Sentetik Reçine Harç Girdileri
Dolgular: İnorganik dolgu maddeleri, sentetik reçine betonunun dayanım özelliklerini belirlemede önemli ölçüde yardımcı olan faktörlerden biridir. Sonuç olarak, sentetik reçine betonunun yüksek dayanımı yalnızca güçlü dolgularla elde edilebilir.
Parçacık boyutunun kompozisyonunun sentetik reçine betonunun dayanım özellikleri üzerindeki etkisi, inorganik harçlarla aynı kurallara bağlıdır. Bu nedenle Fuller eğrisine yaklaşan bir partikül büyüklüğü dağılımı önerilebilir.
Daha büyük ve daha küçük boşlukları doldurmak orta ve ince parçacıkların fonksiyonudur. Aşağıdaki en bilinen parçacık fraksiyonları, epoksi reçine harçları için uygun olan istenen herhangi bir parçacık büyüklüğü dağılımını sağlamaktadır.
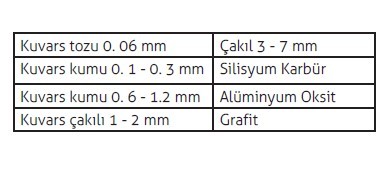
Parçacık boyut kompozisyonu önerilenden farklı olduğunda, özellikle hiç kuvars tozu içermediğinde, aşağıdaki iki sonuç ortaya çıkabilir.
a) Aynı bağlayıcı: Doldurma oranı ile tüm gözenekleri doldurmak için yeterli reçine bulunmamaktadır.
Gözenekli, hava boşlukları olan bir malzeme oluşur.
b) Daha büyük gözenek hacmi daha fazla bağlayıcı ile doldurulduğunda, yani kum: reçine oranı değiştirildiğinde, dayanım özellikleri zarar görür, darbe dayanımı daha düşüktür.
Silisyum karbür ve korindon gibi diğer yüksek nitelikli dolgu maddeleri ile daha da yüksek bir basınç dayanımı elde edilebilir. Sentetik reçine betonu için her zamanki olağan agregaların doğal dayanımı, bağlayıcı maddenin betonlaştıma kuvvetinden daha azdır.
Karşılaştırmalı olarak yapılmış sıkıştırma testlerinde sentetik reçine betonu ve çimento betonu parçalandığında, normal çimento betonundaki kırılma her zaman bağlayıcı maddede ortaya çıkarken, sentetik bir reçine betonunda ise kum parçacıkları kırılır.
Bu nedenle, sentetik bir reçine betonunda yalnızca yüksek kaliteli dolgu maddelerinin kullanılması önerilir.
Grafitin, kuvars veya silisyum karbür dolgularla kombine edilerek kullanılmasıyla, Alman kimya endüstrisinin yönergelerine uygun olarak, 106 Ohm’dan daha düşük bir kaçak akım direncinde elektrik ileten harçlar formüle edilebilir.
Sisteme grafit verilmesi, yüksek miktarda dolgulu harçların iyi olan mekanik dayanımlarını bozmaz. Bazı durumlarda, grafitin neden olduğu koyu renk çirkin olabilir, ancak titanyum dioksit eklenerek bu durum hafifletilebilir.
Epoksi reçine harçları, katran, koumaron-inden reçineleri ve öteki plastifiyanlar gibi sıvı seyrelticiler ile de modifiye edilebilirler. Bazen bu katkı maddeleri solvent bazlı ve solventsiz boyalarda avantaj sağlar, ancak yüksek dolgulu kaplamalarda düşük reaktivite ve düşük mukavemet gibi dezavantajlar verebilir.
Bağlayıcı üzerinden %20 gibi az miktarda koumaron reçinesi ile verildiğinde, kürlenme çok gecikir ve mekanik dayanım katkı verilmemiş harçtakinden yaklaşık %40 daha düşüktür.
Pigmentler:
Kum dolgulu dolgu macunlarının renklendirilmeleri kumun rengine bağlı olarak değişir. Normal olarak,açık renkli kuvars kumlarına toplam olarak karışımda %5 ila %1 pigment verilmesi yeterlidir.İnorganik pigmentler en iyisidir.
Pigmentler sentetik reçine betonuyla oldukça uyumlu olmalıdır ve ayrıca hava koşullarına aromatic solventlere de direnç göstermelidirler.
Ezilmiş mermer,renkli kum,pigmentler karıştırılarak özel dekoratif etkiler elde edilebilir.Tüm dolgu maddeleri kuru olmalıdır;yalnızca organik bileşenlerden arındırılmış kumlar kullanılmalıdır.
