1. Giriş
Öğütme işlemi kristal ya da amorf yapı içindeki kimyasal bağların kopması ile yeni yüzeylerin oluşması işlemidir. Öğütme tesislerinde öğütücü ekipmanlara (değirmen) iletilen enerjinin ancak %1’i yeni yüzey oluşumunda harcanmakta, %99’u ise iletim kayıpları, sürtünme, ısı, ses gibi enerjiler biçiminde tüketilmektedir.
Cevher hazırlama tesislerinde kullanılan enerjinin ise yaklaşık %50’si öğütme devrelerinde harcanmaktadır. Bu nedenle proses maliyetlerinin düşürülmesinde öğütücü maliyetleri öğütme verimliliği bakımından önem taşımaktadır.
Öte yandan, mineral endüstrisi, boya, plastik, ilaç, kâğıt gibi çeşitli endüstriyel alanlarda süper ince/nano partikül boyutlu tozlara olan taleplerdeki artış, yaş yöntemle çok ince öğütmenin giderek artan bir şekilde uygulanmasını beraberinde getirmektedir.
Çok ince öğütmede kullanılan ekipmanlar ise genellikle karıştırmalı (yatay/dik) değirmenlerdir. Karıştırmalı değirmenler çok ince ve mikron altı/nano partikül boyutu elde edilmesinde diğer değirmenlere göre önemli avantajlar sağlamaktadır.
Bu tür değirmenlerde öğütülecek malzemeye göre çeşitli malzemelerden üretilmiş çok farklı bilyeler (boncuk) kullanılmaktadır. Bu bilyeler genellikle şu şekilde sınıflandırılabilir:
• Plastik,
• Silika,
• Alümina,
• Zirkonyum silika,
• Zirkonyum oksit,
• Çelik,
• Diğer.
Öğütmede kullanılan bilyelerin genel özellikleri Tablo 1’de verilmektedir. Buna göre kaba yoğunlukları 0.63-8.2 kg/l, gerçek yoğunlukları 1.05-15 ve renkleri ise genellikle beyaz, sarı, gri ve gümüş renklerde olmaktadır.
Bilye sınıflarına göre; plastik bilyeler 1.2 g/ cc, silika bilyeler 2.6 g/cc, alümina bilyeler 4.2 g/cc, zirkonyum oksit bilyeler 6 g/cc, çelik bilyeler 7.6 g/cc ve tungsten karpit bilyeler 15 g/cc gerçek yoğunluğa ulaşabilmektedir.
Tablo 1. Bilye (boncuk) türü ve özellikleri
(a) polyester (b) poliamid (c) polikarbonat (d) kum (e) soda kireç cam (f) kalıplanmış soda
kireç cam (g) standart alümina (h) yüksek saflıkta alümina (i) zirkonyum silika (j) magnezyumlu
zirkonyum oksit (k) seryumlu zirkonyum oksit (l) yttria zirkonyum oksit (m) paslanmaz çelik (n)
tungten karpit
Şekil 1. Çeşitli bilye (boncuk) görünümleri
Aşağıda öğütücü ortam olarak kullanılan bazı bilyelerin ayrıntılı özellikleri yer almaktadır:
Polyester: Aşındırıcı olmayan, küresel şekillidir. 100 mikrona kadar küçük boyutlarda üretilebilir. Yoğunluğu düşük ama sert ve aşınmaya karşı dirençlidir. Gözenekli, sertleştirilmiş ve dar boyut dağılımlarında da bulunur.
Poliüretan: Tozların karıştırılması ve harmanlanması için kullanılan yüksek yoğunluklu bilyelerdir. Çok uzun aşınma sürelerine imkân verir. En küçük boyutu 4-5 mm’dir.
Kum: Düşük fiyatı nedeniyle hala kullanılmaktadır ancak uzun vadede maliyetli olabilir. Düzensiz şeklinden dolayı değirmeni aşındırır çünkü küreye oranla daha iğnemsi olup uç kısımları kopmaya meyillidir. Alternatifi ise; cam ve mullittir.
Soda kireç cam: Öğütücü ortam olarak kullanılan en popüler cam küredir. Bazı türler saf camdan üretilirken bazıları geri dönüşüm camdan üretilmektedir. Hava kapanımları da boncuğun dayanımını belirlediği için bilye ömrünü belirleyebilen değişkenlik göstermektedir. Düşük viskoziteli malzemeler veya düşük ısıl işlemler için mükemmel bir bilyedir.
