Siemens Switchgear Ltd., Shanghai, expands robotic deployments with Geek+ for lean manufacturing through smart automation.
In order to create an end-to-end system, Geek+ delivers four types of autonomous mobile robots in Siemens Switchgear's Shanghai warehouse.
Siemens Switchgear's Plan For Every Part (PFEP) logistics model, which fully automates both picking and production line distribution, is powered by new robots.
Geekplus, a global leader in autonomous mobile robots, has expanded its collaboration with Shanghai-based electronic components manufacturer Siemens Switchgear Ltd. on the second phase of a smart manufacturing automation project.
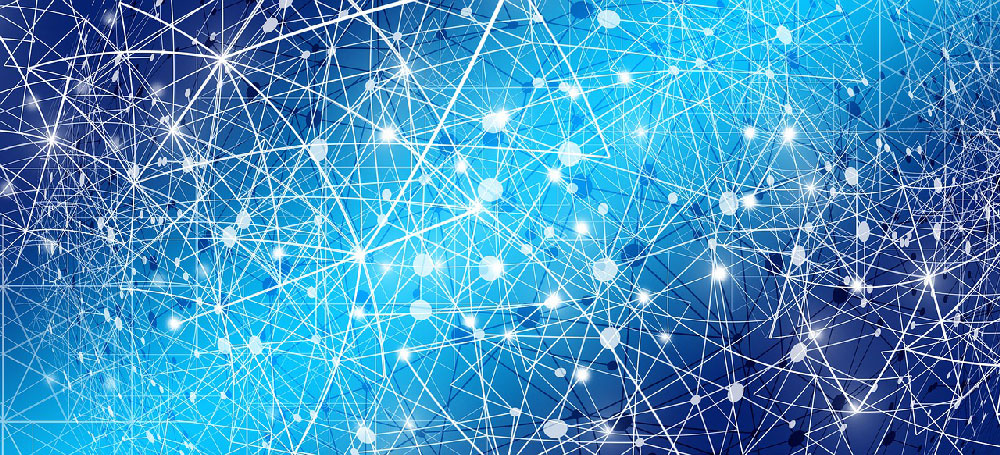
The expansion adds more Geekplus goods-to-person picking and materials handling robots to the multi-robot configuration and adds 3000m2 of automated warehousing space. In the production line, the system achieved a delivery accuracy rate of 100 percent, with materials accuracy of more than 99.98 percent.
Siemens Switchgear Ltd., Shanghai collaborated with Geekplus for the first time in 2019 and successfully built a full-process flexible automated intelligent logistics factory using four types of Geekplus robots: P800R goods-to-person picking robots, MP1000R moving robots, RS2 tote-to-person robots, and X-series four-way shuttles for high-density storage.
Robots now automate the entire manufacturing process, from inbound receiving to in-store stock management, outbound stock collection, and production line delivery.
Junzhe Yang, Vice President of China Region at Geekplus, said: "We are very proud of this end-to-end automation success with Siemens Switchgear Ltd., Shanghai.
The company makes cutting-edge electronics technology, and Geekplus uses robotics technology to power their operations. The result is a beautiful example of how well smart intralogistics can function."
As
Siemens Switchgear's business expanded, new demands for storage capacity, material informatization, distribution timeliness, and accuracy arose. Implementing a Plan For Every Part (PFEP) logistics model is a critical step in Siemens Switchgear Ltd., Shanghai's response to this new reality.
The 360° inventory oversight required by this strategy is provided by entrusting the site's operation to Geekplus's smart technology and sophisticated software. Geekplus has developed a fully automated, flexible, multi-robot solution that marks a watershed moment in intelligent manufacturing.
In this second phase of the project, Geekplus added more MP1000R moving robots equipped with laser-guided simultaneous localization and mapping (SLAM) capabilities to the production line without interrupting operations.
Managed by Geekplus's warehouse management system, these robots autonomously carry out on-time delivery of raw materials to where they are needed in the production line. This precise matching of required materials and delivery times reduces line side warehouse space requirements by half and yields a material handling accuracy rate of over 99.98%.
In realizing this expansion, Geekplus engineers listened to Siemens Switchgear's experiences with the first-phase configuration. To better meet the client's needs, the Geekplus team optimized the paths layout of the four-way shuttle storage system and the layout of the picking workstations.
The outbound throughput rate has increased from 500 pallets per day to 1000 pallets per day. They also added a steel platform to create a second storage level operated by the original P800R fleet, with a new cluster of P800Rs equipped with square pallet docking with low-level hoists in the materials receiving area on the ground floor.
These additions, along with more MP1000R moving robots, have been seamlessly integrated into Siemens Switchgear's fully automated facility and freed up an additional 3000m2 of storage space.
Geekplus and Siemens Switchgear Ltd., Shanghai will expand their collaboration, explore new application scenarios, and continue to lead the intelligent transformation and upgrading of the manufacturing industry.
Note: Content may be edited for style and length.
Source