Özet
Otomatik Fiber Serme (AFP) yöntemi fiberlerin yönelmeli olarak çeşitli üretim sınırlamaları ile serildiği yenilikçi bir fiber takviyeli kompozit üretim yöntemi olarak kullanılmaktadır.
Bu yöntem fiber açılarının bir lamina katmanında değiştirilerek serilmesine izin vererek, sabit rijitlikte
kompozitlerde olduğu gibi istiflenme dizilimlerinin belirlenmesine ilave olarak bir esneklik sağlamakta ve sabit rijitlikteki yapılara göre daha iyi performans veren optimum çözümlere olanak sağlamaktadır.
Bu çalışmada AFP yöntemi ve üretim sınırlamalarına uygun olarak tasarım yapabilmek için yenilikçi bir sonlu eleman yöntemi geliştirilmiştir.
Önerilen yöntem farklı sınır şartlarına sahip plakalar üzerinde test edilmiş ve üretim sınırlamaları uygun olarak fiber dağılımı bulunmuştur. Optimizasyon sonuçları literatürdeki çalışmalar ile tutarlı ve bazı durumlar için daha iyi sonuçlar verdiği bulunmuştur.
Giriş
Fiber takviyeli kompozit malzemeler üretmek için “Otomatik Fiber Yerleştirme” (AFP) yöntemi kullanılmaktadır. Elyaf takviyeli kompozitler, metallere kıyasla daha yüksek sertlik/ağırlık oranlarına sahip olduklarından fiber takviyeli kompozit malzemeler metalik malzemelere bir alternatif haline gelmiştir [1].
AFP metodu havacılık endüstrisinde kritik havacılık parçalarının imalatında kullanılmaktadır. AFP yöntemi insan emeğini azaltan ve kompozit üretim işleminin tekrarlanabilirliğini artıran üretim otomasyonu sağlaması sebebiyle geleneksel kompozit üretim yötemlerine kıyasla daha cazip bir üretim yöntemi olmaktadır.
Şekil 1. Otomatik Fiber Serme (AFP) yöntemi ile fiber takviyeli kompozit serimi [2]
Şekil 1 AFP işlemi ile üretim yapan bir robot manipülatörü göstermektedir [2]. Tow pre-preg malzeme bir kızılötesi ısıtıcı ile ısıtılır ve akabinde kalıbın üzerine yapışmak için bir sıkıştırma silindiri ile kalıba bastırılır. Bu yöntem için fiber yönleri sınırlı bir eğrilik yarıçapından büyük olmak üzere istenildiği doğrultuda kalıba serilebilir [3, 4].
Şekil 2. Kompozit bir laminatta farklı lamina katmanlarının örnek istifleme dizisi
Şekil 2, lamina katmanlarının birbiri üzerine istiflendiği bir örnek istifleme dizisini göstermektedir. Sabit rijitlik, bileşik bir parça boyunca aynı kalan rijitlik anlamına gelir.
Örneğin, lamina tabakalarının istiflenme dizisi ve tabaka kalınlıkları parça boyunca aynı alırsa, o kısmın sertliği sabit kalır.
Önceki çalışmaların birçoğu, sabit sertlikte kompozit laminatların döşeme sırasının belirlenerek tasarımlarına odaklanmaktadır.
Sabit rijitlikli kompozitlerin tasarımı için önemli miktarda araştırma yapılmıştır. Bu çalışmalarda rijitlik, ilk burkulma frekansı, arıza yükü gibi farklı hedef fonksiyonları kullanılmıştır.
Şekil 3. Gürdal ve Olmedo [5]’ kullandığı iki bağımsız parametre; T0 ve T1 ile tanımlanan lineer değişen spline eğrisi
Günümüze daha yakın olan çalışmalar, AFP üretim yöntemi ticari olarak hazır hale geldikten sonra değişken sertlik tasarımına odaklanmıştır.
Buradaki problem, verilen performans gereksinimleri için en iyi fiber yönlerini ve bunların istiflenme dizilimlerini bulmaktır. Gurdal ve Olmedo, fiber açılarının tanımlanması için doğrusal olarak değişen bir spline önermiştir [5].
Benzer çalışmalar, B-spline’ları ve NURBS fonksiyonlarını kullanarak spline’ların aynı kavram tanımını kullanmıştır [6, 7].
Fiberlerin sürekliliği ve fiberin yönlendirebileceği minimum eğrilik yarıçapı gibi üretim sınırlamaları vardır. Son çalışmalar, imalat kısıtlarını göz önünde bulundurarak en iyi fiber yönlerini bulmayı amaçlamaktadır [8].
Tasarım Yöntemi
Tasarım yöntemi sonlu elemanlar modelinden, optimizasyon yönteminden ve üretilebilir fiber açılarını bulmak için yeni bir tasarım yöntemi geliştirilmiştir.