Düşük alkali / Borosilikat cam: Borosilikat cam bilyelerin çeşitli kaliteleri vardır. Düşük alkali uygulamalar için olduğu kadar gıda ve ilaç için de kullanılır. Ayrıca, soda kireç camından daha fazla aşınmaya dirençli olan yüksek bir ezilme kuvveti (crush strength) bulunmaktadır. Soda kireç camından daha pahalıdır, ancak daha değerlidir. Borosilikat cam da mevcuttur ancak son derece pahalıdır.
Çakıl taşı: Doğal haliyle bulunması gittikçe zorlaşan bir kaynaktır. Temel olarak kuvarsa benzer bir yoğunluğa sahiptir ancak düzensiz şekiller ve yüzeylerle sertleşmiştir.Çakılın avantajı en-boy oranıdır, böylece değirmende temas için daha fazla yüzey alanı verir. Kullanılabilir ancak pahalı hale gelmektedir.
Steatit: Bu öğütücü ortam, %62 SiO2’den oluşan erimiş bir magnezyum silikat bileşimidir. Silindir ve küre şekilli olup minimum boyutu 6 mm’dir. Çakıl taşlarına veya büyük cam bilyelere mükemmel bir alternatiftir. Aynı yoğunluğa sahip olmasına karşın camdan daha uzun süre dayanır.
Mullit: Bu bilye yaklaşık %35 SiO2 içerir. Camdan daha fazla ve diğer alüminalardan daha düşük yoğunluğa sahip olma avantajına sahiptir. Bilyeler, boksitle veya boksitsiz çeşitli alümina oranlarında ve yoğunluklarda üretilebilir. Cam bilyeden daha uzun süre dayanır ve diğer alümina bilyeler kadar aşındırıcı değildir.
Standart alümina: Hem tozlarda hem de sıvılarda partikül boyutunun düşürülmesi için kullanılan en yaygın alümina öğütücü ortamdır. Bazı boyutlar hem kuru preslenmiş hem de sıkıştırılmış olarak mevcuttur. Bilyeler aşındırıcı olabilir.
Yüksek yoğunluklu alümina: Yoğunluğu daha yüksektir, bu nedenle kullanmadan önce astar sertliği düşünülmelidir. %93’lük alümina bilyeler küresel olup hem sıvılarda hem de tozda kullanım için mükemmeldir.
Yüksek saflıkta alümina: Daha yüksek saflığa sahip alümina, alüminadan başka kontaminasyonu tolere edemeyen öğütme malzemelerinde kullanılır. Çok daha pahalı olabilir ve diğer alümina formülasyonlarına kıyasla daha kırılgan olabilir. Küre ve silindir şekilli olabilir.
Zirkonyum silikat: Orta yoğunluklu, sinterlenmiş popüler bir bilyedir. Sert bir dış kabuğa ve yumuşak bir iç çekirdeğe sahiptir.
3 mm üzerindeki boyutlar, bilyeyi zayıflatan ve çatlamasına/kopmasına neden olan doğal yapısı nedeniyle pratik değildir.
Değirmende aşındırıcı olabilir.
Zirkonyum silika: Zirkonyum silikat ile hemen hemen aynı görünen popüler bir orta yoğunluklu bilyedir. Bu bilye ergitilmiştir (fused) ve kabuğundan çekirdeğe kadar homojendir. Sinterlenmiş bir bilyeden daha uzun süre kullanılır ancak boşluk olarak bilinen iç hava kapanımları nedeniyle 2 mm üzerindeki boyutlarda kullanılmamalıdır. Kırılabilir ve değirmende aşınma problemlerine neden olabilir.
Yüksek yoğunluklu zirkonyum silika: Daha yaygın olan formülasyona kıyasla daha yüksek miktarda zirkonya içeren ergitilmiş bir zirkonya silisidir. Mükemmel bir performansa ve değere sahiptir.
Magnezyumlu zirkonyum oksit: Her türlü öğütme için çok popüler yüksek yoğunluklu ve silindir şekilli bir seramik bilyedir.
Seryumlu zirkonyum oksit: Yüksek yoğunluklu seramik bilyedir. Dayanıklılık ve değer fiyatlaması nedeniyle çok popülerdir. Çatlamaz ve kırılmaz. Silindir ve küre şeklinde bulunmaktadır.
