A number of updates to Reactor 2 have been implemented as a result of studying and better understanding the types of single-point variables and the detection methods required to identify these conditions.
Flow meters are standard on Reactor 2 elite models E-30, H-30, H-40, and H-50. The ratio tolerance is set at 5% but can be changed between 3%-20%. Ratio alarms are disabled by default but can be enabled in the Advanced Display Module (ADM) System setup menu.
Due to the importance of pressure monitoring as part of the Reactor ratio assurance system, customers interested in being able to detect possible off-ratio conditions must be sure they have inlet pressure monitoring installed when adding flow meters to their system.
The Reactor software was updated requiring both inlet pressure monitoring and pressure imbalance alarms to be enabled with the use of flow meters.
Reactor elite models include inlet pressure monitoring as standard, but inlet monitoring will need to be added to non-elite models when using flow meters.
For this reason, five new flow meter kits have been created to provide flow meters and the necessary inlet monitoring hardware for each Reactor type: E-30, E-30 elite, E-30i, H-30/40/50, and H-30/40/50 elite.
The Reactor 2 software has been updated to optimize inlet pressure monitoring for low pressure alarms and now has added detection for high inlet pressure issues. To minimize the frequency of being shut down for some off-ratio conditions caused by feed pump issues, Graco has developed new software for Reactor 2 E30 models.
Called Reactor Smart Control, it will automatically make adjustments to the Reactor to attempt to prevent off-ratio dispensing. Reactor Smart Control will be enabled as the default setting on new elite model electric Reactors but can be disabled in the ADM System setup menu.
Reactor Smart Control works using the design of the electric Reactor to its advantage. Electric Reactor pumps are double-acting. This means a chemical is pumped out on both the up and down stroke of the pump.
However, the chemical is only taken into the pump on the fill stroke (up direction). Graco’s new Reactor Smart Control runs the pump at a speed needed to be properly fed.
This is achieved by monitoring inlet pressure transducers. When the inlet pressure is insufficient to properly feed chemical into the pump, the Reactor will run slower on the up stroke. To compensate for the loss of speed, the pump runs faster on the down stroke.
Overall, pressure at the gun will only be affected if the feed is severely restricted and unable to keep up. This feature can only be used on electric Reactors.
Hydraulic Reactors require manually setting of the hydraulic pressure to control the speed of the pump. Software cannot be used to compensate for feed pump issues on hydraulic models.
Graph shows the benefit of using the Reactor Smart Control mode
Through the use of flow meters, true volumetric flow data is now collected. This data is important in demonstrating the proper installation of materials.
Through the use of the Reactor app, customers can now view, save, send and print reports summarizing their spray data including ratio. A number of ratio reports are available in a PDF or Excel format: a ratio summary report, and ratio detail report and a ratio graph.
Gaining a Competitive Advantage
As an insulation contractor, understanding the spray foam installation parameters including temperatures, pressures and ratio is becoming more and more important. Builders, homeowners and architects are continuing to request and specify more spray foam as their choice for insulation.
Therefore, they are becoming more educated in the process and are now asking for assurance that the job is being installed correctly. Having the right equipment to monitor and detect possible issues and having the ability to collect the required information to provide proof of installation is important.
A contractor who understands the potential issues, knows how to minimize their occurrence, and is able to quickly resolve them if they do occur, will set themselves apart from their competition.
Understanding Single Point Variables
It is important to understand the types of issues that may cause an off-ratio condition, and the best method of detection for each issue. To identify the preferred detection method for each single-point variable, Graco recommends using a “Good, Better, Best” scale:
• Best: The device is the preferred method to detect the issue. This detection method will be the most sensitive so detection will be the fastest,
• Better: The device will detect the issue, but detection may take longer. The issue may also have to become more severe to be detected,
• Good: The device will detect the issue, but detection will take the longest. This detection method is the least sensitive method of detection and
should not be relied upon as the primary detection method,
• Not Applicable (NA): Device cannot detect this type of issue.
Utilizing inlet and outlet pressure monitoring and flow meters, the Graco Reactor 2 can monitor for these issues and shut the proportioner down if required.
The operator can then make the necessary updates in order to eliminate the off-ratio condition. The table below summarizes the various single point variables that may cause off-ratio foam to be sprayed.
More İnformation
Graco’s Reactor 2 Ratio Assurance System is an industry leading solution that gives confidence that foam is sprayed correctly, and peace of mind to homeowners and sprayers. It eliminates costly repairs and callbacks and allows the quick detection of equipment issues and off-ratio foam. To discover how it can improve your spray foam spraying processes.
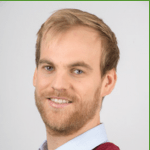
Tom Vandevenne
Product Marketing Specialist
Graco