Giriş
Yüzey profili,yüzeye yüksek hızda darbe uygulayan aşındırıcı ve belirli elektrikli aletleri kullanarak yaratılan darbe ile oluşan maksimum tepe vadi derinliği olarak tanımlanmaktadır. Bu temizleme yöntemleri yüzey alanını etkili bir şekilde arttırır ve uygulanan boya/kaplama sistemi için bir “tutunma noktası” sağlar.
Bir nevi çapa etkisi yaratır. Yüzey profili derinliği, toplam kaplama sistemi kalınlığına uygun olmalıdır; tipik olarak, kaplama sistemi daha kalın, yüzey profili daha derindir. Örneğin, 3 kat 300 mikronluk bir sistem 50-75 mikron profil isteyebilirken, 1000 mikronluk bir sistem 100-125 mikron profil isteyebilir.
Profil derinliği çok önemlidir. Çok derin yüzeylerde boya miktarını arttıramayacağınız durumlarda Pin point rusting (İğne başı paslanma) kaplama hatası, eğer sığ profil olursa kaplama yapışmaması ile karşı karşıya kalacaktır.
Dolayısıyla da minimum ve maksimum belirtilen yüzey profili derinliğine uygunluk boya/kaplama sisteminin başarısı açısından kritik öneme sahiptir.
Yüzey profili derinliğini etkileyen faktörler, hazırlanan yüzeyin dertliği ile kullanılan aşındırıcının türü, sertliği ve boyutunu içermektedir. Daha az önemli faktörler olarak kumlama nozulunun yüzeye mesafesi ve operatörün nozulu yüzeye tuttuğu açıyı içermektedir.
Elektrikli aletle temizleme için, alet türü ve ‘darbeli aletlerin” konfigürasyonu genellikle yüzey profili derinliğini belirler.
Aşındırıcı kumlama ve elektrikli alet ile temizlenmiş çelik yüzeyler, istenilen/belirtilen yüzey profilinin elde edildiğini doğrulamak için sürekli kontrol edilir.
ASTM D4417, Aşındırıcı Kumlama ile Temizlenmiş Çelik Yüzey Profilinin Saha Ölçümü için Standart Test Metotları, NACE International SP0287, Replica Bant Kullanılarak Aşındırıcı Kumlama ile Temizlenmiş Çelik Yüzeylerin Yüzey Profilinin Saha Ölçümü için Standart Uygulama ve SSPC: Koruyucu Kaplamalar Derneği PA 17, Çelik Profil / Yüzey Pürüzlülüğü / Tepe Sayımı Gereksinimlerinin Uygunluğunu Belirleme Prosedürü, bu ölçümlerin uygulanması için prosedürleri ve önerilen ölçümlerin sıklığını ve değerlerin kabul edilebilirliğini açıklar.
Ayrıca, standartlar düzgün çeliğin hazırlandığını varsayar; çukurlu çelik, yaşlandırılmış çelik veya dökme demir yüzeyler gibi pürüzlü veya düzensiz yüzeylerde yüzey profilinin ölçümü hakkında çok az şey anlatmıştır.
Bu makalede, bu düzensiz yüzey tiplerinde yüzey profilinin ölçülmesi için önem arz edebilecek birkaç yöntem ve tercihler izah edilmektedir.
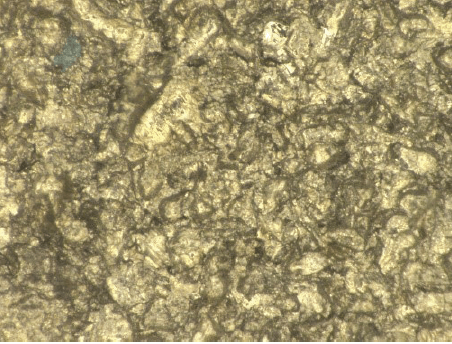
Uzun süreler boyunca hizmet veren birçok çelik yapı, korozyon nedeniyle düzensiz, pürüzlü yüzeyler içerebilir. Genellikle bu, çelik kalınlık kaybı ile neticelenir ve hatta değiştirme gerektirebilir.
Fakat çelik alt tabakaya tamirat yapılması için yeterli miktarda çelik kaybının meydana gelmediği sonucuna varıldığında, kaplama uygulayıcısı, şartnamenin yüzey profili gerekliliklerini sık sık aşan pürüzlü yüzeyler üzerinde temizlik ve profil edinimi için şartname gerekliliklerine uymakla karşı karşıya kalır.
