokok Kompozit Gövde Tasarımı ve İmalatı”. 4. Volkan ARIKAN, “Sandviç Kompozitlerin Onarım Parametrelerinin İncelenmesi”, Dokuz Eylül Üniversitesi Fen Bilimleri Enstitüsü Doktora Tezi, Ocak 2019. 5. Hallal A., Elmarakbi A., Shaito A. and El-Hage H., “Advanced Composite Materials for Automotive Applications: Structural Integrity and Crashworthiness”, page 5.
6. D.D.L Chung, “Composite Materials”, page 1,2. 7. Arslan, F., “Metalografi Laboratuvarı Deney Föyü”, Karadeniz Teknik Üniversitesi, Metalurji ve Malzeme Mühendisliği Bölümü, Trabzon. 8. Tuğberk ÖNAL, Şemsettin TEMİZ, “Balsa Çekirdekli Sandviç Kompozitlerin Darbe Davranışlarının Deneysel Olarak İncelenmesi”, Malatya Turgut Özal Üniversitesi Hekimhan Meslek Yüksek Okulu, İnönü Üniversitesi Makine Mühendisliği Bölümü, El Cezeri Fen ve Mühendislik Dergisi Cilt: 8, No: 1, 2021 (333-345) 9. Batuhan KORKUT, Ahmet ÖZKAN, Aytaç GÖREN, “Elektrikli Otomobilde Kompozit Levha Kullanımı”, Putech & Composites, ISSN: 2146-9563, 8/38, MartNisan 2018, ss. 8-14, Mart 2018. 10. Fatma Ebru ALTINSOY, “Kompozit Malzemelerin Mekanik Bağlantılarında Higrotermal Etkiler”, Balıkesir Üniversitesi, Fen Bilimleri Enstitüsü, Ocak 2020, sayfa 29.
Mehmet Ali Pınar
Dokuz Eylül Üniversitesi Mühendislik Fakültesi
Makina Mühendisliği Bölümü
Mustafa Harman
Dokuz Eylül Üniversitesi Mühendislik Fakültesi
Makina Mühendisliği Bölümü
Asst. Prof. Dr. Aytaç Gören
Dokuz Eylül Üniversitesi Mühendislik Fakültesi Makina Mühendisliği Bölümü Picardy Jules Verne Üniversitesi Yenilikçi Teknolojiler Laboratuvarı