Phosphating
During phosphating, poorly soluble metal phosphate layers are formed on metal surfaces, which are porous, absorbent and firmly anchored to the base metal. The phosphate layers consist of a mixture of secondary and tertiary phosphates of the metal contained in the phosphating solution (zinc, manganese, iron) and the treated base metal (iron, zinc, cadmium, aluminum).
Phosphating is most often performed on steel. The crystal structure of phosphates corresponds approximately to that of the minerals hopeite, phosphophyllite vivianite. Stainless steels are oxalated (metal oxalates are formed by treatment with oxalic acid), since phosphating is not possible due to their resistance to phosphoric acid.
In surface engineering, both conventional processes and special processes are used (Figure 1). Conventional processes are most commonly used, such as layer-forming processes, in
which zinc, manganese or iron phosphates are used, and non-layer-forming processes, in which alkali phosphates are produced.
Phosphate coatings improve the service properties of workpieces. They provide temporary corrosion protection, reduce the coefficient of friction, form a good adhesion base for organic coatings and have an electrically insulating effect. For temporary corrosion
protection of components for storage or transport, layer-forming phosphate coatings with subsequent passivation are used.
[caption id="attachment_140630" align="alignnone" width="300"]
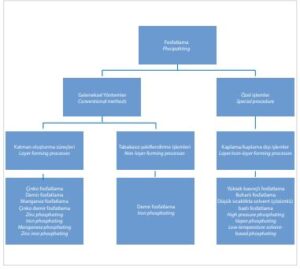
Figure 1. Classification of phosphating processes[/caption]
The coating weight is up to 15 g/m2 (corresponding to a thickness of about 5.5 µm) on steel and up to 4 g/m2 (about 1.6 µm) on electrodeposited zinc or cadmium coatings. Nonlayer-forming processes are only used for very short storage times and for immediate, subsequent coating.
Phosphate coatings with a coating weight of 40 g/m2 (thickness about 15 µm) and post-treatment with a special rust preventive oil or wax provide similar corrosion protection properties as chromated zinc coatings. Both layer-forming and non-layer-forming processes are used to improve the corrosion resistance and adhesion of paint layers and plastic films. The porosity of the phosphate layer and the roughened surface provide good mechanical
anchorage for a subsequent organic layer. The layer weight is between 0.3 and 6.0 g/m2.
An overview of phosphating processes for pretreatment prior to painting and use as a
sliding layer is shown in Table 1. Phosphate coatings also serve as lubricant carriers to facilitate non-cutting deformation, e.g. during deep drawing of parts from sheet metal, wire drawing, tube drawing or extrusion. After phosphating, the surface to be formed is immersed in a soap solution, and metal soaps are formed by a chemical reaction.
The firmly adhering lubricating film reduces the interfacial friction between the die and workpiece surfaces and remains effective throughout the forming process. This ensures higher forming degrees and speeds, longer die service life and better surface quality. The coating weights are between 2 and 20 g/m2 (corresponding to approx. 0.8 to 7 µm).
[caption id="attachment_140632" align="aligncenter" width="664"]
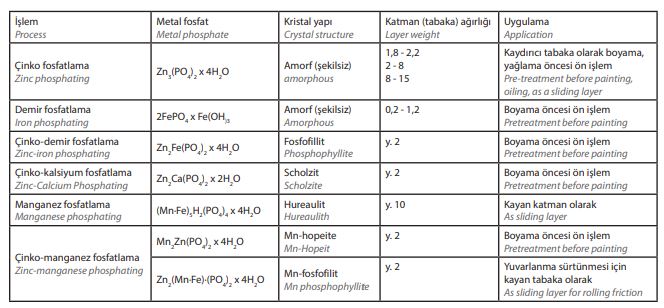
Table 1: Overview of phosphating processes[/caption]
In cutting tools, wear can be significantly reduced by phosphating the surface. The effect is probably due to improved chip flow. The insulating properties of the coatings are mainly
used for transformer sheets, which are phosphated in a continuous process.