Yttria zirkonyum oksit: Bu, en yüksek yoğunluğa sahip, en uzun ömürlü ve en dayanıklı öğütücü ortamdır. Çok sert ve gözeneksizdir, böylelikle kırılmaz. Küre ve silindir şekilli olup çok çeşitli ebatlarda üretilir.
Paslanmaz çelik: Bu bilyeler pahalı olabilir ancak genellikle diğer tür bilyeler kabul edilemez olduğunda kullanılır.
Tungten karpit: Yüksek yoğunluğu nedeniyle ilgi çekmeye devam etmektedir. Bu öğütücü ortamı kullanan değirmenler yüksek yoğunluğa karşı dayanıklı olacak şekilde imal edilmelidir. Küresel olanlar oldukça pahalıdır.
2.En Uygun Bilye Nasıl Seçilir?
i. Kimyasal uyumluluk: Öğütücü ortam herhangi bir kimyasal kirlenme (kontaminasyon) sorununu ortaya çıkaracak mı? Tüm öğütücü ortamlar, kirlilik miktarı ppm veya ppb aralığında olsa bile, öğütülecek ürünün bir dereceye kadar kirlenmesine sebep olabilecektir. Çelik öğütücü ortam nispi yoğunluğu ve düşük maliyeti nedeniyle çekici olmakla birlikte, özellikle beyaz veya açık renkli bir ürünün grileşmesine yol açabilir.
ii. Fiziksel uyumluluk: Öğütücü ortamın nisbi sertliği ve aşındırıcılığı, değirmen ve ürün özellikleri dikkate alınmalıdır.
iii. Bilye yoğunluğu: Piyasada bulunan öğütücü ortam için özgül ağırlık değerleri plastik bilye için 1, tungsten karbür için 15’tir. Yüksek derecede viskoz bir sistem için çok hafif bir bilye veya düşük katı madde içeren bir sulu süspansiyon için yoğunluğu yüksek bilye seçilmemelidir.
iv. Bilye çapı: Genellikle besleme malı tane boyutu iriliştikçe, öğütme için kullanılması gereken bilye çapı da o kadar iri olur. Ayrıca daha ince öğütme için bilyenin daha küçük olması gerekir. Diğer boyut hususları, öğütücü ortamı üründen ayırmak için elek kullanılıp kullanılmayacağını içerir ve bir kural olarak, en küçük bilye çapı, elek açıklığının üç katı olmalıdır.
v. Bütçe: Burada dikkate alınacak birçok husus vardır:
a. İlk maliyet: Genellikle en iyi aşınma özelliklerine sahip bilyeler diğer seçeneklerden daha pahalıdır. Ayrıca öğütücü ortam ne kadar küçük olursa o kadar pahalıdır.
b. Bilye ömrü: Bilyeler aşındıkça değiştirilmeleri gerekir. Bir öğütücü ortam ne kadar uzun süre dayanırsa duruş süresi, yeni bilyeler, bertaraf ve işçilik ile ilgili maliyetler nedeniyle uzun vadede daha ekonomik olabilir.
c. Değirmen aşınması: Düşük maliyetli, sert bilyeler pahalı ekipman onarımına neden olabilir.
d. Ürünün kalitesi: Daha az firesi olan öğütücü ortam (boyutları küçük veya kusurlu parçalar), bu tür hataları ihtiva edebilecek daha ucuz malzemeden daha uzun hizmet ömrüne sahiptir. Yüksek yoğunlukta öğütme gerçekleştiren karıştırmalı değirmenler için ideal öğütücü ortam türü, aşağıda gösterildiği gibi tutarlı ve tekrarlanabilir bazı özelliklere sahip olmalıdır:
• Boyut dağılımı ve en iri bilye boyutu,
• Kimyasal bileşim,
• Sertlik (kimyasal bileşim ve bilye boyutu ile ilgili),
• Yoğunluk,
• Yüksek küresellik,
• Yüksek yuvarlaklık,
• Yetkinlik (mekanik bütünlük).
3. Nano Partikül Üretimi
Nano teknoloji uygulamalarında nano boyutlu partiküller benzersiz fonksiyoner özelliklerinden dolayı önemli bir rol oynamaktadır. Nanopartikül teknolojisi ise yeni nano teknolojiler ile geleneksel toz üretim teknolojileri arasında bir köprü görevi üstlenmektedir.
