Giriş
Günümüz teknolojinin her geçen gün hızla artmaya devam eden ihtiyaçlarını karşılamakta yetersiz kalan bazı monolitik malzemeler söz konusu uygulama alanlarındaki yerlerini yavaş yavaş kompozit malzemelere bırakmaktadır.
Kompozit malzemeler üzerinde çok yoğun araştırmaların yapıldığı ve gerek yeni bileşimlerde ve gerekse yeni tasarımlara sahip malzemelerin geliştirilmesi sürecinin sürekli olarak devam ettiği bir alandır [1-9].
Metal, seramik ve polimer matrisli kompozit malzemeler için yeni uygulama alanları bulmak, mevcut uygulama alanlarını genişletmek, daha iyi özelliklere ulaşmak ve daha ekonomik bir şekilde üretimi gerçekleştirmek gibi çok çeşitli amaçlarla yoğun çalışmalar gerçekleştirilmektedir [10-16].
Kompozit malzemelerin üretimleri için çok basitten çok karmaşık üretim yöntemlerine varıncaya kadar pek çok farklı üretim yöntemi kullanılmaktadır [17-22]. İnfiltrasyon yöntemi kompozit üretiminde en yaygın kullanılmakta olan yöntemlerden biri olarak karşımıza çıkmaktadır.
Seramik–metal kompozit malzemelerde bileşimde yer alan seramik ve metal oranına bağlı olarak elde edilen özellikler önemli oranda değişmektedir. Kompozit içerisinde seramik hacim kesri arttıkça aşınma direnci ve yüksek sıcaklık mukavemeti de artmaktadır.
Düşük hacim kesirlerinde takviye seramik içeren kompozit malzemelerin üretilebilmesi için çok sayıda farklı teknik uygulanabilmektedir.
Ancak yüksek seramik hacim kesrine sahip yoğun kompozit yapıların üretilebilmesi için önceden şekillendirilmiş gözenekli seramik peletlere metal infiltrasyonu kullanılabilecek en uygun ve sınırlı sayıdaki yöntemlerden biridir [23].
Sıvı metalin gözenekli seramik yapı içerisine infiltrasyonu basınç veya vakum yardımıyla sağlanabileceği gibi sıvı damlacıkları katıyı ıslattığı zaman dışarıdan bir etki olmaksızın, gözenekli yapı içerisine sıvının kendi kendine infiltrasyonu da gerçekleşebilmektedir [24, 25].
İnfiltrasyon genel olarak itici gücüne bağlı olarak Şekil 1’de görüldüğü üzere üç farklı grup altında incelenmektedir.
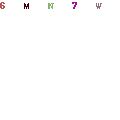
Sıvı metalin gözenekli seramik malzemeye infiltrasyonu büyük ölçüde ıslatma yetersizliği nedeniyle kolay bir şekilde gerçekleşmemektedir. Islatma basit bir şekilde bir sıvının katı bir yüzey üzerinde yayılma kabiliyeti olarak açıklanabilmektedir.
Seramik ve metal matrisli kompozitlerin infiltrasyon süreçleriyle üretilebilmesi için sıvı metalin seramik fazı ıslatması gerekmektedir. Temas açısı 0° olduğunda mükemmel ıslatma sağlanırken, ıslatma açısı 180° olduğunda ise sistem tamamen ıslatmaz hale gelmektedir.
Genellikle metal oksitler ile metal arasındaki temas açısı 90°’den büyüktür. Bu nedenle, katı yüzeyde bulunan kılcal boşluklara ve pürüzlü yüzeylere sıvı metal infiltrasyonunu sağlamak üzere bir dış basınç uygulanması gerekli olmaktadır [25].
Basınç uygulama işlemi bir gaz yardımıyla uygulanabileceği gibi mekanik olarak da uygulanabilmektedir.
İnfiltrasyon sürecinde vakum altında çalışılmasının eriyik metalin seramik pelete infiltrasyonuna yardımcı olduğu bilinmektedir. Bazı metal–seramik sistemlerinde seramik fazının etrafında bir vakum ortamının oluşturulmasının, infiltrasyonu sağlayacak bir büyüklükte basınç farkı oluşturmak için yeterli olduğu gözlemlenmektedir.
