In this article, polyacrylate, known as, polyacrylic resins will be discussed. We can move on to its history by briefly talking about polyacrylates differences from other resins.
Acrylic resin (but not acrylic emulsion, is the basis of acrylic paint) is a thermoplastic, that is one of a group of plastics which can be heated and manipulated repeatedly, whereas polyester resin and epoxy are thermosetting plastics, used in heating or work as a catalyst
to solidify into a solid mass that won’t melt down.
Acrylic is mixed from acrylic polymer, a dry powder, a methyl methacrylate monomer, a thin liquid, and usually an organic peroxide hardener of some sort.
If pieces of any size are contemplated, an autoclave or hydraulic press is necessary for reducing air-bubbles and counteracting the internal stresses created by the strongly exothermic reaction. The dust is toxic, as is the monomer and its vapors.
The organic peroxides are especially poisonous, some of them being explosive
and others causing instant blindness if they get in ones eyes.
Acrylic resin has grown significantly in the solid surface manufacturing industry. It has several advantages; it can be heated, bent into shape, and cooled without any physical effect, making it more durable than polyester. Additionally, acrylic resin can hold up to heavier use.
When made with acrylic casting resin supplies, product seams are far more solid than products made with its polyester counterpart. However, acrylic casting material exhibits less visual depth and is more expensive than polyester. Still, its advantages give more value to your money.
When you look into real-life applications, acrylic resins provide for better adhesion than other products commercially available. For superb product outcomes, water-based acrylic polymers are the smartest choice.
Acrylic resins are used everywhere: brake lights, car tires, dentures, phone screens, art and sculptures, and even theming and decorations.
History
To extend on Polyacrylate also known as polyacrylic resin, in 1873 Caspay and Tollens have discovered acryl acid alkyl ester.
German chemist Otto Rohm who published a research on methacrylic acid methyl ester, in 1915 he had been granted a German patent for the use of the solution of acrylic acid ester in acetone, as a varnish and binder instead of drying oils in paint, for the purpose of impregnation in wood and similar materials. This approach, which Otto Röhm predicted for acrylic acid at that time, still sheds light on today’s technology.
The products obtained by the polymerization of acrylic acid and methacrylic acid esters are named differently. Even though we call it as acryl resin or acrylic resin, when Phenol, Melamine and Ketone Resins are taken into consideration, it seems more correct to say that
acrylic and methacrylic acid polymers, which are polymerization products, are polyacrylic or poly acrylate due to their high molecular structure. Polymers of ester, nitrile and amidine of acryl and methacrylic acid are also included in this group.
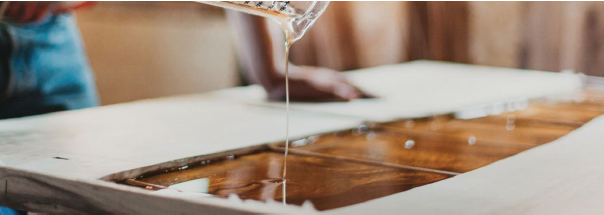
Polyacrylates used as resins in the paint industry have a much lower molecular length than polyacrylate-plastics used in the plastics industry. Therefore, although poly and resin remind of high molecular structure, it would be more accurate to say “polyacrylate resins”
for those used in paint and “polyacrylates” for those used in the plastics industry. The molecular weight of polyacrylic resins used in paint is up to 200,000, while plastic-polyacrylates are 1,000,000 and above.
Since we are focusing on paint technology, Polyacrylic resins can be break down into two main groups.
• Thermoplastic, physically drying polyacrylic resins that do not contain functional groups and therefore do not cross-link.
• Cross-links containing functional groups (such as -COOH, -CONH2, -CONH, -CH2OH, -CONHCH2OR) and Termosettıng are polyacrylic resins. The two main groups are explained in more detail as follows.
Thermoplastic Polyacrylate Resins
Thermoplastic polyacrylate resins are used as paint binders. The small amount of acrylic and/or methacrylic acid in their composition creates the appropriate polarity that provides remarkable adhesion to the ground (especially on metals), as well as increasing pigment wetting.
Thermoplastic acrylic resins are better than other binders with their hardness and solubility, which we call mechanical properties along with the best lightfastness. Same feature is also valid for the thermosetting group.
However, it should be noted that the addition of styrene will reduce light fastness. Another feature is their excellent chemical resistance, especially when the acid content increased in application to metal surfaces. Their resistance to alkalis is high, but we cannot say the same for organic acids.
The pigment wetting and dispersion properties of thermoplastics are mediocre. Nevertheless, wetting can be increased by adding a small amount of plasticizer or another resin. Generally, they are incompatible with alkyds.
Thermoplastic polymethacrylates used in a wide variety of applications, especially poly-n-butylmethacrylates, are used in the food industry, packaging industry (heat-seal), lacquers and inks.
In addition to this, their usage in printing inks, adhesives, auto repair paints, industrial and marine paints, construction sector, has been increasing day by day. It provides perfect bond between plaster and concrete.
Thermosetting Polyacrylate Resins
Thermosetting Polyacrylate resins forms a network structure and hardens, with increasing temperature and polycondensation reaction. This network structure gives the system excellent film stiffness, very good atmospheric and chemical resistance.
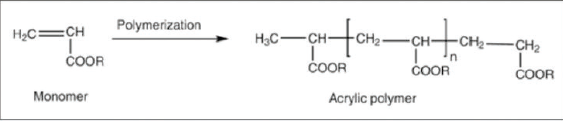
Thermosettings show much better adhesion than thermoplastics. In this type of resin, network formation occurs either between the molecules of the resin itself or between the molecules of the resin and the molecules of the reaction partner. The most ideal, is the use of melamine formaldehyde resins.
By attaching the functional groups, that I have written below, to the polyacrylate molecule, we can obtain polyacrylate resins with different functions.
Epoxy-amine-amide-anhydride-hydroxyl-methylisocyanate
Thermosetting polyacrylic resins are used in auto topcoat paints as well as in white goods coating due to their excellent chemical resistance and high pigment binding function. Usually, the reaction partners are melamine. If epoxy resin was added into this, adhesion
and chemical resistance would increase even more.
I would also like to mention the network structure with polysocyanates in addition to the identification of our resins. It forms excellent paint films as a result of the curing of acrylic resins containing hydroxyl groups with a suitable isocyanate at room temperature by chemical reaction (polyaddition). These films, also called Polyacryl Urethanes, have very high alkali and detergent resistance.
Polyacryurethanes show exceptional corrosion resistance in the salt spray (pure spray) test. Also, It is very resistant to gasoline and hydraulic oils. The most used areas are auto repair paints and special metallic paints.
Last but not least, Polyacrylic paints, which have a network structure with isocyanate, show similar performance to oven paints even though they are air-drying.
Nigar Cangönül
Technical Sales Manager
Günkem