Bütünlüklü Yaklaşım
Öğütme parametrelerinin güç girdisi, enerji verimliliği ve üretim kapasitesi üzerindeki farklı etkilerini göstermek için testler yapılmıştır. Yeni öğütme teknolojisi spesifik enerji ihtiyacını azaltırken güç girdisinin ve dolayısıyla üretim kapasitesinin artırılmasını sağlamaktadır.
Uzmanlar, meslektaşlarımız ve müşterilerle yapılan görüşmelerde boya, kaplama ve mürekkep sektöründe öğütme ve dispersiyon prosesleri tasarlanırken, başta yeni yatırımlar olmak üzere tesisin üretim kapasitesinin belirleyici faktör olduğu görüşü tekrar tekrar ifade edildi.
Çoğu üründe bilyalı karıştırıcı değirmenler kullanılır. Elde edilen ezilmenin esasen bir ürünün spesifik enerjisinin bir fonksiyonu olması nedeniyle bilyalı karıştırıcı değirmenlere mümkün olan maksimum güç girdisinin verilmesi çoğu durumda en kritik çalışma parametresi olarak görülür.
Bu makalede ilk olarak çeşitli parametrelerin güç girdisi, spesifik enerji gerekliliği ve üretim kapasitesi üzerindeki etkisini göstermek için kalsiyum karbonatın ezilmesine yönelik basit bir örnek kullanılacaktır.
Daha sonra, bir yandan verimliliği artırırken diğer yandan daha yüksek kapasitelere ulaşmayı kolaylaştırmak için onaylanmış bir pinli öğütme sisteminin nasıl değiştirildiği ve çalışma parametrelerinin boya, kaplama ve mürekkep sektörüne özel olarak nasıl ayarlandığı açıklanacaktır.
Üretim kapasitesinde potansiyel artışa ilişkin açılama için saha testlerinin sonuçları kullanılacaktır.
Çalışma Parametrelerinin Üretim Verimliliği Üzerindeki Etkisi
Bilyalı karıştırıcı değirmenlerin ezim ve operasyonel davranışı Stehr [1] ve Weit [2] tarafından derinlemesine araştırılmıştır. Spesifik enerji ezim davranışını gösteren genel bir faktördür, yani öğütülen ürünün (katı) kütlesine kıyasla öğütücü haznesine verilen enerji olduğu gösterilmiştir (bkz. Denklem 1).
Özet Sonuçlar
• Öğütme parametrelerinin güç girdisi, enerji verimliliği ve üretim kapasitesi üzerindeki farklı etkilerini göstermek için testler yapılmıştır.
• Önemli çalışma parametreleri temelde bilya boyutu ve değirmenden geçen ürün debisidir. Üretim kapasitesi artışları esasen viskozite, reolojik davranış ve sıcaklık sınırları gibi ürün özelliklerine bağlıdır.
• Yeni öğütme sisteminin kullanımıyla birlikte çeşitli güç girdisi ve dolayısıyla üretim kapasitesi artışları elde edilebilmektedir. Ürün kalitesi sabit tutulurken bile spesifik enerji gerekliliği büyük miktarlarda düşürülebilmektedir.
• Çalışma parametrelerinin optimizasyonu veya değirmendeki güç yoğunluğu artışı nedeniyle ürün üzerindeki yük koşulları değiştirilince formülasyona ilişkin bazı ayarlamalar gerekli olmuştur.
Burada:
E [Wh] = enerji
ESpek [kWh/kg] = kütle ile ilişkili spesifik enerji
P [W] = güç
P0 [W] = yüksüz güç
mkatı [kg] = ürün kütlesi
cm [-] = katı kütle konsantrasyonu
susp [kg/s] = süspansiyon kütle akışı
Farklı bilya büyüklükleriyle yapılan araştırmalar spesifik enerjiye ek olarak öğütme boncuğu boyutunun bilyalı karıştırıcı değirmenlerde ezilme üzerinde önemli bir etkiye sahip olduğunu göstermiştir [3-9]. Bilya boyutundaki değişiklikler bazı ezim hedefinde spesifik enerji gerekliliklerinde önemli düşüş sağlamaktadır.
Kireçtaşının süreksiz ezilmesi konusunda Kwade [10] ayrıca karıştırıcı şaftın çevresel hızının ve bilya yoğunluğunun da spesifik enerji ile ürün inceliği arasındaki korelasyon üzerinde sistematik etkiye sahip olduğuna dikkat çekmiştir.