Ayrıca vakum ortamında infiltrasyon sürecinde sıvı metalin oksitlenmesinin engellendiği ve üretilecek kompozit yapıda gaz veya hava kalması sebebiyle gözeneklerin oluşmasının önlendiği bildirilmektedir.
Dışarıdan basınç uygulamaksızın, özel olarak tasarlanan bileşim ya da süreç koşullarıyla, iyi bir ıslatma sağlanarak yürütülen infiltrasyon yöntemi karmaşık şekilli ürünlerin neredeyse hiç çekme gözlemlenmeksizin oldukça yoğun olarak üretilmesine olanak tanıyan, basit ve ekonomik bir yöntemdir.
Bu yöntemde sıvı metal seramik gözenekli bünye içerisine, basınç uygulanmaksızın kendi kendine sızmakta ve başlangıçta gözenek içeren seramik peletteki boşlukları doldurup daha sonra da bulunduğu yerlerde katılaşmaktadır.
İnfiltrasyon yönteminin en önemli faydalarından biri de elde edilen kompozit yapının her yerinde aynı özelliklerin elde edilebilmesidir [26]. Şekil 2’de temsili bir basınçsız infiltrasyon düzeneği sunulmaktadır.
Basınçsız İnfiltrasyonu Etkileyen Değişkenler
Basınçsız infiltrasyon ile seramik–metal kompozit üretimi ancak bazı özel koşulların sağlandığı durumda mümkün olmaktadır. Kendiliğinden infiltrasyonun gerçekleşmesi için önemli olan genel bazı değişkenler Şekil 3’te özetlenmektedir [27].
Başlangıç Malzemelerinin Yüzey Kimyası (Yüzey oksit tabakası, yüzeyin başka bir faz ile kaplanması
vb.): İnfiltrasyon süreci oldukça hassas ilerleyen bir süreç olup, infiltrasyonu azaltıcı etkiye sahip çeşitli etkenler söz konusudur.
Genelde eriyik yüzeyinde yer alan oksit tabakalar ergimiş metal/alaşımların seramik malzemesini ıslatmasını engeller. Bu oksit tabakaları ergimiş metalin gözenekli seramik bünyeye infiltrasyonuna karşı önemli bir direnç oluşturur.
Örneğin alüminyum metalinin oksijene karşı afinitesi oldukça yüksek olup 400°C’de 4 saatte alüminyum alaşımı yüzeyinde 50 nm ve oda sıcaklığında ise anında 20 nm kalınlığında bir tabaka oluşur.
Dolayısıyla Al bazlı sistemlerde oksit oluşumundan kurtulmak oldukça güçtür. Al alaşımı kullanılan sistemlerde genel olarak 900°C’nin altında infiltrasyon gözlenmez [31].
İnfiltrasyon Sıcaklığı:
Sıcaklık, infiltrasyon yönteminde en önemli üretim değişkenlerinden biri olup artan infiltrasyon sıcaklıklarında sıvı metalin akıcılığı artarak, seramik taneleri arasındaki gözeneklerden infiltrasyonu kolaylaşmaktadır.
Rodriques–Reyes [24], Al–Si–Mg/SiCp kompozit yapılarının basınçsız infiltrasyon yöntemi ile üretilmesinde en önemli değişkenin sıcaklık olduğunu bildirmektedir.
SiC blok parçaların infiltrasyonu artan sıcaklıkla, azalan kuluçka süresiyle gerçekleştirilmiş ve bu sürecin özellikle sıcaklığa bağlı olduğu belirtilmiştir [24].
Chong ve ark., [32] Al/SiCp kompozit yapılarının basınçlı infiltrasyon yöntemi ile üretilmesinde, sıcaklığının artmasıyla eşik basıncın azaldığını tespit etmişlerdir. Ayrıca artan sıcaklığa bağlı olarak kompozit yapıların gözenek miktarının azaldığı da tespit edilmiştir [32].