Özellikle daha yüksek ürün homojenliği, dayanım veya çözünürlük elde etmek için mikron altı (nano) partiküllerin kullanımı daha yüksek ürün kalitesi sunmaktadır.
Pigmentler, ince kaplamalar, mürekkep, kozmetik, biyoteknoloji gibi 100 nm’den daha ince boyutlu stabil süspansiyonlar elde etmek üzere öğütme ve nano yapılı partiküllerin dispersiyonu için genellikle karıştırmalı bilyeli değirmenler (Şekil 2) kullanılmaktadır.
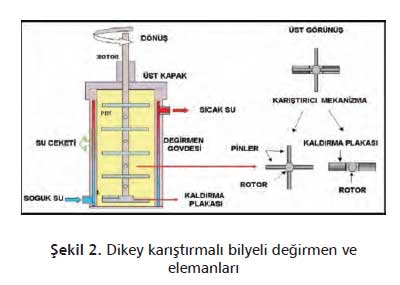
Karıştırmalı bilyeli değirmende ince partikül üretimi çok küçük öğütücü bilyeler kullanmakla mümkündür. Elde edilen ürün boyut dağılımı bilye boyutunun bir fonksiyonudur. Genel bir kural olarak, elde edilecek ürün ortalama partikül boyutu (D50) kullanılan bilyenin 1/1000’ine karşılık gelmektedir.
Bu yüzden, D50’si 100 nm olan bir süspansiyon elde etmek için teorik olarak 100 μm’luk bir bilye kullanmak gerekmektedir. Bu bilyeler ile yaklaşık on yıldır öğütme işlemleri yapılmakta ancak uygulamada malzemeleri nano boyuta öğütmek için 2 temel problem ile karşılaşılmaktadır:
i.Birinci problem dispersiyon kimyası ile ilgilidir. Değirmen taneleri hızla ufalarken ve partikül boyutu küçülürken Van der Waals kuvveti artmakta bu ise aglomerasyon (topaklanma) veya flokülasyona sebep olmaktadır. Flokülasyon ise süspansiyonun görünür viskozitesini artırmaktadır.
Flokülasyon, genellikle süspansiyonlarda istenmeyen bir durumdur. Floküle olmuş taneler, örneğin boyada genellikle arzu edilen düzeyde renk dayanımı, şeffaflık ve perdahlık göstermemektedir.
ii.Flokülasyondan dolayı oluşan viskozite öğütücü bilyeleri ortamdan ayırma problemine de sebep olmaktadır. Bu ikinci önemli problemdir. Değirmen içinde daha yüksek viskozite göründüğünden daha fazla viskoz pülp oluşur. Pülp değirmene pompalandığında öğütücü ortam bilyeler pülpün bir parçası olur ve bu da süspansiyonun katı oranını artırır.
Yukarıdaki problemleri önlemenin 2 yolu vardır: i.İnce tanelerin flokülasyonunu önlemek için süspansiyonu stabil hale getirecek kimyasal madde (öğütme kolaylaştırıcılar) kullanılmasıdır. Nano süspansiyonlar için farklı surfaktant kullanılması önerilmektedir.
ii.300 μm’den daha küçük bilye kullanmak mikron/ nano süspansiyonlar için verimliliği artırmaktadır.
Partikül boyut dağılımının dikliği açısından yaş öğütmede küçük bilyelerin kullanılması bilyeli öğütmedeki en etkili işlem parametresidir ve daha dar partikül boyut dağılımı elde edilebilmektedir.
Daha küçük bilye (50-300 μm) kullanımı özellikle yaş öğütme koşullarında cevher hazırlama prosesleri için etkili olmaktadır. Uygulamada bilye boyutu 20 μm’e kadar inebilmektedir. Tablo 3’te bilye boyutu ve ağırlık oranları belirtilmektedir.
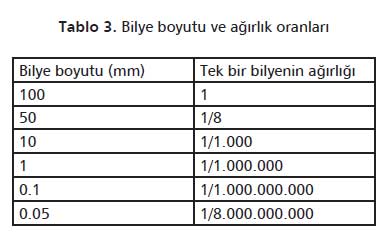
Daha küçük bilye birim değirmen hacmi başına daha fazla sayıda bilye demektir. Örneğin, 1 litrelik bir öğütme haznesinde 1 mm’lik bilyelerden yaklaşık 1.1 milyon adet yer alırken, 0.05 mm’lik (50 μm) bilyelerden ise yaklaşık 9.4 milyar adet kullanılmaktadır. Bu sayede taneler ile bilyeler arasındaki temas olasılığı çok daha artmaktadır.