Bağlayıcılar:
Bağlayıcı yüzdesi,sentetik bir reçine harcının uygulama özellikleri için çok önemlidir.%20 veya daha fazla bağlayıcı madde ve belirli miktarda ince dolgulu (0,06 mm) harçlar self leveling harçlardır.Bu duruma minimum bağlayıcı ile ulaşmak için,dolguların yaklaşık %20si ince dolgu içermelidir.
Kalan öteki %80 dolgu maddesi ise Fuller eğrisine uygun olmalıdır.Yüksek bağlayıcı içeriği ve 2 mm’ye kadar kaba parçacıkların olması nedeniyle,karışım,homojen olmayan bir yapıda bir kaplama oluşturarak belli bir noktada çökelebilir.
Bu nedenle,self eveling sentetik reçine harçlarının darbe dayanımının,mala betonu ile aynı standartlarda olması beklenemez.
Darbe dayanımındaki belirli bir iyileşme, ince dolgu miktarını artırarak ve çökeltiyi azaltmak için kaba parçacıkları dışarıda bırakarak mümkün olabilir. Kuşkusuz, daha fazla dolgu yüzeyini ıslatmak için buna göre daha yüksek miktarda bir bağlayıcıya gerek duyulur.
Bazı durumlarda, daha büyük bir darbe dayanımı gerektiğinde, bu dayanım cam elyaf ekleyerek elde edilebilir. %0,5 kadar küçük bir oranda cam elyafı darbe dayanımını önemli ölçüde arttırır.
Uygulama özelliklerini sağlamak ve cam elyaflarını yeterince ıslatmak için biraz daha fazla bağlayıcı kullanılmalıdır. Liflerin neden olduğu ek keçe kumaş, betonun dikey yüzeylere uygulanmasına olanak sağlar.
Self leveling yamalar, 7 - 10 mm gibi çok kaba bir parçacıklar içerdiğinde, dolgu maddelerine ek olarak ince dolgular verildiğinde düşük oranda bir bağlayıcı ile elde edilebilir. Bir kaplamanın kalınlığı en büyük parçacık boyutunun üç katından az olmamalıdır, çünkü bu harçlar her amaç için kullanılamaz.
Gerçek kaplama, uygulamadan önce oldukça derin delikler açmak için kullanılabilir. Düşük bağlayıcılı sentetik reçine harçlarının uygulanması, emek açısından daha yoğundur, ancak özellikleri daha da iyi oluşur.
Bir kısım bağlayıcı ve altı kısım dolgu maddesi kompozisyonundaki harç mala ile uygulanmalıdır. Bu tür harçlar aşınmaya karşı oldukça dayanıklıdır ve basınç dayanımı çok yüksektir.
Reaktivite:
Reaksiyon hızını karakterize etmek için %14.3’lük bağlayıcı ve sertleştirici karışımı içeren 2 kg harç karışımının karışım ömrü için temsili değerler verilmiştir. Epoksi reçine bileşeni olarak epoksi eşdeğer ağırlığı 182-192 olan ve 9-13 Pa.s viskoziteli modifye edilmemiş epoksi reçine kullanılmıştır.
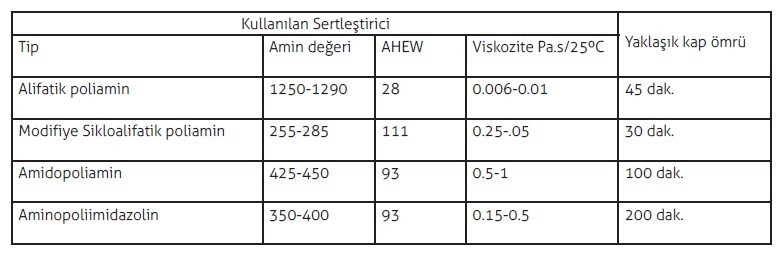
Epoksi eşdeğer ağırlığı 182-192 olan modifiye epoksi rezin kullanıldığında, kap ömürleri yaklaşık % 20 daha uzun olur.
Dolgu pastaları:
Birbirine benzeyen dolgu macunları, çeşitli sıvı epoksi reçinelerinin ve sertleştiricilerin viskozitesindeki farklılıklarına göre formüle edilebilir. Tüm sıvı epoksi reçinelerin olası sertleştirici bileşenleri olarak yukarıda sözü edilen sertleştirici tipleri önerilebilir.
Bunların avantajları, çok çeşitli zeminlere (örneğin beton, metal, ahşap, plastik) mükemmel yapışma, iyi esneklik ve çok düşük büzülme özelliğidir. İnorganik dolgu maddeleri karışımın %30-70’ini oluşturabilir.
Amaca bağlı olarak mineral veya metalik dolgu maddeleri kullanılır. Silisli ve silisli olmayan dolgu maddelerinin karışımları çok uygundur. Sertleştirilmiş dolgu macunlarının aşınması kolaydır ve tüm normal boyalarla boyanabilir.