Contreras ve ark., [33] %56 takviye hacim oranındaki Mg/TiC kompozit yapılarını 850–900°C sıcaklıklarda Ar gaz ortamında, basınçsız infiltrasyon yöntemiyle üretmişlerdir. Artan infiltrasyon sıcaklıklarında, sıvı matrisin takviyeyi başarılı bir ıslatma eğilimi gösterdiğini gözlemlemişlerdir.
Kompozit yapıların mekanik özelliklerinin büyük ölçüde ıslatma davranışına bağlı olduğunu ve artan infiltrasyon sıcaklıklarında mekanik özelliklerin daha iyi olduğunu belirtilmişlerdir [33].
İnfiltrasyon Süresi: İnfiltrasyonun gerçekleşebilmesi için diğer süreç değişkenlerine de bağlı olmakla birlikte bir kuluçka süresine ihtiyaç duyulmaktadır [24, 34].
Rodriques–Reyes [24], Al–Si–Mg/ SiCp kompozit yapılı malzemeleri basınçsız infiltrasyon yöntemi ile üretmişler ve artan infiltrasyon sıcaklıklarında kuluçka süresinin azaldığını tespit etmişlerdir.
Kuluçka süresinin sıcaklığa bağlı bir periyot olduğunu, ancak sıcaklık ve zaman değişkenlerinin ortak etkisinin göz ardı edilebileceğini belirtmişlerdir.
[24] Kevorkijan [35] sıvı infiltrasyon yöntemi ile SiC, Si3N4, AlN, Mg3N2 ve TiO2 seramiklere %7 Si, % 0,3 Mg içeren 356–T6 Al alaşımını infiltre etmiştir. Sonuç olarak infiltrasyon mesafesinin, infiltrasyon süresi ve sıcaklığına bağlı olarak doğrusal bir şekilde arttığını tespit etmiştir [35].
Alaşım Bileşimi:
Takviye ile matris malzemesinin uyumu kompozit yapıların özelliklerini etkileyen önemli değişkenlerden biridir. İnfiltrasyon yönteminde sıvı metalin takviyeyi ıslatma kabiliyeti, infiltrasyon mesafesini önemli bir şekilde etkilemektedir.
Alüminyum matrisli kompozit malzemelerin infiltrasyon yöntemiyle üretildiği birçok araştırmada, sıvı matrisin Mg içeriğinin infiltrasyonu arttıran bir etki gösterdiği belirtilmiştir. Basınçsız infiltrasyonda sıvı matrise Mg ilavesi ve azot gaz ortamının infiltrasyonu kolaylaştırdığı bilinmektedir.
Mg, sıvı Al’nin seramik parçacıkları ıslatmasını geliştirerek infiltrasyonu sağlamaktadır [36, 37]. Aghajanian ve ark.
[38] basınçsız infiltrasyon yöntemiyle Al2O3 ve SiC takviyeli, alüminyum matrisli kompozit üretmişlerdir. Bu çalışmada üretim değişkenlerine bağlı olmakla birlikte infiltrasyonun gerçekleşebilmesi için kritik bir Mg miktarına ihtiyaç olduğu belirtilmiştir.
Bu gerekli Mg miktarı %0,5–1 aralığındadır. 900°C sıcaklık, 5 saat süre, %100 N2(g) ortamı ve Mg ilavesi optimum çalışma değişkenleri olarak bildirilmektedir [38]. Sıvı matris içine Cu ilavesinin infiltrasyonu geciktirdiği, Si ilavesi ile de infiltrasyonun arttığı belirtilmiştir [38].
Chong ve ark. [32] tarafından yapılan bir çalışmada ise SiC bünyelere basınçlı infiltrasyon yöntemiyle 2014 Al alaşımının infiltre edilmesinde saf Al’ye %4,2 Cu ilavesinin eşik basıncını artırdığı belirtilmiştir.[32]
İnfiltrasyon Ortamı:
İnfiltrasyonu arttırmak amacıyla gerçekleştirilmiş olan bazı çalışmalarda infiltrasyon sıcaklığına veya 1000–1150°C’lere kadar Ar gaz ortamı altında çıkıldığı ancak bu sıcaklıkta N2 gaz ortamına geçildiği ve soğutma esnasında da yine N2gaz ortamında devam edildiği bildirilmektedir.