Öğütücü boncukların kinetik enerjisi Ekin’nin bir ifadesi olarak Kwade [10] bilya SEGM’nin stres enerjisini bilya yoğunluğu pGM, bilya çapı dGM ve karıştırıcının çevresel hızı vt’nin bir fonksiyonu olarak tanımlamıştır (bkz. Denklem 2).
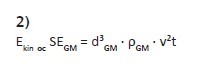
Öğütücü boncuk yoğunluğunun, karıştırıcı diskin ve bilya boyutu çalışma parametrelerinin çevresel hızının etkisine yönelik araştırmalar sırasında, sabit spesifik enerji girdisiyle birlikte en yüksek ürün inceliğinin elde edilebildiği bir optimum stres enerjisinin mevcut olduğunu gösterebilmiştir.
•Pigmentli sistemlerde, test sonuçlarının parçacık boyutu dağılımı açısından basit bir değerlendirmesi, gerçek gerekliliklerle eşleşmemektedir çünkü uygun ürün kalitesini elde etmek için parlaklık, transparanlık ve renk şiddeti gibi özelliklerin kombinasyon halinde eşleşmesi gerekmektedir.
•Ayrıca, yük koşullarının değişmesi boyalar, kaplamalar ve mürekkepler için aynı ürün kalitesini oluşturmak için formülasyonda
değişikliğe gidilmesi gerektiği anlamına gelir.
Ancak bu örnekte ele alınan çalışma parametreleri arasındaki korelasyonlar herhangi bir malzeme sistemine kalitatif olarak
taşınabilir.
Bir optimum bulmak için üç test ortamının minimumunun belirlenmesi gerekmektedir. Ezilmeyi iyileştirmek için gerekli optimum stres enerjisinin aralığı her zaman elde edilemez. Operasyonel güvenilirlik veya hedef ürün debisi açısından, çoğu durumda daha küçük öğütme boncukları kullanmak bile elverişsiz görünür.
Bu örnekte, ticari kireçtaşı ilk olarak aynı öğütme boncuklarıyla, aynı değirmende resirkülasyon modu operasyonuyla ve karıştırıcı şaftta üç farklı çevre hızıyla öğütülmüştür: 7 m/s, 10,5 m/s ve 14 m/s.
Numune parçacık boyutları her seferinde 0.03 kWh/kg katı, 0.07 kWh/kg katı ve 0.1 kWh/kg katı (bkz. Tablo 1) spesifik enerji girdisi “MasterSizer 3000” ile analiz edilmiştir.
Tablo 1: Kireçtaşı öğütürken ve boncuk boyutu dGM’yi azaltırken rotor hızı vt’nin spesifik
enerji verimliliği SEGM üzerindeki etkisi (sonuçların dördüncü grubunda).
En İyi Enerji Verimliliğiyle Debinin Maksimize Edilmesi
Test sonuçları son parçacık boyutu d90’ın spesifik enerji girdisinin bir fonksiyonu olduğu Şekil 1’de gös- terilmiştir. d90 6 μm değeri, hedef değer olarak tanımlanmıştır. Bu durum kullanılan bilyayla istenilen hedef değere en düşük karıştırıcı çevresel hızıyla ve en düşük spesifik enerji tüketimiyle ulaşılabileceğini göstermiştir.
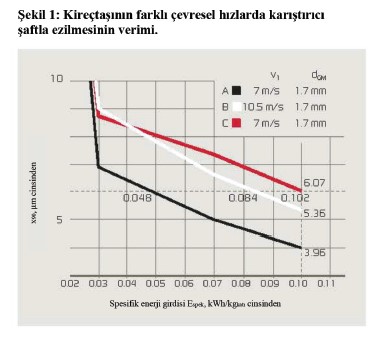
Ancak bu ayarlardaki çok düşük güç girdisi nedeniyle üretim kapasitesi sonucu da en düşük olmuştur (bkz. Şekil 2). Bu bulgu yapılan testler için bilyanın stres enerjileri hesaba katıldığında onaylanmaktadır (bkz. Şekil 2).