Bu yöntem optimizasyon metodu içerisinde sonlu eleman analizlerini kullanmaktadır. Laminasyon parametrelerini kullanmaktadır.
Klasik laminat teorisi MATLAB®’da uygulanmaktadır. Bu, optimizasyonu sayısal verimlilik için sonlu elemanlar ortamı ile aynı ortamda gerçekleştirmek için gereklidir.
Laminasyon Parametreleri, optimizasyonu dışbükey bir soruna dönüştürmek için kullanılır. Örnek olarak Denklem (1)’de, düzlem içi laminasyon parametresi vektörü, {ξ
A}, lamine tabakaların kalınlık koordinatlarının, z
k,z
k+1, bξir fonksiyonu olarak, laminatın toplam kalınlığı, t, N adet lamina tabakalarının toplamı için gösterilmiştir. “k” lamina katmanının fiber açıları, θk ile ifade edilmiştir.

Düzlem dışı laminasyon parametreleri, {ξ
D}, ise kalınlık koordinatının küpü ile orantılıdır.

Optimizasyon, Denklem (3)’te gösterildiği gibi, maksimum rijitliği yani minimum gerinim enerjisini bulmayı amaçlar. Optimum fiber açılarını bulmak için MATLAB® optimizasyon toolbox’ının “fmincon” fonksiyonu kullanılmıştır.

Gerinim enerjisi, R, global sonlu eleman deplasmanları, {d}, global rijitlik matrisini, [K], kullanarak bulunur. Bu iki özellik fiber dağılımının fonksiyonudur ve optimizasyon süresince değişmektedir.

Optimizasyon sonrasında laminasyon parametreleri, her bir sonlu elemanın merkezinde belirlenmiş olur ve doğrudan arama yöntem ile fiber açılarına ve katman dizilimlerine dönüştürülür.
Üretilebilirlik, elyaf açılarının sürekli olmasını ve eğriliklerin maksimum bir eğrilik sınırı içinde olmasını gerektirir. Bunu başarmak için, fiber açılarını alan değişkenleri olarak da tedavi ettik. Daha sonra, optimum çözüme en yakın ve bu kısıtlamaları sağlayan elyaf açılarını aradık. Yöntemin detayları referansta [9] bulunabilir.
Sonuçlar ve Çıkarımlar
Geliştirilen yöntem üç farklı sınır şartı ve yük durumu için test edildi. Şekil 4’te üç farklı sınır şartı gösterilmektedir. Bu çalışmada Ly uzunluğu birim olarak kabul edilmiştir.
Şekil 4. Yöntemin testlerinde kullanılan sınır şartları
Şekil 5 basit mesnetli plaka için optimizasyon sonrasında elde edilen laminasyon parametrelerinin dağılımını göstermektedir.Laminasyon parametresi dört bileşenden oluştuğu için dört ayrı şekil ile plaka üzerindeki dağılımları gösterilmiştir.
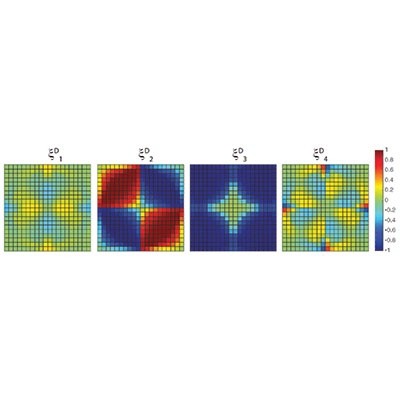
Şekil 5. Basit mesnetli e basınç yüklü plaka için optimum laminasyon parametrelerinin dağılımı
Bulunan en iyi laminasyon parametreleri direkt arama yöntemi ile açılara ve dizilimlere dönüştürülmektdir. Şekil 6, düzlem dışı basınç ile basitçe desteklenen plaka için fiber dağılımlarının sonuçları göstermektedir.
Şekil 6a./6b. Optimizasyon sonrası elde edilen açılar
Şekil 6.a’da optimizasyon sonrası elde edilen açılar gösterilmektedir. Şekil 6.b’de ise üretim sınırlamalarına uygun olarak elde edilen açılar gösterilmektedir. Dikkatli bakılırsa, fiber açıları sürekli bir dağılım göstermektedir. Aynı zamanda bir penaltı parametresi ile eğrilik değerleri sınırlanmıştır.
Şekil 7a./7b. Penaltı faktörleri için elemental eğrilik
Penaltı değeri tanımlanan en yüksek elemental eğrilik değerini (maks. κ
el) kullanarak bulunmuştur. Bu çalışmada maks. κ
el5m-
1 olarak kabul edilmiştir. Şekil 7.a’da gösterildiği gibi çeşitli penaltı faktörleri için elemental eğrilik hesaplanmış ve istenilen değeri sağlayan penaltı faktörü 0.0176 olarak bulunmuştur. Fiber açılarına uygulandığında Şekil 7.b’deki en yüksek eğrilik değerinin 5 m-1 olduğu gözükmektedir.