Gerçekleştirilen bu fırın gaz ortam değişikliğinin infiltrasyonu kolaylaştırdığı bildirilmektedir [36, 39, 40]. Aghajanian ve ark. [38] basınçsız infiltrasyon yöntemiyle Al2O3 ve SiC parçacık takviyeli, Al matrisli kompozit malzeme üretmişlerdir. Bu
çalışmada %75 Ar ve %25 N2 gaz ortamında tam infiltrasyon elde etmişlerdir [38]. Ortamda azot miktarının artmasıyla AlN miktarı da artmış, AlN miktarının artmasıyla infiltrasyon artmıştır [38].
Başlangıç Malzemelerinin Tane Boyut ve Dağılımı:
Seramik taneleri arasında oluşan infiltrasyon öncesi boşluklar, seramik tane büyüklüğüne bağlı olarak infiltrasyonu etkilemektedir. Büyük tane boyutuna sahip seramik taneleri arasında, infiltrasyon öncesi boşlukların büyük olmasıyla sıvı metalin bu gözeneklere infiltrasyonu kolaylaşmaktadır.
Chong ve ark. [32] SiC gözenekli bünyelere basınçlı infiltrasyon yöntemiyle 2014 Al alaşımı infiltrasyonunda artan tane boyutunun infiltrasyon için gerekli eşik basıncını azalttığını tespit etmişlerdir. Elwahed ve Asar, [41] Al–Al2O3 sisteminde basınçlı infiltrasyon yöntemiyle kompozit malzemeler üretmişlerdir.
Bu çalışmada artan takviye boyutunda infiltrasyon mesafesinin arttığı ve % açık gözenek miktarının azaldığını belirtmişlerdir [41].
Candan ve ark. [42] farklı tane boyutuna sahip (12,8 μm–22,8 μm ve 36,7 μm) gözenekli SiC bünyelere 400–900 kPa basınç ile sıvı Al alaşımı infiltre etmişler ve infiltrasyon davranışını bilgisayar yardımıyla gözlemlemişlerdir. Bu çalışmada artan SiC tane boyutuyla, infiltrasyon süresinin azaldığını belirtmişlerdir. [42]
Seramik Hacim Oranı:
İnfiltrasyon yönteminde seramik hacim oranı infiltrasyon davranışını ve kompozit yapıların özelliklerini belirleyen en önemli değişkenlerden biridir. Kompozit yapıların, gözeneklilik, sertlik, çekme dayanımı ve aşınma gibi özellikleri seramik hacim oranı ile doğrudan ilgilidir.
Ayrıca infiltrasyon ile kompozit yapı üretiminde takviye hacim oranının önemli bir etkisi vardır. Basınçsız infiltrasyon yöntemiyle kompozit yapıların üretimi için hazırlanan peletlerin seramik hacim kesri genellikle %40 ile %70 arasında değişmektedir. Seramik hacim kesri belirlenirken dikkat edilmesi gereken önemli etkenler şunlardır: [43]
• İnfiltrasyon aşamasında gözenekli seramik bünyenin gerekli mekanik mukavemete sahip olması,
• Sıvı metalin infiltrasyonunu sağlamak için hazırlanan gözenekli seramik bünyenin yeterli geçirgenliğe sahip olması.
Yaş Bünyenin Gözenek Miktarı:
Glass ve Green [44] tarafından gerçekleştirilen bir çalışmada Y–TZP numuneleri 960–1305°C arasında değişen sıcaklık aralığında 1 saat süreyle sinterlenerek %56 ile %88 arasında değişen yoğunluklara sahip bünyeler üretilmiştir. Hazırlanan gözenekli seramik bünyelere eriyik nitrat tuzları infiltre edilmiştir.
