Linde Gaz A.Ş. Applications in the Plastics Industry
A key player in the Turkish economy is the plastics sector. Its contribution to the Turkish economy is currently steadily growing, with a production of almost 10 million tons, a turnover of close to 40 billion dollars, and an export of roughly 8 billion dollars.
Turkey’s plastics sector ranks sixth globally and second in Europe in terms of manufacturing capacity, after Germany. About 915 million dollars worth of machinery and equipment
investments were made in the plastics sector between 2017 and 2021, including 21% injection, 17% extrusion, etc. components and parts. In the first quarter of 2022, Turkey used 1.2 million tons of plastic product manufacture, and 1.2 million tons were exported.
We at Linde Gas Turkey regularly monitor the advancements being made in the manufacture of plastic in this expanding industry. With solutions that prioritize higher-quality products and machine health in plastic injection manufacturing and the processes that follow it, we support the industry.
The demand for and expectations for injection molded components are growing along with the advancement of machine technology. Our cutting-edge “Gas Injection Molding (GIM)” technology is already utilized by several firms.
We actively participate in the manufacturing of cars, automotive panels, white goods handles, and similar thick section components with GIM technology in order to address the problems of modern product design.
The removal of heat, pressurization capabilities, need for water drying, risk of water leakage, and complexity of the system all contribute to the numerous drawbacks of water injection molding (WIM) in recent years. By combining a proprietary internal cooling system with a nitrogen injector that operates between 50 and 340 pressures, we
provide the industry with our GIM technology.
The GIM nitrogen method uses a controlled injection of nitrogen gas to push the molten mass out of the component’s core with high pressure and toward the mold’s surface as the plastic is injected into the mold. This technique takes use of the gas’s great mobility.
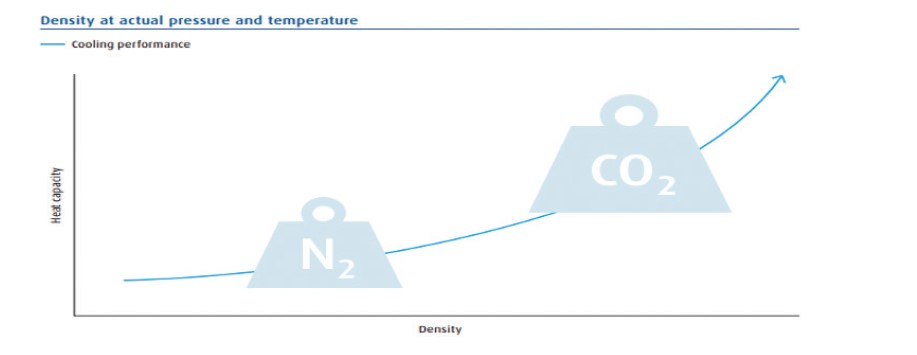
It stops oxidation under pressure, uses less material to fill the mold, and forges a sturdy plastic structure inside the mold. The heat absorption level of nitrogen gas, which is ideal
for high pressure and densely distributed in the atmosphere, is 1.041 kJ. (kgK).
At the same time, it has been discovered that atmospheric gas carbon dioxide, which poses no threat to human health, opens up new possibilities due to its 3.0 kJ (kgK) heat intake capacity. This discovery is the result of research efforts to use the riskfree and quick application possibility of gas injection with nitrogen and the high heat absorption feature.
To further boost the competitive and technological advantages provided, we have increased PLASTINUM GIM technology efficiency. According to the thermal test results, it has been seen that carbon dioxide gas, which is a high density gas, provides an advanced cooling process and a cycle time advantage of 8% to 60% compared to gas injection with nitrogen.
It has also been observed that polymer and additive residues are significantly reduced.
With our nitrogen and carbon dioxide gas injection systems; by providing as few changes as possible in the mold; Less maintenance effort thanks to almost zero downtime, protection of machinery and technology, smooth surface and weight reduction in the product, saving up to 30% from plastic material, prolonging the mold life by preventing mold wear thanks to the reduction of the internal pressure of the mold, and shortening
the cycle time up to 70%.
Together with the high degree of safety proven by the customer, we provide a significant benefit in product quality improvement.
The plastics sector is only one of the numerous industrial uses for carbon dioxide gas. Innovative technique called Cryoclean Snow uses tiny dry ice particles to clean and pretreat surfaces. Liquid carbon dioxide is used to inject dry ice particles onto the surface, and then the particles are removed using compressed air and nozzles.
It allows for a fully autonomous production process since the use of liquid carbon dioxide is
independent of the supply and replenishment of dry ice pellets. To list the impurities that may generally be removed with Cryoclean Snow technology: Dust, fingerprints, limescale, grease and rust inhibitors.
Compared to water or chemical cleaning, cryoclean snow technology offers several benefits. By drastically reducing the use of solvents, its environmental impact, and operating costs, as well as by not requiring additional drying, cleaning time with wet washing is less than a few minutes (for buffers, for example), and all process parameters can be precisely controlled, we can say that it offers significant benefits to the industry.
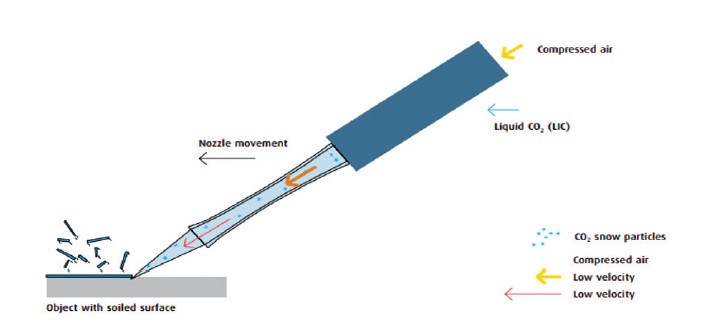
The global output of plastic is rising daily. Turkey’s first three quarters of 2018 had a 12% growth over the same period in 2021. It closely monitors this emerging market, and as Linde Gaz Turkey, we continue to offer manufacturers solutions for all issues with our industrial gases, our engineering division in a cutthroat environment, and our emerging technologies.
We add value to the emerging plastics industry with our Nitrogen Gas Injection, Plastinum GIM, and Cryoclean Snow technologies.
Serhat Soydan
Application Sales Engineer
Chemistry & Plastics Segment
Linde Gaz A.Ş.