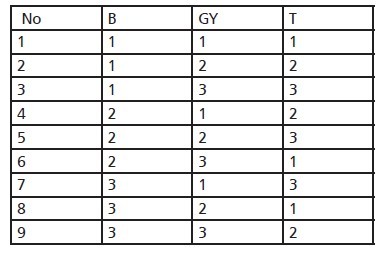
Hedef artık en düşük enerji gerekliliğiyle en yüksek üretim kapasitesini elde etmektir. Bu değerlendirme için değirmenin karıştırıcısının çizgisel hızı arttırılır ve bilya boyutunun belirlenmesi için bilya çarpışmasının oluşturduğu aynı stres enerji hesaplaması yapılır. Bu hesaplama Şekil 3’te gösterilmiştir.
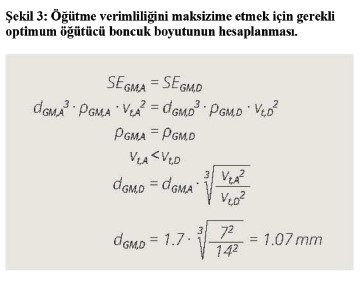
Bu sefer sabit bir bilya yoğunluğuyla 1.7 mm yerine 1.0 çapında öğütme boncukları ve 14 m/s çevresel ajitatör mili hızları kullanılırsa, spesifik enerjinin bir fonksiyonu olarak çizildiğinde ezilme sonuçları karşılaştırılabilir olur (bkz. Şekil 4).
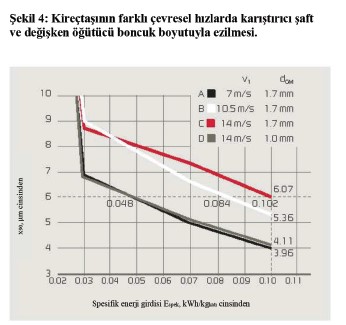
Kinetik enerjisindeki artış nedeniyle sadece güç girdisini artırarak daha yüksek üretim kapasitesinin elde edilebileceği açıkça görülebilir. Ancak bu daha yüksek üretim kapasitesi spesifik enerji gerekliliğinde bir artışla ilişkilidir.
Bunun aksine öğütme boncuğu büyüklüğünün eşzamanlı optimizasyonuyla daha yüksek enerji girdisi gerekmeksizin üretim kapasitesi olağanüstü düzeylerde artırılabilir (bkz. Şekil 5).
Mevcut Pinli Öğütme Sisteminin Optimizasyonu
1991’de patenti alınan “Zeta” pinli öğütme sistemiyle karşılaştırıldığında “Neos” öğütme sistemiyle bir dizi önemli yükseltme gerçekleştirilmiştir (bkz. Şekil 6).
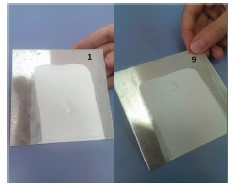
Soğutucunun öğütücü haznesinin çift ceketi içindeki akışı optimize edilmiştir. Ayrıca yüksek aşınma dayanımı ve maksimum termal iletkenliği olan seramik bir malzeme artık öğütücü haznenin iç astarı için standart hale gelmiştir.
Karıştırıcı şaft bir yanda akış optimizasyonu sayesinde soğutucu yüzeylerindeki ürün değişimi iyileşecek şekilde tasarlanmıştır. Diğer yanda ise ek rotor soğutması için maksimum soğutucu yüzeyin mevcut olmasına dikkat edilmiştir.
Soğutucu verimliliğinin iyileştirilmesi öğütücü sistemin yeni tasarımının temel bir yönüdür çünkü çoğu durumda öğütücü haznesine güç girdisi temel olarak ürünün sıcaklık sınırları ile sınırlandırılmaktadır.
Öğütücü hazne astarıyla karıştırıcı şaft üzerindeki pinler arasındaki boşluk azaltılmıştır. Bunun sonucunda aşırı küçük öğütücü boncukların daha yoğun bir şekilde ivmelendirilmesi mümkün olmuştur. Bu durum çok daha yüksek enerji yoğunluğu ve dolayısıyla öğütücü haznesine daha yüksek güç girdisi imkânı sağlamıştır.
Bunun sonucunda aynı öğütücü boncuk boyutu, bilya yoğunluğu ve karıştırıcı şaft hızıyla öğütme boncuklarının daha yüksek ortalama kinetik enerjiye sahip olmuştur.