Aynı şekilde, dökme demir ve yaşlandırılmış çelik gibi diğer çelik yüzeyler (ASTM A588, A242, A606-4, A847 ve A709-50W), tipik olarak atmosfer koşullarından etkilendikten sonra aşındırıcı ile kumlanmış ASTM A36 çeliğinden daha pürüzlü bir yüzeye sahiptir ve şartname izin verilenden daha yüksek bir yüzey profili edinimine ve neticede bir uygunsuzluğa neden olur.
Pürüzlü veya çukurlu yüzeylerde yüzey profili ölçümü genellikle yanlış yüksek okumalara sebep olabilir, çünkü ölçümler çukurların derinliğinin veya çeliğin iç yüzey pürüzlülüğünün, aşındırıcı veya darbe tipi elektrikli aletin kendisi tarafından oluşturulan yüzey profilinden farklı olduğunu ortaya çıkarır.
Bu durum, “Bu tür yüzeylerdeki yüzey profilini nasıl doğrularsınız?” sorusunu sormaktadır. Dikkate alınabilecek birkaç alternatif vardır; ancak, gerektiğinde tartışılmalı ve proje içi ölçüm sırasında değil, iş öncesi toplantıda görüşülmelidir.
Muadil Metotlar
İlk yöntem, hangi metodun seçildiğini / belirtildiğini (derinlik mikrometresi veya replika bandı) dikkate alarak istenilen bir alanda (pürüzlü olmayan) ölçümler elde etmektir. Bununla beraber, çukur veya pürüzlü çelik tek düze olduğunda bu mümkün olmayabilir.
Danışılan standartlarda listelenen üç yöntemden, derinlik mikrometresi (ASTM D4417’de Metot B) genellikle bu durumlarda optimum olarak kabul edilir, çünkü tek bir vadi ölçümü elde edilebilir ve aletin üst aralığı replica bant kullanarak (125 mikron) makul ölçülerde ölçülebilen maksimum değerden (500 mikron) daha yüksektir.
Bir alanda en az on ölçüm yapılır ve ortalama yüzey profili hesaplanır.
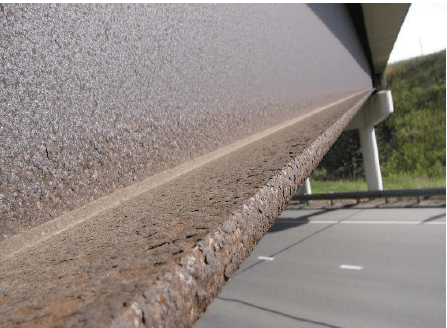
Diğer bir metot, görsel bir karşılaştırıcıya ve bir referans diske güvenmektir. Karşılaştırıcı, kullanıcının yüzey pürüzlülüğünü yakından incelemesini ve farklı derecelerde pürüzlülüğü (disk başına 5 segment) içeren master diskleriyle karşılaştırmasını sağlayan ışıklı bir büyüteçtir (tipik olarak 5-10x güçtür).
Kullanılan aşındırıcıyı (kum / cüruf veya shot) temsil eden uygun referans disk, hazırlanan çelik üzerine yerleştirilir ve kullanıcı, çeliğin yüzey profiline en yakın olan diski ve bölümü seçer.
Üçüncü metot, pürüzlü çelik üzerinde kullanılan (aynı aşındırıcı ve basınç ile ) aşındırıcı kumlama ile temizlenen bir tamamlayıcı çelik parçası olan test plakası üzerindeki yüzey profilini ölçmektir. Bu prosedür, demir döküm motor gövdelerini kaplamak için uzun yıllardan beri nükleer enerji endüstrisinde kabul edilmiştir.
Final olarak, kullanılan tip ve boyuttaki aşındırıcının ürettiği tipik yüzey profili değerlerine ilişkin olarak aşındırıcı üreticisine danışılabilir.
Bazı aşındırıcı üreticileri, belirli bir parti için ölçülen aralığı laboratuvar koşullarında belirten bir Uygunluk Sertifikası sağlayabilir. Yüzey sertliğinin yüzey profili derinliğini büyük ölçüde etkilediğine dikkat etmeliyiz, bu sebeple aşındırıcı üreticisinin verileri yanıltıcı olabilir.
Genel olarak bir yüzey de daha sayısal değer elde etmek için ASTM D 4417 Metod B ve Metod C yöntemleri tercih edilirken aynı proje de her ikisinin kullanılması bazı sorunlar yaratabilir.
Boya yüklenici enspektörü Metod B kullanırken, 3rd party enspektör Replica bant kullandığında her ikisi de ayrı sonuçlar bulduğunda sorunlar yaşanmaktadır. Peki hangi yöntem seçilmesi daha doğrudur?
ASTM D 4417 Yöntem B mi? Yoksa Yöntem C mi?