Tablo 1, farklı geometrilere uygunluktaki genel sonuçları ve gelişmeleri göstermektedir. Önerilen çözüm, aynı problem için literatürdeki bulgular ile tutarlı [10] hatta bir çok durum için daha da iyi sonuçlar vermektedir.
Tablo 1. Üç farklı sınır koşulu türü için optimizasyon sonuçları ve sonucun referans ile karşılaştırılması [10]. Konsol plakası için normalize edilmiş uyum, R, aşağıdaki ilişki ile verilmektedir: R= E
22 t L
3 y R /(p
2 L
5 x), basit mesnetli ve sabit plaka, R=E
22 t
3 R/ (p
2 L
5 )x100 konsol kiriş sınır şartları için kullanıldı.
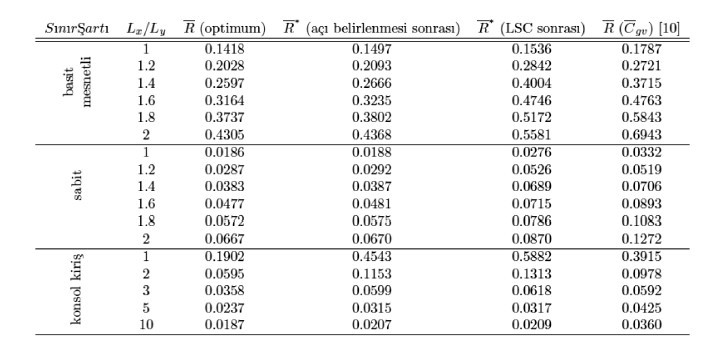
Önerilen yöntem aşağıdaki avantajları getirmiştir:
• Oldukça basit ve etkili bir hesaplama yöntemi ile optimum fiber açılarının ve lamina dizilimlerinin bulunması,
• Fiber sürekliliği ve eğrilik yarıçapı ile ilgili üretim sınırlamalarını dikkate alınması,
• Birçok durum için literatürden daha iyi optimum çözümlerin bulunması.
İleriki çalışmalarda kesintili açıların sürekli fonksiyonlar ile takım yollarının belirleneceği spline fonksiyonlara çevrilmesi, deneysel uygulamalar ve üretimler, kabuk tipi elemanlar ile gerçek parça geometrisinin modellenmesi yapılacaktır.
Dr. Öğretim Üyesi Eralp Demir
Sabancı Üniversitesi
Mühendislik ve Doğa Bilimleri Fakültesi
Mekatronik Bölümü
Referanslar
[1] Albazzan, M. A., Harik, R., Tatting, B. F. & Gürdal, Z. Efficient design optimization of nonconventional laminated composites using lamination parameters: A state of the art. Compos. Struct. 209, 362–374 (2019).
[2] http://www.materialsforengineering.co.uk/engineering- materials-features/weaving-the-future/111265/
[3] B. Denkena, C. Schmidt, P. Weber, Automated fiber placement head for manufacturing of innovative aerospace stiffening structures, Procedia Manufacturing 6, 96-104 (2016).
[4] D. M. Peeters, G. G. Lozano, M. M. Abdalla, Effect of steering limit constraints on the performance of variable stiffness laminates, Computers and Structures 196, 94-111 (2018).
[5] Gürdal, Z.&Olmedo, R. In-Plane Response of Laminates with Spatially Varying Fiber Orientations: Variable Stiffness Concept. AIAA J. 31 (1993).
[6] Montemurro, M.&Catapano, A. On the effective integration of manufacturability constraints within the multi-scale methodology for designing variable angletow laminates. Compos. Struct. 161, 145–159 (2017).
[7] Wu, Z., Raju, G.&Weaver, P. M. Framework for the Buckling Optimization of Variable-Angle Tow Composite Plates. AIAA J. 53, 3788–3804 (2015).
[8] Peeters, D. M. J., Lozano, G. G.&Abdalla, M. M. Effect of steering limit constraints on the performance of variable stiffness laminates. Comput. Struct. 196, 94–111 (2018).
[9] E. Demir, P. Yousefi-Louyeh, M. Yildiz, Design of variable stiffness composite structures using lamination parameters with fiber steering constraint, Composites Part B: Engineering 165, 733-746 (2019).
[10] S. Setoodeh, M. M. Abdalla, Z. Gürdal, Design of variable stiffness laminates using lamination parameters, Composites Part B: Engineering 37 (4), 301-309 (2006).