Ayrıca bu durum ürün üzerinde daha yüksek kesme gerilimine neden olmakta ve bu da özellikle kesme kuvveti ile incelen ürünlerde makine içinde daha düşük viskoziteli bir ürüne yol açmaktadır.
Bilya ayrımındaki eleğin çapı büyütülmüştür. Bu durum eleğin ayırma alanını önemli ölçüde artırmıştır. Viskozite azaltma etkisiyle birlikte bu durum ayırma eleğinde öğütücü boncuk ve kalın ürün parçası birikintilerinin oluşmasını daha etkili bir şekilde önler.
Revize Edilmiş Makine Kurulumunun Yararları
Bu yeni özellikler sayesinde çeşitli ürünlerin öğütülmesi veya dispersiyonu sırasında daha küçük öğütücü boncukları çok daha yüksek ürün debi hızlarında kullanmak mümkün hale gelmiştir.
Aynı bilya doluluk oranında, daha küçük bilya kullanılması öğütücü boncuk sayısının ve dolayısıyla birim zamandaki temas veya stres sayısının üstel olarak artması anlamına gelir.
Daha yüksek potansiyel ürün debi öğütme süresi başına daha yüksek çevrim sayısına ve dolayısıyla ürün parçacıklarının öğütme haznesinde daha dar kalma süresi dağılımına yol açar.
Ürün beslemesinden ürün çıktısına öğütme haznesinden bir geçişte daha kısa kalma süresi ve dolayısıyla daha düşük enerji girdisi nedeniyle ürün sıcaklığının enerjisini kontrol etmek kolaylaşır; ancak öğütücü devre soğutmalı ürün tankları ile donatılmış olmalıdır.
Ayrıca karıştırıcı şaft geometrisi, çok yüksek debilerde bile boncukları elek kısmına sıkıştırmaksızın bilya hareketliliğini geliştirecek şekilde değiştirilmiştir.
Bu durum, karşılaştırılabilir kurulu motor gücü ve öğütme haznesi boyutlarında daha yüksek üretim kapasitesi elde edilebilmesi anlamına gelmektedir. Daha küçük bilya kullanabilme yeteneği ve daha yüksek ürün debi hızları sayesinde enerji gereklilikleri de çok sayıda farklı ürün için daha düşüktür.
Ayrıca bu durum bilya üzerindeki aşınmanın azaltılmasına, makine bileşenleri üzerinde daha az strese ve dolayısıyla üretilen ürün hacmine göre daha düşük durma süresi, bakım ve yedek parça maliyetlerine yol açmaktadır.
Gerçek Müşteri Ürünleriyle Yapılan Saha Testlerinin Sonuçları
Siegwerk Druckfarben şirketiyle birlikte çeşitli gerçek ürünlerle saha testleri yapılmıştır. Orijinal “Zeta” öğütme sisteminden yeni öğütme sistemine geçiş yaparak makinenin öğütme haznesine olan güç girdisini tüm ürünler için %18’den %143’e uzanan geniş bir aralıkta artırmak mümkün olmuştur ancak güç girdisindeki potansiyel artış bir dizi kriterin bir fonksiyonudur.
Makinenin kurulu motor gücünün yanı sıra buradaki önemli faktörler ürünün sıcaklık sınırı, viskozitesi ve reolojik davranışıdır. Orijinal öğütme sisteminde, güçlü kesme ile incelen ürünlerin viskozitesine bağlı olarak çeşitli ürünler için makinenin güç sınırına ulaşmak genelde mümkün olmuyordu.
Bunun aksine yeni öğütücü sistemde ürünün sıcaklık sınırına ulaşmadan değirmenin güç sınırına ulaşmak daima mümkün oluyordu (bkz. Şekil 7).
Şekil 7: Çeşitli müşteri ürünleri için “Zeta 25”ten (LMZ 25) “Neos 20” öğütücü sistemine
geçmekten elde edilen performans artışı [11].
Bu durum kuşkusuz bir yanda makinenin soğutma kapasitesiyle ancak diğer yanda aynı zamanda zaten tartışıldığı gibi viskozite azaltma etkisiyle açıklanabilmektedir. Değirmendeki ürünün daha yüksek kesme stresi ve bunun sonucundaki daha düşük viskozitesi sayesinde öğütücü haznesi duvarı yakınında ve karıştırıcı şaft yakınında daha iyi ürün değişimi olur ve bu da öğütme haznesinden daha iyi ısı yayılımıyla sonuçlanır.