1. Conventional Methods
1.1 Layer Forming Phosphating
Layer-forming phosphating solutions usually contain a soluble primary metal phosphate (zinc, manganese or iron phosphates), free phosphoric acid and usually an oxidizing agent
as an accelerator. During phosphating, the primary dihydrogen phosphates form more difficult to dissolve secondary hydrogen phosphates and finally practically insoluble tertiary
phosphates:

The reaction is triggered by the initial pickling effect of the phosphoric acid on the iron in the case of steel sheets or on the zinc in the case of galvanized sheets:

The consumption of phosphoric acid shifts the equilibria to the right and leads to the formation of the insoluble phosphates. These form phosphate crystals at crystallization nuclei on the surface, which are oriented according to the crystal lattice of the metal.
Through further crystal growth and covering of the surface, a phosphate layer is formed, which protects the base metal from further attack by the acid when a sufficient layer
thickness is reached. Phosphated zinc surfaces exhibit a light to dark gray coloration.
Zinc-based phosphating solutions contain zinc orthophosphates and free phosphoric acid. Typical zinc contents are 5 to 20 g/l. The treatment times for dipping are 30 to 60 minutes,
and the achievable coating weights are 30 to 50 g/m2.
The working temperature ranges from 70 to 90 cc. The result of the layer-forming
phosphating process depends on (Figure 2):
[caption id="attachment_140642" align="aligncenter" width="360"]
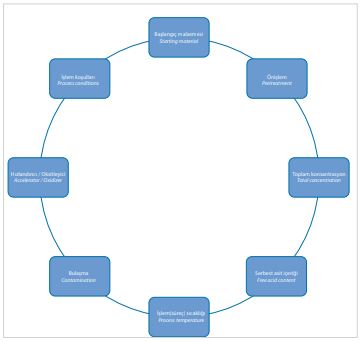
Figure 2: Factors influencing the phosphating process[/caption]
The rate of formation of phosphate layers increases by in creasing the concentration of the solution, decreasing the amount of free phosphoric acid, increasing the temperature of
the solution and by the addition of oxidizing agents. The layer thickness and crystal size depend on the surface condition of the base material before phosphating.
Thicker and more coarsely crystalline layers are formed on rough surfaces than on smooth metal surfaces. Inhomogeneous phosphate layers can result from impurities in the base material or from rolling defects. Another source of defects is insufficient cleaning of the parts to be phosphated. The greatest source of defects is the actual phosphating process. Monitoring of the process parameters is therefore of particular importance.
The higher the total concentration of dissolved salts in the solution, the more insoluble phosphates are formed, i.e. the faster the phosphate layer is formed. The content of free phos phoric acid is decisive for the dissolution reaction. The higher the proportion of free acid, the greater the pickling attack. On the one hand, the acid attack produces a bright metallic surface, and on the other hand, the surface is roughened, which promotes the adhesion of the phosphate coatings.
Constant monitoring is therefore necessary. The impurities introduced into the phosphating solution due to insufficient pretreatment adversely affect phosphating. Foreign substances enriched in the solution, such as sodium, calcium and magnesium, are incorporated into the phosphate layers. Excessive contents of grease/oil, chloride and sludge can also be detrimental to the layer structure. The process temperature for phosphating is approximately 90°C. If oxidizing agents are used, the temperature of the phosphating solution may be reduced.
The use of accelerators or oxidizing agents leads to a shift in the chemical equilibrium and an increase in the reaction rate. This results in more uniform phosphate layers and the working temperature can be lowered to 35 to 60°C. The phosphating result is strongly dependent on the choice of oxidizing agent.
The additives also contribute to the reduction of pickle removal. In the process, the divalent iron is oxidized to the trivalent, resulting in very poorly soluble iron(III) phosphate, which precipitates as sludge.
The main oxidizing agents are:
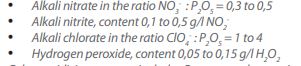
Other oxidizing agents include. Borates and organic nitro compounds.