Yine, bilye boyutu azalırken, bilyeler arasındaki boşluk da azalmakta, böylece bilyeler iri aglomeratları tutan bir filtre malzemesi gibi çalışmaktadır. Bilyeler arasındaki
bu boşluk 1mm’lik için 44 μm iken 0.05 mm’lik bilye için yaklaşık 2 μm olmaktadır. Değirmenlerdeki karıştırma hızı da oldukça önemlidir.
Yüksek karıştırma hızlarında (13 m/s) aglomeratlar, oluşan darbe ve gerilmelerden kaçamayarak daha verimli öğütme ve dispersiyon gerçekleşebilmektedir. Tablo 4 ise yeni geliştirilen karıştırmalı bilyeli değirmenlerde test edilen öğütücü ortam bilyelerin farklı uygulamalarını göstermektedir.
4.Sonuç
Daha yüksek ürün homojenliği, dayanım veya çözünürlük elde etmek için mikron altı (nano) partikül kullanımı daha yüksek ürün kalitesi sunmaktadır.
Pigmentler, ince kaplamalar, mürekkep, kozmetik, biyoteknoloji gibi 100 nm’den daha ince boyutlu stabil süspansiyonlar elde etmek üzere öğütme ve nano yapılı partiküllerin dispersiyonu için genellikle karıştırmalı bilyeli değirmenler kullanılmaktadır. Bu değirmenlerde uygulamada bilye (boncuk) boyutu 3-4 mm’den 20 μm’e kadar inebilmektedir.
Prof. Dr. Öner Yusuf Toraman / Endüstriyel Hammaddeler ve Yapı Malzemeleri Uygulama ve Araştırma Merkezi / Ömer Halisdemir Üniversitesi
Harun Köse / Ar-Ge Merkezi Müdürü / Niğtaş Ltd. Şti.
Doç. Dr. Orkun Ersoy / Endüstriyel Hammaddeler ve Yapı Malzemeleri Uygulama ve Araştırma Merkezi / Ömer Halisdemir Üniversitesi
Bedrana Bitirmiş / Ar-Ge Merkezi Müdür Yardımcısı / Niğtaş Ltd. Şti.
Kaynaklar
1. Clermont B., Philippe, C., 2012, Do’s and Don’ts of measuring ceramic beads wear in the lab and in the industry. http://www.
magotteaux.com/wp-content/ uploads/Do%E2%80%99s-and-Don%E2%80%99tsof- measuring-ceramic-beads-wear-in-the-
lab-and-inthe- industry.pdf
2. Collins, D., 2011, Nano milling with micro beads, http://connect.innovateuk.org/web/nanotechnologyand- coatings-industry-
2011/speakers
3. Lichter, J, Davey, G., 2002, Selection and sizing of ultrafine and stirred grinding mills, SME Mineral Processing Plant Design
Symposium, Vancouver, Canada.
4. Mende, S., Schwedes, J., Mechanical production and stabilization of nanoparticles by wet comminution in stirred media mills,
Powder Handling & Processing, Vol.18, No. 6, 2006, S. 366-373.
5. Mende, S., Grinding and dispersion in the field of nanotechnology, Ceramic Forum International, Ber. DKG 82, 2005, No.9,S.
E39-E43.
6. Mende, S., Kolb, G., Enderle, U., Nanoparticle grinding and dispersing, http://www.ceramicindustry. com, August 2006.
7. Shemanski, B., Miranda, S., Nano sizing via wet or dry grinding, http://powderbulksolids.com
8. Stenger, F., Mende, S., Schwedes, J., Peukert, W., 2005, The influence of suspension properties on the grinding behaviour of
alumina particles in the submicron size range in stirred media mills, Powder Technology, 156, s.103-110.
9. Toraman, Ö.Y., 2012, Karıştırmalı değirmenlerde çok ince (100 μm) öğütücü bilyalar kullanılarak nano partikül üretimi,
TurkChem, Eylül/Ekim 2012, Yıl:5 Sayı:30, s.130-134.
10. http://www.norstoneinc.com/our-products/beads/ grinding-media-depot/grinding-media-definitions/
11.http://www.glenmills. com/grinding-media/