Dolgu pastaları için inorganik dolgu maddeleri:Dolgu macunlarında modifiye edilmiş epoksi reçineler kullanıldığında, epoksi reçine bileşeni ve dolgu, uzun süreli depolamada reaksiyona girebilir. Karışım az ya da çok katı durumda olabilir ve hoş olmayan bir koku çıkarabilir.
Bu reaksiyonların çoğu, modifiye edilmemiş epoksi reçineler kullanılarak önlenir. Kuşku durumunda, hızlandırılmış bir test inorganik dolgu kullanımının uygun olup olmadığı konusunda bilgi sağlayabilir.
Dolgu için test yöntemi:
Test edilecek epoksi reçineyi, macun olana kadar gerekli dolgu maddesiyle karıştırın. Bu karışımın yaklaşık 25 - 30 ml’sini yaklaşık 50 ml’lik kapaklı bir kutuya koyun. Bu kapalı kutuyu dört saat boyunca 140°C’de bir fırında tutun.
Soğuduktan sonra oluşabilecek herhangi bir değişiklik ısıtılmamış örnekle karşılaştırıldığında kolayca belirlenir. Bu test yöntemi aşağıdaki etkileri gösterir:
• Dolgu pastasının kıvamı,çeşitli baryum sülfat türleri ve blanc fixe,Lithopone, Kalsiyum karbonat ve öteki kalsit türleri, Microdol, Çinko oksit, Kuvars tozu, Alüminyum ve demir tozu (azaltılmış demir) kullanıldığında aynı kalır.
• Dolgu pastasında, talk ve kayrak tozu kullanıldığında belirgin şekilde sertleşir:
• Dolgu pastasında, kaolin, grafit, Neuburg silisli tebeşir kullanıldığında katı duruma gelir.
Yüzeyin hazırlanması:
Kaplamanın, zemini hasara karşı koruma amacını tümüyle karşılaması için, iki yüzey mümkün olduğunca sıkı bir şekilde yapışmalıdır. Mükemmel yüzey hazırlığı sentetik reçine betonunun iyi yapışması için gerekli bir durumdur.
Kötü hazırlanmış bir yüzey, bağlayıcı sistemden bağımsız olarak, en başından itibaren iyi performansı tehlikeye atabilir.Metal yüzeyler uygun mekanik işlemlerle temizlenmelidir.
Çelik yüzeyler en iyi şekilde pas ve benzeri kalıntılardan kumlama ile temizlenir. Kumlamanın mümkün olmadığı durumlarda, en azından el ile pas çıkarma işlemi yapılması gerekir. Alt tabakanın gerektiği biçimde ıslanmasını sağlamak için gres, yağ ve öteki yabancı maddelerden arındırılmalıdır.
Herhangi bir kaplı beton da hazırlanabilir.Bazen çimento serpilerek hazırlanmış bir kaplama kalıntısının,yalnızca çok az bir dayanımı vardır.
Başka bir durum ise bağlayıcı astar bu kapalı yüzeye yalnızca büyük bir güçlükle penetre olur ve bu nedenle bu tür kaplamalar uygulamadan önce çıkarılmalıdır.Aynı şey,çok kuvvetli olmayan “su açlığı” diye nitelenen susuz beton için de geçerlidir. Alevle temizleme ve kumlama uygun hazırlama yöntemleridir.
Mekanik dayanım için eski beton kontrol edilmelidir. Kirlenmiş yamalar (yağ, gres yağı, kimyasal maddeler vb.) alevle yakılarak en güvenilir şekilde temizlenir. Yalnızca solventle temizlik yapmak yeterli değildir.
Betonun temizlendikten sonra bir sızdırmazlık malzemesiyle kaplanması önerilir. Amaç gözenekleri tıkamak ve bir sonraki kat için daha iyi bir yüzey sağlamaktır.
Böylece, emprenye edilmiş bölgedeki ufalanmış betonun içsel gücü de artırılmış olur.Bir sızdırmazlık maddesi özellikle beton çok yoğun ve pürüzsüz olduğunda veya arkadan su basıncı beklendiğinde (yeraltı suyu) önerilir.
Hem sıvı hem de katı reçine sistemleri uygun sızdırmazlık maddelerini olarak kullanılabilir, ancak sıvı reçineli olan tercih edilir.Bunlar, alt tabakaya daha iyi yayılır ve daha fazla katı içerdiklerinden yapışma bölgesini daha fazla sağlamlaştırır.
Bu amaç için kullanılacak sıvı reçine sistemleri,bir sonraki katın yapışmasının zarar görmesine neden olacak hidrasyonu önlemek için nemden etkilenmeyen sertleştiricilerle kullanılmalıdır.
