Bilinen en eski döküm işlemi olan kum dökümü, milattan önce 1000’li yıllardan bu yana uygulanmaktadır.
Proses kontrolleri, malzeme seçenekleri, tolerans yetenekleri,özenli parçalar üretme kabiliyeti, geniş ebat aralıkları gibi özelikleri elbette çok önemli gelişmeler göstermesine rağmen uygulamanın temelleri büyük ölçüde aynı kalmıştır.
En kısa anlatımıyla kum döküm işlemi, istenilen parça şeklinde bir boşluk oluşturulması ve içine erimiş metal dökülmesidir. Kum dökümü, en çok yönlü ve muhtemelen binlerce yıldır en çok kullanılan metal döküm yöntemidir.
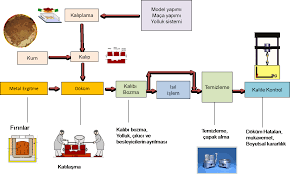
Bir ürünün nasıl üretileceğini seçerken hangi metal işleme proseslerinin (hangi döküm süreçleri dahil) en uygun olduğu konusunda tasarım gereksinimleri (şekillendirme ve boyutsal ihtiyaçlar dahil), parça ve takım maliyeti, ihtiyaç duyulan miktar ve hatta fizibilite üretimi süreci şekillendirir.
Kum döküm işlemi, çok büyük parçalar ve iç geçitler içeren neredeyse her tasarımın şekillendirilmiş parçalarını üreten teknikler kullanır.
Herhangi bir spesifik ürün için gerekli toleranslar, tasarım karmaşıklığı, hacim, takım kullanılabilirliği veya teslim süresine göre daha uygun döküm veya metal işleme süreçleri olabilir, ancak ihtiyaç duyulan konfigürasyonda bir dökümün kum işlemi kullanılarak yapılması mümkündür ve bu tasarım mühendisine bırakılan bir karar olmaktadır.
Proses, kum dökümü olarak adlandırılır çünkü metalin içine döküldüğü boşluğu içeren kalıp, sıkıştırılmış veya konsantre edilmiş kumdan yapılır. Kum, şeklini korumak için takviye edici başka malzemeler de içerebilmektedir.
Kum Döküm Prosesi
A. Döküm Modeli Üretmek - İstenen Ürün
İşlem, istenen bitmiş parça ile aynı ayrıntılara sahip yeniden kullanılabilir bir model kullanmaktadır. Termal büzülme veya küçülme için bir tolerans taşımaktadır.
B. Döküm Modeli: Akaçlar (Gates)
ve Besleyiciler (Risers): Metal Dağıtım Sistemi
“A” adımında üretilen döküm modeli, aynı zamanda, arzu edilen dökme ürün tasarımını uygun akaç ve besleyicilerle besleyecek olan metal yolları da içerir. Bu, kaçınılmaz ısıl büzülmeyi kabul edilebilir bölgelere (gerçek istenen nihai üründen başka bir yere) çeker ve metal akışı ve gerekli gaz havalandırmasını yönetir.
Döküm modelleri, gerekli hacme ve toleransa bağlı olarak ahşap, metal, sentetik, harcanabilir polistiren (EPS) ve diğerleri gibi birçok farklı malzemeden yapılmıştır.
C. Kalıbın Oluşturulması
Döküm modelin çevresinde yüksek sıcaklıkta (örneğimizde kum) stabil olan bir refrakter malzeme oluşur. Materyal, döküm sırasında erimiş metalin ağırlığını taşıyacak kadar güçlü olmalı ve metal ile reaksiyona dirençli olmasına rağmen, döküm soğuduktan sonra katılaşmış metalden kolayca ayrılacak kadar kırılgan olmalıdır.
Kalıbı yapmak için kullanılabilecek çeşitli kum malzemeleri vardır. Kum tipik olarak, dökme işlemine dayanacak şekilde kil veya başka kimyasal bağlama maddeleri gibi diğer malzemelerle de güçlendirir. Alternatif olarak kalıp, istenen şekilli kavitenin doğrudan bir kum bloğuna işlenmesiyle de oluşturulabilir.
Bu teknik, ürün geliştirme sırasında yaygın olarak uygulanır, çünkü tasarım değişiklikleri hızlı bir şekilde yönetilebilir, uygulanabilir veya fiziksel bir modelin depolanmasını, bakımını önlemek için seyrek kullanımlı parçalar için kullanılabilir.
Kalıp, genel olarak üst ve alt yarı olmak üzere iki parça halinde üretilir. Kum ayarlandığında (geleneksel / makine kullanılmadan), yarımlar ayrılır ve döküm modeli kaldırılır.
Daha iyi bir yüzey kaplaması sağlamak ve dökülmüş metalin türbülansından kalıbı korumak için bir refrakter kaplama eklenir. Yarımlar, bir araya yerleştirilir ve Döküm modeli şeklinde bir boşluk bırakılır. Kalıp ayrıca, nihai üründe istenen iç geçitleri üretmek için kullanılan bir usul olan maçaları (core) da içerebilir.
D. Metalin Kalıba Dökülmesi
Erimiş metal, doğrudan statik kalıba dökülür. Hem bitmiş parçayı, hem de yükselticileri tanımlayan boşluğu doldurur. Besleyiciler, döküm işlemini mevcut bir sıvı metal kaynağıyla besler. Son olarak soğumaya ve katılaşmaya yönelik tasarlandıklarından, küçülme ve potansiyel boşluk, istenen kısımdan ziyade besleyicide yoğunlaşır.
Eğimli dökmenin çeşitli varyasyonları vardır, metalin döküm içine daha düzgün akmasını ve türbülansı ortadan kaldırmasını sağlayan bir süreçtir. Daha az türbülans, oksitlerin ve döküm kusurlarının oluşumunu önlemeye yardımcı olabilir.
Hemen hemen her alaşım bu işlem kullanılarak üretilebilir. Oksijen ile özellikle reaktif olan malzemeler için, havayı erimiş metalden uzak tutmak için argon koruyucu gibi bir prosedür kullanılabilir.
E. Shakeout (Silkelenme)
Hem istenen kısmı hem de onu oluşturmak için gereken ek metali içeren döküm, katılaşır ve soğutur. Kum, sarsıntılı bir süreçte kırılır. Kalıbı oluşturmak için kullanılan kumun çoğu, toplanır, yenilenir ve tekrar kullanılır.
F. Son İşlemler
Akaçlar, yolluklar (runners) ve besleyiciler dökümden kesilir ve gerektiğinde, dökümün boyutsal olarak bitirilmesi için kumlama, taşlama, vb. gerçekleştirilir. Genel olarak kum dökümleri nihai boyutlara veya toleranslara ulaşmak için en azından bazı ek işlemler gerektirir.
Parçalar, boyutsal kararlılığı veya özellikleri iyileştirmek için ısıyla işlenebilir. Tahribatsız muayene de yapılabilir. Bu floresan penetrant, manyetik parçacık, radyografik veya diğer denetimleri içerebilir. Son boyut kontrolleri, alaşım test sonuçları ve NDT, sevkiyat öncesi doğrulanır.
Kaynakça
• Metal Casting: A Sand Casting Manual for the Small Foundry, Volume 2. Steve Chastain, 2004.
• The Complete Handbook of Sand Casting. C. W. Ammen. McGraw Hill Professional, Mar 22, 1979.
• Metal Casting: Principles And Practice. Ramana Rao. New Age International, 2007.