Ancak Schönstedt [12] özellikle ürüne bağlı olarak formülasyonun değiştirilmesinin de gerekli olabileceğini göstermiştir. Kullanılan değirmen teknolojisine bağlı olarak örneğin ürün viskozitesinde, renk yoğunluğunda, şeffaflığında veya parlaklığında değişiklikler gerçekleşebilir.
Standardın spesifikasyonlarını elde etmek için dolayısıyla en basit durumunda çözücünün konsantrasyonunu değiştirmek gerekmektedir. Ancak bazı durumlarda yalnızca bağlayıcı maddenin değiştirilmesi istenen sonucu vermektedir.
Daha Düşük Enerji ve Daha Yüksek Çıktıyla Sabit Kalite
Yeni öğütme sisteminin kullanımıyla birlikte çeşitli güç girdisi ve dolayısıyla üretim kapasitesi artışları elde edilebildiği saha testlerinde gösterilmiştir. Değirmenin çalışma parametrelerinin ve/veya ürün formülasyonunun değiştirilmesiyle birlikte, spesifik enerji gerekliliği sabit ürün kalitesiyle birlikte dahi büyük ölçüde azaltılabilmektedir.
Burada önemli çalışma parametreleri temelde bilya büyüklüğü ve değirmenden geçen ürün debidir. Elde edilebilecek üretim kapasitesi artışına yönelik belirleyici faktörler
temelde viskozite, reolojik davranış ve sıcaklık sınırları gibi ürün özellikleridir.
Ayrıca, çalışma parametrelerinin optimizasyonu veya değirmendeki güç yoğunluğu artışı nedeniyle ürün üzerindeki yük koşulları değiştirilince formülasyona ilişkin bazı ayarlamaların gerekli olduğu gösterilmiştir.
Dr. Stefan Mende - Teknik ve Bilimsel İletişim Yöneticisi - Netzsch-Feinmahltechnik GmbH
Kaynaklar
[1] Stehr N., Zerkleinerung und Materialtransport in einer Rührwerkskugelmühle, Dissertation, TU Braunschweig, 1982.
[2] Weit H., Betriebsverhalten und Maßstabsvergrößerung von Rührwerkskugelmühlen. Dissertation, TU Braunschweig, 1987.
[3] Joost B., Kwade A., Feinstzerkleinerung in Rührwerksmühlen, Das Keramiker-Jahrbuch, 1996, pp. 23-38.
[4] Schwedes J., Kwade A., Stender H.-H., Hochschulkurs Zerkleinern und Dispergieren mit Rührwerkskugelmühlen Umdruck
zum Hochschulkurs vom Institut für Mechanische Verfahrenstechnik und Kwade+ Schwedes Zerkleinerungstechnik,
Braunschweig, 2008.
[5] Thiel J.-P., Energiebedarf und Durchsatzverhalten der Kohlenasszerkleinerung in einer Rührwerkskugelmühle, Dissertation,
TU Braunschweig, 1993.
[6] Bunge F., Mechanischer Zellaufschluß in Rührwerkskugelmühlen, Dissertation, TU Braunschweig, 1992.
[7] Mankosa M.J., Adel G.T., Yoon R.H., Effect of media size in stirred ball mill grinding of coal, Powder Technology, 1986,
Vol. 49, pp 75-82.
[8] Stadler R. et al, Naßmahlung in Rührwerkskugelmühlen, Chemie-Ingenieur-Technik, 1990, Vol. 62, pp 907-915.
[9] Roelofsen D. P., Entwicklungen auf dem Gebiet des Pigmentdispergierens mit Rührwerkskugelmühlen, Farbe + Lack, 1991,
Vol. 97, No. 3, pp 235-242.
[10] Kwade A., Autogenzerkleinerung von Kalkstein in Rührwerkmühlen, Dissertation, TU Braunschweig, 1996, ISBN 3-8265-
2082-3.
[11] Stender H.-H., First industry test results of packaging ink production with NETZSCH Neos technology, presentation,
Dispersion Days, May 15-17, 2017, Selb.
[12] Schönstedt B., Implementation of new bead mill technology into regular production, presentation, Dispersion Days,
May 15-17, 2017, Selb.