Astar (bağlayıcı madde):
Bir yüzey,yüksek dolgulu bir sentetik sentetik harçla (ör., %10 bağlayıcı,%90 dolgu maddeleri) kaplanacaksa kesinlikle bir astar gereklidir, çünkü harç yüzeyi tümüyle ıslatmaya yetecek kadar bağlayıcı içermez.
Uygulamada normal olarak harcın bağlayıcı bileşenlerinden oluşan bir astar, gerçek sentetik reçine harcı ile kaplanmadan önce yüzeye uygulanır. Astarın iki amacı vardır:
1. Zemin ve uygulanan sentetik reçine betonu arasında bir bağlayıcı madde görevi görür.
2. Harcı mala ile yayılmasını kolaylaştıran yapışkan bir yüzey oluşturarak kaplama işini büyük ölçüde iyileştirir.
Astarlanmış alanın yalnızca kısa bir süre atmosferik nem tarafından saldırıya açık kalması için sentetik reçine betonunun kaplanmasından hemen önce astarın uygulanması önerilir. Astar neme duyarlı sertleştiriciler içerdiğinde bu nokta en katı şekilde gözlemlenmelidir.
Harç yayma işlemi sürekli olduğundan ve bu iş her zaman astarla kesildiğinden, uygulamada, oldukça uzun bir süre boyunca (büyük bir olasılıkla bütün bir çalışma günü) kaplanması beklenen alanın tamamının önceden astarlanması uygun olacaktır.
Bu nedenle en kötü durumda, astar, sekiz saat boyunca atmosferik nem tarafından saldırıya açık kalacaktır. Sentetik reçine harcının hidrasyonunu ve zayıf yapışmasını engellemek için, kesinlikle nemden etkilenmeyen sertleştiricilerin kullanılması gerekir. Astar ve harç arasında istenen bir bağın sağlanması için, son kat, astar jel durumuna gelmeden önce uygulanmalıdır.
Tiksotropik primerler:
Pürüzlü yüzeylerde, yüzey çöküntülerinde bulunan büyük bir miktarlardaki astarın, kaplamanın yüzeyine doğru çıkma, düzensiz bir yayılma, yağlı bir görünüme ya da malaya yapışan harca neden olma riski vardır.
Bu dezavantajlara, astara yaklaşık %3 Aerosil (füm silika) eklenerek önlenebilir. Harcın dikey yüzeylerde kaymasını önlemek için bir kat sentetik reçine harcı uygulanırken, bir tiksotropik astar kullanılmalıdır. Bu amaç için aşağıdaki astarı bileşimi kolay uygulama sağlar:
Eski betonla taze beton arasındaki bağlayıcı madde:
Taze bir çimento betonu, eski bir betona çok zayıf bir biçimde yapışır. Bu tip bir yapışma sorunu, epoksi reçine bazlı bir bağlayıcı madde ile giderilebilir.
Uygulamada amin değeri 230-260 ve AHEW 186 olan modifiye amino poliimidazolin tip sertleştirici / Epoksi Reçine veya amin değeri 370-410 ve AHEW 93 olan amino poliimidazolin tip sertleştirici / Epoksi reçine bazlı self leveling bir sentetik reçine harcı uygulanır.
Amin değeri 230-260 ve AHEW 186 olan modifiye amino poliimidazolin tip sertleştirici içeren bağlama ajanları her türlü tazel betona (nemli, plastik, pompalanabilir beton) uygundur.
Amin değeri 370-410 ve AHEW 93 olan amino poliimidazolin tip sertleştirici içeren bağlayıcı maddeler yanızca doğal olarak nemli veya yoğunlaştırılmış betonda kullanılmalıdır (En fazla su / çimento oranı = 0,5).
Çimento betonu, taze sentetik reçine harcı üzerine jelleşmeden önce dökülür. Sertleşmeden sonra, alt tabaka ile sentetik reçine harcı arasındaki ve ikincisi ile yeni beton tabaka arasındaki bağ mükemmeldir.Bağ test edildiğinde, kırılma derzlerden çok betonun gövdesinde ortaya çıkar.
Bağlayıcı madde en az %75 dolgu içermelidir. Kaba tanecikler de içeren dolgular, orada burada çimento betonu dökülürken yapıştırıcı maddenin itilmelerini önler.
M. Namık Kayaalp
Kimya Mühendisi
Ecelak Boya Kimya Ltd. Şti.
Kaynakça:
1. Schering Industrie-Chemikalien.
2. H.Lee, K.Neville handbook of Epoxy Resins.
3. Huntsman Advanced Materials (Switzerland) GmbHKlybeckstrasse 200 P.O. Box 4002 Basel Switzerland.
4. Epoxy Polymers, Edited by Jean-Pierre Pascault and Roberto J. J. Williams, WILEY-VLH Verlag umbH.
5. Paint and Coating Testing Manual Fifteenth Edition of the Gardner-Sward Handbook, Joseph V. Koleske.