Endüstriyel ve koruyucu kaplama endüstrisinde, metal yüzeyler kimyasal olarak kazınmış, mekanik olarak öğütülmüş veya kumlanmış, diğer şeylerin yanı sıra, yüzey hatları yani profilleri oluşturulmuştur. Yüzey profili, kaplamanın yapışmasında anahtar rolü oynayan yüzey alanını arttırır.
Gerekli yüzey profili, kaplama üreticisi tarafından veya tüm kabul edilen kaplama özellikleri tarafından belirlenir. Yüzey profili vadi ve tepe arasındaki farkı kullanılarak belirlenir.
Yüzey profili özelliklere uymuyorsa ve çok büyük veya çok küçükse, kaplama hatalarına dolayısıyla korozyona neden olur. Bu yüzden yüzey profili çok önemlidir.
Yüzey profilini ölçmenin birçok yolu vardır ve hepsi farklı şekillerde çalışır. ASTM D 4417 standartlarına göre belirlenmiş üç yöntem bulunmaktadır. Bunlar;
• Yöntem A- Görsel karşılaştırıcı,
• Yöntem B- Derinlik mikrometre,
• Yöntem C- Replika bant.
Yöntem B ve Yöntem C yüzey profili ölçümünde yaygın olarak kullanılan iki yöntemdir.
Yöntem B
Derinlik mikrometre, derinlik mikrometresinin profil ölçüm prensibi vadi tepe arasındaki mesafeyi bir yaylı iğne yardımıyla ölçer.
Bir alanda ASTM D 4417-B standardına göre on okuma yapılır ve istatiksel ortalamasını alınır.
Yöntem C
Replika bant yöntemi, yüzeye sıkıştırılabilir bir köpük ped ile çoğaltma bandıyla birlikte uygulanır ve parlatma aletiyle ovalanır. Replika bandının yüzeye sürtünmesiyle, köpük aşağı doğru itilir, ters veya aynalı bir profil oluşturulur. Kopyalama bandı daha sonra çıkarılır ve bir kalınlık ölçer kullanılarak ölçülür.
Ne yazık ki, bu yöntem daha az doğrudur çünkü vadi tepe derinliğini kopyalayan bant bazı ölçüm noktalarını vadinin dibinden değil yamaçta bir yerde almış olabilir veya çizgisel hat aralıkları için aynı alanı birden fazla test etmeniz gerekebilir.
Yine de tamamıyla doğru ölçümler alınamayabilir ve az da olsa Yöntem B’ye göre daha öznel olma özelliğine sahiptir. Derinlik mikrometresi, cihazın tabanının altındaki potansiyel olarak yüzlerce “tepe noktası” ile ilişkili olarak tek bir vadi derinliğini ölçmektedir.
Tersine, replika bandı görüntüsü birçok tepe / vadiyi temsil eder, ve mikrometre elde edilenlerin bir kısmını ölçer (çoğaltma bandı üzerindeki test alanı yaklaşık 3/8” çapta ve mikrometrenin iğneleri yaklaşık 1/8” çapındadır).
Bu nedenle, mikrometre veya replika bandından okunması birkaç tepe noktasını ve vadileri temsil ederken derinlik mikrometresininki temsil etmemektedir.
Bu nedenle, özellikle daha derin yüzey profilleri ile farklılıklar kaçınılmazdır ve sonuçlar, iki yöntemden biri için belirtilen aralık içinde olabilir veya olmayabilir. Bu tutarsızlıkları önlemek için, bir projede tek bir yöntemin kullanılması kararlaştırılmalıdır.
Sonuç
Hatırlanması gereken önemli nokta, yüzey pürüzlü veya düzensiz olduğunda, bu profillerin bir veya daha fazlasının, yüzey profili derinliğini daha doğru bir şekilde belirlemek için kullanılabileceğidir.
Ayrıca, pürüzlü yüzeyler, korozyon korumasının sağlanmasına yardımcı olmak için daha kalın bir katın veya ek kaplama katmanlarının uygulanmasını gerektirebilir. Bu kararları verirken kaplama üreticisi devreye girmelidir.
Seda Ömercikoğlu Yüce - MICorr / Direktör - STM Coatech
Referans:
1) KTA University, Surface Profile Measurement Options on Rough/Pitted Steel Surfaces, Erişim Tarihi: 22 Kasım 2018, https://ktauniversity.com/surface-profile-pitted-steel-surfaces/
2) https://www.elcometerusa.com/Methods-For-The-Measurement-of-Surface-Profile-in-the-Field_2.pdf (son erişim tarihi ve saati: 28.11.2019 – 16:45)
3) https://kta.com/kta-university/surface-profile-astm-d4417/ (son erişim tarihi ve saati: 28.11.2019 – 16:45)