The type of accelerator determines the growth of the phosphate layer and its structure. For example, phosphate layers deposited from nitrite-accelerated phosphating solutions are
fine crystalline and show good coverage even at low thickness. When choosing a phosphating agent, these relationships must be taken into account in the decision to ensure that the quality requirements for the phosphate layers are met.
Phosphating can be carried out by dipping, spraying or rollcoating - that is, applying measured quantities of liquid. The phosphating result depends primarily on the exchange conditions in the solution in the immediate vicinity of the surface, i.e. the boundary layer. In the immersion process, the exchange can be improved by intensifying the circulation.
Care must be taken to avoid supersaturation; for this reason, in practice, a procedural compromise must be found between the agitation of the solution and the concentration. Using vibration and ultrasound, particularly fine-grained layers are formed.
A further reduction in reaction time is achieved by using spray technology. The surface to be treated is continuously supplied with fresh phosphating solution, resulting in the formation of closed phosphate layers in a relatively short time. The acceleration of the process is due to the turbulent mass transfer in the boundary layer and the resulting increased diffusion rate.
Cold-rolled strip can be phosphated in a continuous process by spraying or by application with a rotating roller in the socalled roller application or roll coat process. In the roller application process, selective, one-sided coating is possible. Compared with the spray process, this method requires less space and offers advantages in terms of maintenance, process control and preparation of the phosphating solution.
In conventional zinc phosphating, the basis weight of the applied coating is usually 5 to 20 g/m2. The phosphating solution contains approximately 12.2% zinc, 22.5% phosphorus pentoxide and 15.6% nitrate. The density of the solution is 1.6 g/ cm3.
1.2. Non-layer-forming Phosphatization
In the non-layer-forming processes, the phosphating solutions contain alkali phosphates which react with the base metal. Very thin layers are formed (layer weights between 0.2 and 2.0 g/m2). The anion PO43- involved in the phosphating reaction is supplied in the form of the alkali hydrogen phosphate, and the cation is supplied by the metal to be coated itself. Because of the iron phosphate content, this is also referred to as iron phosphating, which is of great importance in practice for optimum adhesion of paints or powder coatings.
The pickling reaction is much slower at pH 3.5 to 6 than in zinc phosphating:
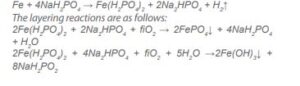
The layers formed contain a mixture of tertiary iron(III) phosphate and iron(III) hydroxide. The crystal structure of the layer has the same orientation as that of the base material.
The iron-phosphated metal surfaces exhibit a bluish iridescent coloration. The process solutions for non-layer forming phosphating work with concentrations of 2 to 20 g/l NaH2
P04 at temperatures around 70°C.
The pH is corrected by adding phosphoric acid, acidic alkyl phosphate ester or acidic alkyl
phosphonium salts The addition of oxidizing agents accelerates film formation, increases adhesion and improves functional properties. Alkali chlorates, nitrates, nitrites or bromates
are used as accelerators.
2. Special Procedure
The special processes include phosphating using the highpressure or steam-jet process and low-temperature solventbased phosphating. In the high-pressure and steam-blasting processes, cleaning and phosphating are combined in one combined in a single stage. In terms of plant engineering, this is easy to implement, especially for large-area parts or
for phosphating in small batches.
Neither process offers any particular advantages over conventional techniques, since the
specified exposure times for pretreatment and phosphating must be observed. In organic phosphating, the protective layer consists of a passive and amorphous phosphate layer covered with a thin film of phosphate polymer. The process conditions must be strictly observed.
References
• Die Phosphatierung von Metallen, Eugen G. Leuze.
• Technologie der Galvanotechnik, Eugen G. Leuze.
• Phosphatieren, Oxalatieren, Merkblatt 166,Stahlanwendung
İzzet Aydın
General Manager
Hillebrand Chemicals Kimyasal Pazarlama Ltd. Şti.