Bu çalışmada infiltrasyon kalınlığının infiltrasyon süresi ve başlangıç bünye yoğunluğunun bir fonksiyonu olduğu belirlenmiştir. İnfiltrasyon kalınlığı ve zamanın karekökü arasında doğrusal bir bağıntı olduğu saptanmıştır. Peletin yoğunluğu arttıkça, infiltrasyon kalınlığının azaldığı gözlemlenmiştir. [44]
Yrd. Doç. Dr. Ayşe Kalemtaş / Metalürji ve Malzeme Mühendisliği Bölümü - Doğa Bilimleri, Mimarlık ve Mühendislik Fakültesi
Bursa Teknik Üniversitesi
Kaynaklar
[1] V. Torabinejad, M. Aliofkhazraei, S. Assareh, M.H. Allahyarzadeh, A.S. Rouhaghdam, Electrodeposition of Ni- Fe alloys, composites, and nano coatings-A review, J Alloy Compd 691 (2017) 841-859.
[2] K. Zyka, A. Mohajerani, Composite piles: A review, Constr Build Mater 107 (2016) 394-410.
[3] S.S. Sidhu, S. Kumar, A. Batish, Metal Matrix Composites for Thermal Management: A Review, Crit Rev Solid State 41(2) (2016) 132-157.
[4] T. Vaisanen, A. Haapala, R. Lappalainen, L. Tomppo, Utilization of agricultural and forest industry waste and residues in natural fiber-polymer composites: A review, Waste Manage 54 (2016) 62-73.
[5] K.L. Pickering, M.G.A. Efendy, T.M. Le, A review of recent developments in natural fibre composites and their mechanical performance, Compos Part a-Appl S 83 (2016) 98-112.
[6] X. Xiang, G.K. Zhang, X.L. Wang, X.C. Lai, Review on Preparation Techniques of FeAl/Al2O3 Composite Tritium Permeation Barriers, Rare Metal Mat Eng 45(2) (2016) 522-528.
[7] A. Afzal, A. Kausar, M. Siddiq, A Review on Polymer/ Cement Composite with Carbon Nanofiller and Inorganic Filler, Polym-Plast Technol 55(12) (2016) 1299-1323.
[8] M.N. Avettand-Fenoel, A. Simar, A review about Friction Stir Welding of metal matrix composites, Mater Charact 120 (2016) 1-17.
[9] P. Kumar, V.K. Srivastava, Tribological behaviour of C/C-SiC composites-A review, J Adv Ceram 5(1) (2016) 1-12.
[10] E. Ayas, A. Kalemtas, G. Arslan, A. Kara, F. Kara, Spark plasma sintering of Si3N4-B4C composites, J Ceram Soc Jpn 116(1354) (2008) 727-731.
[11] E.E. Belgin, G.A. Aycik, A. Kalemtas, A. Pelit, D.A. Dilek, M.T. Kavak, Usability of natural titanium-iron oxide as filler material for ionizing electromagnetic radiation shielding composites; preparation, characterization and performance, J Radioanal Nucl Ch 309(2) (2016) 659-666.
[12] E.E. Belgin, G.A. Aycik, A. Kalemtas, A. Pelit, D.A. Dilek, M.T. Kayak, Preparation and characterization of a novel ionizing electromagnetic radiation shielding material: Hematite filled polyester based composites, Radiat Phys Chem 115 (2015) 43-48.
[13] E. Ayas, A. Kalemtas, G. Arslan, A. Kara, F. Kara, Spark Plasma Sintering of Silicon Nitride-Boron Carbide Composites, Key Eng Mat 403 (2009) 225-226.
[14] C.C. Thong, D.C.L. Teo, C.K. Ng, Application of polyvinyl alcohol (PVA) in cement-based composite materials: A review of its engineering properties and microstructure behavior, Constr Build Mater 107 (2016) 172-180.
[15] R.Z. Yang, Y.Z. He, Optically and non-optically excited thermography for composites: A review (vol 75, pg